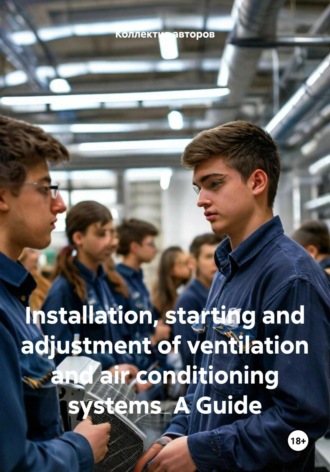
Полная версия
Installation, starting and adjustment of ventilation and air conditioning systems A Guide
– normalized, they are characterized by low coefficients of local resistance, but are laborious to manufacture;
– direct embedding;
– rectangular tees, they are usually equipped with one-sided unified transitions, which allows you to establish a constant ratio of the duct route from the wall along which it is laid.
According to the material used for the manufacture of air ducts, they are divided into several groups:
1. Folded air ducts made of thin-sheet galvanized steel, up to 1 mm thick (without painting).
2. Folding air ducts made of thin-sheet black steel, up to 1 mm thick (with subsequent painting inside and outside).
3. Welded air ducts made of sheet steel, 1.2- 3.0 mm thick (with subsequent painting with primer).
4. Seam and welded air ducts made of corrosion–resistant steel, thickness from 0.5 mm to 3 mm (usually grades X18N9T) – without painting.
5. Folding air ducts made of titanium (ρ = 4,500 kg/m3), which have the highest corrosion resistance when moving an aggressive medium.
6. Folding ducts made of metal plastic, clad on one or both sides with PVC or PVC film. With a one-sided coating, the film must be inside the duct, in contact with an aggressive environment.
The connection of individual parts of round air ducts to each other is performed by flanging bandages (with a diameter of up to 800 mm) or on flanges made of angular steel (with large diameters).
The connection of rectangular air ducts with a side less than 1600 mm is performed on profiled tires fastened with 4 bolts at the corners. If the side dimensions exceed 1600 mm, additional latches are used.
For conventional general exchange systems, it is preferable to use folded air ducts made of galvanized steel. Welded air ducts are installed with increased density requirements (smoke extraction shafts, air ducts passing through rooms with explosion hazard category A and B) and air movement with a temperature above 80 °C.
Flexible reinforced air ducts are widely used to avoid difficult fitting when connecting from mains to air distributors and grilles.
One of the latest solutions in the field of air distribution is textile air ducts. They are inflated by the flow of air and evenly distribute it along their entire length. In addition to noise reduction, textile ducts have the ability to trap all dust particles larger than 5 microns. They can be used in rooms with a high frequency of air exchange, without creating local areas with increased air mobility, as is the case with jet distribution.
This type of duct combines two devices – the duct itself and the air distributor.
There are several options for the operation of a textile duct. The air supply to the room can be carried out through its entire surface (in this case, airtight fabric channels made of 100% polyester are used) or through special holes made in the duct material (an impermeable fabric with perforated injector holes is used). Mixed versions are also used. The air flow velocity inside the airtight material does not exceed 0.01–0.5 m/sec, the air velocity coming out of the cracks is 4–10 m/sec, through perforated holes (injectors) is 7–13 m/sec.
Cylindrical fabric ducts are the most common. They are convenient if you need to provide intensive air exchange, preventing drafts. Semicircular air ducts are used in rooms with low ceilings, for example, in catering establishments, non-food stores, hotels, etc. Air ducts in a quarter-section of a circle can also be used, installed around the perimeter of the room.
Installation of steel ducts in rooms with high ceilings is quite laborious and time-consuming. The use of textile air ducts greatly facilitates the work. Sections of air ducts (usually 5 m long) are connected to each other with the help of zippers. The air ducts are suspended using stretched cables or rails. In the latter case, the fastening is more rigid, and the duct retains its shape even without air supply. When condensation occurs, a nutrient medium is formed that promotes the development of microorganisms. Textile ducts can be easily dismantled, washed or cleaned. They are produced with a diameter of 100 to 1000 mm and a length of up to 100 m, as well as various densities that allow changing the air supply from 160 to 500 m3 / g * m2 at a static pressure inside 100 Pa.
