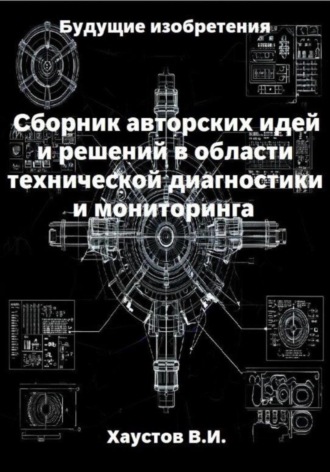
Полная версия
Сборник авторских инженерно-технических идей и решений в области систем технической диагностики и мониторинга

Владимир Хаустов
Сборник авторских инженерно-технических идей и решений в области систем технической диагностики и мониторинга
Введение
Современная наука и промышленность переживают период стремительных технологических изменений. В этом контексте особое значение приобретают нестандартные инженерные подходы, прорывные идеи и авторские решения, способные обеспечить повышение эффективности, надёжности и функциональности производственных, измерительных и управляющих систем. Инженерное мышление, основанное на точной научной интуиции и практической наблюдательности, позволяет находить элегантные решения даже в тех случаях, где традиционные методы оказываются недостаточными или избыточно сложными.
Настоящий сборник представляет собой тематически сгруппированную коллекцию оригинальных авторских технических идей, основанных на сочетании классических физических эффектов с современной элементной базой и практико-ориентированной логикой внедрения. В центре внимания – компактность, простота, гибкость и адаптивность каждого решения, а также его потенциальная применимость в условиях научных лабораторий, малых и средних производств, инженерных центров и отраслевого НИОКР.
Сознательно избегая излишней теоретизации, акцент сделан на прикладной стороне – на технической реализуемости, аппаратной логике, схематических решениях и методах адаптации под конкретные задачи. Подход, применённый в сборнике, основан на следующих принципах:
– Использование известных, но недооценённых физических эффектов в новых инженерных интерпретациях;
– Минимальное вмешательство в существующие технологические и производственные процессы;
– Повышение функциональности оборудования без масштабной реконструкции систем;
– Возможность адаптации решений под различные бюджеты, включая опытные и пилотные образцы;
– Потенциал патентоспособности и оригинальности.
Каждая идея в сборнике снабжена кратким техническим описанием, указанием принципа действия, областью применения и выводами по функциональности. Некоторые разработки уже прошли предварительную экспериментальную отработку, часть остаётся концептуальными, но технологически доступными для реализации в условиях экспериментального цеха или научной лаборатории.
Предлагаемый сборник не претендует на энциклопедическую полноту, но может стать источником инженерного вдохновения, набором отправных точек для собственных исследований и полезным материалом для специалистов в сфере автоматизации, диагностики, машиностроения, материаловедения, энергетики, инжиниринговых решений и промышленных испытаний.
1. Лазерный способ идентификации железнодорожных вагонов по осевым профилям баз тележек
Заявленный способ является альтернативой дорогостоящим оптическим системам распознавания с использованием видеокамер и искусственного интеллекта.
Единственное условие, ограничивающее применение способа заключается в том, что система должна заранее знать информация о каждом железнодорожном составе, который поступит на территорию промышленного производства. Должны быть известны все номера вагонов и последовательность расположения в железнодорожном составе.
Это условие для крупного промышленного производства в настоящее время выполняется. Информация о каждом железнодорожном составе, поступающим на территории промышленного производства, представлена в виде телеграммы натурного листа поезда (ТГНЛ), с указанием всехвагонов входящих в его состав и их последовательности номеров.
Предлагается за идентификационный параметр для каждого грузового вагона брать колёсные базы его двух тележек. Каждый Ж/Д вагон в своей серии конструктивного исполнения, в том числе и тележек – индивидуален. Невозможно изготовить две строго идентичные тележки. К тому же база каждой тележки в течении относительно небольшого периода будет зависеть только от температурных условий окружающей среды, которые можно легко учесть программным способом.
Таким образом, идентификационная характеристика каждого вагона носи вероятностный характер.
Рассмотрим пример использования способа идентификации применительно к самому распространённому типу колёсных тележек с базой в 1850 мм., согласно рис. 1.
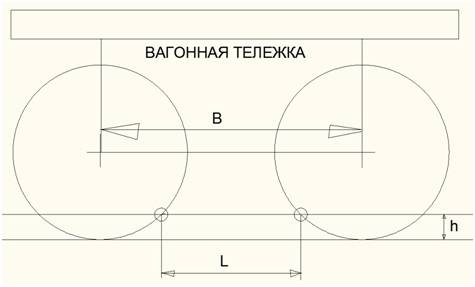
Рис. № 1. Вагонная тележка, размеры.
Где:
B – колёсная база, мм.
L – идентификатор, мм.
H – высота идентификатора над Ж/Д полотном, мм.
Для других типов тележек способ идентификации идентичен и будет зависеть только от места статического расположения оптических датчиков.
Согласно ГОСТ колёсная база классической тележки равна 1850 мм с погрешностью от 1800 до 1890 мм.
Измерение расстояния колёсной базы будем проводить с помощью лазерных импульсно-оптических датчиков с чувствительностью на переключение – 0,01 мм.
В диапазоне выше указанных отклонений базы согласно ГОСТ в 90 мм для одной тележки в идеальных условиях (без влияния температуры окружающей среды и степени износа вагона) вероятность распознавания в идеальных условиях составит 1:90 000. Вероятность распознавания системой одного вагона с двумя тележками будет составлять 1:180 000.
В реальных условиях с учётом степени износа вагона и температурных условий окружающей среды – вероятностные значения идентификации будут в разы меньше, но достаточны для заявляемых целей учёта времени нахождения на территории промышленного производства.
Техническая реализация способа в упрощённом виде представлена на рис. № 2 только для одной стороны Ж/Д пути. Для другой стороны Ж/Д пути принцип идентичен.
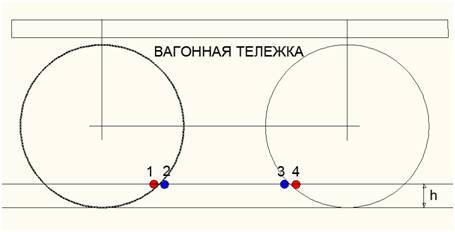
Рис. № 2. Способ идентификации по колёсной базе.
Четыре оптические пары датчиков (в дальнейшем – датчики) стационарно размещены вдоль Ж/Д полотна на высоте h в пункте входа/выхода Ж/Д составов на/из территории промышленного производства.
Датчики располагаются таким способом, чтобы с учётом возможного максимального расстояния колёсной базы из стандарта ГОСТ– два крайних датчика (1,4) перекрывались колёсами, а два внутренних (2,3) – были открытыми. В случае выше указанного расстоянием размещения крайних датчиков будет 890 мм плюс расстояние однозначного распознавания перекрытия. Расстояние между 1 и 2, а также между 3 и 4 датчиками выбирается также исходя из однозначного распознавания переключения их по отдельности.
Направление переключения между 1 и 2, а также между 3 и 4 датчиками определяет направление движения вагона и его мгновенную скорость.
Разница во времени переключения между 1,2 и 3,4 для двух тележек вагона будет являться идентификатором самого вагона с учётом температурной коррекции воздействия окружающей среды.
При этом информация из телеграммы натурного листа поезда (ТГНЛ) от РЖД привяжет этот идентификатор к конкретному номеру вагона для заявленных целей учёта времени нахождения на территории промышленного производства.
Конструктивное исполнение способа достаточно просто. В упрощённом виде минимум – 8 лазерных датчиков (по 4 на каждую сторону Ж/Д полотна), плата сопряжения и компьютер.
Программное обеспечение способа также относительно просто по сравнению с искусственным интеллектом систем оптического распознавания номеров.
Таким образом с учётом Выше изложенного каждому прибывающему грузовому Ж/Д вагону по его номеру система присваивает свой идентификатор по измеренным расстояниям между колёсными базами двух тележек. По этому идентификатору система определяет время нахождения вагона на территории промышленного производства. Как уже было сказано выше – идентификатор имеет вероятностную характеристику и в идеальных условиях равен 1:180 000.
В реальных условиях с учётом степени износа вагона и температурных условий окружающей среды – вероятностные значения идентификации системой будут в разы меньше, но достаточны для заявляемых целей.
Таким образом:
Преимущества метода:
1. Экономичность:
– Лазерные датчики существенно дешевле комплексных систем видеонаблюдения с системами распознавания ГОСТ-номеров и нейросетевой обработки.
2. Надёжность:
– Отсутствие зависимости от погодных условий, загрязнения вагонов, повреждений маркировки и помех в виде граффити.
