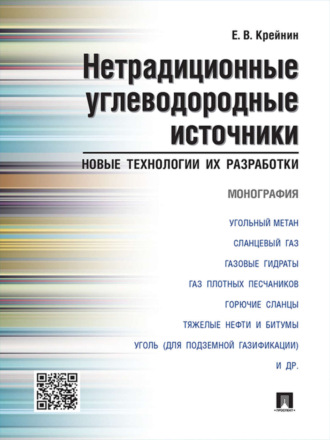
Полная версия
Нетрадиционные углеводородные источники: новые технологии их разработки. Монография
Тунгусский и Ленский угольные бассейны в настоящее время крайне слабо изучены. Тем не менее, по существующим оценкам, они имеют большой потенциал в будущем благодаря предполагаемым значительным ресурсам угольного метана в них, их плотности на различных глубинах (до 230 млн м3/км2), а также высокой природной метаноносности углей (до 40 м3/т).
Помимо рассмотренных наиболее крупных угленосных регионов Российской Федерации, значительным потенциалом в качестве источников метана обладают Таймырский, Горловский, Южно-Якутский, Зырянский, Буреинский и Сахалинский бассейны.
Таким образом, угленосные площади Российской Федерации имеют существенно больший потенциал как источник этого нетрадиционного вида топлива, чем многие угольные бассейны в мире.
Отмеченные выше малоэффективные методы шахтной дегазации угольных пластов, заключающиеся в бурении с поверхности или из шахтных выработок различных скважин с дальнейшим вакуумированием метановоздушной смеси, являются практически обязательным этапом разработки метаноносных угольных месторождений.
Однако периодически случающиеся аварии (например, в Кузнецком и Печорском бассейнах и Восточном Донбассе), вызванные взрывами метановоздушной смеси в шахтных выработках, свидетельствуют о малой степени извлечения метана из углепородного массива при предварительной его дегазации. Необходимы более эффективные методы дегазации угольных пластов.
Низкая газопроницаемость каменноугольных пластов обусловливает их невысокую метаноотдачу. Отсюда, очень важно при дегазации применять методы искусственного увеличения метаноотдачи углепородного массива путем его гидравлического разрыва.
Первые гидравлические разрывы угольного пласта с целью его разупрочнения были осуществлены в Донбассе в 1955 г., на Лисичанской станции «Подземгаз», при научном и инженерном руководстве ученых Всесоюзного научно-исследовательского института подземной газификации угля. Позже к этой проблеме активно подключились ученые Московского горного института, Института горного дела им. А. А. Скочинского, Научно-исследовательского института геомеханики и маркшейдерского дела, Института проблем комплексного освоения недр Российской академии наук и др.
Очень эффективными для интенсификации метаноотдачи оказались способы физико-химической обработки созданных щелей гидравлического разрыва в угольном пласте [31]. В качестве рабочих жидкостей применялись химически-активные растворы (например, соляная кислота), поверхностно-активные вещества, а также растворы комплексов.
Опыт физико-химического воздействия на угольные пласты Карагандинского и Донецкого угольных бассейнов показал следующее:
• воздействие соляной кислоты повышает метаноотдачу на 25–35 %, по сравнению с обычной скважинной вакуумной дегазацией, степень дегазации возрастает до 40–50 %;
• последовательное воздействие на угольный пласт растворов соляной кислоты и поверхностно-активных веществ повышает метаноотдачу на 50–60 %, а степень извлечения метана возрастает до 60–70 %.
В настоящее время идет поиск и апробирование новых методов повышения метаноотдачи угольных пластов как при шахтной (предварительной), так и при промысловой (заблаговременной) дегазации метаноугольных месторождений. К этим методам следует отнести: протяженные горизонтальные скважины, волновое и вибрационное воздействие на угольный пласт, закачка в метаноносный пласт инертных газов (углекислого газа, азота), а также другие методы.
Работы по промысловой (заблаговременной) дегазации угольных пластов в Российской Федерации только начинаются, в то время как в США, Австралии, Китае, Индии, Польше и других странах они находятся на промышленной стадии.
1.4.1. Экспериментальный опыт в Кузбассе
Первые экспериментальные работы по обоснованию промышленной добычи метана из угольных пластов Кузбасса были начаты ОАО «Газпром» в 2001 г. В результате проведенных геолого-разведочных работ наиболее перспективными для добычи метана были признаны Талдинская и Нарыкско-Осташкинская площади [15].
Первые четыре экспериментальных скважины были пробурены в 2003–2004 гг. на Талдинской синклинали, а в 2008 г. Государственная комиссия по запасам полезных ископаемых (ГКЗ «Роснедра») утвердила первые запасы метана по промышленным категориям С1 + С2 в количестве 45 млрд м3 [32].
Основные характеристики метаноугольной толщи:
• угленосность – от 5 до 12 %;
• метаноносность – до 25 м3/т;
• плотность ресурсов метана – 2,0–2,5 млрд м3/км2;
• газопроницаемость угольных пластов – 0,001–0,02 мкм2.
На рис. 4 представлен геологический разрез по одной из экспериментальных скважин (УМ-1.1). Как правило, в каждой скважине вскрывалось 3–5 угольных пластов, в каждом из которых проводили гидравлический разрыв с закачкой твердого пропанта в количестве от 8 до 20 т.
В процессе пробного освоения экспериментальных скважин на Талдинском метаноугольном месторождении были отработаны основные технологические этапы:
• бурение и обустройство метаноугольных скважин;
• процесс и последовательность гидравлического разрыва нескольких угольных пластов;
• откачка подземных вод и понижение их динамического уровня;
• извлечение угольного метана и его промысловая подготовка;
• варианты использования добытого метана.
За два года (2010–2011 гг.) эксплуатации 7 экспериментальных скважин было извлечено 11 млн м3 метана.
На Нарыкско-Осташкинской площади в течение 2011–2012 гг. бурили первые промысловые скважины (30 скважин, в соответствии с проектом) и в дальнейшем планируют их промышленную эксплуатацию.
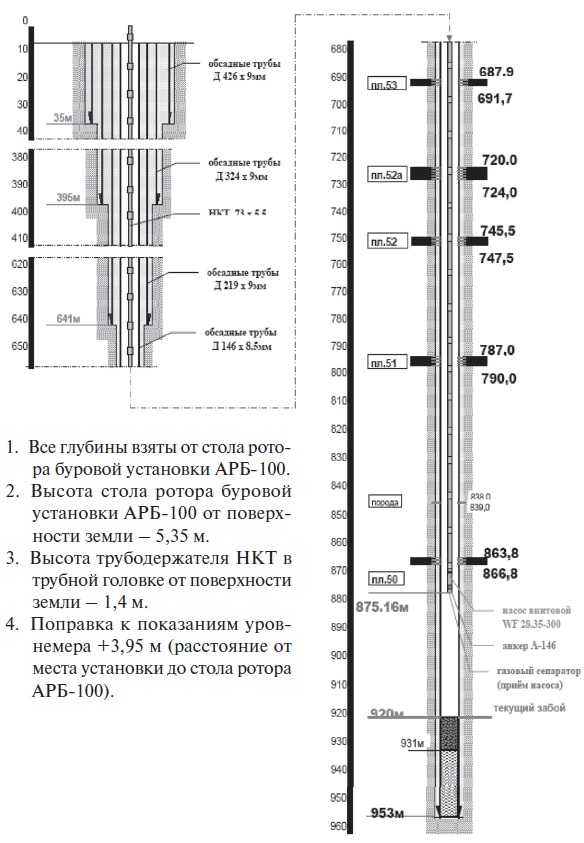
Рис. 4 – Геологический разрез по экспериментальной скважине УМ-1.1
1.5. Технологии интенсифицированного извлечения метанаДля интенсификации притока метана к дегазационным скважинам до 10–20 тыс м3/сут. нужны новые технологии воздействия на метаноугольные пласты.
Если шахтную дегазацию осуществляют в основном скважинами, пробуренными из шахтных выработок, то при заблаговременной дегазации добычные скважины бурят с поверхности земли. При этом в первом случае угленосный массив уже частично разгружен, а во втором – не разгружен. Статистика аварий свидетельствует о том, что опережающая шахтная дегазация не гарантирует безопасности труда шахтера. На наш взгляд, только интенсивная заблаговременная дегазация угольного пласта (за несколько лет до шахтной разработки) способна обезопасить дальнейшую его шахтную выемку. Тем более что, в соответствии с американскими данными, при заблаговременной дегазации степень извлечения метана из угольных пластов достигает 80–90 %.
Ниже представлены некоторые новые технологии интенсифицированного извлечения метана, которые используют в основном при заблаговременной дегазации угольного пласта.
Большая часть угольного метана (75–80 %) находится в сорбированном состоянии, и главная задача для его извлечения заключается в разрыве прочной и устойчивой физико-химической связи «уголь-метан», что возможно только при интенсивном разупрочнении угленосной толщи (прежде всего, угольного пласта) и его разгрузке. В связи с этим, на наш взгляд, много практически полезного по созданию в угольном пласте искусственных коллекторов (микро- и макроразмеров) как необходимых конструктивных элементов подземных газогенераторов накоплено в подземной газификации угля. И задача метаноугольной подотрасли – максимально использовать этот накопленный инженерный потенциал.
1.5.1. Гидравлический разрыв угольного пласта
Первые эксперименты по разупрочнению (разрыву) угольного пласта были проведены в 1954 г. на Лисичанской станции «Подземгаз», на пласте L6, на глубине 150 м [33].
Естественная газопроницаемость угольного пласта на этой глубине составляла всего1,5 мД, и, в соответствии с теорией течения дутья в неизменяемой среде, для нагнетания в вертикальную скважину 150–200 нм3/ч воздуха потребовалось бы давление в сотни атмосфер. При давлении же 2,0–3,0 МПа приемистость скважины составляла лишь 10–20 нм3/ч, и поток дутья между соединяемыми вертикальными скважинами был настолько мал, что противоточное перемещение очага горения либо вообще было невозможно, либо затянулось бы на очень длительное время.
Однако в данном случае при давлении 4,2–4,5 МПа было зафиксировано резкое увеличение приема дутья скважиной, в соответствии с рис. 5. Под действием давления, немного превышающего давление вышележащих горных пород на глубине 150 м, происходит искусственное расширение естественных микротрещин и микропор. Это явление было названо «разрывом угольного пласта».
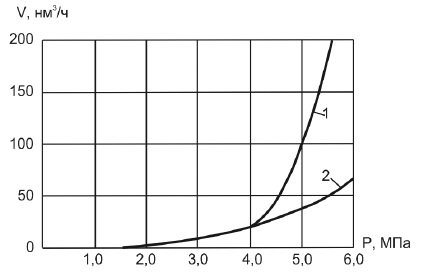
Рис. 5 – Зависимость приема дутья скважиной от давления: 1 – экспериментальная кривая; 2 – расчетная кривая
Начиная с 1956 г., при подземной газификации угольных пластов стали применять их разрыв с помощью жидкостей и закрепление созданных щелей кварцевым песком [34, 35].
Таким образом, Всесоюзный научно-исследовательский институт использования газа в народном хозяйстве (до 1966 г. – Всесоюзный научно-исследовательский институт подземной газификации угля) впервые в мировой практике в 1954 г. начал применять пневматический и гидравлический разрыв угольного пласта с целью его разупрочнения и существенного повышения газопроницаемости.
Первое опробование процесса гидроразрыва угольного пласта в Кузбассе было проведено в 1960 г., на Южно-Абинской станции «Подземгаз» (на чистой воде и без песка). На опытном газогенераторе № 4 было пробурено пять вертикальных скважин на пласт «VI Внутренний» и на глубину 240 м [10]. Одной из основных целей эксперимента было соединение всех пяти скважин в один канал.
Гидроразрыв угольного пласта на этой глубине, как правило, начинался при давлении 8,0–8,5 МПа. График зависимости расхода воды от давления ее нагнетания аналогичен кривым на рис. 5.
Для иллюстрации процесса гидроразрыва угольного пласта «VI Внутренний» на рис. 6 представлено изменение основных его параметров на одной из скважин.
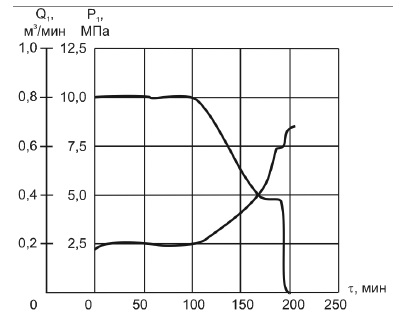
Рис. 6 – Изменение давления и расхода воды во времени при гидроразрыве угольного пласта «VI Внутренний»
Через 2 часа давление нагнетания воды стало падать, а расход – расти. Щель гидроразрыва достигла соседней открытой скважины, удалённой на 25 м от нагнетательной скважины. По прошествии 3 часов давление нагнетания упало практически до нуля, а темп закачки вырос с 200 до 700 л/мин
Механизм и развитие процесса гидравлического разрыва угольного пласта водой целесообразно рассмотреть на рис. 7.
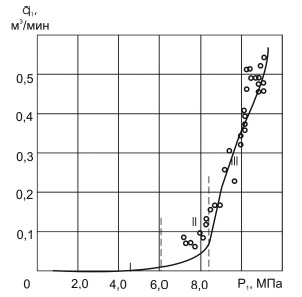
Рис. 7 – Зависимость расхода воды, нагнетаемой в угольный пласт, от давления
Здесь представлены параметры процесса нагнетания воды через одну из скважин в угольный пласт «VI Внутренний», имеющий на глубине 240 м мощность 1,8 м и газопроницаемость 4–5 мД. С увеличением количества воды, нагнетаемой в скважину, росло давление нагнетания. Однако характер этой зависимости был различным по участкам графика. