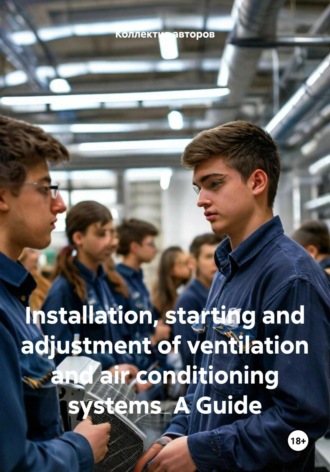
Полная версия
Installation, starting and adjustment of ventilation and air conditioning systems A Guide
We divide fans into three groups, depending on the magnitude of the total air pressure they create: low pressure (up to 1 kPa), the maximum circumferential speed of such wheels does not exceed 50 m/s; medium pressure (up to 3 kPa), the maximum circumferential speed reaches 80 m/s; high pressure (up to 12 kPa), the circumferential speed of the impellers is more than 80 m/s.
The separation of fans by pressure is conditional, since any high-pressure fan with a decrease in the speed of rotation can be used as a medium-pressure fan.
In the direction of rotation of the impeller (when viewed from the suction side), the fans can be of right rotation (the wheel rotates clockwise) and left rotation (the wheel rotates counterclockwise).
Depending on the composition of the transported medium and operating conditions, fans are divided into: conventional – for air (gases) with a temperature of up to 80 °C, corrosion-resistant – for corrosive environments, heat-resistant – for air with a temperature above 80 °C, explosion-proof – for explosive environments, dust-proof – for dusty air (solid impurities in the amount of more than 100 mg/m3). According to the method of connecting the fan impeller and the electric motor, the fans can be: with a direct connection, with a connection on an elastic coupling, with a V-belt transmission, with an adjustable stepless transmission.
At the place of installation, fans are divided into: conventional, mounted on a special support (frame, foundation, etc.), ducted, installed directly in the duct, roof, placed on the roof.
The main characteristics of the fans are the following parameters: air consumption (m3/h), total pressure (Pa), rotation speed – rotations per minute (rpm), power consumption spent on the fan drive (kW), EFFICIENCY – the efficiency of the fan, taking into account mechanical power losses due to various types of friction in the fan working bodies, volume losses as a result of leaks through seals and aerodynamic losses in the flow part of the fan, the sound pressure level (dB).
3.4. Supply installations
The supply units (Fig.5) filter fresh air, if necessary, heat it (in the cold season) and supply it to the duct system for subsequent distribution around the premises.
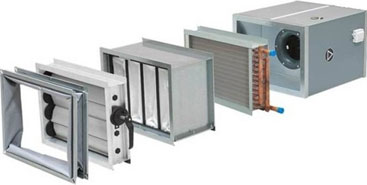
Fig.5. The supply unit
Inlet ventilation units consist of a housing in which are mounted: filter, water or electric heater, fan, automation system, sound insulation material,
Conditionally, Inlet installations can be divided into several types:
by type of heater (with an electric heater or with a water heater), by air consumption (up to 200–3000 m3/h – mini-supply installations, more than 3000 m3/h – central supply installations), by design (for vertical installation, for horizontal mounting, universal)
The automatic control system of the supply unit allows you to gradually or smoothly adjust the thermal power of the electric heater. If a water heater is used in the supply unit, then the automation has a more complex design, since in this case it is necessary to provide additional protection against freezing of the heater in winter.
In ventilation systems with supply installations, the following additional elements can be used: air intake grilles, a valve for supply air (with an electric drive or manual drive), mufflers, devices for adjusting air flow in rooms, air distribution devices (diffusers, grilles, plafonds).
Structurally, the chambers are a monoblock structure and can be equipped with automatic control of various levels of complexity from simple functions such as START, STOP, OPEN-CLOSE VALVE, to programmable control of parameters (room temperature, performance, temperature inside the chamber, etc.) along a continuous circuit.
The supply chamber includes the following elements:
A double-sided suction fan, which is attached to the frame traverses through rubber vibration isolators. The frame is made of aluminum profiles and connecting corners.
Insulated panels made of galvanized steel on the outside and inside. Foam insulation is laid in the panel as a heater and sound insulator. For tightness, a self-adhesive sealer is laid between the panels and the frame. On one side of the camera, for ease of maintenance, the panels are made quick-detachable, for which they are equipped with rotary clamps.