3. Высокая относительная уникальность сигнатур:
– Несмотря на то что ГОСТ допускает только 90 мм отклонений колёсной базы (1800–1890 мм), в сочетании со вторичной базой тележки и температурной коррекцией достигается высокая вероятностная уникальность идентификации 1:180 000 (в идеальных условиях) и 1:10 000–1:30 000 в реальных условиях, что достаточно в задачах «учёт-пребывание-выход».
4. Объективность данных:
– Колёсная база – это физическая характеристика, не подверженная визуальному искажениям и фальсификации, в отличие от табличек или радиометок.
5. Простота интеграции:
– Система может быть интегрирована в существующие IT-структуры
(АСУ ТП, ERP, MES) предприятия для ведения автоматизированного учёта железнодорожного трафика.
Алгоритм работы системы
– Оптические датчики, установленные по обе стороны рельсов (или с одной стороны при подтверждённой точности), фиксируют моменты прохождения каждой оси;
– По времени переключений фиксируются метки входа/выхода передней и задней пары колёс;
– Измеряется база тележек, направление движения, мгновенная скорость;
– Рассчитанные значения обрабатываются с учётом температуры и подаются в модуль идентификации;
– Происходит привязка к вагону согласно ТГНЛ (натурному листу), интеграция с системой учёта времени пребывания на территории;
– При выходе из промплощадки система автоматически фиксирует момент покидания вагона и рассчитывает общее время пребывания.
Прогнозируемая точность и надёжность:
– Даже с учётом допустимых погрешностей (+-0,01 мм лазерный датчик, +-2–3 мм температурная компенсация) система показывает высокую стабильность метки;
– Вероятность перекрёстной ошибки ниже допустимого для задач оперативного учёта (менее 1/1000 при соблюдении термокоррекции и высокой частоте дискретизации);
– Уникальность базов зависит от возраста, модели, условий эксплуатации тележек, что усиливает различимость.
Технические особенности реализации:
– Независимое питание/резервируемость датчиков – при установке вблизи ж/д рампы или ворот;
– Климатическая защита IP65+; возможна установка в теплоизолированных кожухах;
– Интерфейс связи с АСУ предприятия – OPC UA / Modbus / MQTT / REST API;
– Возможность модернизации до контроля геометрии всего состава или интеграции в систему контроля технического состояния вагонов.
Ограничения метода:
– Не подходит для ситуаций, в которых запрещена или невозможна предварительная загрузка информации о составе (ТГНЛ);
– Не заменяет классическую систему идентификации (для служб безопасности, например), но дополняет её в производственном учёте;
– Требует точной установки датчиков и периодической повторной метрологической поверки измерительной системы.
Заключение
Представленный способ является надёжной, масштабируемой и малозатратной альтернативой дорогим системам видеоанализа и радиометок в задачах учёта времени нахождения железнодорожных вагонов на территории промышленного предприятия. Используя физически воспроизводимую характеристику – колёсную базу тележек, измеряемую с высокой точностью с помощью лазерных датчиков, он обеспечивает достаточную степень уникальности для оперативного контроля, автоматизации логистики и оптимизации работы служб снабжения и отгрузки.
Заключение
Предложенный способ представляет собой эффективную, экономически оправданную и инженерно реализуемую альтернативу классическим системам идентификации железнодорожных вагонов на базе видеоаналитики, компьютерного зрения и распознавания символов (OCR). Он ориентирован на промышленное применение в условиях, когда заранее известна структура состава, а режим времени пребывания вагонов на территории или в производственном цикле критичен для управления логистикой и планирования.
Примечание
Более подробная информация о способе, а также сведения о экспериментальных работах, этапах опытно-конструкторских разработок и вариантах практического применения представлены в авторском исследовательском проекте: **Вихри Хаоса – Инновационный шторм идей и экспериментов в науке и технике**.
Официальный ресурс: [https://vihrihaosa.ru]
2. Вихре кольцевой детонационный способ измерения толщины покрытия стального листа
Идея способа основывается на одном интересном эффекте, который проявляется в любом вихревом кольце при его прямолинейном распространении.
Сформированное любым способом и движущееся прямолинейно воздушное интенсивное вихревое кольцо является достаточно продолжительное время замкнутой самоподдерживающей упругой вихревой структурой, степень упругости которой зависит только от интенсивности формирования вихревого кольца.
