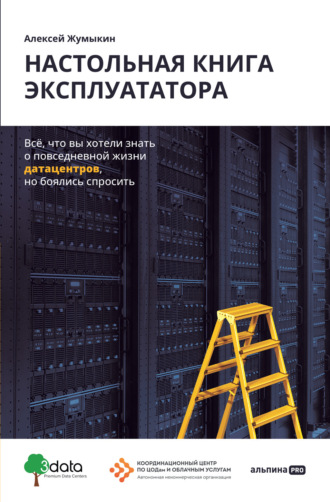
Полная версия
Настольная книга эксплуататора. Всё, что вы хотели знать о повседневной жизни датацентров, но боялись спросить
Как таковой программы тестирования на этой стадии нет – достаточно, чтобы команда эксплуатации участвовала в общих обсуждениях проекта и в окончательном выборе конкретных типов оборудования.
В то же время этот этап в проекте используется для настройки взаимодействия между участниками, оформления документов и подготовки скриптов (программ) тестов, как показано в таблице далее.
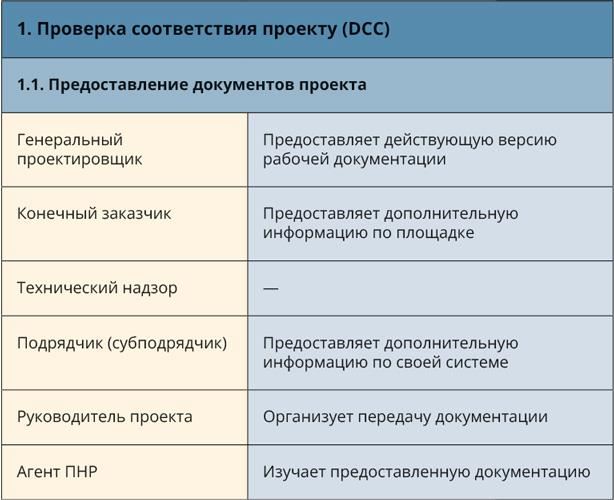
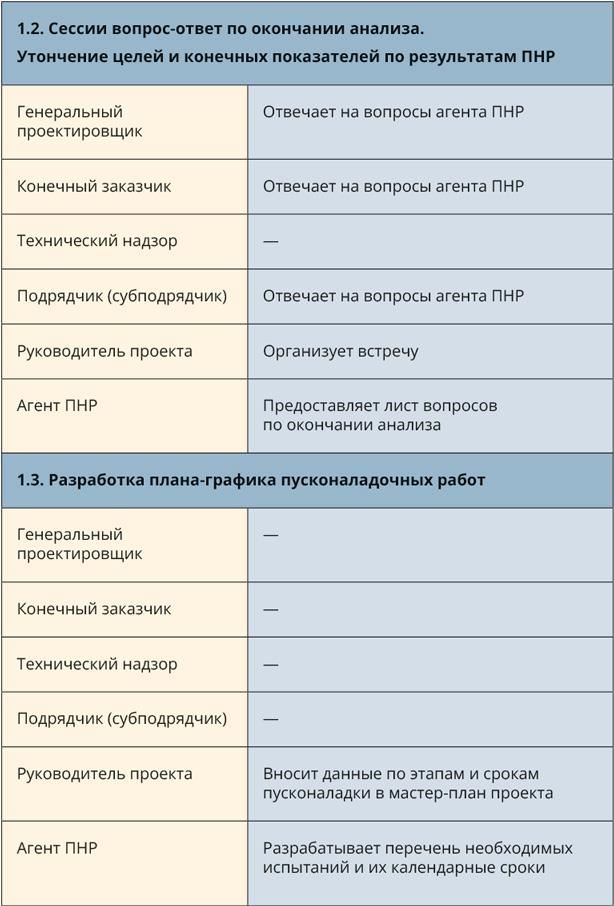
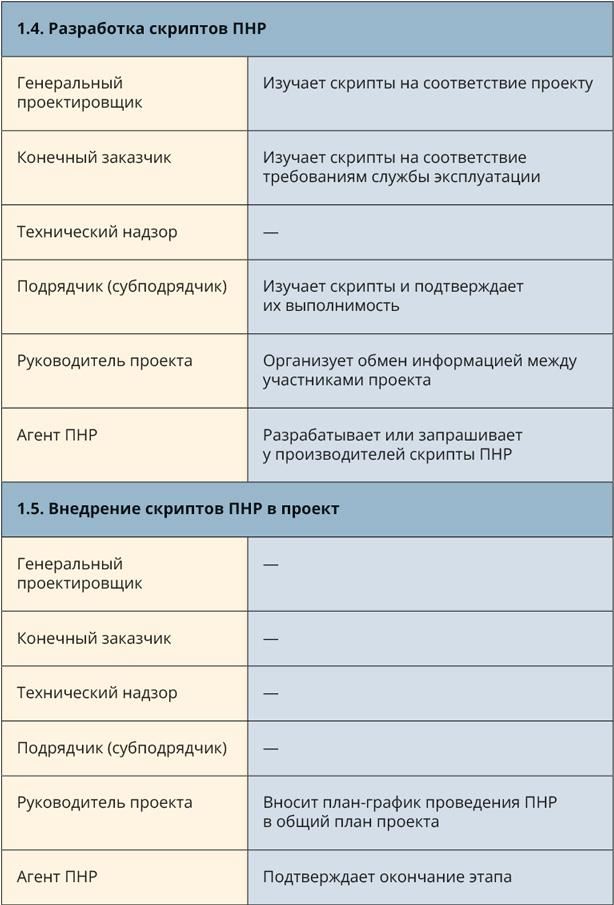
2. FAT, FWT[15] (Factory Acceptance Test, Factory Witness Test) – заводские испытания оборудования
Основная задача на этой стадии – убедиться в том, что оборудование обладает заявленными характеристиками и покинуло завод пригодным для дальнейших монтажа и эксплуатации.
Обычно компании-производители используют свои собственные программы для заводских тестов, которые в случае визитов представителей заказчика могут быть даже существенно упрощены. Для команды эксплуатации особенный интерес могут представлять так называемые type tests – расширенные испытания, которые проходят не все собранные единицы, а только несколько из партии, или самые первые образцы, если речь идет о новой модели. Ведь именно на таких тестах выбранные единицы оборудования проверяются в по-настоящему пограничных условиях, а остальная партия таким тестам не подвергается. Поэтому имеет смысл напроситься к производителю именно на подобное тестирование, даже если это и не те экземпляры, которые поедут именно к вам. Часто производитель не возражает против участия заказчика в таких тестах, если ему обоснованно разъяснить, зачем это нужно.
