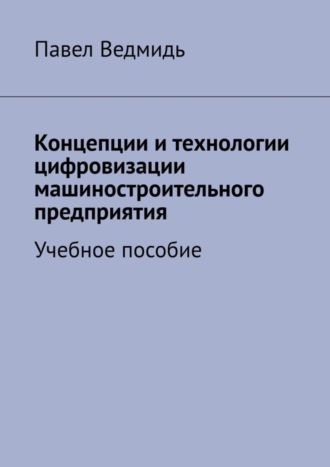
Полная версия
Концепции и технологии цифровизации машиностроительного предприятия. Учебное пособие
• экспертные системы и искусственный интеллект
В рамках концепции умного производства можно выделить концепцию фабрик будущего (Factories of the Future). Так в [5] выделено три вида фабрик будущего: цифровые фабрики (Digital Factory), умные фабрики (Smart Factory) и виртуальные фабрики (Virtual Factory). Эти три вида производств отличаются по целям создания и применяемым технологиям.
Цифровые фабрики ставят целью «увидеть» продукт до того, как он будет реально произведен. Основные технологии: CAD/CAM/CAE, PDM/PLM, cтанки с ЧПУ, аддитивные технологии и др.
Умные фабрики в дополнение к целям цифровых фабрик предполагают более широкое использование средств автоматизации, улучшенный контроль и оптимизацию процессов. Умные фабрики нацелены на серийный выпуск изделий, но при сохранении максимальной гибкости производства. Обеспечивается это благодаря высокому уровню автоматизации и роботизации предприятия. Широко применяются автоматизированные системы управления технологическими и производственными процессами. Технологии промышленного интернета вещей (IIoT) обеспечивают межмашинное взаимодействие оборудования. Справиться с резко возросшими потоками информации, поступающими от датчиков и автоматизированных систем управления, позволяют технологии обработки больших данных (Big Data). Основные технологии: MDS (АСУТП), MES, IIoT, Big Data и др.
Виртуальные фабрики суммируют цели и технологии цифровых и умных фабрик, а также создаются с целью управления цепочками поставок и для того чтобы создавать ценность посредством объединения продуктов и услуг. Основные технологии: ERP, CRM, SCM (Supply Chain Management, управление цепочками поставок) и др.
Цифровое предприятие предусматривает цифровизацию и интеграцию процессов по вертикали в рамках всего предприятия, начиная от разработки продуктов и закупок и заканчивая производством, логистикой и обслуживанием в процессе эксплуатации. В свою очередь, горизонтальная интеграция цифрового предприятия выходит за рамки внутренних операций и охватывает поставщиков, потребителей и всех ключевых партнеров по всей цепочке создания стоимости.
В соответствии с результатами данного исследования основные препятствия на пути к цифровизации, с которыми сталкиваются российские компании, – это недостаточная зрелость текущих бизнес-процессов и отсутствие необходимых навыков и компетенций.
1.4 Концепции непрерывного совершенствования
Концепций непрерывного совершенствования существует довольно много. Некоторые известны уже более 50 лет, например, бережливое производство, 6 Сигма. Некоторые появились относительно недавно, например, Индустрия 4.0, цифровая трансформация, цифровые двойники и др. Причем обычно не существует строгого определения концепции и их содержания.
Далее рассмотрим некоторые из них.
1.5 Индустрия 4.0
Промышленная концепция «Индустрия 4.0» – это глобальная, сложная, многоуровневая организационно-техническая система, основанная на интеграции в единое информационное пространство физических операций и сопутствующих процессов. Обычно выделяют шесть составляющих [6]:
– PLM – Product Lifecycle Management – Управление жизненным циклом изделия.
– Big Data – Большие данные.
– Smart Factory – Умное производство.
– Cyber-physical Systems – Киберфизические системы.
– Internet of Things (IoT) – Интернет вещей.
– Interoperability – Функциональная совместимость.
PLM (Product Lifecycle Management) – «управление жизненным циклом изделия»
Организационно-техническая система управления жизненным циклом изделий, основанная на принципе дуализма объект-операция/физическое-информационное.