Heater (water heater or electric heating elements).
Soft insert made of rubberized fabric with flanges on both sides. The flanges are made of a galvanized tire connected by corners.
Quick-release air filter.
Insulated air valve with electric drive.
To create a balance of the incoming and outgoing air from the room, exhaust ventilation is used, which can be represented by:
• autonomous axial fans installed directly in the wall;
• roof fans installed on the roof;
• centrifugal fans mounted on brackets in the wall or on metal roof structures;
• duct fans in a shell-shaped housing or in a box-shaped housing installed in a network of air ducts (have a nozzle at the inlet and a diffuser at the outlet, and in the case of installing a two-way suction fan – two at the inlet and one at the outlet).
• exhaust ventilation units equipped with fans, flexible inserts, control valves and assembled in a single housing (Fig. 6).
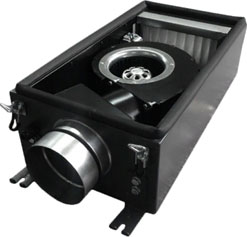
Fig.6 Exhaust system
Supply and exhaust ventilation systems can significantly reduce heating costs by using heat recovery. The heat removed from the room air can be used to heat the supply air in special heat exchangers called recuperators.
Such a system, using a cross-flow recuperator and made in the form of a monoblock, is characterized by a high efficiency of heat recovery, reaching 70%, and provides at least a twofold reduction in operating costs for air heating due to heat recovery (Fig.7).
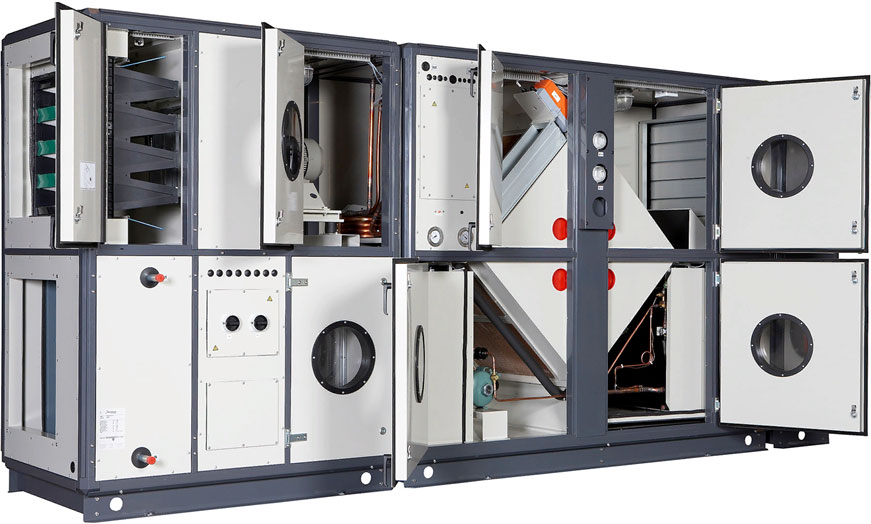
Fig.7. Supply and exhaust system with recovery
Heat recovery units are designed for the organization of supply and exhaust ventilation in comfortable air conditioning systems, i.e. they change the temperature and humidity of incoming fresh air taking into account the climatic conditions inside the serviced room.
The cross-flow plate regenerative heat exchanger is made of a heat-conducting material having the property of selective permeability with respect to water molecules (practically the membrane is impermeable with respect to molecules of other gases and substances). Due to this, the difference in the partial pressures of water vapor in the outdoor and exhaust air leads to the transfer of moisture from one stream to another. In the cold season, water molecules from the wetter exhaust air penetrate through the membrane into the outside air stream, humidifying it. In the warm season, water molecules from the wetter outdoor air penetrate into the exhaust air stream, preventing excessive humidification of the room.
3.5. Heaters
To heat the air in the supply ventilation units, heaters (air heaters) are used.
