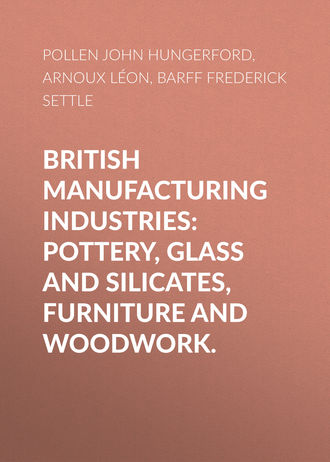
Полная версия
British Manufacturing Industries: Pottery, Glass and Silicates, Furniture and Woodwork.

British Manufacturing Industries: Pottery, Glass and Silicates, Furniture and Woodwork
PREFACE
The object of this series is to bring into one focus the leading features and present position of the most important industries of the kingdom, so as to enable the general reader to comprehend the enormous development that has taken place within the last twenty or thirty years. It is evident that the great increase in education throughout the country has tended largely to foster a simultaneous interest in technical knowledge, as evinced by the spread of Art and Science Schools, Trade Museums, International Exhibitions, &c.; and this fact is borne out by a perusal of the daily papers, in which the prominence given to every improvement in trade or machinery attests the desire of the reading public to know more about these matters. Here, however, the difficulty commences, for the only means of acquiring this information are from handbooks to the various manufactures (which are usually too minute in detail for general instruction), from trade journals and the reports of scientific societies; and to obtain and systematize these scattered details is a labour and a tax upon time and patience which comparatively few persons care to surmount. In these volumes all these facts are gathered together and presented in as readable a form as is compatible with accuracy and a freedom from superficiality; and though they do not lay claim to being a technical guide to each industry, the names of the contributors are a sufficient guarantee that they are a reliable and standard work of reference. Great stress is laid on the progressive developments of the manufactures, and the various applications to them of the collateral arts and sciences; the history of each is truly given, while present processes and recent inventions are succinctly described.
BRITISH MANUFACTURING INDUSTRIES
POTTERY
By L. Arnoux, Art Director and Superintendent of Minton's FactoryWithout entering into an elaborate dissertation on the antiquity of the Art of Pottery, which would be out of place in so short an article as this, I will briefly state that the practice of making vessels from plastic clays, for holding liquids and provisions, first resulted from the exertions made by man to emerge from his primary condition. It is a well known fact that vessels of clay, only partially baked, have been found, together with stone implements belonging to prehistoric times, and that those vessels, unfinished as they were, had peculiar characteristics. But supposing that this was not so, it must strike everybody that, after providing himself with those rude instruments wherewith to obtain his food and protect his life, man must have taken advantage of his power of observation to notice the property of plastic clay to retain water, and to find out to what useful purpose it might be brought for making vessels better suited to his wants, than the skins of animals or pieces of wood roughly hollowed out. If not probable, it is however not impossible, that the first man, taking in his hand a lump of soft clay, should have tried to give it a defined shape, in which case the art of pottery would be as ancient as the human race. It may have been anterior to the use of fire, for a sound and useful pottery may be made with clay hardened in the sun, as still practised in Egypt and India. At all events, it existed previous to the working of the first metal, as one can hardly understand how bronze could have been melted, without the assistance of vessels made of fired clay carefully selected. Consequently it is admitted by everybody, that this is one of the earliest of human inventions, and that the material has proved most durable. This durability, secured by the application of heat, is a very remarkable phenomenon; for while many other materials, apparently very hard, have been found unable to stand the atmospheric changes or the continuous contact with a damp soil, it was sufficient to submit this one to a very moderate heat, to be enabled to resist these various agencies for several thousands of years. This is particularly noticeable in the black Greek pottery, which, while possessing all its former appearance, can, however, be scratched by the nail or broken by a gentle pressure between the fingers. It is thus that we are indebted to the art of pottery for innumerable works of art, many of which have proved most useful in elucidating historical facts, and making us acquainted with the habits, dresses, and ceremonies of ancient peoples.
One can understand how difficult it is to decide who were the earliest potters. It is a question that archæologists have often tried to answer, but which is not likely to be ever solved. Pottery was created to meet a special want of the human race, and we find early pottery existing in almost every part of the world, in unknown America, as well as in Europe or Asia. It is, however, easier to decide which people first excelled in it, and in this respect we must give equal credit to the Egyptians and the Chinese. It is mentioned in sacred history that more than 2000 years B.C. the Egyptian potters were celebrated for their skill, and if we can believe Chinese tradition, the manufacturers in China were at this same time under the control of a superintendent appointed by the government. Unfortunately, we have very little information respecting the history of the art in China, previous to the sixteenth century; and although we have a notion of what they did and how they did it, it is wiser, with our imperfect knowledge, to abstain from speculating as to when the different sorts of Chinese ware were produced. But as regards the Egyptians, there is no uncertainty; some of their ceramic relics bear their own inscriptions, and others have been found associated with objects or monuments whose dates have been carefully ascertained. We may well believe in their skill, when we know that they were acquainted with the most difficult processes for making the bodies and glazes, and that they used the same metallic oxides for colouring their ornaments that we are now using, though often, let us acknowledge, with less success. During a period of at least eleven hundred years, from the eighteenth to the twenty-fourth dynasty, they displayed considerable ingenuity in the production of small figures, jewellery ornaments, and hieroglyphic tablets, in which several sorts of pottery mixtures and differently coloured glazes were most cleverly associated. It is from Egypt that sound principles of pottery making seem to have spread to the different nations; first to the Phœnicians, who in their turn became famous for their knowledge in the art of vitrifying mineral substances; and then to the Assyrians, who seem to have applied pottery more specially to the ornamentation of their buildings.
Greece, who shortly after received her first notions of art from the two former nations, did not devote her energies so much to improvement of material and richness of colour, as to the refined beauty of the shape and the excellence of the painting.
In pottery, the material is of little value, and it is only by the art displayed in shaping and decorating it, that its price can be increased. In this respect the Greeks proved to what enormous value it could be raised, by making it the groundwork of their art, since sums equivalent to several thousand pounds of our money were readily paid by Roman patricians for a single Corinthian vase. In this, as in the other branches of art, the recognized taste of the Greeks will never be surpassed; and if at the present time little attention is paid by collectors to their ceramic productions, it is probably owing as much to the versatility of our tastes and fancies, as to our inability of showing the articles to their advantage.
The Greeks seem to have monopolized the ceramic production of these fine works for seven or eight centuries at the least; for although vessels of the same description were largely produced in Italy, it was invariably by the Greeks, following closely the traditions and mode of decorations of their own country. It was only about a century B.C. that the Romans began to create a pottery on which they impressed their stamp, a pottery really their own; I mean that which is so improperly called Samian, and so easily known by its reddish colour and the embossed ornaments by which it is profusely covered. It is, however, genuine and characteristic, neatly executed, and possessing some standing qualities which did not belong to the Greek. On the other hand, the refinement is deficient; the forms are derived from the circle instead of the ellipse; the plain surfaces are replaced by embossments, and the painting is absent. For four centuries, the Romans seem to have made this class of pottery in several of their European settlements, chiefly in Italy and in the provinces adjoining the Rhine. In the operation they seem to have required some special material, which imparted to its bright red surface a semi-shining lustre or glaze, and which has proved remarkably durable. After this, the art of pottery experienced a time of darkness, when all the refined processes seem to have been neglected, and primitive vessels, like those produced by the Saxons, Gauls, and Celts, ranked amongst the best examples. The decorations, if any, are rudimentary; not only is the painting reduced in a few instances to some lines or spots made of a different clay, but even the embossed ornaments are replaced by lumps of clay or impressed lines in a kind of geometrical disposition. Art was not quite dead, but it scarcely breathed. However, these specimens are not altogether uninteresting, for they were the first efforts of our forefathers, and there is always a certain pleasure in witnessing the feeblest attempts made in the research of art.
But the time came when pottery was to accomplish another revolution, no less remarkable than the first. Strangely enough, it was again from the East, in nearly the same province in which it originally took its rise, that it was revived, and it is not unlikely that some faint tradition of the old processes was the source whence sprung the new ceramic era, which was to extend to our own time.
The precise date of this revival is not positively ascertained; but it was probably contemporary with the establishment of Islamism amongst the Arabs. The energy displayed by this people in improving and adapting the different fabrics to the requirements of their new religion, was no doubt beneficial to the art of pottery, and with their fanaticism and spirit of proselytism, they carried their new ideas to every country which they conquered. Syria became a great industrial centre, and some of its towns, such as Damascus, were soon famous for the perfection of their wares. To reach Europe, however, this new movement did not take its course through Greece and Italy, as in the first instance; it was through Egypt and the North of Africa that, at the beginning of the eighth century, it made its way to Spain, where it became firmly established. As regards pottery, nowhere were better specimens produced than in the towns of Malaga, Grenada, Cordova, and others, going northwards as far as Valencia and Toledo. The newest feature of the Arabian or Saracenic pottery (called Hispano-Moresco ware, when made in Spain) was the introduction of the oxide of tin in the glaze, to render it opaque. Previous to this innovation, when white was required for a design executed on a clay which did not take that colour in firing, these parts had to be covered with a silicious mixture, and subsequently coated over with a transparent glaze. This was the Assyrian and Persian process. To find a white opaque enamel, which could be applied direct on a coloured clay and adhere firmly to it, was a great discovery.
Everyone now knows how successfully these people used pottery for the ornamentation of their buildings, and how ingeniously they mixed transparent and opaque enamels to obtain an unprecedented harmony of effect. Not only did they use this tin enamel in parts, but also all over the ware, making it more or less opaque as they wished; and this was the origin of the pottery called majolica, which, according to tradition, was imported from Majorca to Italy, at the beginning of the fifteenth century, and for the introduction of which credit is given to Lucca Della Robia. Terra in-vitriata was the first name given by this sculptor to his works, when they were coated with this opaque mixture. There was at that time such an earnest desire to find suitable materials for art decorations, that the new enamels soon ceased to be exclusively applied to architectural purposes. Under the beneficial influence of the revival of taste for ancient art, and the encouragements with which it met from the princes at that time ruling the Italian Republics, majolica attained its beauty, though its external appearance reminded us but little of its Spanish or Oriental origin. During the course of the fifteenth and sixteenth centuries, the most famous in the history of modern art, the influence of the great painters of that period was soon felt by those whom we may call the artists of pottery, for the name of potters could hardly do them justice; and several of them applied their talents to the reproduction, on that ware, of their most celebrated paintings. It was reported that Perugino, Michael Angelo, Raphael, and many others painted majolica ware, probably on account of their cartoons being often reproduced; and it is sufficient to say that such talented men as Francisco Xanto da Rovigo, Orazia Fontana, and Georgio Andreoli, devoted their energies to the improvement of this branch of art. Most of the Italian towns had their manufactory, each of them possessing a style of its own. Beginning at Caffagiolo and Deruta, they extended rapidly to Gubbio, Ferrara, and Ravenna, to be continued to Casteldurante, Rimini, Urbino, Florence, Venice, and many other places.