When transporting hot gases with a temperature of more than 100 °C in ventilation systems, the thickness of the steel walls of the air ducts should be 1–2 mm. To transport air with an admixture of toxic gases and vapors, air ducts must be made of certain materials, depending on the composition of the gases (steel with a thickness of at least 0.7 mm, aluminum, vinyl, etc.).
In ventilation systems of residential, public and administrative buildings, as well as office and auxiliary premises of industrial enterprises, air ducts made of slag-alabaster, cinder-concrete, reinforced cement and plastic plates, bricks, concrete, etc
. are used for portable ventilation installations rubberized, as well as metal flexible hoses.
When laying rectangular vertical air ducts, they try to make the most of the internal walls, in which appropriate channels are left for this purpose. If this is not possible, side channels and shafts are mounted to the walls.
In addition, spiral-wound metal air ducts are used in construction practice, as well as plastic air ducts that resist corrosion (made of vinyl, polyisobutylene, etc.). Their disadvantage lies in the fact that they can only be used at a temperature of transported air no higher than 70 °C.
In addition to these modifications, the ducts can be flexible, semi-flexible, thermally insulated, and also acting as a muffler.
4.2. Metal air ducts
Most often, metal ducts are used in air conditioning systems, which have great strength and resistance to fire.
They are made of galvanized or stainless steel.
Spiral-lock round (with a folding connection). They are made of steel tape with an anti-corrosion coating 0.5–1 mm thick, about 130 mm wide. They have increased rigidity compared to straight-seam ducts, there is no length restriction, aesthetic appearance, high seam density. The disadvantages include the fact that the seam takes about 15% of the metal from which the duct is made.
Spiral-welded round. They are made of steel tape with an anti-corrosion coating 0.8–2.2 mm thick, about 400–750 mm wide. The joints are welded overlap. Spiral-wound air ducts have less metal consumption compared to spiral-lock air ducts, there is no length restriction, high seam density. However, they cannot be made from steel thinner than 0.8 mm.
Rectangular straight-folding air ducts. They are made of steel sheet, it is desirable to place the seam on the bend so that it serves as an additional stiffener. Such ducts are easier than round ones to place in a space with a limited height, they fit better into the interior of the building. Rectangular ducts have greater aerodynamic drag than circular ducts with similar performance.
Round straight-folding air ducts. According to the manufacturing method and material, they are similar to rectangular air ducts, they differ only in a circular cross section.
4.3. Metal-plastic air ducts
Metal-plastic air ducts consist of two layers of metal, between which foam plastic is laid. Usually such a construction is used: foamed plastic 2 cm thick, located between layers of corrugated aluminum 80 microns thick. They have a small mass with high strength. They have a smooth surface, aesthetic appearance, do not require additional thermal insulation.
4.4.Non-metallic air ducts
Non-metallic air ducts are made of synthetic materials: polyethylene, fiberglass, etc.
Polyethylene air ducts: are usually used in supply ventilation systems. When the fan is turned on, the duct (in the form of a sleeve) is inflated with air.
Fiberglass ducts: usually used to connect the fan and air distributors. They are stretched on a metal frame.
Vinyl plastic air ducts: used when moving air containing acid vapors, etc., causing corrosion of steel. The thickness of the vinyl plastic is 3–9 mm, connected by welding.
Non-metallic air ducts are resistant to corrosion, they can be bent in any plane and at any angle.
4.5. Flexible air ducts
Flexible ducts of circular cross-section, lightweight, do not need special turns, as a result of which the duct has fewer connections, which simplifies installation. However, flexible ducts create a large aerodynamic drag, which may be excessive with an extended network, so they are often used as connecting pipes of small length. Flexible ducts are divided into:
• Flexible aluminum ducts without heat and noise insulation;
• Aluminum ducts with polymer coating without heat and noise insulation;
• Highly flexible polyvinyl chloride ducts;
• Highly flexible insulated air ducts consisting of two layers of polyvinyl chloride coated with polyamide fabric. A flexible steel wire spiral is located between the two layers.
• Semi-rigid aluminum ducts with thermal insulation;
• Flexible heat-insulated sound-absorbing air ducts. They consist of:
– Micro-perforated air duct made of high-strength metallized polymer;
– 25- 50 mm of thermal insulation layer with a density of 16 kg/m3;
– An outer coating made of aluminum seamlessly reinforced with fiber.
These ducts have excellent noise reduction performance in the low frequency range. To reduce the possible consequences of the use of mineral fibers on human health, the inner sleeve has minimal perforation, a special acoustic film is placed between the inner sleeve and the insulation layer. This reduces the probability of fiber entrainment at normal air flow speeds to almost a minimum.