Материальное-техническое обеспечение, производство, эксплуатация, утилизация и все сопутствующие процессы происходят в физическом пространстве, им соответствуют процессы, происходящие в информационном пространстве, протекающие в компьютерных системах. Поэтому для эффективного использования IT-технологий необходимо преобразовать процессы, происходящие в физическом пространстве в информационные проблемы, а также иметь возможность обратного преобразования информационных процессов в физические. Комплексы предметно-ориентированного прикладного программного обеспечения, также имеющие общее название PLM-системы, предназначены для структурирования массива данных и автоматизации управления физическими и информационными процессами на протяжении всего жизненного цикла изделия.
Big Data – Большие Данные
Совокупность подходов, инструментов и методов обработки структурированных и неструктурированных данных больших объёмов и значительного многообразия для получения воспринимаемых человеком или компьютерной системой результатов, эффективных в условиях непрерывного прироста, распределения по многочисленным узлам вычислительной сети. Данные собираются везде: от датчиков, сотрудников компании, компаний-контрагентов, клиентов, сервисных центров, поставщиков и т.д., поле чего данные структурируются, анализируются и используются. Основная задача предприятий при работе с Big Data, наилучшим образом интерпретировать данные для дальнейшего использования.
Управлять, структурировать, интерпретировать, анализировать и использовать данные – одна из основных наиважнейших задач организации производства в концепции Industry 4.0
Smart Factory – Умное производство
Термин Smart Factory используют преимущественно в англоязычной среде, он соответствует немецкому термину – Intelligente Fabrik. В русскоязычной среде, эти термины чаще всего переводят как «Умное производство».
Фундаментом «Smart Factory» является концепция «Digital Manufacturing». Digital Manufacturing – это организационно-техническая система моделирования производства основанная на продвинутых симуляторах на базе CAD. На сегодняшний существует несколько систем виртуализации производства, такие как: DELMIA Digital Manufacturing (Dassault Systèmes); Tecnomatix (Siemens PLM Software); Factory Design Suite (Autodesk); Visual Components и др.
Cyber-physical systems – Кибер-физические системы
Киберфизическая система – это организационно-техническая концепция управления информационными потоками, интеграция вычислительных ресурсов в физические процессы производства. В такой системе датчики, контроллеры и информационные системы объединены в единую сеть на протяжении всего жизненного цикла изделия. Кибер-физическая сеть может быть, как в рамках одного предприятия, так и в рамках динамической бизнес-модели в составе которой несколько предприятий. Операции на протяжении всего жизненного цикла взаимодействуют друг с другом с помощью стандартных интернет-протоколов для управления, планирования, самонастройки и адаптации к изменениям. Интернет вещей не может существовать без кибер-физические системы, так как CPS является инфраструктурой интернета вещей.
Internet of Things (IoT) – Интернет вещей
Интернет вещей – это простое определение грандиозной концепции. IoT – концепция вычислительной сети физических предметов (вещей), оснащённых встроенными технологиями для взаимодействия друг с другом или с внешней средой, рассматривающая организацию таких сетей как явление, способное перестроить экономические и общественные процессы, исключающее из части действий и операций необходимость участия человека. IoT связывает вещи, подключённые к интернету друг с другом и обеспечивает их совместную работу, управляемую облачными вычислительными системами. Интернет вещей обеспечивает взаимодействие физических производственных операций и сопутствующих процессов.
Концепция IoT сформулирована в 1999 году как осмысление перспектив широкого применения средств радиочастотной идентификации для взаимодействия физических предметов между собой и с внешним окружением. Наполнение концепции «интернета вещей» многообразным технологическим содержанием и внедрение практических решений для её реализации начиная с 2010-х годов является устойчивой тенденцией в развитии информационных технологий, прежде всего, благодаря повсеместному распространению беспроводных сетей, появлению облачных вычислений, развитию технологий межмашинного взаимодействия, началу активного перехода на IPv6 и освоению программно-конфигурируемых сетей.