After the sixteenth century, majolica soon degenerated in appearance and quality, the producers being more anxious to supply the market, than to devote to their ware the care and attention bestowed on it by their predecessors. In increasing the quantity of tin in their enamel, to make it look more like porcelain, they impoverished their colours, and this alteration, however prejudicial to majolica, assisted greatly in the new transformation which it was subsequently to undergo. It was under the name of faïence that it continued to be known, and France and Holland became the principal centres of its manufacture. At Nevers, it still resembled slightly the Italian ware, though at Delft, in Holland, it was principally made to imitate the blue and white ware of the Chinese, in which attempt the makers were often remarkably successful. At Rouen, the blue ornamentation was relieved with touches of red, green, and yellow; at Moustiers, the monochrome designs were light and uncommonly elegant; at Paris, Marseilles, and many other places, the flower decoration of the old Sèvres and Dresden ware was imitated with a freedom of touch and a freshness of colour which is really charming. This pottery, which was a great favourite in the seventeenth and eighteenth centuries, declined rapidly soon after our present earthenware made its appearance; the chief inducement for the change, on the part of the manufacturers, being the excessive price of tin, which is the principal ingredient of enamel.
Except in the provinces contiguous to France, Germany was never a producer of majolica. It created, however, a pottery entirely of its own, full of originality in its general appearance, and which, by the peculiarity of the process, was really a very distinct type. I am alluding to the Flemish and German stoneware. There is a tradition, that the first pieces were made in Holland at the very beginning of the fifteenth century. The principal centre of its production was, however, in Germany, at Nuremberg, Ratisbon, Bayreuth, Mansfeld, and other places; but the best were made in the neighbourhood of the Lower Rhine, where the clays most fitted for that class of pottery were easily to be found. Here we find, for the first time in Europe, the body of the ware partly vitrified by the high temperature to which it was submitted, and also the remarkable peculiarity, that it was glazed by the volatilization of common salt, thrown into the oven when the temperature had reached its climax. The combination of these two processes had never been effected before, and it would be difficult on that account to find any connection between stoneware and some of the Egyptian potteries. This stoneware varied in colour: some were almost white, some brown, others of a light grey, the last being the most valuable when the effect was increased by blue or purple grounds, harmonizing admirably with the foundation colour of the ware. The shapes are generally elaborate, with a great many mouldings, enriched with embossed ornaments in good taste, some of which were designed by no less an artist than T. Hopfer. The decline of this stoneware began with the seventeenth century, and from that time to the present, this material was only used for wares of the commonest kind. It is only very lately, that it was revived successfully by Messrs. Doulton and Co., of Lambeth.
France, which had not as yet any ideas about the process for imitating the Italian majolica, created towards the same time two new sorts of pottery, one of which is the Palissy ware, the other the faïence d'Oiron. Palissy, a very inquisitive and intelligent man, is said to have been possessed by a strong desire to reproduce some Italian ware, which he had the opportunity of seeing; whether it was a piece of majolica or of graffito, is not known. Left to his own resources – for there was nobody to instruct him – he succeeded by perseverance and industry in finding out the process for making the different coloured glazes that the Moors had used long before him. There was no discovery in this, but the talent which he displayed in the mixing and blending of these vitreous colours, combined with the incontestable originality of his compositions, have made this ware very difficult to imitate.
The time of its production was limited to the life of Palissy, for there is not really a single good piece which can be traced to his successors. In the faïence d'Oiron, incorrectly called Henri Deux ware, we find a real cream-coloured earthenware taking precedence of two hundred years over our own. It was made between the years 1524 and 1567, and we have now every proof that three persons co-operated in this invention: Heléne de Hangest, who had been formerly entrusted by François I. with the education of his son, afterwards Henry II.; her potter at Oiron, named François Charpentier; and her secretary Jehan Bernart. The charming pieces resulting from the combination of these three intellects were few, and only intended to be offered as presents to the friends of the noble lady at court. This sufficiently explains the monograms and devices, which are found associated with the elaborate ornaments profusely spread over their surface. No ware was ever made before or after this, which required more care and delicate manipulation, and this explains why the highest prices paid in our generation for an article of pottery have been freely given for several of these curiosities. Their principal feature consists in inlaying differently coloured clays one into the other, a process not quite new, as it had been extensively used in mediæval times for making encaustic tiles for the flooring of our churches, but they were so minutely and neatly executed, and the designs so well distributed, that they are justly considered as marvels of workmanship. In speaking of these faïences d'Oiron, we can hardly admire sufficiently the variety in the productions of this period of the Renaissance; and if we select four of these specimens, such as a piece of Faenza ware, one of stoneware, one of Palissy, and another of Oiron, they may fairly stand as good illustrations of the ingenuity of man.
