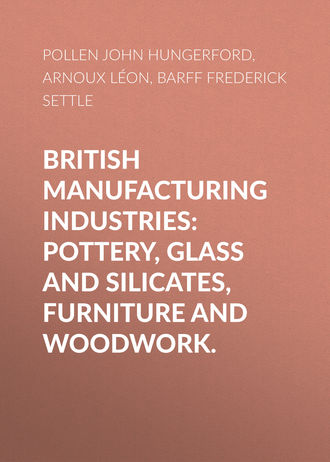
Полная версия
British Manufacturing Industries: Pottery, Glass and Silicates, Furniture and Woodwork.
Two German brothers, of the name of Elers, who settled near this town in 1688, seem to have been the first to try to produce pottery of a better class than the crouch ware. Their first attempt resulted in the production of a well finished red stoneware, which probably resembled the red ware made in Saxony by Bottger at the same time. Those who have left any written information about it, say that for general appearance and careful execution, it was quite equal to any similar article made by the Chinese; but I must confess, that the specimens that I had the opportunity of seeing are rather porous and far from being highly baked. These foreigners paid also great attention to the improvement of the white ware, and they were the first to employ the plastic clay from Dorsetshire for the purpose of whitening the cane marl of the locality. Their ware was generally light and well-shaped, and though the plaster moulds were wholly unknown at the time, and were only introduced fifty years later, the impressions taken from metal moulds are neat, and show the ornaments standing sharply out from the surface. This, combined with the peculiar appearance given to the surface by the sublimation of the salt, and its light colour, are the principal feature of the Burslem ware, which continued in existence till 1780, although before that date more perfected articles had found their way to the market. The brothers Elers used to make a great secret of their mixtures, and left the district as soon as the other manufacturers became acquainted with them. Astbury, who had been instrumental in robbing them of their processes, was one of the most intelligent amongst these potters, and it was he who, in 1720, introduced the flint, calcined and ground, for whitening the body of the ware, one of the greatest improvements in the making of earthenware. He seems to have been a thoughtful and persevering man, and it is said that the idea of this new material was suggested to him, by seeing a shoeing smith calcining a flint, for the purpose of blowing the dust into the eyes of his horse, suddenly afflicted with a kind of blindness. This is probably only a fiction, as the idea must have originated from witnessing the change undergone by flint when brought to a red heat.
As the pottery trade was taking root in the district, it is no wonder that we find many intelligent manufacturers doing their best to improve it and make it profitable. Eminent amongst them was Josiah Wedgwood, whose name as a potter is never likely to perish. For particulars concerning his private life, trade, and manufacture, there are two excellent books, by Miss Meteyard and Mr. Llewellyn Jewitt, in which every matter of interest about him has been carefully entered. Born at Burslem, in 1730, of a family of potters, he began by serving his apprenticeship as a thrower under his brother, and must have settled in business very early, as he had had already two partners when he set up on his own account, in 1759, being then only twenty-nine years of age. His first attempts seem to have been directed to making a green ware, that is, a white ware covered with a glaze of that colour, which he succeeded in getting particularly bright; and also to the tortoiseshell, which had its surface mottled with glazes differently stained, and which, by their blending when they are fused in the oven, present some analogy with the works of Palissy.
One of Wedgwood's decided successes was, perfecting the white cream-colour ware, which was so superior to anything done before, that it commanded at once a great sale at home and abroad. Queen Charlotte admired it much, and, in consequence of her patronage, it took the name of Queen's ware, under which it was known for a long time. It is light, of a pleasing colour, elegantly shaped, and in the hands of artists has proved an admirable material to paint upon.
It would take too long to enumerate all the improvements which Wedgwood effected in his trade in the second half of the last century, but I must mention as prominent amongst his works, the black Egyptian and jasper wares, in making which he had no assistance whatever, and which constitute two new and perfect types in pottery. From Wedgwood's origin and early labours, it is easy to guess that his instruction must have been limited; but he was a clear-minded and inquiring man, possessing that sort of intuition by which he could easily understand things, which in other people would have required preliminary studies; besides, he had a natural taste for art and a systematic way of going through his experiments, which were sure to bring them to a successful issue. It was his good fortune to be assisted by two men of superior intelligence, viz. Flaxman, the sculptor, who designed many of his shapes, and modelled for him an almost innumerable number of subjects for slabs and cameos; and Thomas Bentley, a distinguished scholar, with whom he was commercially connected, and whose knowledge of art he found of great utility.
When Wedgwood died, in 1795, the ceramic manufacture had extensively developed, and had extended from Burslem to the small towns in the neighbourhood. From all this it must appear that, although Wedgwood was the most brilliant type amongst the English potters of that period, the trade was already well established when he entered the business, and there was every probability, that it would become one of the staple industries of this country. To give all the credit to him would be an injustice to several men, who, like the two Josiah Spodes, effected great improvements, or brought into play new and useful materials.
When I speak of the china manufacture, it will be seen that, besides the Staffordshire potters, several very clever men at Bow, Chelsea, Plymouth, Worcester, Derby, and other places, were at work to establish the manufacture of the soft and hard porcelain, proving beyond a doubt, that most energetic efforts were being made to raise the pottery trade of England to the same level as that of France or Germany. If we did not then succeed in making soft china like that of Sèvres, or hard porcelain as good as the Dresden, we soon became the masters of the market as regards earthenware – a position that we are not likely to lose for many years to come. Amongst the circumstances which combine to make our position particularly strong, it is enough to mention our independence as regards the supply of the raw materials, and the abundance of our clays and fuel, of a better quality than those at the disposal of our competitors. Besides, the localization of this manufacture in Staffordshire has caused the concentration in this spot of an intelligent population, acquainted with the traditions, from which the different branches of the trade can be easily fed.
The soil of Staffordshire produces a variety of clays which are used for common ware; but the most important is the one called marl, which is fire-clay from the beds of the coal measures, used for making the "saggers," or clay boxes, in which the ware is placed before it is sent to the ovens. The quantity required for this purpose is very large, and it was of the utmost importance that such material should be good, cheap, and easily procured.
At present, however, the clays necessary to make china or earthenware are not found in Staffordshire, but are sent from the counties of Dorset, Devon, and the Duchy of Cornwall, where they constitute an important branch of commerce. It is a common occurrence to hear people, visiting Staffordshire for the first time, wonder at the apparently abnormal fact of an industry settling in a district where none of the requisite materials are to be found. I have mentioned in the preceding pages how it happened that the trade first settled in Burslem; and a short explanation will show that, although more perfect clays from distant counties had to be used, there was no need to change.
For baking pottery, the quantity of fuel required is comparatively large. When, independently of the ovens and kilns, we take into account what is absorbed by the steam-engines, preparation of materials, and warming of the shops, we find that for every ton of manufactured goods, at least three tons of coals are wanted, and that for decorated goods, it will take twice that quantity, and even more. As the districts from which the clays are sent have no coals, the advantage of paying the carriage on the smallest number of tons to be brought to the works becomes evident.