Interoperability – Интероперабельность (функциональная совместимость)
Интероперабельность – наиважнейший фактор промышленной концепции Industry 4.0. Без функциональной совместимости, создать работоспособную интегрированную производственную систему «Industry 4.0» невозможно. К сожалению, компании-разработчики систем автоматизации долгое время развивали свои продукты без единых стандартов, не учитывая перспективы глобализации и потенциальные потребности в интеграции своих клиентов. При работе над проектами модернизации производства, обязательно нужно проводить проверку на интероперабельность автоматизированного оборудования и программного обеспечения.
Таким образом, Industry 4.0 – это совокупность технологий [6]: PLM, Big Data, Smart Factory, Cyber-physical systems, Internet of Things, Interoperability, позволяющих создать эффективную бизнес-модель предприятия. Высокая эффективность достигается главным образом за счёт рационального управления систем автоматизации физических операций производства и сопутствующих процессов интегрированных в единое информационное пространство.
1.6 Бережливое производство и цифровое производство
Интерес к методам Бережливого производства (БП или Lean manufacturing) не ослабевает уже более 40 лет, более того, он растет. Основные методы Бережливого производства зародились в то время, когда информационные технологии не играли заметной роли в производстве. В современном мире ситуация изменилась. Уже трудно представить разработку изделия без 3D моделирования, управление конструкторскими и технологическими данными – без PDM/PLM системы, изготовление без станка с ЧПУ, для которого программа создана в CAM системе. Работа с заказами, с финансами ведется в ERP системе, работа с поставщиками – в SCM системе. Управление производством – это область, где используются системы оперативного управления производством или MES системы. Однако большинство публикаций по бережливому производству в России, по прежнему, игнорируют современные ИТ системы [7].
Одно из определений Цифрового производства гласит: Цифровое производство – интегрированная компьютерная система, включающая в себя средства численного моделирования, трехмерной (3D) визуализации, инженерного анализа и совместной работы, предназначенные для разработки конструкции изделий и технологических процессов их изготовления. Цифровое производство начиналось с таких инициатив, как конструирование с учетом технологичности (DFM), компьютерно-интегрированное производство (CIM), гибкое производство, бережливое производство и других. Как видим, Бережливое производство здесь фигурирует как составная часть Цифрового производства.
Какие же методы Бережливого производства внедряют чаще? В России в основном применяют такие инструменты как 5S (оптимизация рабочих мест), SMED (быстрая переналадка оборудования), VSM (карты потока создания ценности), т.е. улучшения в основном затрагивают лишь сам производственный процесс. Там же отмечается, что «крайне мало внимания уделяется интеграции Lean-инструментов с современными информационными технологиями управления производством, такими как ERP, APS, MES и др.».
Концепция БП не является просто набором инструментов по снижению издержек, которые можно использовать отдельно друг от друга. Однако компании часто фокусируются на отдельных аспектах процесса, вместо того чтобы акцентировать внимание на процессе в целом. Таким образом, концепция LP выступает как группа решений, которые необходимо применять одновременно: совершенствование производственного процесса с целью снижения издержек (SMED, just-in-time, kanban, SOP, TPM, 5S, VSM); постоянное улучшение качества (Кайдзен, Jidoka); обучение и мотивация персонала (Кайдзен, 5S); создание «вытягивающей системы» от конечного потребителя продукции (just-in-time, kanban, VSM). Однако, при таком подходе только ручными методами уже не обойтись.
Исследование компании ARC проводилось среди лидеров использования Бережливого производства и лидеров использования MES систем. Задача была – сопоставить лучшие практики и найти корреляцию между ними. Было выявлено, что 77% компаний используют MES системы в своих программах Непрерывного улучшения, проводимых по методикам Lean и Six Sigma. Рассмотрим некоторые соображения в пользу использования ИТ систем предприятия (чаще всего MES) совместно с методами бережливого производства.