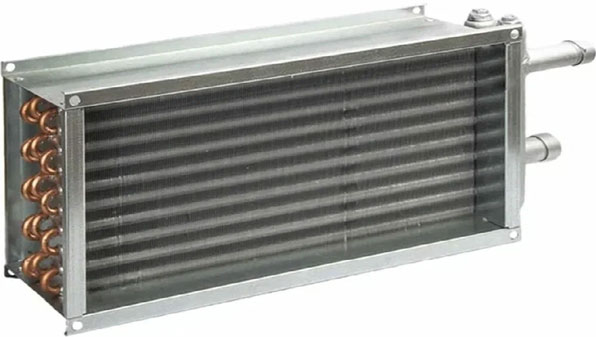
Fig.8. Water heater
High-temperature water or steam is used as a heat carrier for heaters. When the heating liquid is water, the heaters are marked as HW, when steam is marked as HS.
Heaters designed to work with a steam coolant are manufactured single – pass, with a water coolant-both single-pass and multi-pass. In single-pass heaters, the coolant passes through the entire bundle of tubes simultaneously from one collector to another, and in multi-pass collectors are separated by internal partitions that repeatedly change the direction of movement of the coolant, which increases the speed of water movement through the tubes and, as a consequence, increases the heat transfer of the heater. The connection of fittings in single-pass heaters is diagonal, and in multi-pass ones it is one-sided (Fig. 9).

Fig. 9. The flow diagram of the coolant in the heaters:
a – single–pass; b – multi-pass
Fins in the form of plates (plate heaters) or wound steel tape (spiral-wound heaters) are placed on the tubes to increase the contact area with the air passing through the heater. The outer fins are galvanized to reduce corrosion and better contact of the fins with the tubes. Fittings for the coolant are welded into the collectors, and to protect the fins from damage from the side, side shields are welded between the collectors. Flanges are used to connect the heater to adjacent elements of the ventilation system.
The arrangement of the tubes with the heating liquid can be consistent in the direction of air movement (corridor), staggered and offset along the corridor (most effectively). The tubes themselves can be either round or flat-oval in cross-section.
The best thermal engineering indicators have spiral-rolled bimetallic three- and four-row heaters for both steam (single-pass) and water (multi-pass) heater. The tubes for the heat carrier in these heaters are steel, the fins are rolled from aluminum.
Heaters are often grouped into several pieces, both with a parallel installation through the air, and with a sequential or combined one. If the heat carrier is steam, then the heaters are installed with a vertical arrangement of tubes and steam supply to the upper branch pipe; if the heat carrier is water, then the position of the tubes should be horizontal, which ensures the removal of air when filling the heaters with water and draining water from it when the system stops working.
Electric heaters are also available (Fig.10).
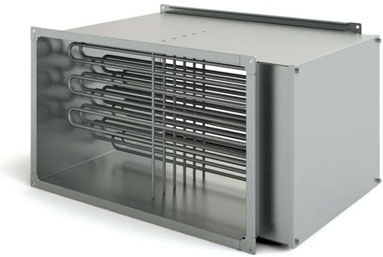
Fig.10. Electric heater
Electric heaters consist of a steel casing with tubular heating elements: 1.6 or 2.5 kW each. To increase the heating surface area, the heating elements have ribs with a diameter of 42 mm. Electric heaters can work both in manual and automatic mode, maintaining a constant temperature of the air at the outlet or in the room.
3.6. Duct heaters
The duct heater is used to heat the supply (outdoor) air in the ducts (conventional circular section). In central ventilation systems, duct heaters are used as auxiliary heaters, and in decentralized ones – as the main air heaters.
The heater body is made of galvanized steel. Air heating is carried out by heating elements. It is mandatory to have protective and regulating thermostats, which provides the product with high safety and the ability to function in automatic mode at the same time.
Channel heaters are equipped with two thermostats for overheating protection: heat-protective with automatic restart (operating temperature +50 °C) and fire-fighting with manual restart (operating temperature +110 °C). Channel heaters are designed for a minimum air flow velocity of 1.5 m/s and a maximum operating temperature of 40 °C of the outgoing air.
3.7. Air coolers
Duct air coolers (Fig. 11) are designed for cooling and dehumidification of supply, recirculating air or a mixture thereof in ventilation and air conditioning systems of industrial, public or residential buildings.
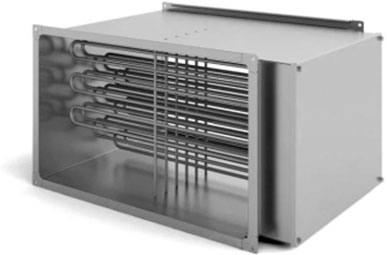
Fig. 11. Air cooler with ducted water and freon coolers
Water or non-freezing mixtures can be used as a refrigerant in ducted water coolers. The maximum allowable liquid pressure in them is 1.6 Mpa.