The potter's clay derives its origin from several felspathic rocks, which under various influences have been decomposed, and the finest portion washed away, to be collected in natural depressions of the soil, where it has formed beds of various thickness. Chemically speaking, it is a silicate of alumina in combination with water, with the addition, in small quantities, of different materials, such as potash, soda, lime, or iron, acting as fluxes on the silicate, which otherwise would give no signs of vitrification. The iron, which may exist in different states, has a colouring effect injurious to the clay, which, to be useful, must be almost free from it. When this condition occurs, the excellence of the clay is determined by the quantity of alumina that it contains. Pure silica, in the form of quartz, flint, or sand, is a very easy material to procure when wanted, but as no geological formation yields alumina in the pure state, no other can be got, besides that which already exists in the clays. It is a common error to say, that it is the silica which renders them refractory. It is true that pure silica can stand any amount of heat without fusing, but its readiness to combine with alkaline matter, and to form vitreous compounds, renders its use objectionable when heated with metallic oxides. An excess makes the wares brittle and unable to resist sudden changes of temperature, while alumina, on the contrary, gives these qualities, and with them the plasticity required for the working of the ware. From it the clays derive the property of absorbing and retaining a large quantity of water, and such is its affinity for it, that sometimes a red heat will hardly suffice to expel it completely. Alumina is a light material – silica a heavy one; and a potter ought to know approximatively in testing the density of a sample, whether it is rich or poor in either of the two. The reason why the clay deposits are richer in alumina than the rocks from which they originated, is explained by the lightness of this element, which, being kept in suspension in water for a longer time, was consequently carried farther, leaving the silicious refuse to settle on its way.
For earthenware or china, the English potters use only two sorts of clays: the ball clay, also called blue clay, and the kaolin. For porcelain the last only is used; for earthenware, both. The ball clay, exported from Teignmouth and Poole, comes from the lower tertiary clays of Devon and Dorset, and is remarkably good and plastic, the quantity of iron being comparatively very small. The ball clay from Poole is dug in the neighbourhood of Wareham, by Mr. Pike. It is of a very superior kind, and more than 70,000 tons are sent from that harbour alone to the potteries, besides smaller quantities to the Continent. As it possesses a little more alumina than those from Teignmouth, which are dug at Teigngrace and Whiteway, near Bovey Heathfield, they ought to have a little superiority over these, although in practice the difference is not always perceptible.
Kaolin is the Chinese word given to the clay from which hard porcelain is made, though here it is generally called China or Cornish clay. This material is found in some granitic rocks in an advanced state of decomposition; the felspar, their most important element, having under external influence lost the greatest portion of its alkali, and become converted into a kind of earth. By agitation in a large quantity of water it dissolves readily; the refuse, composed of quartz, mica, schorl, and undecomposed felspar, sinks by its own weight to the bottom of the tank where the liquid mixture is to run; and the finest part, which is the kaolin, is carried farther to large receptacles, where it accumulates. When these are full, the clay is removed and dried for export. In that state it is very white, and although not so plastic as the ball clay, contains a little more alumina and less iron, which accounts for its resisting much better the action of fire. It is principally obtained at St. Stephens and St. Austell, in Cornwall; Lee Moor, near Dartmoor, in Devon, and a few other places; the whole of them sending to the potteries about 130,000 tons annually.
From the same districts comes another granite, in a less advanced state of decomposition, called Cornish stone, which is used fresh from the mine without further preparation. In it the felspar retains its alkaline element, so that it can be easily melted, and is found a useful and cheap flux for the vitrification of the different mixtures. The composition of these rocks varies considerably, so that it requires constant experiments to determine in what proportion the quartz and the fusible parts stand to each other.
Flints are also largely used in the manufacture of earthenware. They are found abundantly in the chalk districts, the brown sort being considered the best. Under a moderate red heat they become white and opaque, and may be easily crushed between iron rollers. In that state they are placed in pans of water and ground by large stones of chert, till they become sufficiently divided to remain in suspension in the liquid without sinking and hardening at the bottom of the tanks, which, by the way, are called "arks." Flints are comparatively a cheap material, and their carriage to Staffordshire represents a large portion of their cost.
Such are the four materials essential for making earthenware. The respective quantities in which they are used vary in each manufactory, but the principle is always the same: the ball clay being the foundation, and flint the whitening material; but as an excess of this would make the body difficult to work, Cornish clay assists in making it whiter and less liable to break under a heavy weight or sudden changes of temperature. The Cornish stone is used in a small quantity as a flux, to render the ware more compact and of a closer texture. When the mixture of these materials is completed, the colour taken by earthenware when fired would not be a perfect white; the quantity of oxide of iron existing in the clays, however small, would be still sufficient to impart a yellowish tint, particularly after the glazing of the ware. This is counteracted by the addition of a small quantity of oxide of cobalt, the power of which over the iron, as a staining material, is such as to neutralize it completely; the result, in fact, being the same as that obtained by washerwomen, who use blue to the linen with the object of making it look white.