MES система постоянно работает с изменениями
Одна из ключевых особенностей применения методов Бережливого производства – это способность изменять процессы, оптимизируя их. Однако это делается не оперативно. MES контролирует правильность выполнения процессов, отслеживает отклонения и оперативно реагирует на них, т.е. выполняет мониторинг процесса. Применение MES более эффективно, если исходный процесс построен методами БП, и в нем уже устранены многие потери. Дополнительно MES оперативно реагирует на отклонения типа поломки станка, изменение параметров заготовки, появление более приоритетных заказов и т. д. Можно сказать, что БП оптимизирует процессы методологически, а MES обеспечивает выполнение этой методологии.
Электронный Канбан
Канбан – в традиционных Lean программах это карточки, сигнализирующие о количестве материалов, о потребности в них и дающие указания по их перемещению на следующую операцию. Обычно они связаны с так называемым «вытягивающим» планированием, позволяющим существенно минимизировать промежуточные накопители полуфабрикатов. Идеология Канбан: «не делать ничего лишнего, не делать раньше времени, сообщать о возникающей потребности только тогда, когда это реально необходимо». Обычно они используются внутри одного предприятия.
Методами Lean можно оптимизировать вид и объем информации, а передавать эту информацию между рабочими местами (а также между предприятием, поставщиками и заказчиками) может MES система. Более того, в этом варианте можно отображать не всю информацию, а только ту, которая нужна на конкретном рабочем месте и в данный момент. Т. к. MES обычно интегрирован с другими системами предприятия, информация для канбана может поступать из других систем или передаваться в другие системы.
Планирование производства
MES системы используют различные критерии при планировании производства и даже комплексные показатели как совокупность разных критериев. То же относится к оптимизации маршрутов движения деталей в цехе. MES может в реальном времени пересчитать маршрут в случае, например, выхода из строя одного из станков.
MES может создавать так называемые «пробные планы», сравнить их и конвертировать один из них в реальный план. Также MES может служить инструментом анализа «Что если», можно виртуально проверить последствия планируемого изменения процесса.
Данные для быстрой переналадки SMED и обслуживания оборудования TPM, полученные методами БП, учитываются в MES при планировании производства. Причем учитываться могут различным способом в зависимости от критериев планирования.
Точно в срок (Just in time, JIT), Выстраивание потока (Continuous Flow), Хейджнка (Heijunka) – инструмент выравнивания заказов в производстве – все это обычно встроено в MES системы разработчиками как набор инструментов. Однако, как показала практика, реальное производство сложнее. И там используются разные подходы и наборы инструментов в зависимости от конкретного случая. Например, использование накопителей или промежуточных складов является злом с позиций БП, но может быть оправдано и эффективно при компьютерном планировании. В этом случае, их емкость – еще один параметр для оптимизации производственного процесса.
Автоматизация сбора данных
Сбор данных для анализа методами Lean может быть весьма трудоемким. Современное оборудование часто позволяет данные измерения или данные о состоянии оборудования снять и передать в ИТ системы автоматически. Алгоритмы анализа данных MES системы позволяют рассчитать более сложные характеристики (включая КПЭ – ключевые показатели эффективности) и использовать их в отчетах.
Частота расчета КПЭ лидерами по данным исследования компании ARC Advisory Group (дано по работе [7]) (табл. 1.1).
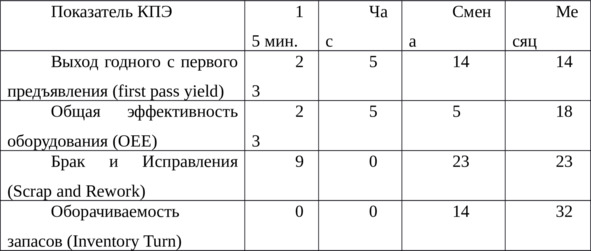
Здесь приведены показатели, которые часто используются в программах Бережливого производства. Нам здесь важно, что некоторые предприятия вычисляют эти показатели каждые 15 минут. Понятно, что это невозможно сделать без автоматизации расчета на основе одной из ИТ систем. Компания ARC прямо пишет, что первые 2 показателя, для которых расчет выполняется каждые 15 минут или час, рассчитываются в MES системе. Для расчета показателей, которые рассчитываются раз в смену или реже, используются ERP или MES системы.
