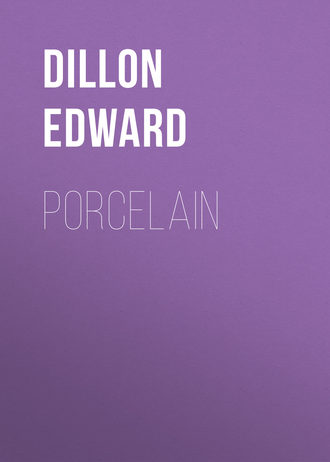
Полная версия
Porcelain
The punch-bowl of porcelain, however, came to the rescue about this time.
152
In the porcelain gallery at Dresden may be seen (together with one or two small lumps of gold and silver, the results of Böttger’s alchemistic experiments) some snuff-boxes and little flasks of a marbled glass, made by Tschirnhaus at an early date. It is probable that the latter experimenter’s researches lay rather in the way of a frit-made soft paste, on the same lines as the contemporary attempts in France.
153
And yet, forty years later (so well was the secret kept), it was maintained by practical authorities in France that the Saxon ware was no true porcelain, but only some kind of hard enamel. See Hellot’s Mémoire, quoted below.
154
We hear, however, of Dutch potters being engaged as early as 1708, and with their assistance Böttger, in 1709, made some imitations of Delft ware.
155
In a contemporary German pamphlet, which I only know from a French translation (Secret des Vrais Porcelaines de la Chine et de Saxe, Paris, 1752), a certain ‘spath alkalin’ is mentioned as an important element in Saxon porcelain, and this substance is identified with the petuntse of the Père D’Entrecolles.
156
If this colour is derived from the purple of Cassius, as seems probable, it is an important instance of the early use of this pigment upon porcelain.
157
Above all the famous ‘Swan Service’ of 1736, Kändler’s masterpiece.
158
We had in England until lately an unrivalled collection of these little groups—priceless specimens of the best period. They were exhibited by their owner, Mr. Massey Mainwaring, for some time at Bethnal Green. This collection has, however, now found its way to America.
159
On the other hand, as early as 1732 the Meissen ware was finding its way to the East. Quantities of little coffee-cups (known as Türken Copjen, corrupted into Türken Köpfchen) were sent to Constantinople to be re-exported to other Mohammedan countries.
160
We may remind the reader that it was a syndicate of Berlin merchants who at an earlier date sought, it is said, to purchase from Böttger his secret. There is little doubt, however, that the anecdotes about Ringler, which abound in the notices on German porcelain, are little more than ‘porcelain myths.’ Very similar anecdotes are told of the early days at Vincennes, and in Japan, as we have seen, such stories sometimes take a more tragical form. There is a strong temptation, no doubt, in traversing the somewhat arid ground of German ceramics, to fall back on such tales. At all events they belong to the class of tendenz Mährchen, and illustrate the difficulties to be overcome at that time in starting a new factory.
161
Not but that we have proof of his interest in the subject, as the following letter, dated Meissen, March 28, 1761, will show. It is written to Madame Camas, his chère Maman, who was then with the queen at Magdeburg:—‘I send you, my dear mamma, a little trifle, by way of keepsake and memento. You may use the box for your rouge, for your patches, or you may put snuff in it or bonbons or pills.... I have ordered porcelain for all the world, for Schönhausen, for my sisters-in-law,—in fact I am rich in this brittle material only. And I hope the receivers will accept it as current money: for the truth is, we are poor as can be, good mamma. I have nothing left but my honour, my coat, my sword, and my porcelain.’—Carlyle’s Frederick the Great, Book xx. chap. vi. Marryat, who gives this letter in his notes, mixes up Carlyle’s comments with the text.
162
The Hohenzollern shield bears two sceptres in saltire en surtout.
163
Another account gives the credit to Von Löwenfinck, a porcelain painter from Meissen.
164
Politically, that is to say; for the town formed part of the ‘Pays d’Étrangers,’ and its commercial and social relations were still rather with Germany than with France.
165
I take these facts about the Hannong family from Sir A. Wollaston Franks’s Catalogue of Continental Porcelain, 1896.
166
In the same year we find Count Schimmelmann, who at a later date interested himself in the Copenhagen factory, selling by auction at Hamburg some of the vast stocks of Meissen china that Frederick had thrown on the market.
167
As a royal factory, however, it became extinct in 1864. See chap. xxiii.
168
Thus we have, during the Seven Years’ War, Frederick’s three bitter opponents—Maria Theresa in Austria, Elizabeth in Russia, and the Marquise de Pompadour in France—all taking an active interest in promoting the manufacture of porcelain, and this rivalry may have added to the zest of Frederick when he looted Meissen and sought to make Berlin take its place as the metropolis of porcelain.
169
An American writer has arranged the tests by which soft pastes may be distinguished from true porcelains under six heads. 1. The file test.—Soft porcelain may be marked by a file. 2. The foot test.—In hard porcelain the foot is generally rough and unglazed. This test is rather of value in distinguishing porcelain from fayence. 3. The fire test.—Depending on the greater fusibility of the soft pastes. 4. Chemical test. 5. Colour test.—Soft paste is generally mellow ivory by transmitted light, and this is especially true of ‘bone-ware.’ The hard paste tends to bluish shades. 6. Fracture test.—The fracture is glassy to vitreous, and the glaze passes into the paste in the case of hard pastes (the subconchoidal splintery fracture is rather the point to observe); dry and chalky, and the glaze more or less separated from the paste in the case of soft pastes.—E. A. Barber, Pottery and Porcelain of the United States, New York, 1901.
170
De Réaumur, we must remember, had made some kind of hard-paste porcelain from Chinese materials. After that he fell back upon his devitrified glass. Something very similar had been made by Tschirnhaus many years before.
171
These, I think, are almost the only instances in which a distinctly seventeenth century decoration is to be found on porcelain.
172
These trembleuse saucers of the early eighteenth century have a projecting ring into which the base of the teacup fits.
173
The extreme limits for this mark are 1712-62, but Chaffers says it was not used before 1730, according to another authority not before 1735. De Frasnay, in a note to his curious little poem in praise of fayence (1735), says: ‘le secret du beau rouge n’est guère connu en France que d’un très petit nombre de personnes.’ The point is of interest in connection with the origin of the famille rose in China. We may here note that the minute quantity of gold—the source of all these pink and purple colours—is not necessarily introduced in the form of the tin salt, the purple of Cassius. But this difficult question will be best treated in connection with the history of glass.
174
Generally known as the Duc de Bourbon (1710-40). He was an enthusiast for the art of the Far East. An important work on Chinese art was published under his auspices in 1735. He imitated the painted hangings of the East, and even attempted to make Japanese lacquer. After his death, the two brothers Dubois, épiciers à Chantilly, migrated to Vincennes, and the Chantilly works were for a time neglected. See Gustave Macon, Les arts dans la Maison de Condé, 1903.
175
Of the many European imitations of the ‘Kakiyemon’ style the Chantilly is most successful, while the ‘Old Japan’ was best copied at Chelsea. No European imitation in porcelain of the Chinese blue and white approaches in brilliancy that made in Delft ware in the seventeenth century.
176
The porcelain of Saint-Cloud and Chantilly is well represented in the Fitzhenry collection.
177
Some twenty miles south of Paris, not far from Corbeil.
178
The name is written ‘Sèves’ in English catalogues of the eighteenth century, and the same form is found sometimes in contemporary French writings. We may compare the favourite signature ‘Fédéric’ of the Prussian king.
179
Mémoire Historique pour la Manufacture, rédigé en 1781 par Bachelier, re-edited, with preface and notes, by G. Gouellain, Paris, 1878.