Freons are used as a refrigerant in ducted freon coolers. Upon delivery, the heat exchangers are filled with inert gas, which must be removed during connection to the refrigeration circuit.
The design of the cooler is a housing made of galvanized steel, inside which a heat exchanger, a drop trap and a pallet are installed.
The heat exchanger is made of copper tubes with aluminum fins arranged in a staggered order.
The freon cooler is distinguished by the design of the distribution unit ("spider") and the specifics of the refrigerant supply.
The collectors of the freon heat exchanger are made of copper tubes.
The drip trap (Fig. 12) is a set of special plastic plates that effectively trap condensate and collect it into a tray located in the lower part of the cooler body.
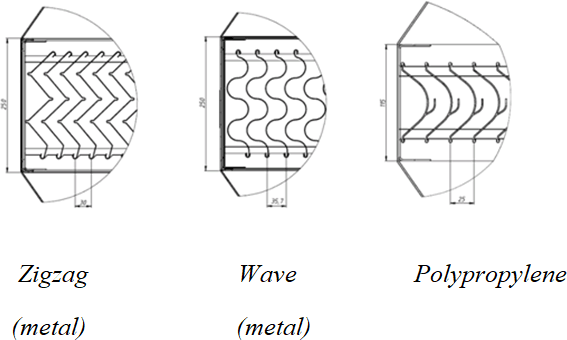
Fig. 12. The shape of the droplet trap plates.
The pallet is additionally thermally insulated and equipped with a discharge pipe for draining condensate
When installing the air cooler, it is necessary to ensure its horizontal position.
3.8. Filters
Filters are divided into three classes according to their effectiveness. Class I filters trap dust particles of all sizes (the cleaning coefficient is not less than 0.99), Class II filters – particles of more than 1 micron (cleaning coefficient is more than 0.85), class III filters – particles of more than 10–50 microns (cleaning coefficient is not less than 0.60).
3.9. Noise suppression equipment
The noise level generated by ventilation systems is an essential criterion of ventilation quality. The sources of noise in ventilation installations are fans and electric motors, as well as the movement of air in the ducts and its exit from the holes. Two types of noise are considered: aerodynamic and mechanical.
The reasons for the appearance of aerodynamic noise in fans are: the formation of vortices and their periodic disruption from the blades of the impeller, local air flows at the entrance to the wheel and at the exit from it, leading to unsteady flow around the blades of the wheel, perturbation of the medium by rotating blades. Mechanical noise occurs in bearings, in the drive, in the installation sites (fasteners) of the ventilation unit on building structures, etc. The degree of noise increases with insufficient balancing of the fan impeller.
Of all the sources of noise generation, the dominant ones are fans that create aerodynamic noise. The noise generated by the ventilation system can be reduced by the following measures: installation of fans with the most advanced acoustic characteristics, in particular, fans with blades bent backwards; the choice of fans with the highest efficiency (not less than 0.9 of the maximum), with a minimum angular velocity of the impeller (not higher than 30 m/s), i.e. fans with a small diameter of the impeller and a small number of revolutions (at the same time, you should not overestimate the pressure against the calculated one, since this causes an increase in noise level); careful balancing of the impeller.
Noise reduction along the path of its propagation is achieved by limiting the speed of air movement in the ducts or lining the inner surfaces of the ducts with a sound-proofing material.
In order to reduce the transmission of fan vibration to the ducts, the latter must be connected to the fan nozzles using soft inserts made of rubber, rubberized tarpaulin.
Vibration noise reduction is achieved by installing ventilation units on vibration isolators. Standard designs of spring and rubber vibration isolators are used (Fig. 13).