Электронные отчеты в реальном времени и оповещения персонала
Отчеты также могут быть электронными и динамическими, отражающими реально текущую информацию. Такие отчеты могут оперативно показать проблему (например, на табло в виде электронной планировки цеха (рис. 1.4). А это влияет и на оперативное принятие решений в производстве.
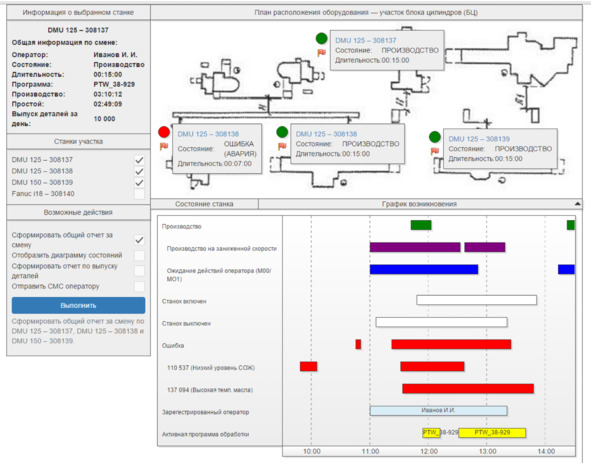
Рис. 1.4. Пример табло системы DPA в виде электронной планировки цеха (дано по работе [7])
В MES поддерживаются различные способы оповещения персонала. Это и мониторы реального времени (дашборды) с выделением цветом, звуком состояний, требующих внимания, и уведомления на электронную почту, через SMS, через специальное приложение на рабочее место специалиста и др.
Визуализация
Визуализация (Visual Factory) как метод простых и понятных индикаторов, используемых на заводе для обмена информацией, является частью БП. При интеграции с MES он может быть реализован на новом уровне.
Виртуальное производство в PLM среде
Выше мы говорили больше о MES системах для более эффективного использования методов бережливого производства. Для предприятий сложного машиностроения эффективное внедрение MES систем невозможно без PLM систем, автоматизирующих стадии конструкторско-технологической подготовки производства.
Развитие функционала цифрового моделирования в PLM системах привело к появлению терминов Виртуальное производство, Цифровое производство, Цифровой двойник и др.
Цифровое производство позволяет осуществлять имитационное моделирование производственных процессов, направленное на повторное использование существующих знаний и оптимизацию технологии до начала выпуска изделия. Кроме того, цифровое производство позволяет получать обратную связь от реальных технологических операций и встраивать ее в процесс конструирования изделия, благодаря чему предприятия уже на этапе разработки могут решать производственно-технологические задачи.
Такой подход вписывается в концепцию Непрерывного совершенствования, когда улучшения процесса изготовления, выполненные в цехе, влияют и на саму конструкцию изделия либо на первоначальный техпроцесс.
1.6 Цифровые двойники
Цифровой двойник – это виртуальное представление изделия или процесса, которое используется, чтобы оценивать и прогнозировать рабочие характеристики этого изделия или процесса. Цифровые двойники используются на протяжении всего жизненного цикла изделия, чтобы проводить инженерный анализ, прогнозировать и оптимизировать работу изделия или производственной системы, прежде чем инвестировать в физические прототипы и ресурсы [8].
Благодаря мультифизическому моделированию, аналитике данных и машинному обучению цифровые двойники могут демонстрировать влияние изменений конструкции, различных сценариев использования, условий окружающей среды и других факторов на изделие или процесс и избавляют от необходимости изготовления физических прототипов. Это позволяет сократить время разработки и повысить качество получившегося в результате изделия или процесса.
Чтобы обеспечить точное моделирование на протяжении всего жизненного цикла изделия или его производства, цифровые двойники используют данные с датчиков, установленных на физических объектах, чтобы фиксировать производительность объекта в реальном времени, условия работы и изменения с течением времени. Используя эти данные, цифровые двойники совершенствуются и постоянно обновляются в соответствии с изменениями физического аналога на протяжении жизненного цикла изделия. Таким образом, возникает замкнутая обратная связь в виртуальной среде, которая позволяет компаниям постоянно оптимизировать свои изделия, производство и повышать производительность с минимальными затратами.