180
See the note on p. 286. It would seem that the first successes at Vincennes were, in a measure, dependent upon the temporary breaking up of the factory at Chantilly on the death of the Duc de Bourbon in 1740.
181
At a later time this man had a contract for the delivery of the paste, the secret of which he preserved, at a fixed rate per pound. In one year he is said to have received for this 800,000 livres!
182
Such is my general impression, but M. Garnier, I see, speaks highly of his artistic capabilities. Bachelier founded in 1763 a free school of design, one of the few institutions of the old régime that have survived the many changes of government. It still exists as the École Nationale des Beaux-Arts.
183
By this we get a hint as to the kind of ware made at Vincennes at the commencement, when under the influence of Chantilly.
184
The account-books of these sales are still preserved. M. Davillier, in his little book on Les porcelaines de Sèvres et Madame du Barry, quotes the record of purchases made (at a later date, for the most part) by the royal family, by Madame du Deffand, and by M. de Voltaire. The latter bought, for 120 livres, ‘Deux bustes de mondit Sieur, en biscuit.’ Besides this, large sales were made yearly to the trade.
185
The above description is that given by the Prince de Ligne in his memoirs. In the Johanneum at Dresden there is now to be seen a ‘bouquet’ which in every way corresponds to the prince’s account. The Meissen works for long had the credit of this trophy, but it is now acknowledged that it is identical with the present sent by the dauphine, in 1748, to her father, the Elector of Saxony. M. Davillier quotes a curious account from a contemporary memoir describing the difficulties and expenses incurred in transporting this ‘bouquet’ from Paris to Dresden. Are we, then, to regard it as the actual present given by M. de Fulvi to the queen, or as a duplicate?
186
See for this and other references to porcelain in the chronique scandaleuse of the day, the little book of M. Davillier quoted above.
187
Some attention was paid to the housing and comfort of the workmen at the new establishment, but Bachelier makes no mention of ‘the gardens, cascades, fruit-trees, groves, woods, and a small chase for the artists, who enjoyed to hunt the stag and the wild boar none the less for their sedentary lives in the art palace’ (Marryat, p. 414). On the contrary, we are told that in a few years the houses and workshops were already threatening to fall down on the workmen’s heads.
188
M. Bertin was himself a great collector of Chinese porcelain. In the avertissement of the catalogue of his collection which was sold in Paris in 1815, we are told that through the medium of the Père Amiot he obtained many choice specimens, some of them direct presents from the Chinese emperor. We have already alluded to Kien-lung’s interest in exotic wares, and to the influence of these upon the native decoration.
189
In the fond lapis caillouté the deep blue ground is painted with fine veins of gold, to imitate the pyrites which generally accompanies the native stone (lapis lazuli). It was used as early as 1758 (see Wallace collection, Gallery xviii., Case c.).
190
As many as one hundred and sixty pieces, it is said, were carried off during a fire at Tsarskoe Selo. Some of these were afterwards repurchased by the Tsar Nicholas.
191
Marryat quotes a passage to the following effect from a little work published at Venice soon after the death of the favourite. Praising the good taste of the ‘Madame Marchesa,’ the writer states that this was, above all, manifested in the adornment of her table. All the porcelain was expressly manufactured for her at Sèvres, and was of a rose colour mixed with gold. The value amounted to 257,000 livres, and no sovereign possessed a service of equal beauty.
192
It is found as a ground on pieces bearing the earliest letter-marks, so that it is difficult to accept the statement that it was first made by Xhrouet, a painter of landscapes, in 1757.
193
Much of it found its way to England, and was there decorated in the old Sèvres style, both in London and in the West.
194
For a detailed description of these deposits and their geological relations, see Brongniart’s great work.
195
Napoleon at one time sent Daru to Sèvres to convey to Brongniart, in the most lively terms, his dissatisfaction with what he called the simplicity and tameness of the designs in use at Sèvres. Every piece should, he protests, ‘dire quelque chose.’ Every plate should record glorious deeds, the capture of the enemy’s towns, or the triumphant return of the victors.