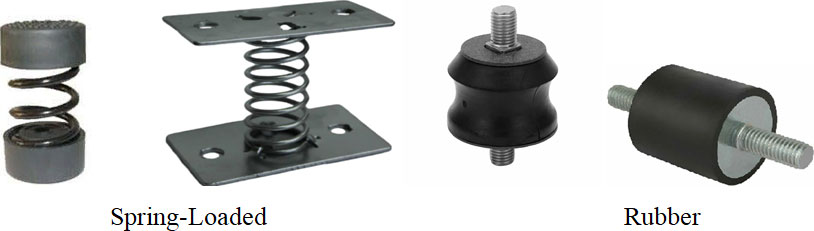
Fig. 13. Vibration Isolator
With the number of revolutions of the impeller up to 1800 rpm, it is recommended to use spring vibration isolators, characterized by stability of elastic properties, allowing large deflection and weakening vibrations even at very low frequencies. With large numbers of revolutions, the use of rubber vibration isolators is allowed.
In order to reduce the transmission of vibration to the structure of the building, fans should be mounted on their own concrete foundations on the ground. In the case of installation of ventilation units on the load-bearing structures of buildings, the plates or beams on which they are located must be mounted on vibration-absorbing supports.
The reduction of the noise level transmitted from the ventilation chamber to adjacent rooms is achieved by the installation of fences around it from structures with increased sound absorption, as well as the use of sound-absorbing linings in chambers and rooms. In ventilation chambers, it is possible to arrange "floating" floors consisting of layers of fiberglass plates, soundproof strips, etc.
. For active muffling of aerodynamic noise, mufflers are widely used in ventilation systems, the principle of operation of which is based on the conversion of sound energy into thermal energy by friction.
By their design, silencers are divided into tubular, honeycomb, plate and chamber silencers (Fig. 14).
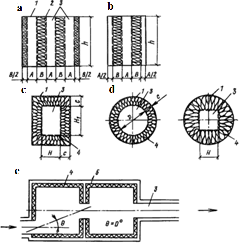
Fig. 14. Muffler designs
a – lamellar with extreme plates; b – lamellar without extreme plates; c – tubular rectangular section; d – tubular circular section; e – chamber;
1 – muffler casing; 2 – sound – absorbing plate; 3 – air channels; 4 – sound-absorbing lining; 5 – internal partition;
A – the distance between the plates; B – the thickness of the plates; H, Hx – the dimensions of the duct; C -the thickness of the lining of the duct; D – the diameter of the duct
By design, silencers are divided into tubular, cellular, plate and chamber.
Tubular silencers are made round, rectangular. Cellular and plate silencers are made only rectangular. As a sound-absorbing material, soft mats made of superfine fiberglass with a thickness of 100 mm are used for tubular and cellular silencers and with a thickness of 100, 200 and 400 mm for plate silencers. To prevent the entrainment of the fiber with the air flow, the sound-absorbing layer is protected with fiberglass and metal mesh or perforated sheets with a perforation of at least 20%.
The plate silencer is a box made of a thin metal sheet. A tubular silencer is made in the form of two round or rectangular pipes inserted into one another. Tubular silencers are used on air ducts with a diameter of up to 500 mm.
Currently, active silencers have been developed that carry out broadband active noise suppression (especially effective at low frequencies). Noise neutralization is carried out by introducing antiphase noise.
3.10. Check valves
Check valves are used to allow air to pass in one direction and prevent it from moving in the opposite direction. They are available in two of the simplest modifications: the "butterfly" type and the "inertial lattice" type (Fig. 15).
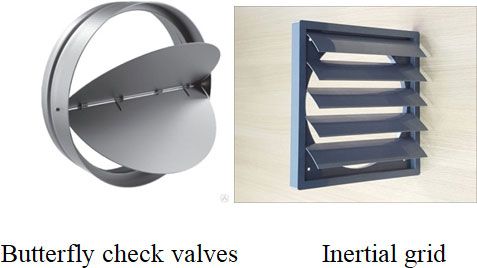
Fig. 15. Check valves
The butterfly valve is made of galvanized steel, has two spring-loaded lobes, and can be installed in any position.
A petal check valve of the "inertial grid" type with light plastic blinds inserted into a galvanized steel box can only be installed on horizontal air ducts, under the action of the air flow in the permitted direction, the petals rise, in all other cases they are lowered.
One of the main characteristics of check valves is the maximum possible air velocity.
Check valves are used to prevent air flow: when several supply units are operating on the same network; when installing a backup supply or exhaust fan; when connecting several exhaust systems to one exhaust shaft.
They are also installed to prevent backflow of air when exhaust air is released onto the facade or in front of roof fans.
