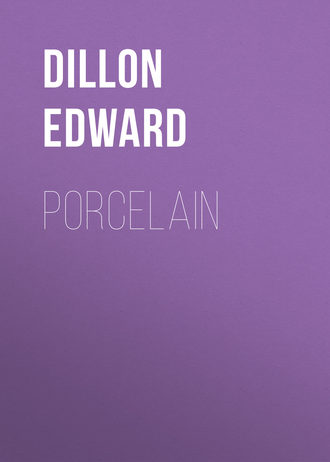
Полная версия
Porcelain
To return to our raw materials, which we may now suppose to be weighed out in a dry state in the required proportions. These are once more thoroughly mixed with water to form the slip or barbotine, which is again passed through a fine sieve. To remove any particles of iron which may have come from the machinery or elsewhere, and which if allowed to remain would form unsightly stains on the finished ware, it is usual to pass the slip at this stage through a vessel in which a number of horse-shoe magnets are suspended. In some of the large French factories a more complicated machine is used for this purpose. The superfluous water has now to be removed either by evaporation or by pressure between canvas bags in the manner described above. The paste may then be passed through a pug-mill to render it uniform in consistency.
A curious question arises with regard to the prepared clay. There was formerly a widespread idea, which may contain an element of truth, that instead of handing the clay at once to the potter, it should be kept, under certain conditions, for a long space of time that it may undergo a process of ‘aging’ and fermentation. By the ‘aging,’ the working qualities, especially of a ‘short’ or non-plastic paste (such as that in use at Sèvres in the eighteenth century, in making the pâte tendre), were doubtless increased, the more so when the clay was at intervals subjected to fresh kneading and watering. With regard to the long periods for which the clay was kept by the Chinese, the most exaggerated statements were formerly made. Mr. William Burton is of opinion that there may be in some cases an evolution of carbonic acid and sulphuretted hydrogen when natural plastic clays are used, for these may contain both vegetable remains and small quantities of iron pyrites. But the change, he thinks, is chiefly a physical one, due to the settling down of the mass. Might there not also, I would suggest, be a change of a more intimate nature, due to the formation of gelatinous silica and perhaps also of fresh alkaline or other silicates, among these minutely comminuted particles of various materials now freshly brought together? We know very little of the conditions that give to natural clays their peculiar unctuous quality and their plasticity.
We come now to what has been called the ‘shaping’ of the clay, using that word as an equivalent to the French façonnage to include all the processes, throwing on the wheel, turning of the lathe, ‘pressing’ and ‘casting,’ by which the desired form is given to the vessel.
The Potter’s Wheel, perhaps the most ancient of all mechanical contrivances, is still largely used in the shaping of porcelain, and that, too, in a simple form which differs little from that employed three or four thousand years ago in Egypt,10 and perhaps for nearly as long a period in China. From an æsthetic standpoint, the wheel holds the same relation to the art of the potter as the brush does to that of the painter. It is perhaps a just cause of reproach against that branch of the ceramic art with which we are now concerned, that so comparatively little use is made of the potter’s wheel. Not only in Europe, but for long ages in China also, the use of the wheel, for many classes of vessels, has been replaced by various processes of moulding. With us, but not in the East, a third process, that of ‘casting’ with liquid slip, is largely used. But when made either by casting or moulding, the hand of the potter is not seen in the shape of the finished vessel. By means of the wheel alone do we get the full expression of the peculiar qualities of a plastic material. This was recognised by the Greeks, when the potter who made the vase signed his name by the side of the painter who decorated it. This it is that gives a certain charm to the roughest earthenware which we may look for in vain in the most elaborately decorated specimen of either Chinese or European porcelain.
The clay as it comes from the filter-presses or from the drying-beds is subjected to a series of kneading processes to ensure uniformity of texture. The last of these is the ‘slapping,’ when the clay is made up into hollow balls, and thrown vigorously on to a board until all bubbles and irregularities of texture are removed.
The thrower’s wheel is essentially a revolving vertical spindle, with a small round table at the top, beside which the thrower sits. The clay is handed to him in balls, and he throws it upon the whirling table between his knees. The table is put into motion either directly by the pressure of the workman’s foot on a lower table, or by some arrangement of straps and pedals. If the movement is given by the potter himself, as is still the case at Sèvres, and to some extent in China, there is the advantage that a more delicate and intimate control of the speed is possible. The movement of the clay under the potter’s hand is instinctively regulated by him. Every one has seen and marvelled at the wonderful process. The clay is first drawn up into a pillar, and then depressed into a flat cake, so that the circular arrangement of the particles may spread through the whole mass. The thrower then opens the hollow of the vessel with his thumbs, and proceeds to give it the desired shape, moistening his hands at intervals by dipping them into the slip. Small pieces are shaped between the thumb and first finger, either of one or of both hands. For larger pieces the whole hand and wrist is called into play, with the assistance, it may be, of a sponge. Still larger vessels are built up by piling on to the circular edge as it revolves strips of the clay. Delicacy of hand is of the greatest importance—the pressure applied and the movements of the fingers must be regulated by the nature of the clay, and especially by its greater or lesser plasticity. It is essential that the workman should not only press evenly and steadily on the clay as it rises, but that the speed of the rotation should have a definite relation to the rate at which he raises his hands. With a ‘fat’ or unctuous clay especially any irregularity of pressure will betray itself, and the marks will be more prominent after firing. This is the origin of the spiral ridges that we often see on the surface not only of common earthenware, but sometimes of high-class porcelain. To this cause are due the rings so characteristic of Plymouth porcelain; this ‘wreathing’ or ‘vissage’ is sometimes seen on Chinese porcelain also.
When the thrower has finished his vessel, it is cut off from the table by a piece of thread or by a brass wire, and taken to the stoveroom to dry and harden. When sufficiently dry the vessel is placed on a lathe, and the turner shaves off all superfluous clay. The finer mouldings (using the word here in its architectural sense) may also be given at this stage, and sometimes the surface is shaped by a ‘profile’ of steel (it may be a piece from the blade of an old saw), which cuts the surface down to the desired shape. The shavings are carefully preserved and returned to the slip-house, to be blended with the new clay, the working qualities of which are thereby improved.
There are certain parts, especially handles, spouts, and projecting ornaments, which must in all cases be separately moulded. The foot also, in the case of large vases, is separately prepared and subsequently attached. These parts are made in plaster moulds by the ‘handler,’ whose duty it now is to fix them to the vase. Carefully marking the exact place, he spreads on it a thin layer of slip with a spatula, and then presses home the handle or other appendage. Should, however, the two surfaces be dry and absorbent, it may be necessary to add some gum to the slip thus employed. A similar process, but one requiring greater care and skill, is that of fixing together the separate pieces of large vases and figures. This is done in the way we have already described in the case of the handles and spouts—that is by applying a coating of slip to the parts to be joined.
It is at this stage that any decorations in relief that may be required are applied to the surface. These are often made in flat moulds, and to fix them it is enough to run a little water from a camel’s hair pencil behind the ornament after adjusting it to its proper place. These processes of fitting on of appendages and ornaments are included by the French under the term garniture.
Moulding and Pressing.—It is evident that only vessels of a cylindrical or conical form, or, more exactly, such as have a circular section when divided horizontally, can be formed on the wheel. To produce any other form, the vessel must be either shaped directly by the hand or made in some kind of mould. The use of moulds for pottery is as old, if not older than that of the wheel. It was in this way that the Ushabti figures of the old Egyptians were made, and many of these date back to the Early Empire. So in China, the further back we go, the more the use of moulds seems to have prevailed. I take from the excellent article on the manufacture of pottery in the Penny Cyclopædia the following account of the process in use in England at the beginning of the last century:—
‘The mould is made in two parts, and each is separately filled by laying in a cake of clay which has been beaten out to the proper thickness on a wet plaster-block; it is pressed into the mould by repeated blows from a ball of wet sponge, then squeezed into all the angular parts and smoothed with sponge, wet leather, and horn. When both sides of the moulds are thus lined with clay, they are joined together, and the man lays a roll of clay along the inside of the joining, which he works down until the whole is smooth and solid.’ The mould is then carried into a stoveroom, and the plaster here absorbs the moisture so as to release the clay. The contents are carefully taken out, and the empty mould returned to the stove previous to being filled again. The seam that remains on the outside of vessels after fitting the two parts together11 is removed by scraping and burnishing with wet horn; the handles and other appendages are then attached.
This is the process that is called ‘hollow-ware pressing’ or ‘squeezing.’ In ‘flat-ware pressing’ the mould is used to give the shape to the inside of the vessel only. The mould is placed on the extremity of the ‘whirler,’ a vertical revolving spindle provided with a circular table, similar to that of the thrower’s wheel. The plate-maker takes a cake of clay, which he has previously flattened out with his ‘batter,’ places it on the mould, and presses down with his hand. The upper surface of the cake of clay (what will ultimately be the bottom of the plate) is now shaped by an earthenware ‘profile.’ The mould is now taken off the whirler and at once replaced by another. Flat-ware, especially when greater finish is required, is also made in a double mould, and the clay may then be first thrown on the wheel so as to approximate to the shape required before being placed in the mould.
Processes very similar to the hollow and flat-ware pressing are largely used by the Chinese. Dr. Bushell has unearthed a passage from a technical work, written in the time of the Chou dynasty, more than two thousand years ago, in which a distinction is made between the ordinary potters who worked with the wheel, and the moulders who made oblong bowls and sacrificial dishes. In a somewhat later work (19-90 A.D.) the writer notes both the advantage resulting from regularity of size, and the obstacles arising from the shrinkage of the parts in firing, when vessels are made in moulds.12
Casting.—There is yet another process which is largely resorted to in European works, but which appears to be unknown to the Chinese. It depends upon the rapidity with which dry plaster of Paris will absorb the water from a slip of creamy consistency, without allowing any of the solid particles to pass along with the water absorbed. The slip-mixture is poured into the plaster mould, which at once absorbs the water, leaving a uniform deposit upon the surface of the mould. After pouring or otherwise drawing off the water, a second and thicker slip may be added so as to form a second layer. The paste of the porcelain so prepared is likely to be of a lighter and more porous consistency than when made by throwing or pressing. This process was used in the eighteenth century at Derby, and doubtless elsewhere, and it was preferred to moulding for making statuettes. Some account of it is given by Haslem, a good practical authority, in his Old Derby China. For small objects, ‘casting’ has long been employed in France, and more lately Ebelmen and Regnault have so improved the process, that vessels of all shapes and dimensions are made by it. This has been rendered possible by the introduction of compressed air into the interior of the vessel, by which means the paste is kept in position until it is sufficiently dry to support itself. A still better way of doing this is to exhaust the air on the outside, by placing the mould in an air-pump; the upper part can then be left open, and the whole operation is under the eye of the workman. M. Vogt (La Porcelaine, pp. 157 seq.) laments that in France the increased use of these mechanical processes had so reduced the demand for skilful potters, that the race is nearly extinct.
Firing and Furnaces.—So far in our treatment of the operations involved in the manufacture of porcelain, the same general description has been applicable, with trifling exceptions, to the processes in use both in Europe and in the far East, and to soft as well as to hard paste. But now that we have to describe the firing of the ware, a division into three classes is necessary:—
1st. The Chinese system. This is the simplest plan. The glaze is applied at once to the air-dried ware, which is then subjected to but one firing—that of the ‘grand feu.’
2nd. The French system for hard paste. The unglazed vessel is exposed to a heat varying from dull to full red, generally in the dome over the main body of the furnace. It is then glazed, and again fired to the full point required by the paste. This is essentially a French process, and the preliminary fire is known as the feu dégourdi.
3rd. The English system used for bone pastes. In this case it is the first firing that is the most severe. The ‘biscuit oven,’ therefore, in which this is effected, must not be confused with the feu dégourdi just mentioned. After dipping, the ware is heated again in the ‘glozing’ or glazing oven, but only to a temperature sufficient to melt the glaze.
In the case of ware decorated with enamel colours over the glaze, there will be required in all these cases one or more additional firings at comparatively low temperatures in the muffle-stove.
The furnaces, ovens, or kilns in which porcelain is fired are always of the reverberatory type; that is to say, the fuel is burned in a separate chamber or fireplace, and the products of combustion pass over or among the ware that is being fired. Such furnaces differ on the one hand from the arrangement in a blast furnace, or that often used in the burning of bricks, where the fuel is mixed with the material to be heated, and on the other hand from the muffle-stove, where the object exposed to the heat is protected from the direct flame by the box of fireclay or iron in which it is placed.
Kilns of many shapes and sizes have been used for firing porcelain, but they may most of them be included in one or the other of the following broad classes.
1st. The old bee-hive ovens of China, the use of which appears to have been abandoned in that country by the end of the seventeenth century. These ovens were generally small, in some cases only holding one vase. A row of them may be heated from one fireplace, and they are then built on a rising slope. This type has survived to the present day in Japan.
2nd. The oblong horizontal furnaces, often of considerable dimensions, used during the present dynasty in China. They resemble in section the ordinary type of reverberatory furnace found in metallurgical works. A very similar form was long employed at Meissen.
3rd. The large conical furnaces, now in general use in the porcelain factories of Europe. They may be heated by either direct or by reversed flame.13
In China the fuel is generally pinewood, in billets of uniform size. In many European kilns wood is still used: birchwood, cut in lengths of fifteen to twenty inches, is the only fuel used at the present day at Sèvres. In England, however, the difficulties attendant on the use of coal appear to have been overcome.
The reader will find in the third volume of Brongniart’s great work (Traité des Arts Céramiques, Paris, 1877) several plates giving plans and sections of all these types of furnaces. From a careful examination of these engravings more is to be learned than from any amount of verbal description. A thorough grasp of the process of firing is of the greatest assistance in understanding the problems and difficulties that arise in the manufacture of porcelain, and we shall have to return to the subject when we come to treat of the several wares.
Whatever differences there may be in the shape of the furnaces, when it comes to filling the interior with the ware to be baked, there is one precaution which has been adopted in nearly every country.14 The ware must be protected from the direct heat of the flame by means of a case of fireclay in which it is placed. These are the seggars (French cassettes; the process of filling and arranging them is called encastage), to the preparation of which so important a department has to be set apart in all porcelain works, and whose manufacture adds so much to the working expenses.
The seggar proper is a cylindrical pan of fireclay, in shape and size like a hatbox. They are piled, in the furnace, one over the other, and these piles or ‘bungs’ are arranged in the furnace so as to allow a free circulation of the hot gases between them, but otherwise they are packed as closely together as possible. These seggars may be used several times over. When broken, the fragments are ground up and mixed with fresh fireclay or argile-plastique to form new cases—without this addition the clay would be too plastic or ‘fat’ for the purpose. The greatest precautions are taken in the packing of the seggars in the furnace. The giving way of one pile from any inaccuracy in the arrangement may destroy the contents of the whole oven. So again infinite care must be taken in the arrangement and support of the objects in each seggar. The bottom is covered with ground flint or other infusible material, and the vessel is supported, when necessary, by various forms of struts, props, or crow-claws, which sometimes leave their mark on the base or side of the finished object. In spite of these precautions, a large quantity of defective pieces or ‘wasters’ are produced in all works, and these are usually cast aside. The finding of such fragments in after days is sometimes the only proof we have that porcelain or pottery has formerly been made at the spot. But the proof is final, for defective pieces and ‘crow-claws’ are not objects likely to have been imported from a distance. Again, the indelible marks left on the porcelain, either on the edge which rested directly on the seggar or at the points where the object was supported by the crow-claws, often give valuable hints as to the provenance of the piece in question.15 In the case of valuable wares these rough edges and marks are removed as far as possible by grinding on a small wheel, and then polishing the surface with pumice or with putty.