196
We must, however, place some of these discoveries to the credit of the staff of the Viennese factory, and Dihl again, the chemist of the porcelain works in the Rue de Bondy, has a claim to others.
197
The death of M. Garnier occurred since the above was written.
198
The use of a bone-paste ware of the ‘Spode’ type is, however, now prevalent not only in many parts of the continent, but porcelain of this kind is now largely made in the United States.
199
Unless it be in the catalogue drawn up by Sir A. W. Franks for his collection of continental china. The ceramic collection in the Hamburg Museum has also been very thoroughly catalogued by Dr. Brinckmann.
200
It is curious to find Venice at this time exporting porcelain to the East, for at an earlier period it was through this town that so much Oriental porcelain and fayence reached Europe.
201
This Venetian china, either of hard paste or of the hybrid class, must not be confused with the opaque glass, the lattimo, or, more properly, Latisuol, ware, made about 1730 in imitation of porcelain both at Murano, and also near Bassano.
202
Compare with this the use of steatite, a magnesian rock, from the Lizard, at Worcester, and at other West of England factories. The Chinese have also at times made use of a steatitic rock.
203
Marryat (p. 451) gives an interesting account of this enterprising man. He was occupied also in the draining of marshes, the improvement of agriculture, and the promotion of commerce.
204
With this appointment we may perhaps connect the elaborate trophy of white porcelain at South Kensington. The figures of slaves on which this is supported are modelled after those of Tacca on the celebrated monument at Leghorn. This piece is attributed, however, to the Capo di Monte factory.
205
The word ‘china’ is sometimes used in Spain in the same vague sense as in England, but the name seems only to have come in with the Staffordshire ware so largely imported in the last century. Note, however, that the factory at Buen Retiro was known as La China.
206
I quote this remarkable passage from Sir A. W. Franks’s paper on the origin of the Chelsea porcelain works (Archæol. Journal, 1862). Marryat misquotes and misinterprets the passage.
207
One possible exception to this very general statement may be found in a pamphlet quoted by Mr. Solon, Instructions how to make as good china as was ever sold by the East India Company by A. Hill, London, 1716. According to this writer, fragments of Oriental china were to be finely ground and mixed with fluxing and plastic materials to form a paste. Now there is evidence that at a much later date ‘potsherds’ were imported from China, and ground up to form an ingredient of the porcelain, both at Bow and at Worcester.
208
The memorandum-book of Duesbury, the future porcelain king, begins in 1742. He was then working, on weekly wages, as an ‘enameller’ of china figures. But was the ware that he was decorating at this time a true porcelain?
209
Mr. Burton says that at the present day the Staffordshire porcelain is composed of bone-ash 6 parts, china-stone 4 parts, and kaolin 3½ parts.
210
Mr. Willett, of Brighton, has a pair of ‘goat and bee’ jugs in silver, with the hall-mark of 1739.
211
There is an interesting series of these very early pieces in the British Museum. A white ware salt-cellar, with crayfish in relief, has the triangle mark. A jug, in the form of a grotesque Chinaman, is a good specimen of the early paste. We notice the same waxy look in the paste that we find in the Saint-Cloud ware. The surface, however, is generally grayer.
212
In 1758 we find an advertisement of a house to let in ‘China Walk,’ Chelsea.
213
Both Gouyn and his successor, Sprimont, were very likely Walloons from the neighbourhood of Liége. In a contemporary work, however, the latter is spoken of as ‘a French artist of great abilities.’ Rouguet’s Present State of the Arts, 1755.
214
Note the term ‘earthenware.’ As in a much earlier proclamation of the time of Charles ii. (forbidding the importation of painted earthenware, except ‘those of China, and stone bottles and jugs’), the word is used officially to include porcelain.