3.11. Air curtains
Air curtains (without air heating) they are arranged between rooms with the same or similar thermal conditions. They are used to prevent access of air from some rooms in which harmful vapors or gases are released to others.
The principle of operation of air-heat curtains is as follows: air is taken from the upper area of the lobby, heated in heaters up to 50 °C, fed by a fan into the air distribution chamber and then released through the uniform distribution duct at the door. The air is discharged through cracks or holes in the duct. The resulting jet creates a vertical air curtain. The air can be released from the bottom at the door or from the side to the desired height. Air is supplied to the air curtain from the supply ventilation without additional heating.
According to the principle and effect of the curtain, there can be gate and mixing types. In the first case, the curtain maximally or completely prevents (blocks) air access to the enclosed space; the air velocity from the installation to create such curtains should be high (up to 25 m/s). Such curtains are arranged at low outdoor temperature and frequent opening of doors. In mixing type installations, the rushing cold air is mixed with the heated air of the heat curtain. As a result, warm air enters the room through the door and the curtain, which does not create a feeling of cold blowing.
Questions to Chapter 3
1. What is the reason for the location of outdoor air intake devices in ventilation systems?
2. Name the main types of fans by type and design.
3. What is the reason for the mandatory installation of the filter in front of the heat exchange equipment (heaters and coolers)?
4. Give an example in which cases it is advantageous to use electric air heaters.
5. What are the advantages of using water heaters?
6. Why the range of air velocity in heat exchange equipment is strictly limited?
7. What is the fundamental difference between water (water-glycol) and freon air coolers?
8. What measures are envisaged to reduce noise in ventilation systems?
9. Which device is used to prevent air flow when the fan is turned off?
10. In which places of the building are provided air heat curtains with heated air?
Chapter IV. Ducts and Fittings
4.1 Air ducts of ventilation systems
According to the type of section, the ducts are divided into round, square or rectangular. Circular air ducts are much stronger than rectangular ones, and their manufacture is less laborious.
However, circular air ducts often do not fit into the interior of public and civil buildings. In addition, in a confined space (under false ceilings, etc.), as a rule, only rectangular air ducts can be used.
According to the manufacturing method, the air ducts can be folded or welded. (Fig. 16.).
The first ones are connected with seam seams. The thickness of the metal for such ducts should not exceed 2.0 mm (if aluminum is used) and 1.0 mm (if corrosion-resistant steel is used).
The welded air ducts are connected by an overlap weld. The thickness of the metal with this type of connection is allowed in the range of 1.2 -3.0 mm.
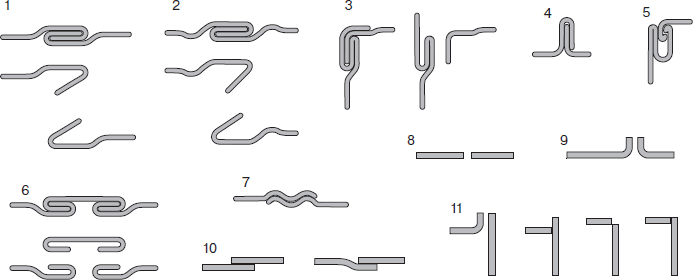
Fig.16. Types of seam and welded joints of metal ducts:
1 – on a simple recumbent seam; 2 – on a double–cut seam; 3 – on an angular seam; 4 – on a transverse seam; 5 – on a seam with a latch; 6 – with a connecting bar; 7 – on zigs; 8 – butt; 9 – butt–to–butt with flanging; 10 – lap; 11 – corner
This type of duct is classified as dense.
All the various ventilation systems are assembled from only four standard parts.
The first is pipes with a length of 2000 mm or 2500 mm, depending on the metal used.
The second is from water, usually consisting of two or three segments and two glasses with an average radius of curvature equal to the diameter (Fig.17). They are used for general exchange ventilation systems.
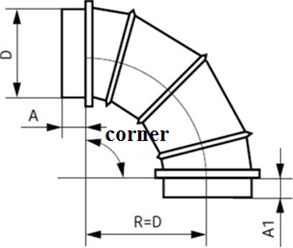
Fig. 17. Outlet for air ducts
The third is rectangular bends, which are characterized by only two neck radii: 150 mm (for bends with a side less than 1000 mm) and 300 mm (with a larger size).
The fourth is the tees (branch nodes) of circular cross section. They exist in 3 versions: