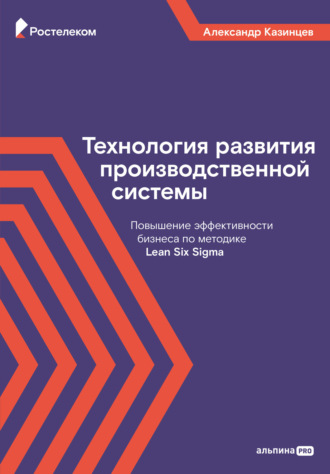
Полная версия
Технология развития производственной системы. Повышение эффективности бизнеса по методике Lean Six Sigma
Комфортная работа – для сотрудников. Если рабочее пространство рационально организовано и сотруднику удобно выполнять свою работу, повышаются производительность и качество, что автоматически приводит к улучшению бизнес-показателей. К сожалению, наши традиционные формы управления часто пренебрегают связью между обеспечением комфортных условий труда и эффективностью бизнеса.
● Скорость реагирования процессов на изменения требований рынка.
Высокая адаптивность процессов – для сильной конкурентной позиции. Изменения на рынках происходят активнее и быстрее с каждым годом. Условия конкуренции становятся жестче, требования потребителей – выше. Перегруженный ненужными и нерациональными действиями процесс неспособен оперативно реагировать на подобные вызовы окружающего мира.
Тот, кто успевает адаптировать свои процессы к этим изменениям, выживает и, возможно, даже получает дополнительный доход. Тот, кто не успевает…
Не мы придумали оптимизацию. Все руководители более или менее успешно устраняют проблемы, развивают процессы, повышают ключевые показатели эффективности (КПЭ), обеспечивают достижение поставленных бизнес-целей. Производственная система, как продуманная логика организации и управления внедрением изменений, просто повышает эффективность этой работы. Значительно повышает.
ПС – инструмент решения проблем руководителей
Ключевая характеристика проблемы – отсутствие известных решений или несоответствие традиционных решений существующим ресурсам.
Проблема – существенное отклонение ключевых показателей эффективности процесса или качества результата от утвержденных нормативов, значительный разрыв между существующими и целевыми характеристиками процесса.
Традиционный подход к решению проблем в процессах – «устранение аварий». Мы реагируем на появление проблемы, инициируя расследование ее причин и устранение последствий. Проблема всегда заметна потому, что уже нанесла конкретный вред бизнесу: упали продажи и доход, не выполнен план по количеству или качеству, ушел ключевой клиент, сломалось оборудование, не хватает ресурсов на достижение поставленных целей, увольняются квалифицированные сотрудники.
Вполне закономерно, что в момент обнаружения проблемы у нас уже недостаточно времени и ресурсов для качественной проработки причин. И быстрые решения принимаются ситуационно. При таком подходе, как правило, соотношение получаемого эффекта и затрат ресурсов далеко от оптимального. Мы затыкаем дыры, лишь бы здесь и сейчас избавиться от негативных последствий проблемы.
В этом случае технология ПС просто помогает быстрее разобраться в причинах и разработать более надежные решения при рациональном расходовании ресурсов.

Также ПС предлагает качественно иной способ решения – предупреждение аварий. Планомерное целевое исследование процессов выявляет все источники потерь, а разработанная на основе диагностики программа оптимизации выполняется с учетом приоритетов задач и наличия ресурсов. Мы предупреждаем существенные проблемы – переходим от аварийного к планово-предупредительному ремонту процессов.
Банк, бэк-офис бизнес-блока. Вывод на рынок новых массовых продуктов привел к быстрому росту потребительской активности и существенному увеличению операционной нагрузки подразделения. Расчетный тренд трудозатрат на будущий период показал разрыв в ~100 штатных единиц.