В такой кольцевой вихревой структуре любые внешние изменения, влияющие на геометрические характеристики вихревого кольца, в любом месте при его распространении мгновенно отражаются во всём объёме его объёме.
Можно сказать, что вихревое кольцо ведёт себя как достаточно упругий движущийся элемент, в котором степень упругости зависит от скорости его распространения, циркуляции и угла расходимости. В этом легко убедится на примере дымового сигаретного кольца курильщика. Такое кольцо с совсем небольшой циркуляцией и скоростью распространения проявляет свойства упругого элемента – достаточно слегка толкнуть движущееся кольцо.
При этом сам Роберт Вуд о вихревых кольцах говорил следующее: Аудитория может получить представление о «твердости» вращающегося воздушного вихря, если последовательно выпускать невидимые кольца в зал. Удар кольца в лицо человека ощущается как мягкий толчок пуховой подушкой.
Этот эффект можно считать относящимся и для вихревых полуколец, сформированных так называемым “материнским” вихревым кольцом при прохождении через относительно тонкий лист. Такой разделитель не способен разрушить ядра полукольцевых вихрей, но оказывает влияющее воздействие, о котором будет сказано ниже и на основании которого базируется сама идея измерений.
Вихревые полукольца являются движущимися с обеих сторон листа независимыми “твёрдыми” элементами. Толщина листа в этом случае будет являться тем маркером, изменение которого в каждом конкретном месте мгновенно влияет на ядра полукольцевых вихрей, сжимая их или растягивая. Это означает, что мгновенно будут меняться, но с разными знаками значения давлений снаружи таких вихревых полуколец, движущихся поперёк так называемого “делительно-измеряемого” стального листа.
Вихревые полукольца, сформированные от общего “материнского” вихревого кольца, имеют абсолютно идентичные характеристики по скорости, распространения, циркуляции, углу расходимости и т.п. Это значит, что, измеряя значения давлений снаружи движущихся вихревых полуколец можно определить математическую зависимость толщины листа с покрытием, относительно толщины листа без покрытия. При этом влияющие на значения давлений вибрации при движении самого листа также могут быть нивелированы математически.
Интенсивное вихревое кольцо
В качестве источника формирования следующих друг за другом с частотой 2 Гц высокоинтенсивных вихревых кольцевых структур предлагается использовать детонационный источник энергии цилиндрической формы, бесклапанный с сферическим резонатором на выходе, см. рис. № 3.
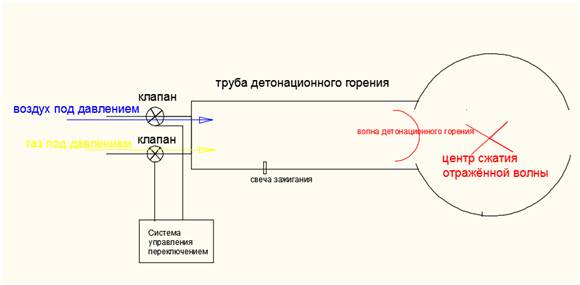
Рис. № 3. Трубчатый источник волн детонационного горения с сферическим резонатором на выходе.
Экспериментальным путём установлено формирование одновременно два вихревых кольца, т.е. волна детонационного горения формирует два вихревых кольца, одно – фронтом волны, другое – областью между волной горения и разряжением.
Первичное высокоинтенсивное вихревое кольцо распространяется прямолинейно с углом расширения – 0,2 градуса.
Вторичное вихревое кольцо распространяется с углом расширения примерно 150 градусов.
На основании выше изложенного реализация предлагаемого способа представлена на рис. № 4.