Программу FAT стоит запросить у производителя сразу после покупки оборудования (а иногда даже еще во время тендера), также следует разобраться в каждой строчке: зачем этот тест делается, что именно проверяется? После этого нужно принять решение, стоит ли ехать на завод. Чаще всего – да, ведь это не только первое знакомство с новым оборудованием, но и прекрасная возможность лучше понять культуру производства, разобраться в его особенностях, а также познакомиться не только с продавцами и маркетологами, но и с настоящими инженерами производства. Последним можно напрямую задать интересующие вас вопросы, ответы на которые иногда содержат такую информацию, которую маркетологи могут не знать или даже специально скрывать. Это отличный и при этом сравнительно недорогой способ профессионального обучения. Между нами скажу, что иногда получалось упросить инженеров на производстве провести тестирование, которое не входило в стандартную программу испытаний и вряд ли было бы одобрено отделом продаж производителя, но было важно с точки зрения заказчика, а с профессиональной точки зрения интересно и самим инженерам на производстве.
Еще одной важной причиной посетить завод и посмотреть свое новое оборудование является заблаговременная проверка качества маркировки, компоновочных решений и монтажа, особенно если речь идет об уникальных продуктах, таких как ГРЩ (главный распределительный щит), собранный под конкретного заказчика. Когда инженер эксплуатации, зная, что ему предстоит ежегодная протяжка болтовых соединений шин, прямо на заводе берет гаечный ключ и пытается их подтянуть, он сразу может оценить, и какой ему понадобится инструмент, и можно ли вообще дотянуться до нужного болта. Кстати, совершенно не исключаются варианты, когда представитель заказчика еще на заводе наткнется на недостаточный момент затяжки.
Другой повод для визита находится где-то посередине между упомянутыми DCC и FAT. Когда оборудование изготавливается впервые, например по ТЗ заказчика, то имеет смысл приехать на так называемый pre-FAT, чтобы убедиться, что мелочи, которые невозможно было сразу разглядеть в документации на новое изделие, не помешают качественно эксплуатировать оборудование. Для примера приведу случай, когда изготовитель установил контрольный прибор на высоте около 2,5 м, и для снятия показаний была нужна лесенка. Или рама вент-установки, на которой крепились фильтры, имела недостаточную жесткость и при работе вентиляторов прогибалась бы под напором воздуха. Такие мелочи рано или поздно были бы обнаружены, но устранить их, пока оборудование еще на заводе, – гораздо быстрее, дешевле, да и правильнее.
Подводя итог, если есть возможность съездить на производство – нужно ехать. В любом случае такой визит приведет к появлению новых идей, что в нашем инженерном мире, наверное, самое главное. Если же такой возможности нет – ее надо организовать…
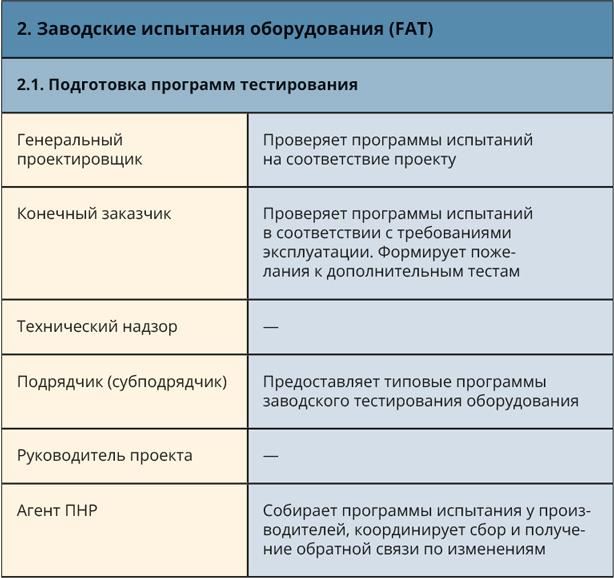
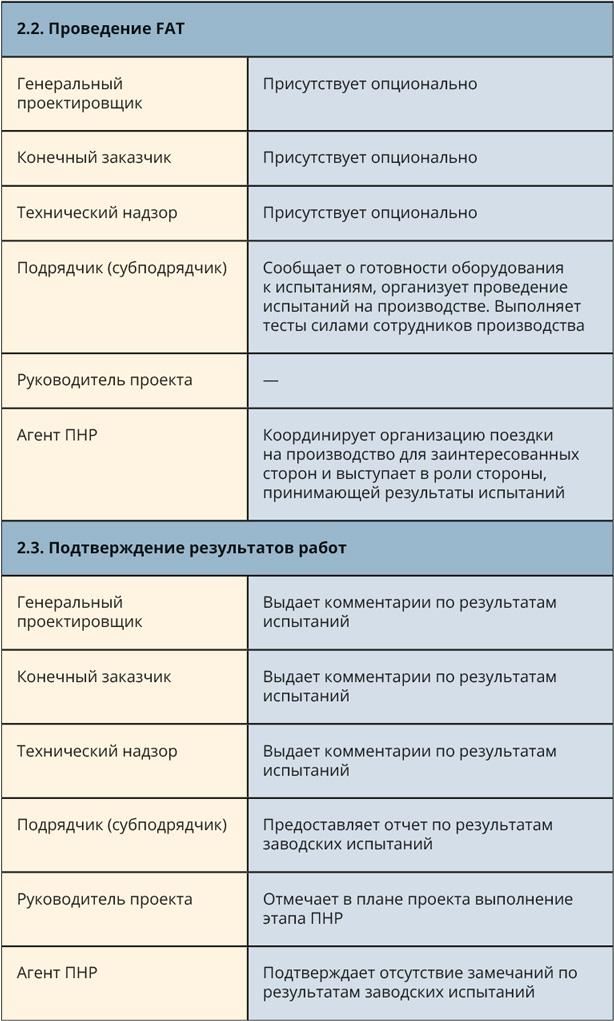
3. IA (Installation Acceptance) – приемка монтажа
После того как оборудование доехало на площадку и было установлено в помещении, включать его еще рано. Сначала нужно убедиться, что оно смонтировано именно в проектном месте и такая установка соответствует отраслевым нормативам (тут неоценимую помощь окажет специалист по техническому надзору, лучше всех разбирающийся в тонкостях СНиПов и подобной документации) и требованиям производителя. Внимательный осмотр позволит найти даже мелкие повреждения, убедиться в полной комплектности поставки и уже на своей территории еще раз удостовериться, что нет никаких проблем с дальнейшей эксплуатацией, например что все органы управления, контроля и регулировок легко доступны.
В одной из команд, с которыми мне приходилось работать, был специалист-слаботочник, до того дотошно контролировавший шкафы управления, что вручную проверял каждый, да-да, каждый проводок – хорошо ли он зажат в разъеме. Зато именно такой подход дает бóльшую уверенность, что в ближайшее время в этих местах соединений не проявится дребезг контактов.
Подробной программы таких испытаний обычно нет ни у производителя, ни у монтажников. Исключением, наверное, являются большие производители дизель-генераторных установок, скрупулезности проверочных документов которых можно только поражаться. Для другого оборудования программу придется составлять агенту пусконаладки. Важно не забыть заблаговременно согласовать ее с монтажниками, чтобы они знали, к чему готовиться, и заранее устраняли досадные мелкие недочеты, чтобы сберечь время в проекте.
Приемка монтажа – самый «дружелюбный» тест в том смысле, что на этом этапе очень многое может быть временно прощено поставщику (некомплектность, отсутствие маркировки и т. п.) и оборудование может быть допущено к следующим шагам тестирования. Однако тщательный подход к проведению ПНР обязывает зафиксировать все найденные неисправности и по каждой из них проставить время исправления.
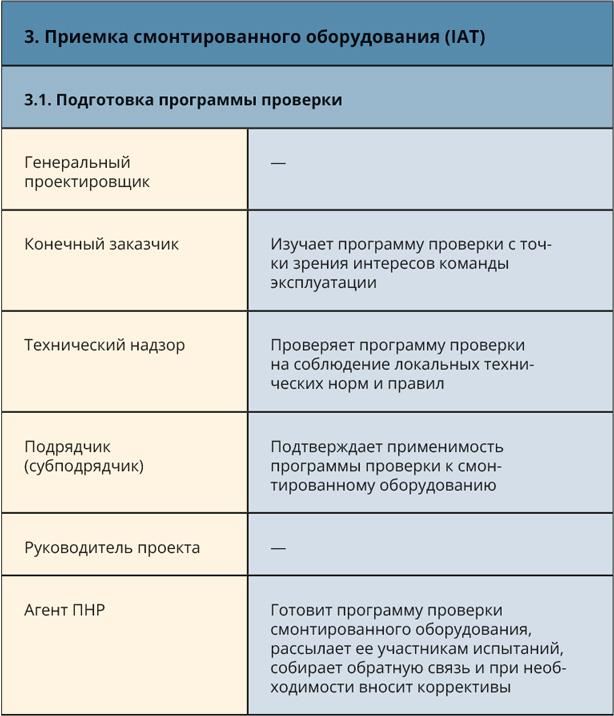
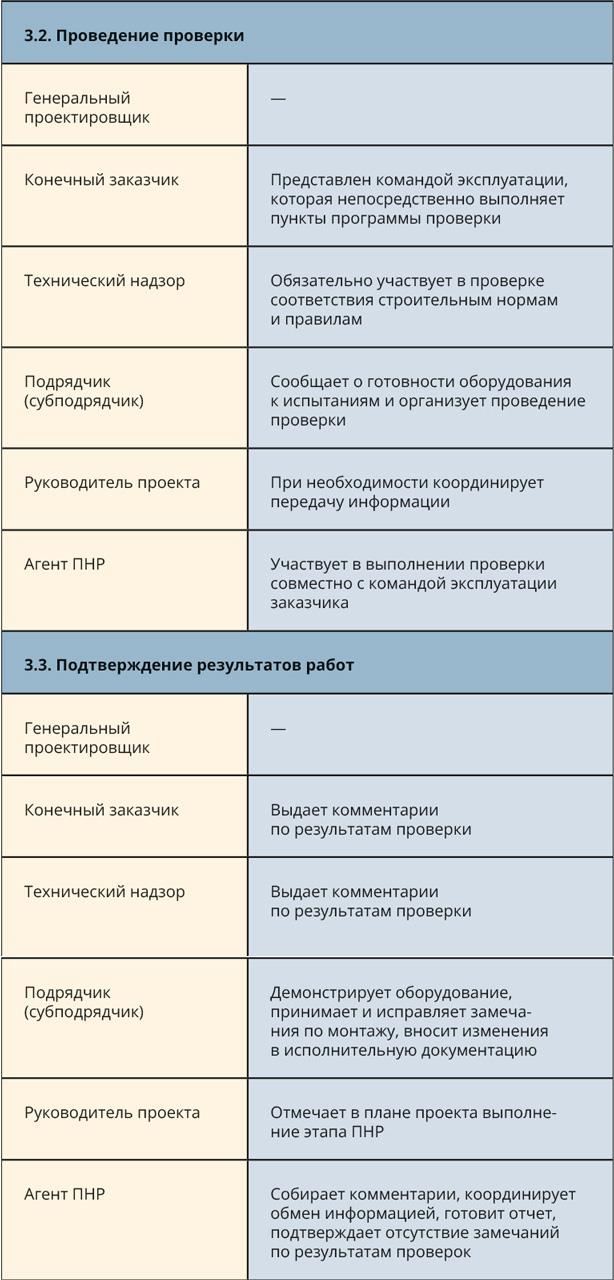
4. CT (Component Test) – компонентное тестирование (индивидуальные испытания)
После успешной приемки монтажа на оборудование можно подавать напряжение и приступать к поочередной проверке всех его составляющих. Это достаточно долгий и утомительный тест, но с точки зрения конечного результата его ценность трудно преувеличить. Так, например, приходилось видеть стену из двух десятков вентиляторов, вполне себе работоспособную, в которой из-за неисправности модуля управления один вентилятор всегда вращался с постоянной скоростью, остальные свою скорость меняли. Найти такой недочет можно или случайно, или путем последовательной проверки каждого вентилятора одного за другим. Понятно, что рано или поздно подобный неисправный компонент все равно бы нашелся, но предположу, что времени на его поиски было бы потрачено намного больше.
Программу таких испытаний написать трудно. Иногда для стандартных продуктов производитель готовит соответствующие чек-листы, но для специально спроектированного оборудования это, скорее всего, будет задачей агента пусконаладки. И тут будет необходимо привлечь весь опыт и всю экспертизу эксплуатации, чтобы не только учесть все уже известные типы неисправностей, но и предположить, что еще может произойти с конкретным компонентом в конкретном типе оборудования.
В идеальном случае на этом же этапе необходимо убедиться в сопряжении оборудования с системой мониторинга датацентра, чтобы уже на следующем тесте наблюдать изменение режимов работы, находясь не только непосредственно перед пультом управления, но и удаленно, с места дежурного.
Я бы не рекомендовал переходить к следующему этапу тестирования, если на CT остаются недочеты. Практически невозможно провести полное функциональное тестирование всей системы, если какой-то ее компонент все еще не готов или неисправен. Тем не менее могут быть объективные причины, по которым проект задерживать нельзя, поэтому особое внимание здесь стоит обратить на тщательное заполнение листа доработок и последующий регулярный, вплоть до ежедневного, контроль за их устранением.
Часто для стандартного оборудования компонентное тестирование производится сразу же после проверки монтажа, в тот же день. Это значит, что обе программы лучше подготовить одновременно. Однако здравый смысл должен преобладать. Слишком долгие испытания приводят к повышенной утомляемости, большему количеству ошибок и стремлению поскорее закончить весь процесс. А это противоречит самой главной цели пусконаладки.
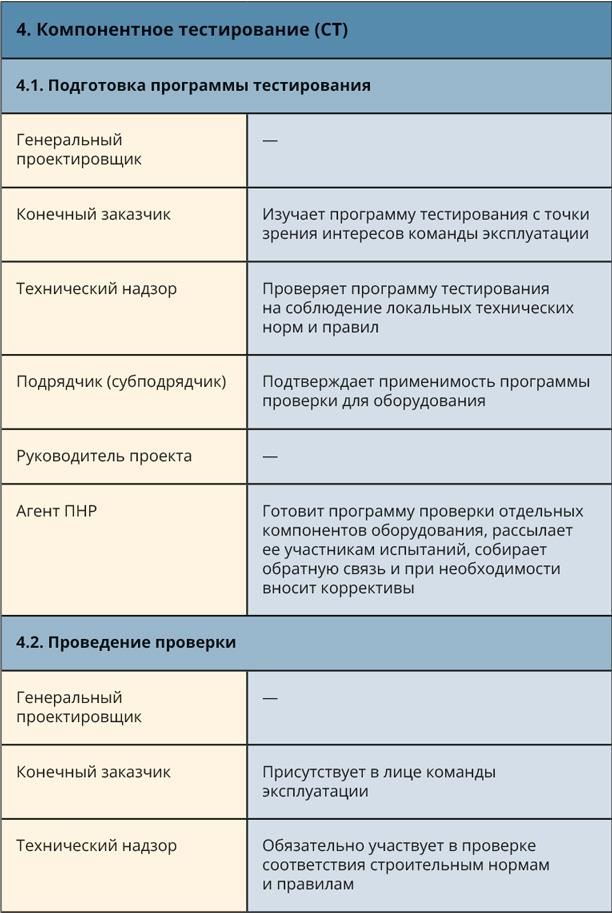
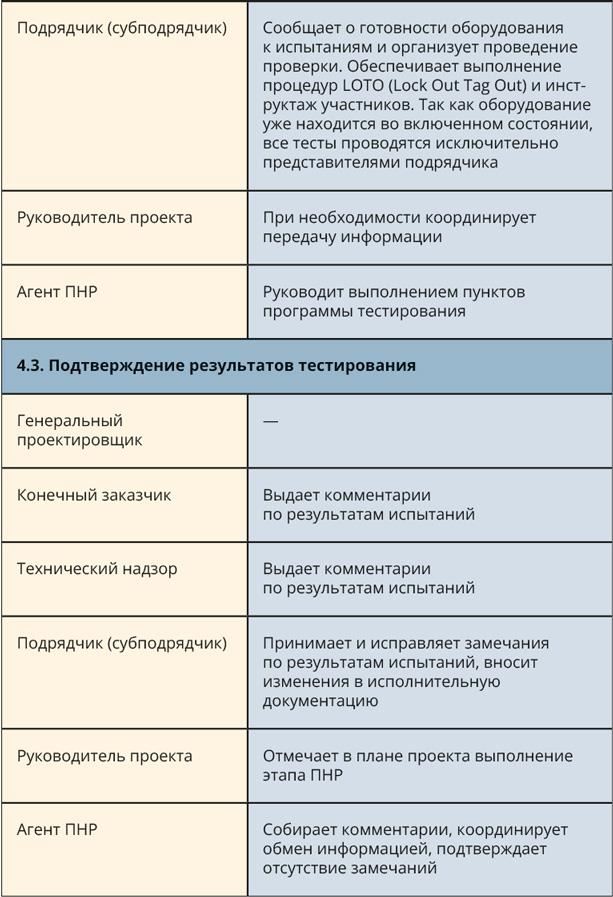
5. SAT (Site Acceptance Test) – приемо-сдаточные испытания
В большинстве контрактов именно этим шагом отмечается окончание всех работ – когда подрядчик сдает, а заказчик принимает собранную и проверенную систему. Для этого подрядчик может заранее подготовить форму соответствующего акта и даже сделать ее приложением к контракту. Большие и уважаемые компании-поставщики вообще разрабатывают стандартную международную форму актов и программы испытаний, оспорить которую совсем не легко. Тут нужно хорошо понимать, устраивает ли вас стандартная форма, или вы хотите каких-то дополнительных проверок, и если да, то как именно договориться с подрядчиком об изменении процедуры проверки.
Для локальных или более мелких поставщиков разработку программы тестирования можно поручить агенту ПНР. Принципиальная разница в том, что при создании проекта часть оборудования берется с рынка и проект как бы подстраивается под спецификацию конкретных моделей. Тогда очевидно, что и процедура проверки решения должна определяться производителем. Другая же часть, наоборот, изготавливается под конкретное техническое задание, а значит, и тестирование должно исходить из задачи получения проектных значений.
Конец ознакомительного фрагмента.
Текст предоставлен ООО «ЛитРес».
Прочитайте эту книгу целиком, купив полную легальную версию на ЛитРес.
Безопасно оплатить книгу можно банковской картой Visa, MasterCard, Maestro, со счета мобильного телефона, с платежного терминала, в салоне МТС или Связной, через PayPal, WebMoney, Яндекс.Деньги, QIWI Кошелек, бонусными картами или другим удобным Вам способом.
Сноски
1
Датацентр, или дата-центр, – единого официального написания нет, даже американцы напишут data center, тогда как британцы – data centre. В книге мы будем использовать вариант написания «датацентр».
2
Федеральная сеть дата центров, учредитель Координационного совета по ЦОДам и облачным технологиям (АНО КС ЦОД), член Ассоциации участников отрасли ЦОД.
3
Data Center Operations.Выдуманный жаргонный термин, обозначающий команду эксплуатации инженерных систем датацентра. Как правило, эта же команда следит и за зданиями и сооружениями на площадке.
4
IT Operations. Как и DCOPS, выдуманный термин, описывающий специалистов по серверному и сетевому оборудованию.
5
Network Operations Center. Центр сетевой связности объекта. В отрасли существуют и другие термины, по сути обозначающие то же самое: meet-me room, коммутационный центр и т. п. Может отличаться от FMR.
6
Пусконаладочные работы. Ответственный этап в строительстве датацентра, во время которого по частям и полностью проверяется пригодность построенного объекта к дальнейшей эксплуатации.
7
Большая, шумная и дымящая машина, предназначенная для генерации электричества из топлива в том случае, если электроэнергия по проводам больше не приходит.
8
Агент пусконаладки. Команда, берущая на себя бремя лидерства в процессе пусконаладочных работ.
9
Computerized Maintenance Management System. Единая система, хранящая все аспекты эксплуатации объекта. Производители программного обеспечения с разным успехом приближаются к идеальному продукту, но окончательно достичь этой цели, по-видимому, невозможно.
10
Project Management Body of Knowledge. Культовая книга руководителей проектов из любой отрасли, наподобие той, которую вы сейчас держите в руках. Рассказывает о всех тонкостях профессии.
11
Factory Acceptance Test. Производственная проверка оборудования перед отправкой заказчику.
12
Site Acceptance Test. Функцональные испытания отдельно взятой системы или оборудования.
13
Responsible, Accountable, Consulted, Informed. Популярный вид отображения ролей в проекте, где для каждой задачи определяются исполнители, ответственные, консультанты и «те, кто стоит в копии», – пользователи информации.
14
Design Compliance Check. Начальный этап пусконаладки, на котором проверяют, насколько проектные решения соответствуют требованиям технического задания и годятся для реальной эксплуатации в дальнейшем.
15
Factory Witness Test. Разновидность FAT, при котором заказчики посещают завод производителя и присутствуют при выполнении теста.