CHAPTER III
GLAZES
BEFORE attacking the somewhat complicated subject of the nature and composition of glazes, it will be well to take up again the thread of the mechanical processes that are involved in the making of a piece of porcelain.
The materials that enter into the glaze are reduced to the finest powder in mills similar to those in which the china-stone and flint are ground for the preparation of the paste. If any substance soluble in water, such as borax or salts of the alkalis, enter into the composition of the glaze, these must be first partially fused in combination with the other materials to form a frit, a kind of imperfect glass. These frits, which enter so largely into the composition of soft-paste porcelain, are formed with the object of bringing the soluble constituents into an insoluble form before mixing with water to form the slip. There are indeed other practical reasons that render a preliminary partial fusion desirable.
The finely ground elements of the glaze, mixed in due proportion, are worked up with water to form a creamlike slip into which the vessel to be glazed is now dipped. In China, in many cases, the glaze-slip is blown upon the surface in the form of a spray. This is done by means of a bamboo tube, covered at one end by a piece of silk gauze, through which the liquid is projected by the breath of the operator (French, insufflation); in other cases the glaze may be painted on with a brush. In China, as we have mentioned, the glaze-slip is generally applied to the raw surface of the thoroughly dried but unbaked ware, but in other countries there is, almost without exception, a preliminary firing of greater or less degree to produce a biscuit.
We shall restrict the use of the word glaze to the vitreous coating applied directly to the surface of the raw paste or of the biscuit to enhance the decorative effect of the ware, and with the more prosaic object of allowing the surface to be easily kept clean. In the case of porcelain this coating is always more or less transparent.16 There is here no necessity for concealing the natural white colour of the paste. In the case of many kinds of pottery, however, as in the ‘enamelled fayence’ of Delft and Italy, the glaze is rendered opaque by the addition of oxide of tin, so that the ill-favoured ground is concealed by a white shiny surface which may be made to resemble closely the natural surface of porcelain. A glaze of this kind is often called an enamel, but as we are not concerned with such an expedient we shall confine the use of that word to the various forms in which a vitreous decoration, whether translucent or opaque, is superimposed upon the glaze and fused into it, more or less thoroughly, by a subsequent firing in a muffle furnace.
The English word ‘glaze’ is only another form of the word ‘glass,’ and we may say at once that, in composition at least, there is often little difference between the two substances. The French word for ‘glaze’ is couverte or vernis; the last term applies well to the thin skin of glaze found on Greek pottery. The Chinese have several expressions, but it is a curious fact that the characters with which most of these terms are written contain the radical for ‘oil,’ and indeed the word ‘oil’ itself is often used in the sense of ‘glaze.’
Mr. Rix puts it well when he says that the glaze is to the enameller of porcelain what his canvas is to the painter; while in the case of a decoration ‘sous couverte,’ the glaze corresponds to the varnish which, while protecting his work, gives brilliancy to the colouring (Journal of Society of Arts, vol. xli.). It is, moreover, the vehicle by which the design is harmonised and rendered mellow. The effect is produced at once and endures practically for all time.
The hardness and fusibility of glazes differ widely, and they are conditioned by the nature of the wares that they cover. It is evident that there must be a close relation between the fusing-points of paste and glaze, and that the latter should be the more fusible of the two. The difference of melting-point should, however, not be too great. The melted glaze should rather, by penetrating into the already softened paste or by a chemical action upon its surface, form a more or less uniform mass with it. In cooling, the contraction of the glaze should follow that of the subjacent paste. This is a most important point; any discordance may lead to splitting, cracking, and ‘crazing.’
The beauty of the surface of porcelain depends on the fact that the glaze has become intimately united with the paste during the long exposure of both to a high temperature. We should not be conscious, in regarding a fine specimen of porcelain, of a greater or less thickness of glass covering an opaque substance; we should rather see in it the polished surface of ivory or of some precious marble.