215
Such a regulation would seem to show that in England the enamel-painters were in the field earlier than the manufacturers of porcelain.
216
The later date is supported by the statement of Sprimont in his ‘Case,’ that ‘the ground flat of the manufacturer has gone on still increasing,’ for we know that the works were enlarged in 1757. The expression ‘crowned head’ applies better to the King of Prussia than to the Elector of Saxony. In 1760, as we have seen, Count Schimmelmann was at Hamburg selling, on behalf of Frederick, part of the vast stocks accumulated at Meissen.
217
In a London paper of December 4, 1763, appeared the following statement—I quote from Mr. Nightingale’s book,—‘A few days since, his R. Highness the Duke of Cumberland was at Mr. Sprimont’s manufactory at Chelsea, and we are informed that his Highness will shortly purchase the same, that so matchless an art should not be lost.’ A week later, however, a formal contradiction of this report appeared in another paper, in the form of a note at the end of an advertisement of the sale of the contents of Sprimont’s factory. All this has a very modern air. We have a skilful combination of the ballon d’essai and the puff preliminary.
218
This collection has lately disappeared from its old home in the Geological Museum, where it had been the delight of two generations of collectors. Most of the specimens have, however, quite recently been discovered at South Kensington.
219
Much of the white ware at this time was decorated outside by ‘chamberers.’ Compare the memorandum-book of Duesbury quoted below.
220
The advertisement of these sales in contemporary newspapers, and many of the catalogues, have been collected together and reprinted by the late Mr. J. E. Nightingale.
221
Before this time the gold had been simply laid on with japanner’s size and only gently heated. See Burton’s English Porcelain, p. 46.
222
There was a revival of the practice of mounting, or, to use the old term, ‘garnishing’ porcelain in ormolu about this time. At Boulton’s works at Soho, near Birmingham, famous, a little later, in the history of the steam-engine, these metal mountings were largely made, and Wedgwood began to apply them to some of his wares (see Nightingale, p. xxxiv.).
223
I can find no confirmation of the statement that Roubiliac modelled figures for Sprimont. Certain statuettes bearing an R. impressed on the paste have been attributed to him. There is no reference to any such work in the life of the artist by M. Le Roy de St. Croix (Lyons, 1886). Roubiliac, who died in 1762, was already in 1750 at the height of his reputation, and fully employed in more important work.
224
Mr. Burton points out that it would be quite impossible to make a translucent ware with the materials of the first patent. He doubts also the use of bone-ash in the earlier porcelain of Bow, the paste of which is distinctly of the Saint-Cloud type. I think, however, that there can be little doubt but that the ‘virgin earth’ refers to bone-ash, and the fragments from Bow in which this substance has been found seem to be derived from an early ware.
225
Specimens from this find may be seen at the British Museum, at South Kensington, and in the late Jermyn Street collection. An interesting and detailed account of the fragments, which were excavated and arranged by Mr. Higgins of the adjacent match-works, will be found in Chaffers’s Marks, pp. 908 seq.
226
This difficulty of making the decoration keep pace with the outturn of the kilns was felt at this time at other kilns—from King-te-chen to Sèvres and Worcester. Recourse was more and more had to the outside enameller—the ‘chamberer’—on the one hand, and to transfer-printing on the other.
227
This document is exhibited at the British Museum by the side of the punch-bowl.
228
These figures are probably exaggerated. Sprimont, a little earlier, says that he was employing at Chelsea ‘at least one hundred hands.’
229
‘Printed teas and mugs’ are mentioned in Bowcocke’s memorandum-book in 1756.
230
See Nightingale’s English Porcelain, pp. li. seq., and Bemrose’s Bow, Chelsea, and Derby Porcelain, pp. 153 seq.
231
The rococo vases, however, of this ware in the British Museum seem to be of a somewhat later date, if we take Sprimont’s work at Chelsea as a criterion.