Condensation formation, safety, noise, energy saving – these are the criteria that should be taken into account when choosing a material for thermal insulation of air ducts.
4.6. Thermal insulation
Thermal insulation of air ducts performs the following main functions:
• Prevention of condensation on both the inner and outer surfaces of the duct.
• Ensuring fire resistance to prevent the spread of fire in case of fire.
• Attenuation of noise and vibrations that occur during the movement of air through the duct.
• Reduction of heat transfer between the air flow in the duct and the environment.
For the organization of air ducts, materials with a zero (0) fire resistance class are used. If the channel has a multilayer lining, the fire resistance class "zero-one" (0–1) is allowed. This condition is met if all surfaces in the operating mode consist of non-combustible material with a thickness of at least 0.08 mm and if they provide continuous protection of the internal thermal insulation layer having a fire resistance class not higher than the first (1). Fasteners and connections whose length is not more than five times the diameter of the duct itself must be made of a material having a fire resistance class of "zero" (0), "zero-one" (0–1), "one-zero" (1–0), "one-one" (1–1) or "one" (1). Ducts of class "zero" (0) have an outer skin made of a material of fire resistance class not higher than the first (1).
Air treatment and air distribution systems create noise transmitted, among other things, through the duct system. It is possible to reduce noise if you maintain a low air velocity in the ducts, install damping devices at the point where the fan is connected to the duct, use an elastic suspension for the ducts, as well as damping gaskets at the points where the ducts intersect wall structures. The noise propagated through the air ducts can also be attenuated by the use of special silencers and a sound-proofing coating. Many thermal insulation materials have good sound insulation properties and can be used as both heat and sound insulation.
Thermal insulation of the duct can be performed from the inside or from the outside. When using thermal insulation inside the duct, it is necessary to increase the section of the duct to maintain the calculated carrying capacity at a given air velocity. In addition, the side of the thermal insulation in contact with the air flow should be smooth enough so as not to increase the resistance when air moves through the duct.
When installing silencers, the use of external thermal insulation is preferable. Also, the installation of external thermal insulation is the prevention of the occurrence of bacterial foci, the formation of dust and dirt deposits, due to which the thermal insulation material may begin to delaminate, release volatile substances and lose its qualities.
In addition, with external thermal insulation, the risk of fire spreading from room to room in the event of a fire is significantly reduced. The most important factor in the installation of thermal insulation is the prevention of thermal bridges that reduce the effectiveness of thermal insulation, as well as ensuring high vapor resistance. Heat transfer bridges can also occur in places where air ducts are attached to building structures.
The destruction of the thermal insulation material is prevented by:
• For internal thermal insulation – the use of composite materials, where thermal insulation is combined with a metal layer or film.
• For external thermal insulation – the use of neoprene sheathing, galvanized steel sheet or aluminum sheet.
Questions to Chapter 4
1. What are the disadvantages of circular ducts?
2. What are the advantages of rectangular ducts?
3. What material is used in the manufacture of air ducts for buildings and structures for general civil purposes?
4. What factors influence the choice of material for the manufacture of metal ducts?
5. How does the use of flexible air ducts affect the extended sections of the routes of ventilation systems?
Chapter V. Ventilation Parts and Network Equipment
5.1.Ventilation grilles
The grilles can be supply and exhaust. Those and others are adjustable and unregulated; round, square, rectangular; metal (more often steel or aluminum) or plastic; with and without decorative design; of various colors and sizes; with the direction of the flow of supply (or with the intake of the removed) air in one, two, three or four sides. Depending on the design of the grid, compact, flat, incomplete fan or other types of jets are created.
The control devices of the supply grids are the following types of regulators: flow regulator, jet characteristics regulator, direction regulator.
If the air distributor is equipped with more than one of the above regulators, then the regulating devices are usually installed in the same order along the air flow.
Exhaust grilles can also have flow and direction regulators. Some grid designs are universal and are used in both supply and exhaust systems.
Grilles are installed more often on the walls above the serviced area. At the same time, they can be specially designed for installation in the ceiling (for exhaust, inflow or universal).
5.2. Air distributors
The supply of the air in ducted and ductless air distribution systems is carried out in the form of jets.
Table 5.1 shows the schemes of air distribution devices and their main characteristics: aerodynamic coefficient m, temperature coefficient n and local resistance coefficient ξ. The coefficients m and n characterize the rate of attenuation of air velocity and temperature in the supply jet.Such indicators are necessary to calculate the speed and temperature of the air in the working area of the premises.
Table 5.1. Characteristics of air distribution devices
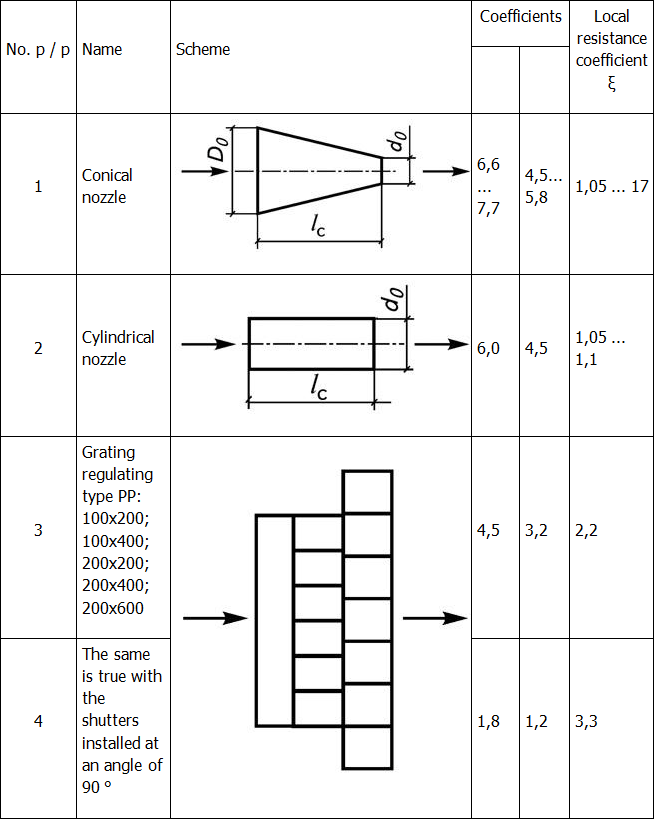

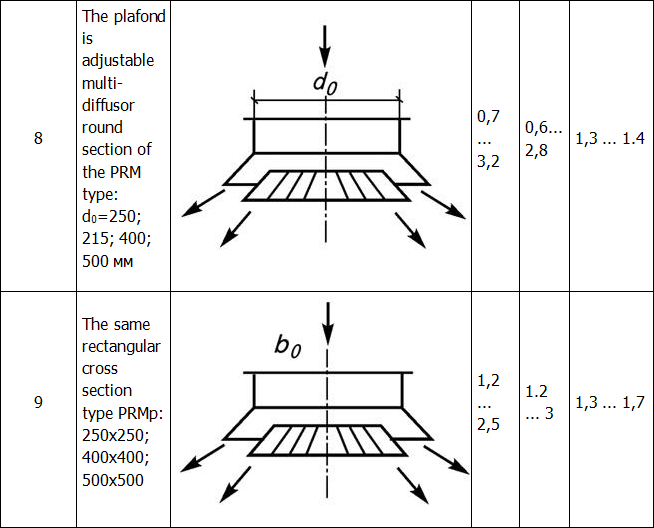
The choice of air supply methods depends on the height and purpose of the premises, the height and placement options of the equipment, as well as on the requirements for the uniformity of the distribution of air parameters.
Choosing the methods of air supply and removal, at the same time pre-select the supply and exhaust air distribution devices, their number and placement options relative to each other. The joint choice of air supply and removal methods is practically determined by the choice of the air distribution method in this room.
The applied methods of air distribution are characterized depending on the direction of movement of the air supplied to the premises: "from top to bottom", if the supply occurs in the upper zone, and removal – in the working; "from top to top", if the supply and removal of air occur in the upper zone of the premises, as a rule, this method ensures the movement of the supplied flows above the working level zones, and in the working area, the set air velocity is created by the reverse flow; "side up", etc. When choosing the method of air distribution, the direction of heat flows and the areas of the premises characterized by the maximum intake of heat or moisture are taken into account.
If it’s necessary to provide increased air velocity in air conditioning systems with an increased value of the height of the working area of the premises (hP. Z > 2 m) it’s possible to provide air distribution through conical nozzles.
The aerodynamic coefficient of conical nozzles m varies in a wide range, and its values depend on the angle of taper of the nozzle. Conical nozzles are characterized by the highest (maximum possible) values of the aerodynamic coefficient. As the taper angle increases, the value of m also increases. At the same time, the maximum value of m = 7.7 … 7.8. Simultaneously with an increase in m, the coefficient of local resistance also changes significantly. Figure 5.1 shows a diagram of a cylindrical nozzle with preload.
Supply grilles of various designs, ceiling lampshades and diffusers are also widely used, capable of working as supply and exhaust devices.
In rooms of small height (up to 5 m), air distribution can be carried out through perforated panels mounted in the ceiling. In this case, the normative mobility of air in the working area is achieved with a large multiplicity of air exchange. Perforation holes are made with a diameter of 2 to 10 mm, the area of the living section of the panel does not exceed 10% of the total area of the panel.
In air distributors-lamps, air is released (removed) through fluorescent lamps mounted in the suspended ceiling structure. Such a solution in the case of air extraction reduces the heat input from the lighting into the room, since part of this heat is carried away together with the exhaust air, moreover, due to the cooling of the lamps, it increases illumination.
A sufficiently satisfactory air distribution can be achieved by using perforated air ducts. The holes in the duct of variable cross-section length are located in its lower part.
Local exhaust ventilation is used when the places of harmful emissions in the room are localized and it is possible to prevent their spread throughout the room.
5.3. Devices for adjusting ventilation systems
General-purpose check valves are designed to prevent air from flowing through the branches to the disconnected fans (from the disconnected fans) when the latter are connected to the collectors. When installing valves in a vertical duct, the air flow should be directed from the bottom up. Installation of the valve in the network is allowed at air speeds in horizontal sections V ≥ 5…6m/s and on vertical V ≥ 4m/s.
The steel valve lobe valves in the usual design are designed to be installed on the discharge side of axial fans in order to prevent cold air and precipitation from entering the production premises after the fans are turned off. The design of the lobe valve is a housing in the bearings of which the blades are fixed on the axes. The purpose of the bearings is to ensure the free opening of the valve in conditions of negative external temperatures during periodic operation of the fans. When the fan is turned on, the blades are supported in the open position by the action of the airflow. After the fan is turned off, the blades return to their original position and overlap the valve section. In order to reduce the width of the valve, instead of switching from a circular fan section to a rectangular valve section, a transitional diaphragm is provided. The minimum dynamic pressure at which the lobe valve operates is 30…40 Pa.
Valves (dampers) air insulated designed for installation in low-pressure supply (exhaust) ventilation systems to prevent the penetration of outside air into the supply chambers and rooms when the fan is not working and to regulate the amount of air entering the system. The dampers can be either electrically heated or without it. The electric heaters in the valves serve only to warm up the flaps in case of icing, in order to prevent damage to the frozen flaps when opening. The electric heaters of the valves are switched on for 5–7 minutes before opening the valve. Valves (dampers) air insulated consist of a housing, double-walled rotary blades with thermal insulation properties, a drive and a motion transmission system from the drive to the blades. A rubber seal is installed at the interface points of the blades of the sound. An actuator is installed as a drive. It is possible to manufacture a manual-driven system. The maximum allowable pressure drop in the closed position is 1225 Pa (125 kgs/m2). Air passage in the closed position at a pressure drop of no more than 5%.
Resistance coefficient in the open position, not more than 0.2.
Dampers are available in the following types:
• Air unified;
• Round section with electric drive;
• Rectangular cross-section with electric drive;
• Circular cross section with manual drive;
• Rectangular cross-section with manual drive;
Air dampers are designed to regulate the amount of air and are used in air ventilation systems, air heating and other sanitary systems with an operating pressure of up to 1000 Pa.
Questions to Chapter 5
1. For what purpose are air distribution devices used?
2. Name the main characteristics of air distribution devices.
3. What factors are taken into account when choosing the type of air distribution device in the room?
4. What is the value of the dynamic pressure required for the operation of the lobe check valve?
5. What is the purpose of electric heating of air dampers, in which cases it is used?
Chapter VI. Mounting tools, fixtures and accessories for mechanization of installation work
Installation of ventilation systems is carried out by a team. As a rule, the integrated team of ventilation fitters includes two or three people with related specialties of an electric welder and a gas cutter. The numerical composition of the team is usually six to seven people. Each team is provided with a set of tools, which allows the team or its units to independently perform almost the entire scope of work on the installation of ventilation systems.
Table 6.1.
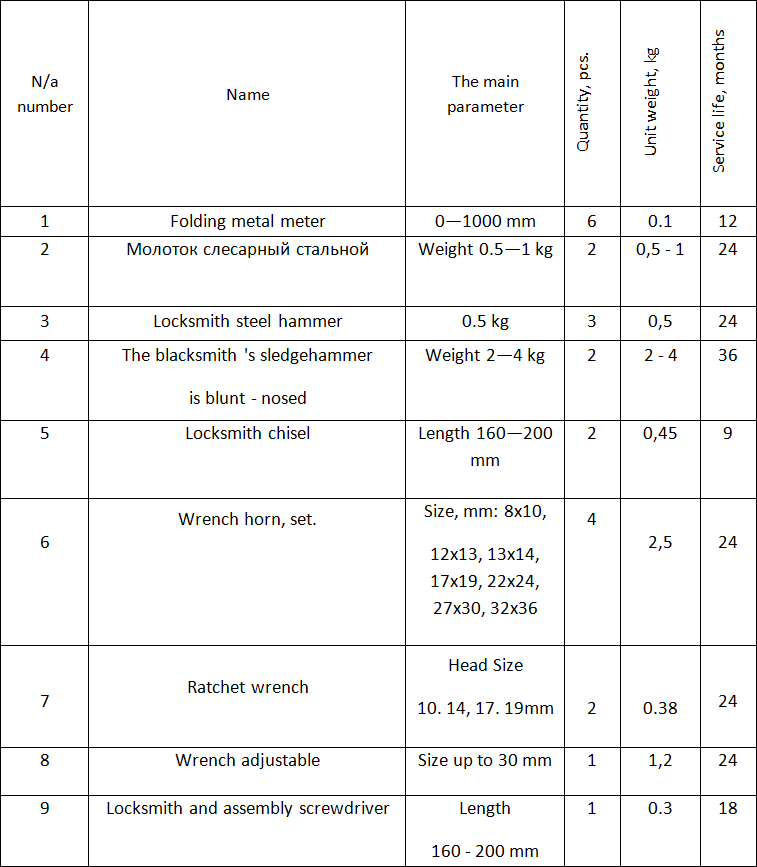
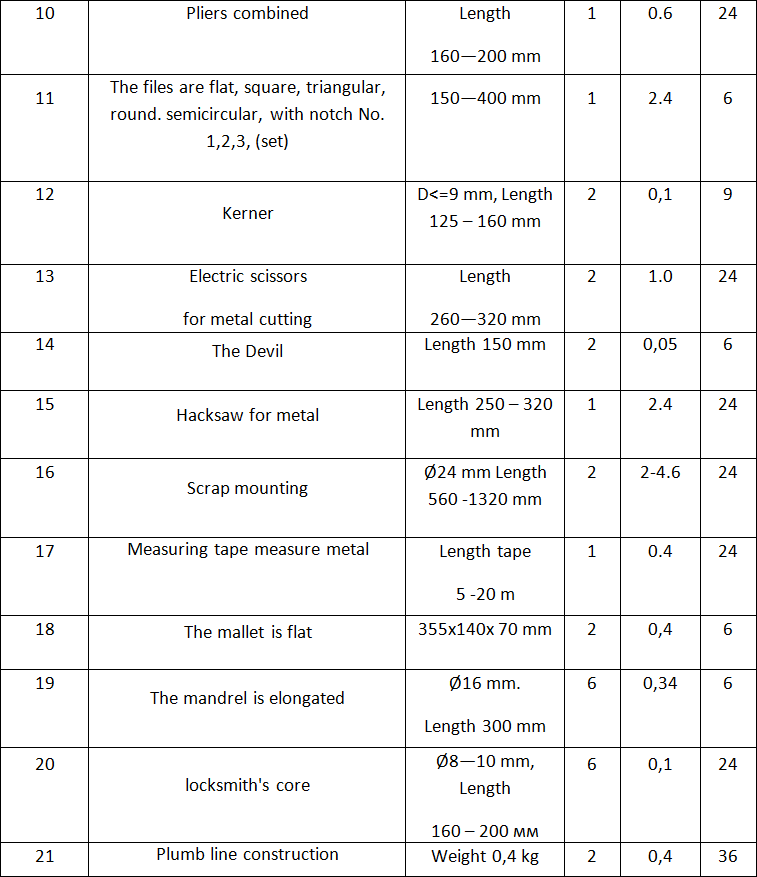
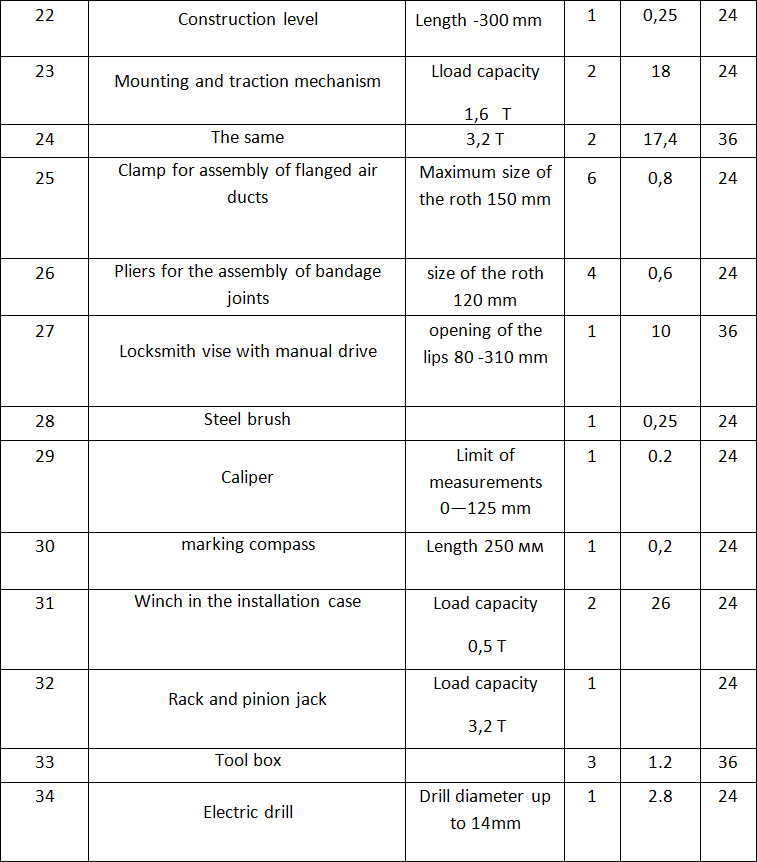