From the moment that the materials are extracted, to the time when the goods are perfected, the number of distinct operations to perform is so great, that I can only give a summary description of the most important. The grinding of those materials which are not already in a fine state of division is one of the most essential, for upon it depends the soundness of the ware, and without it the difficulties of workmanship would be greatly increased. It must be so perfect, that when the different components are put together in the slip state, they should mix readily and form a homogeneous compound. The grinding for the use of potters is a trade of itself; but good quality is of such importance, that the manufacturers who can afford it prefer having mills of their own. In these, the different materials are ground in water in separate pans, till they can pass freely through fine silk lawn, and are afterwards stored in distinct reservoirs, and the excess of water removed, so that a quart measure of each should weigh a determined number of ounces. As the potter knows beforehand the proportion of solid matter contained in each liquid measure, it only remains for him to count the number of quarts or gallons which must be introduced into the body of the ware. This being done, the liquid mass must be deprived of its superabundance of water. Till lately it was the custom to effect this by running the slip 10 or 12 inches thick over the surface of long kilns, paved with bricks and provided with flues underneath. The heat which was maintained in these, assisted by the porous nature of the bricks, was sufficient to bring it to the proper state of toughness; but the kilns could not be filled more than once a day, and required besides a large quantity of fuel, much of which was wasted in the form of dense smoke. Now, thanks to the new apparatus of Messrs. Needham and Kyte, the same result is obtained with great saving in space, time, and fuel.
The process is simple, and easy to manage. As soon as the final mixture is sifted, the slip is directed to a well, whence it is raised by an hydraulic pump and sent to the presses, which are composed of a variable number of large wooden frames. These are closely ribbed on both faces, and, when placed side by side in a vertical position, they leave in the middle an interval of about three-quarters of an inch in thickness. Each of these hollow compartments is lined with a sheet of strong cotton stuff, folded in such a way as to form a bag, in the middle of which a small metal fitting passes through the upper part of the frames, and forms the spring by which the slip can be admitted into the interior. When the bags are tied together, the slip is admitted into their interior and submitted to such pressure from the pump, that the water filters through the interstices of the stuff, and escapes by the small intervals left between the ribs of the frames. After allowing a sufficient time for the action of the pump, the presses are dismounted, and the solid clay is found in the middle of the bags, ready for use in the various departments.
The processes for shaping the different articles are many. For the more expeditious preparation of the wares, it was necessary that each workman should devote the whole of his time to a special branch of his art. For this reason we have several classes of potters, called according to their avocation: throwers, turners, handlers, hollow and flat ware pressers, figure and ornament makers, tile makers, modellers, mould and sagger makers, besides those who are employed in the decoration of the goods. Of all these various branches, the most attractive for those who are witnessing it for the first time, is the throwing; and it is a source of amazement for them to see how quickly, in the hands of the potter, the same lump of clay can be transformed in a variety of ways.