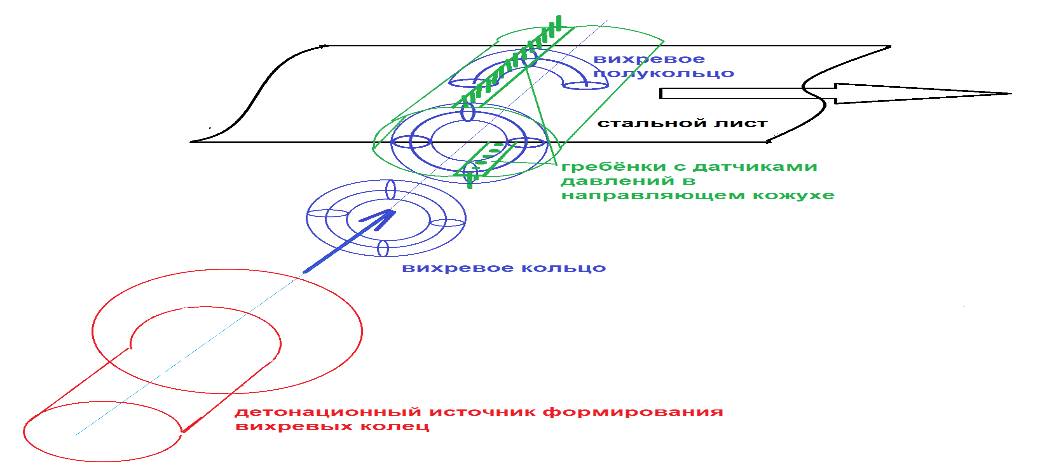
Рис. № 4. Вихре кольцевой детонационный способ измерения толщины покрытия стального листа.
Симметрично с обеих сторон листа на одинаковом расстоянии установлены строго параллельные линейки с датчиками давления.
Поперёк стального листа друг за другом движутся сформированные внешним детонационным источником энергии воздушные высокоинтенсивные вихревые кольца.
Каждое такое вихревое кольцо после полного сформирования при своём движении “разрезается” тонким стальным листом пополам. Таким образом, с обеих сторон стального листа движутся уже синхронно два зеркальных вихревых полукольца, имеющие одинаковую скорость распространения, циркуляцию и угол расходимости.
Одновременно с движением вихревых полу колец – датчиками измеряются значения их наружных давлений в каждом месте стального листа по всей его длине.
Изменение толщины листа в определённом месте или местоположение в случае вибрации даже на 1 микрон приведёт к мгновенному воздействию на полу ядра полукольцевых вихревых потоков. Это означает, что практически мгновенно изменятся значения давлений диаметрально по всему объёму обоих вихревых полуколец. С одной стороны листа давление увеличится, с другой стороны листа либо уменьшится, либо останется без изменений.
Два диаметрально расположенных датчика давления, зафиксируют изменения, которое затем математически будут преобразованы в единицы линейных размеров толщины в заданном месте.
Предложенная технология определения толщины стального листа с использованием вихревых полукольцевых потоков, формируемых путём рассечения детонационно сформированного вихревого кольца, представляет собой эффективный и экономически целесообразный метод неразрушающего контроля геометрических параметров материала в реальном времени.
При прохождении синхронных полукольцевых вихревых потоков с обеих сторон листа создаются зеркальные аэродинамические поля, чувствительные к микроскопическим изменениям расстояния между ними. Благодаря высокой циркуляции, направленному движению и стабильной структуре вихревого потока, даже незначительное отклонение в толщине листа (порядка 1 микрометра) мгновенно вызывает отличие в давлении в образовавшихся полукольцах. Это отличие надёжно фиксируется парой синхронных датчиков давления и может быть мгновенно преобразовано в точное значение толщины в заданной точке.
Преимущества технологии:
– Чрезвычайно высокая чувствительность измерения при минимальной стоимости оборудования;
– Простота и дешевизна конструктивного исполнения детонационного источника вихревых колец;
– Модульность и масштабируемость системы – возможна адаптация под листы различной ширины, за счёт изменения количества датчиков;
– Отсутствие физического контакта с измеряемой поверхностью, что исключает износ чувствующих элементов и позволяет использовать систему в условиях высокой скорости движения листа.
Ограничения:
– Метод не позволяет раздельно измерять толщину покрытий на одной стороне листа – выводится суммарная толщина основы и покрытия;
– Измерения выполняются дискретно как по длине, так и по ширине листа (шаг определён частотой формирования вихревых колец и количеством датчиков давления);
– Для прецизионных измерений необходима предварительная калибровка и адаптация под конкретные физико-газодинамические условия (плотность газовой среды, температура, скорость листа и т.д.).
Заключение
Предложенная система может стать надёжным, недорогим и технологически пригодным инструментом для организации непрерывного неинвазивного мониторинга толщины металлопроката в условиях серийного производства. Она способна дополнить или в ряде случаев заменить более сложные и дорогие методы (такие как рентгеновские, вихретоковые, лазерные измерители), особенно при производстве тонкого листа, алюминиевого, оцинкованного или другого проката, где необходима высокая чувствительность контроля при минимальных затратах на обслуживание оборудования.
Примечание
Более подробная информация о способе, а также сведения о экспериментальных работах, этапах опытно-конструкторских разработок и вариантах практического применения представлены в авторском исследовательском проекте: **Вихри Хаоса – Инновационный шторм идей и экспериментов в науке и технике**.
Официальный ресурс: [https://vihrihaosa.ru]
3. Пьезоэлектрический способ измерения крутящего момента приводных валов
Предложена экспериментальная модель простейшего тензоэлектрического (термоэлектрического) датчика на основе тонкой плёнки оксида меди, формируемой на поверхности медного стержня методом термоокисления в пламени. При изгибе или кручении такого стержня наблюдается изменение выходного сигнала в пределах 100 мкВ – 1 мВ, что может быть связано с изменением термоэлектрических свойств полупроводникового слоя под действием механической деформации. Такое устройство может служить основой для разработки упрощённых позиционных или деформационных сенсоров, а также как учебный макет для демонстрации эффекта электромеханического преобразования в оксидах металлов.
Введение
Всем известно, что крутящий момент – это сила, при которой происходит деформация вала, только не на изгиб, а скручивание, при котором отдельные сечения вала не повторяют друг друга, а оказываются повернутыми друг относительно друга на определённые углы, тем большие, чем больше приложенная сила. При этом не следует заблуждаться, что мы увидим эту закрутку стального вала, нанеся на поверхность вала линии, параллельные его оси. Величина закрутки будет в реальности настолько мала, что её непросто измерить даже с помощью специальных датчиков существующих измерительных системах.
Для понимания привожу усреднённые значения максимально допустимой “крутки” классического стального вала исходя из его усреднённых прочностных характеристик:
0 3- для каждого метра вала при статической нагрузке,
0 25 – для каждого метра вала при переменной нагрузке,
0 15, для каждого метра вала при ударной нагрузке.
В настоящее время разработано большое количество датчиков и измерительных систем для решения таких задач, но все они имеют один существенный недостаток.
Измерительный элемент любого датчика непосредственно не участвует в процессе измерения деформации измеряемого объекта, а только через так называемую подложку. В качестве подложки в существующих измерительных системах, всегда выступает какой – либо промежуточный материал, защищающий сам чувствительный элемент от различных внешних воздействий, например – электрод датчика. Такой материал, как правило, имеет свои механические свойства, которые не позволяют непосредственно передавать значения деформации в сам измерительный элемент и влияют на чувствительность всей системы.
Чувствительность такой измерительной системы всегда зависит от механических свойств такой подложки.
Исходя из выше изложенного, предлагается непосредственный способ измерения крутящего момента приводных валов, основывающийся на классическом пьезоэфекте в полупроводниках.
В заявляемом способе предлагается полностью отказаться от каких-либо подложек между измерительным элементом и объектом измерения – стальным валом.
Сам измерительный элемент в виде плёнки из полупроводника предлагается химическим или гальваническим способом нанести непосредственно на сам шпиндель в виде кольца, спирали или полоски по всей длине шпинделя.
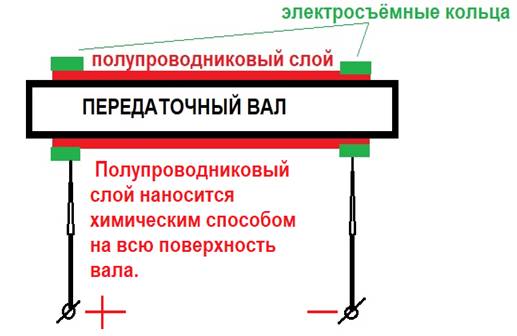
Рис. № 5. Пьезоэлектрический полупроводниковый непосредственный способ измерения крутящего момента приводных валов
Способов нанесения полупроводникового слоя химическим или гальваническим способом достаточно много.
Рассмотрим самый простой и технологичный (хорошо повторяемый) химический способ нанесения полупроводникового слоя, который был опубликован ещё во времена СССР в школьных факультативах старших классов по химии – изготовление солнечной батареи и термоэлемента. Например, тиомочевина из расчёта 114 грамм на 1 литр воды, ацетат свинца из расчёта 345 грамм на 1 литр воды и едкий натр из расчёта 40 грамм на 1 литр воды даже в любительских условиях позволяют получить достаточно прочную полупроводниковую плёнку толщиной 5 микрон на стальном основании.