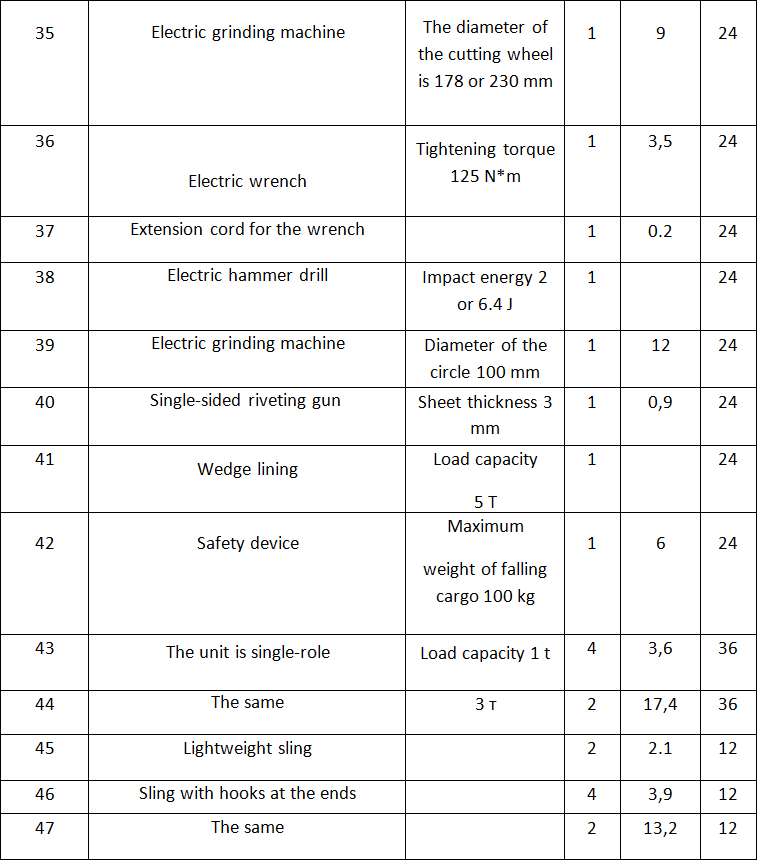
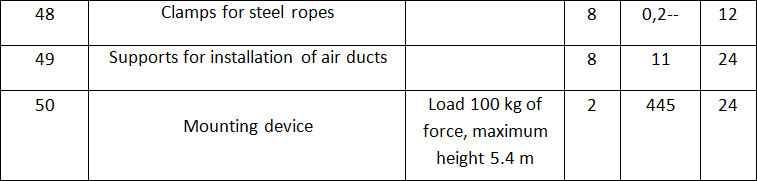
Table 6.2
Recommended set of electric welding equipment and tools for a team of locksmiths – ventilators