В реальных условиях банка для руководителя была очевидна низкая вероятность такого увеличения численности подразделения. Понимая все риски ситуации, он инициировал проекты по исключению потерь производительности и высвобождению рабочего времени своих сотрудников. При этом всю работу выполняли специалисты подразделения.
В результате оптимизации дополнительный объем работ был реализован прежним составом подразделения без повышения интенсивности труда людей и снижения качества результатов.
Будь то существующие проблемы или проблемы будущих периодов, ПС призвана эффективно помогать руководителю в их решении. Это бизнес-система, и она должна приносить реальную пользу руководителю, инвестирующему ресурсы в ее создание. Поэтому производственная система будет нормально существовать и развиваться только в случае реальных бизнес-целей и успеха большинства проектов оптимизации.
Задачи ПС – стандартные задачи управления
Достижение целей бизнеса можно обеспечивать с различной эффективностью. К сожалению, достаточно часто проблемы просто «заливаются» деньгами и ресурсами. ПС предлагает качественно иной путь:

Один из базовых принципов ПС – максимальный эффект при минимальных затратах ресурсов. И в полной мере это относится к принципам создания самой производственной системы:
● Постоянное повышение качества продуктов и процессов.
Это долгосрочная работа, охватывающая все ключевые процессы компании. Начав с исключения простых источников потерь ресурсов в ключевых процессах, необходимо перейти к целевому совершенствованию качества во всех процессах, разработке новых стандартов на основе лучших практик и внедрению организационных механизмов постоянных улучшений.
● Массовое вовлечение сотрудников в инициативы оптимизации.
В наших процессах очень много различных проблем, создающих разные виды потерь. Самый правильный и эффективный способ борьбы с ними – научить сотрудников устранять дефекты непосредственно в месте их возникновения.
Это предполагает правильную мотивацию и развитие потенциала сотрудников, обучение современным методам совершенствования процессов, создание системы тиражирования успешных решений и обмена лучшими практиками, профессиональную подготовку и карьерное развитие успешных руководителей проектов.
● Эффективное управление оптимизацией.
Повышение успешности и результативности проектов оптимизации. Для этого необходимо обеспечить правильную постановку задач по улучшению КПЭ процессов, внедрение современных методов проектного управления, формирование кросс-функциональных команд на всех уровнях организационной структуры и оперативный контроль всех инициатив по совершенствованию процессов.
Результаты системной оптимизации достаточно просто оценить: КПЭ процессов и подразделений целенаправленно улучшаются, инновационные решения внедряются дешевле, быстрее и успешнее, их бизнес-логика прозрачна, проблемы устраняются оперативно и на том же уровне управления, где обнаружены.
Потери – катастрофический масштаб утраченных возможностей
Производственная система последовательно и планомерно устраняет любые виды снижения ценности для клиентов, компании и сотрудников:
● теряем удовлетворенность клиентов при снижении качества продуктов и услуг;
● теряем доход из-за отказа клиентов от продуктов или услуг компании;
● теряем трудовые и материальные ресурсы, направляя их на исправление брака и ошибок;
● теряем время и силы сотрудников на нерациональные действия в процессе.
Потери – это бесполезно потраченные ресурсы, неполученные выгоды или доходы, альтернативные издержки, разница между полученными результатами и результатами, возможными при правильном функционировании процесса.
Потери могут превышать 40 % ресурсов процесса
Потери ресурсов в наших процессах, к сожалению, очень велики и даже могут превышать 40 % общего объема. И это не уникальный случай, а весьма часто повторяющаяся ситуация в любой бизнес-деятельности.
Банк, розничный бэк-офис. Исправление 15 типов ошибок требует больше 40 % рабочего времени сотрудников ключевого процесса. Этот объем трудозатрат составляет около 60 штатных единиц.
Завод, производство материалов. Аварийные и избыточные плановые простои производственных линий приводят к потерям миллионов долларов дохода в год.
Технические услуги, аварийное энергообеспечение. Потери из-за низкой эффективности вспомогательных процессов сопоставимы с доходами компании.
Завод, машиностроение. Потери времени на ожидания и простои процесса составляют более 90 %. В результате уходят потребители продукции, которых не устраивают сроки выполнения заказов. Годовые потери сопоставимы с доходом.
С другой стороны, потери – это огромный потенциал развития, и научиться его использовать значительно проще и дешевле, чем создавать и продвигать новые продукты, захватывать новые сегменты рынка или диверсифицировать бизнес. Странно было бы не использовать такую возможность.

Представим ситуацию: процесс работает с загрузкой 100 %, потребляет минимальное количество ресурсов и производит продукцию превосходного качества, которую потребители готовы покупать по максимальной цене. При этом процесс надежен и стабилен, люди выполняют свои задачи в комфортных условиях, а у руководителей достаточно времени и ресурсов, чтобы заниматься дальнейшим развитием бизнеса. Это наша цель.
Дефект – источник разных видов потерь
Проблемы и потери в процессах создаются дефектами.
Дефект – наблюдаемое в процессе негативное событие, нарушение норматива или оптимального способа выполнения операций, приводящее к снижению качества продукта/услуги или непроизводительным затратам ресурсов.
Достаточно часто из-за одного дефекта мы теряем даже несколько видов ценностей. Например, брак в продукте или услуге приводит и к снижению удовлетворенности клиента, и к затратам ресурсов на исправление и доработку, и к уменьшению скорости процесса, что автоматически ухудшает все связанные с этими явлениями показатели.
Дефект – удобный объект для оптимизации
Дефект – это максимальная определенность всех характеристик: дефект очевиден, количество дефектов легко установить, возникающий из-за дефектов экономический вред несложно рассчитать. Если грамотно сформулировать операционное определение дефекта, любой сотрудник, наблюдая конкретную ситуацию в процессе, сможет однозначно обнаружить наличие или отсутствие дефекта.
Операционное определение дефекта – понятная формулировка дефекта, его точное описание для уверенной и однозначной идентификации дефекта в ходе контроля процесса.
Количество и разнообразие дефектов – реальный показатель качества управления. Современный руководитель стремится целенаправленно снижать потери в своих процессах, организуя выполнение множества задач оптимизации по поиску и исключению источников дефектов. Основная цель ПС – помогать руководителю в этой сложной, но необходимой работе.
Проекты пс: Устранение дефектов и потерь
Большие проблемы часто собраны из огромного количества маленьких дефектов. И именно поэтому с ними так сложно бороться: необходимо провести одновременно много разных улучшений на различных участках процесса, много разных специалистов должны исследовать причины дефектов и придумать новые эффективные решения.
Задача оптимизации / задача ПС – внедрение локального изменения в рамках одного участка бизнес-процесса, направленное на устранение одного или нескольких дефектов с целью исключения потерь и улучшения КПЭ процесса или подразделения.
Производственная система инициирует массовое устранение дефектов и потерь в множестве разных процессов. В результате мы, как правило, получаем большое количество выполняемых одновременно задач оптимизации. Необходимо контролировать и сопровождать все задачи, вовремя оказывать методологическую и организационную поддержку. Поэтому для повышения эффективности управления имеет смысл группировать задачи в целевые проекты, направленные на улучшение конкретного КПЭ.
Проект оптимизации / проект ПС – проект по целевому улучшению КПЭ процесса или подразделения компании, может включать в себя множество задач оптимизации, объединенных по признакам цели, процесса, показателя или подразделения.
Не реже встречается ситуация, когда руководитель с самого начала внедрения ПС формирует целевой заказ на улучшение показателей конкретного процесса или подразделения. В этом случае также открывается отдельный ПС-проект.
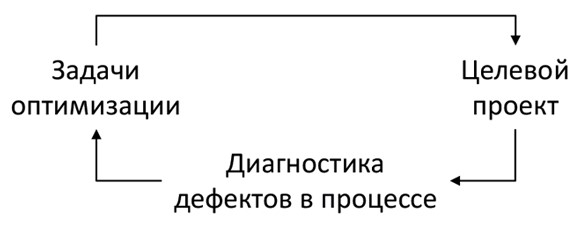
● В первом варианте мы исследуем процессы и группируем обнаруженные дефекты в целевые проекты по признакам влияния на КПЭ подразделения или процесса.
● Во втором варианте диагностику проводим сразу в рамках утвержденных условий проекта и фокусируем внимание на дефектах, отрицательно влияющих на конкретные целевые КПЭ.
Различие в подходах связано в основном с областью управления группами задач, а методы диагностики и организация работы по устранению дефектов практически идентичны.
Технология ПС – эффективная оптимизация
Цель ПС-Технологии, как и любой технологии, – улучшение качества и снижение расходов на производство получаемого результата. В нашем случае влияние технологии измерить очень просто: успешных изменений в процессах становится намного больше, а их внедрение происходит значительно быстрее и с меньшими затратами ресурсов.

Основанная на методике Lean Six Sigma проектная ПС-Технология обладает неоспоримыми преимуществами:
● обеспечивает существенный экономический и качественный эффект при сравнительно малых затратах, устраняя большой объем «процессного мусора»: ненужные операции и нерациональные издержки, брак, ошибки, очереди, простои;
● применима для любых процессов, так как мы работаем с универсальными понятиями «потери» и «дефекты», их статистическими характеристиками и обычными действиями людей;
● сознательно сведена к относительно легкой для понимания последовательности действий, что позволяет сделать работу по оптимизации общедоступной и масштабной, охватывающей все ключевые процессы и подразделения;
● объединяет и усиливает команды оптимизаторов: люди начинают говорить на одном языке эффективности процессов, свободно заменяют друг друга в ключевых функциях, создают синергию различных компетенций.
Lean Six Sigma показывает отличные результаты, но не следует ограничивать ПС утверждением какой-либо одной технологии совершенствования процессов. Система, открытая для методических инноваций и использующая широкий спектр инструментов, получает очевидные преимущества. Мы будем применять инструментарий любых методик. Главное – чтобы они эффективно работали в наших процессах.

Правильная производственная система предполагает жесткие требования к технологии: высокую скорость и низкую стоимость внедрения, охват всех ключевых и дорогостоящих процессов, параллельное выполнение множества задач оптимизации, обеспечение быстрых побед и долгосрочных преимуществ. Как в хорошей консультационной компании.
Производственная система – бизнес внутри бизнеса
Инвестирование в производственную систему развития можно представить как создание консультационной компании, встроенной в бизнес-структуру нашей организации и распределенной по всем подразделениям и процессам. В этой компании работают наши сотрудники, и мы привлекаем их к решению различных проблем, когда это нужно руководителям подразделений и процессов.

Инвестирование в эффективность процессов – исключительно выгодный бизнес:
● Риски инвестирования минимальны – свои процессы известны и управляемы.
● Затраты минимальны – в основном используются уже существующие ресурсы.
● Доходность максимальна – мы сами можем выбирать наиболее перспективные проекты с максимальным эффектом, поскольку диагностика, как правило, выявляет множество дефектов и большой объем потерь.
● Эффект легко монетизируется – мы сокращаем непроизводительные издержки и добавляем «потерянные» доходы собственных процессов.
● Барьер входа отсутствует – это наша компания и наши люди, все необходимые элементы инфраструктуры уже есть.
Компания «Производственная система» специализируется на поиске и решении проблем в процессах и создает дополнительный доход за счет устранения потерь материальных и трудовых ресурсов, снижения себестоимости и повышения качества продукции, повышения производительности при улучшении условий работы сотрудников.