The potter's wheel is of great antiquity. In some Egyptian hieroglyphics from the tombs of Beni-Hassan, known to have been made during the twelfth dynasty, the different occupations of the potter are painted with great distinctness. In one of these, two potters are using the wheel for making their vessels – implying that this contrivance has been in use for something like four thousand years. The forms and proportions of the wheels may be varied without altering the principle. A spindle, finished at its lower end in the form of a pointed pivot, is placed on a hard substance on which it can easily revolve. The upper end is furnished with a wooden head or small platform, on which the lump of clay is to be placed, and between this head and pivot is fixed an horizontal wooden disc of large diameter, which acts as a fly-wheel and keeps the spindle in motion for a certain length of time. The motion may be given by the hand, the foot, or mechanical power, which causes the spindle to revolve with great velocity. A good thrower requires a great deal of practice, as he is expected to throw several hundred pieces a day, although the art is far from being what it was in the olden times. In consequence of the new plan of pressing all large pieces in plaster moulds, the thrower has but small or moderate size pieces to work, and these he finishes only in the inside, leaving the outside to be done by the turner, when the pieces are in a more advanced state of dryness. This division of work, brought about by the exigencies of the trade, is very much to be regretted, for the old thrower was really an artist, who could impress his feeling on the work which was entrusted to him from beginning to end. He has not now the same opportunity of showing his skill, and cannot take in his work the pride and interest which he would have felt, if circumstances had not been altered. The same may be said of the turner, who finishes the outside on a lathe like that used for turning wood. The thrower prepares the pieces of a thicker bulk than is required, and it is the turner's business to bring them to a proper thickness, by removing the excess of material and giving to the exterior a smooth and highly finished surface. If the handles are ornamented, they are pressed in plaster moulds; if plain, they are squeezed from a brass cylinder, filled with clay, with a small aperture at the bottom, from which it escapes under the pressure in long ribbons. These are placed side by side on a board, cut across at the required length, and bent in the form of handles when they get sufficiently hard. They are afterwards fitted, and made to adhere to the pieces by means of a little water or slip dropped from the point of a brush.
Flat pieces, such as plates, dishes, saucers, and the like, are made in plaster moulds, on which a bat of soft clay is tightly compressed by a hand tool, called a polisher. The process is very expeditious, although the presser is obliged to repeat the operation, to give more pressure and finish. For this kind of ware, the potter's wheel called a jigger, is simplified so far, that the iron spindle resting on its point and fixed to a bench, is provided only with a round plaster head on which the moulds are placed. The presser keeps this in motion with his left hand, whilst with the right he guides the polisher.
In those manufactories which have adopted the latest improvements, the jiggers are worked by steam power, and the stoves in which the pieces are sent to dry are heated by steam pipes. These are constructed on a new principle, consisting of a number of shelves which revolve round a central spindle, so that by a gentle push of the hand, each section is successively brought in front of the door, giving the opportunity of removing or putting in the moulds. This simple contrivance does away with the necessity for the assistant boy entering the stove, and feeling the bad effects of the heat.
When the pieces are not exactly round, and cannot be thrown or pressed on jiggers, it is the custom to have them made in plaster moulds, which have been cast on models prepared for the purpose. As long as the clay keeps soft, it takes the shape of any hard substance against which it is pressed, and for that reason, plaster, which has the property of absorbing moisture readily, is preferred. The use of plaster for moulds is comparatively recent, and although its properties were known in early times, there is no evidence that it was ever employed for that object. Greeks, Etruscans, and Romans, had their moulds made of fired clay; the Chinese, in raw clay thoroughly dried. In Staffordshire, before the use of plaster, they were made of fired clay or metal; but plaster is more economical than any of these, although moulds made of this material do not last long, and require constant renewing.
The making of moulds, well adapted for pressing the various shapes, is a very important part of the potter's business. They must allow of a certain amount of contraction, and, at the same time, must easily dislocate without pulling away any part of the piece, which is still sufficiently soft to be distorted by careless handling. Some pieces will require moulds made in one or two parts; others, a large quantity of them, the various fragments being in that case pressed separately, and carefully put together afterwards. The pressing is done in this way: the potter begins to flatten a lump of clay in the form of a bat, and transfers it to the inside of the mould; then, by the repeated blows of a sponge in his right hand, he compels the soft material to take the exact form of the mould, and, of course, of any ornamentation which may be on its inner surface. A good presser ought to be systematic in his work, and not to apply more pressure to one part than to another, otherwise the different portions of the pieces would not contract alike, and would be liable to show an irregular surface, or even crack in the drying or firing processes.