The progress realized in these times seems to have undergone a sort of lull, and if we accept the French and Delft faïences, which were a transformation of majolica, we find that the greatest portion of the seventeenth century was not marked by any new discovery or decided improvement. Towards its close, however, we begin to notice in Germany and the western countries of Europe several attempts at making a ware, possessing the three standard qualities of whiteness, hardness, and transparency of the Chinese, and these were the precursors of the great movement which occupied the whole of the eighteenth century. As might be expected, inquiries made in different countries by persons unacquainted with each other, brought different results; and if they failed in so much, that a porcelain identical to the Oriental was not reproduced, all of them succeeded in making a white ware of their own, adapted to the materials which they had at their disposal. And thus arose in each country the source of a prosperous trade.
It is only at that period, that England began to take her position amongst the producers of pottery, at least in a manner deserving of that name. Up to that time, if we were to judge by the quality of her work, she did not seem fitted for it, no more than for any sort of manufacture which required taste or a certain knowledge of the arts of design. In fact, it is easy to notice in looking at our collections of art manufactures, that the English samples are deficient in many respects; they may be gaudy without harmony of colour, or elaborate without refinement, exhibiting a certain amount of roughness in execution, when placed side by side with Italian, French, or German specimens of the same class. It is likely, with certain exceptions, that the Anglo-Saxon race did not feel much the want of all those niceties, and did not make great exertion to excel in the practice of those arts, for the appreciation of which its mind was not yet sufficiently cultivated. It has been remarked, that as the progress of art was constantly from East to West, the geographical position of England might account in some respects for her backwardness. However, like children of slow growth whose understanding does not seem quick or acute, but who afterwards derive the benefit of their reserved strength, England, coming almost the last in the production of pottery, seems as though she did so for maturing her capabilities. In this, as in the practice of other arts, she is slow, and her first steps are clumsy. Experimenting for some time, with mixed or indifferent success, she seems to hesitate, till she begins to feel that she holds the thing in her grasp, and then the day soon comes when she teaches the world what she can make of it. We can scarcely give her credit in the preceding review for some Staffordshire pottery made with the yellow or red marl, thickly glazed with the galena extracted from the Derbyshire mines, the decoration of these pieces being effected by pouring the light clay on the dark one in a symmetrical manner. This pottery was in use from the time of Queen Elizabeth down to the year 1775, the date of the latest specimen that I have seen. Some pieces preserved in the British Museum, in the Museum of Geology, and in M. Solon's collection, are to be noticed for their quaintness.
Up to the eighteenth century, no other clays than those extracted from the coal measures seem to have been used in Staffordshire; and the advantages derived from an abundant supply of both clay and fuel must have powerfully contributed to the settlement of this industry in that county. In Shaw's 'History of the Staffordshire Potteries,' which with Plot's 'History of Staffordshire,' are the only books to afford information on the then state of this trade, and whose most interesting extracts have been given by Sir Henry de la Beche in his excellent catalogue of the pottery exhibited in the Museum of Practical Geology, we gather this fact, that so far back as 1661, an Act of Parliament regulated the dimensions and quality of earthen vessels manufactured at Burslem, for holding the butter brought to the markets.
Towards 1680, a radical change seems to have taken place in the way of making the ware, by substituting common salt for the galena in the glazing process. This new production was called crouch ware, and there is every probability that the substitution was first made by a person acquainted with the manufacture of the German and Flemish stoneware, which at a former period had been tried in England. At that time Burslem possessed twenty-two ovens, and Shaw says, that when these were at work, the vapours emanating from the salt were such as to produce a dense fog in the town. These assertions leave no doubt as to the date of the commencement of this manufacture in Staffordshire, and that Burslem was its first seat.