Структура такой «встроенной консультационной компании» близка к идеальной:
● формирование команд только на время проектов и без дополнительных расходов;
● обеспечение и развитие за счет реинвестирования высвобожденных ресурсов;
● минимальная себестоимость и высокий уровень управляемости;
● максимально возможный начальный уровень знаний по бизнес-процессам.
Но придется согласиться с тем, что формирование и развитие такой системы, как и создание любой настоящей компании, требует вполне реальных инвестиций и вполне конкретных организационных усилий. Без этого не получится.
Условия успеха. Типичные ошибки
Очевидно, что и факторов успеха, и способов сделать что-то неправильно много в каждом большом проекте. Перечислить и описать все просто невозможно. И не нужно. Но, полагаю, рассказать о наиболее существенных и стандартных ситуациях будет полезно.
● Цели должны быть жизненно важными для руководства. Производственная система должна приносить конкретные бизнес-результаты: экономия ресурсов и сокращение бюджета, повышение доходности и производительности, улучшение качества.
Построение системы – дело нелегкое, и ПС обязана очень четко показывать свою эффективность в простой бизнес-логике «доходы/затраты».
● Опасно разделять власть и ответственность. Классическая ошибка, приводящая к множеству проблем. Если вы определяете достижение каких-либо показателей только как цели ПС, то будьте готовы, что никто в компании не бросится помогать.
У каждого бизнес-процесса уже есть хозяин, отвечающий за его результат и развитие, – владелец процесса или руководитель подразделения. Неправильно перекладывать ответственность за улучшение процессов или продуктов на ПС. Такой подход превращает руководителя из заинтересованного хозяина в администратора, пытающегося спрятать свои проблемы и потери.
● Необходимо реалистично оценивать цели и возможности ПС. Производственная система не обладает выделенными людьми для выполнения сотен проектов в десятках процессов. Для этого потребуется армия наемных специалистов, что явно противоречит базовой идее экономии и рациональности.
ПС предоставляет необходимые знания, экспертизу и организационную поддержку подразделениям и процессам, в которых будет проводиться оптимизация, а ставить цели и обеспечивать проекты ресурсами должны их руководители.
● Не следует спешить. Цена ошибки велика – второй попытки может и не быть. Внедрение в живую структуру компании такого беспокойного элемента, как ПС, нужно проводить аккуратно и с учетом всех рисков. При этом бессмысленно вслепую копировать чужой успешный опыт. Каждая компания уникальна, и система, которая где-то дает отличные результаты, может оказаться неприемлемой именно для вас.
Практика показывает, что базовые методы и инструменты ПС работают в любой компании. Но их эффективность и результат напрямую зависят от того, как вы проведете внедрение именно в своей структуре и в своем коллективе, как оно впишется в ваш традиционный формат управления.
1.2. Концепция внедрения и развития производственной системы
ПС является вспомогательной матричной системой, максимально интегрированной в функциональную и организационную структуру компании. Помогает обеспечить выполнение целей руководителям различных направлений деятельности, структурных и территориальных подразделений, основных и вспомогательных процессов компании.
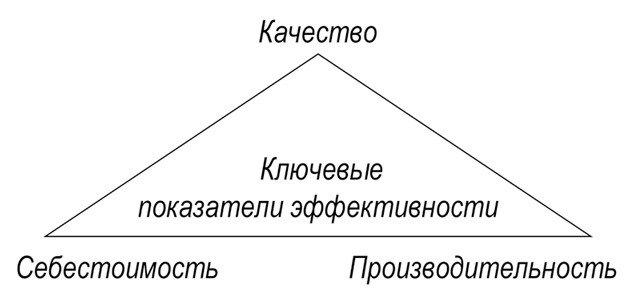
При этом ПС – не приглашенные консультанты, которые приходят и решают за нас наши задачи, а наши собственные менеджеры и специалисты в процессах, обладающие знаниями и навыками применения инструментов оптимизации. И таких сотрудников должно быть достаточно для выполнения множества задач в разных подразделениях и процессах.