Область применения цифрового двойника зависит от того, на каком этапе жизненного цикла изделия происходит моделирование. Можно выделить 4 типа цифровых двойников: двойник изделия, двойник производства и двойник процесса, цифровой двойник эксплуатации. Видение компании Сименс показано на рис. 1.5
Цифровых двойников может быть сколь угодно много, они создаются под задачу и имеют детализацию, необходимую для ее решения.
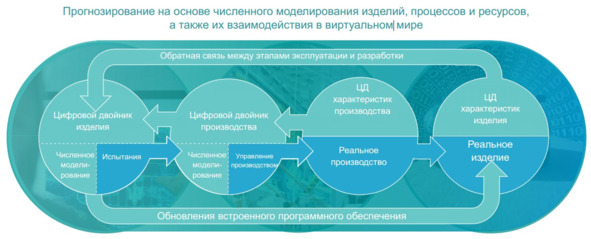
Рис. 1.5. Цифровые двойники (Видение компании Сименс)
Цифровые двойники изделия
Цифровые двойники могут использоваться для виртуальной проверки характеристик изделия. Они также показывают, каким образом изделия функционируют в реальном мире. Этот цифровой двойник изделия обеспечивает связь между виртуальным и физическим миром. Такая связь позволяет проводить разные типы анализа, чтобы понять, как изделие будет вести себя в разных условиях. По результатам анализа можно внести изменения в виртуальную модель, чтобы следующее физическое изделие полностью соответствовало необходимым характеристикам. Неважно, насколько сложна система или материалы – цифровые двойники изделия помогают успешно преодолевать эти сложности и принимать самые оптимальные решения. Больше не нужно создавать множество физических прототипов, сокращается срок разработки, повышается качество итогового изделия. Кроме того, при наличии цифрового двойника можно гораздо быстрее отреагировать на замечания заказчиков.
Цифровые двойники изделий можно разделить на подтипы [8]: двойники-прототипы (Digital Twin Prototype, DTP), цифровые двойники-экземпляры (Digital Twin Instance, DTI) и агрегированные двойники (Digital Twin Aggregate, DTA). Цифровые двойники производственной системы: инжиниринговая и эксплуатационная модель производства
Цифровые двойники-прототипы (Digital Twin Prototype, DTP). DTP-двойник характеризует изделие, прототипом которого он является, и содержит информацию, необходимую для описания и создания физических версий экземпляров изделия.
Digital Twin Instance – цифровой двойник экземпляра. Фактически, это сбор информации с датчиков, установленных на оборудовании, и получение копии работающей единицы в системе. Это позволяет автоматически отслеживать и прогнозировать поведение этого оборудования, предсказывать аварийные остановы и создавать симуляции режимов работы.
Digital Twin Aggregate – модель серии оборудования. Это двойник существующего оборудования, которая в первую очередь применяется для обучения персонала и оптимизации процессов ТОиР. С такой моделью специалисту не нужно читать мануалы по эксплуатации оборудования, а можно сразу практиковаться и смотреть результаты действий на виртуальной модели.
Цифровые двойники производства
Цифровой двойник производства позволяет до начала фактического производства понять, насколько хорошо будет работать производственный процесс в заводском цехе. Моделируя процесс с помощью цифрового двойника и анализируя происходящее с помощью цифровой связи, компании могут создать методологию производства, которая будет эффективной при самых разных условиях [3].
Цифровой двойник» производственной системы включает в себя:
– Инжиниринговую модель ПС, содержащую цифровое описание ресурсов предприятия, структуру станочной системы, средства технологического оснащения, номенклатуру и технологии изготовления изделий, систему сбора информации о текущем состоянии оборудования.
– Эксплуатационную модель ПС, являющуюся цифровой платформой для описания логистической архитектуры предприятия, формирования планов-графиков изготовления изделий, межцеховой и внешней кооперации, включая регламенты технического обслуживания и ремонта оборудования. Математическому описанию также подлежит динамика внутрицеховых материальных потоков, на основе цифровизации которых формируются оптимальные производственные расписания выполняемых работ.