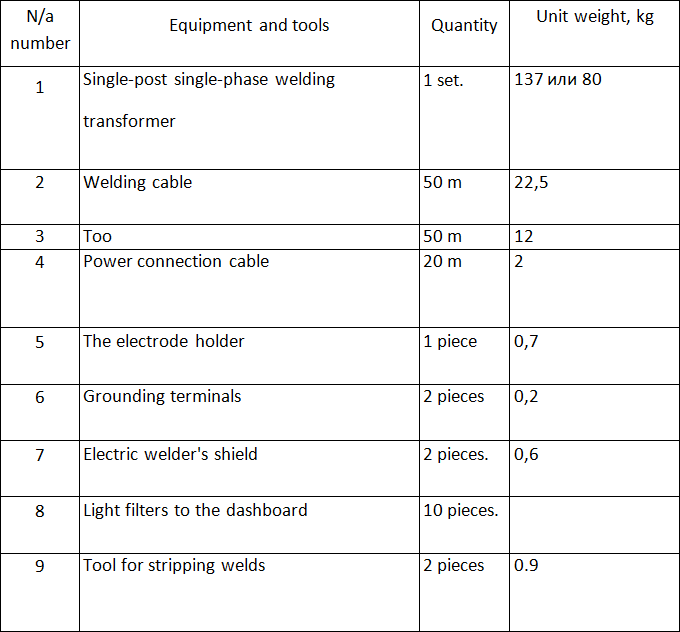
Table 6.3
Tools for gas cutting of steel
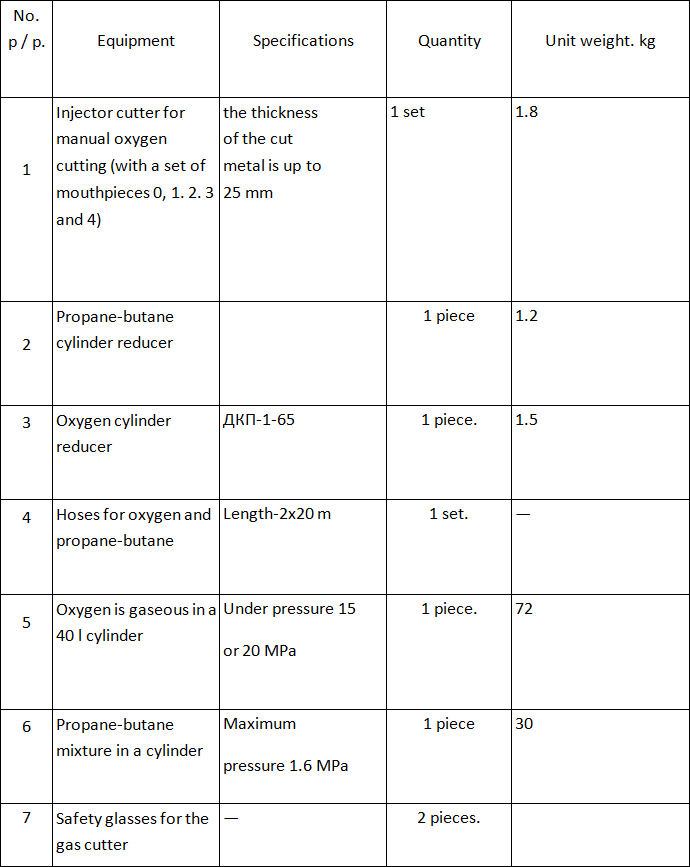
Table. 6.4.