Функциональная структура ПС
Чтобы производственная система эффективно работала и целенаправленно развивалась, необходимо сформировать работоспособную функциональную структуру. Как в любой компании. В идеальном случае мы должны получить саморазвивающуюся систему непрерывного совершенствования процессов.
Ключевые требования к функциональной структуре ПС:
● обеспечение последовательного и постоянного развития процессов компании;
● интеграция в функциональную и организационную структуру компании;
● использование минимального количества ресурсов для реализации деятельности.
Основные функции ПС можно разделить на две группы – реализации проектов оптимизации и развития системы. В первую группу входят функции ПС, обеспечивающие выполнение большого количества задач оптимизации и достижение целевых результатов.
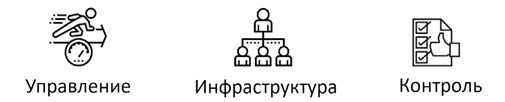
● ПС-Управление – декомпозиция целей развития бизнеса в целевые КПЭ оптимизации процессов, инициирование задач для достижения этих КПЭ и грамотное управление большими группами задач оптимизации.
Реализация функции в общем случае предполагает: правильный выбор процессов для оптимизации, организацию диагностики и выявление дефектов и потерь, рациональный выбор задач, выделение ресурсов на разработку и внедрение решений, оценку результатов изменений и тиражирование успешных практик в масштабе компании.
Если определение цели и постановка задачи проведены неправильно, вся остальная работа обычно не имеет смысла. Прямые потери ресурсов и репутации ПС.
● ПС-Инфраструктура – обеспечение необходимого и достаточного количества сотрудников, вовлеченных в работу по выполнению задач оптимизации и обладающих необходимыми знаниями, навыками и опытом.
Постоянное совершенствование процессов и получение реального экономического эффекта, естественно, требует инвестирования определенного объема ресурсов. В первую очередь это рабочее время сотрудников для выполнения задач оптимизации и трудозатраты менеджеров по организации и сопровождению проектов.
Инфраструктура ПС – это правильно выбранные, обученные и мотивированные люди в процессах. Естественно, нет необходимости учить всех подряд, но качественно подготовленные специалисты должны быть во всех ключевых точках бизнес-структуры. Такие люди – основа производственной системы.
● ПС-Контроль – регулярный сбор и анализ данных о выполнении задач оптимизации и результатах внедрения изменений в процессах, динамике КПЭ.
Без контроля нет реального управления, особенно в проектных структурах. Руководители должны регулярно получать исчерпывающую информацию о результатах выполнения задач, экономической эффективности тиражирования решений, динамике целевых КПЭ, количественных, качественных и финансовых показателях оптимизации.
Очень важно, чтобы подсистема контроля была направлена на реальные бизнес-показатели: снижение себестоимости, повышение качества и производительности. Попытка оценивать результативность системы по количеству выполненных задач, обученных сотрудников, выданных сертификатов приводит к бюрократизации системы и потере ее бизнес-эффективности.
Правильно сформированный контур реализации «ПС-Управление – ПС-Инфраструктура – ПС-Контроль» обеспечивает бизнес-эффективность на всех этапах работы и уровнях управления. Мы выбираем наиболее перспективные задачи и рационально инвестируем ресурсы в решения, обеспечивающие максимальный финансовый и качественный эффект. И многократно увеличиваем этот эффект с помощью тиражирования лучших практик.
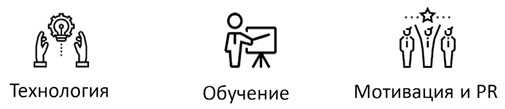
Вторая группа функций направлена на создание и развитие производственной системы:
● ПС-Технология – внедрение методов и инструментов оптимизации процессов, соответствующих современным мировым и российским стандартам и оптимальных для уровня развития процессов компании.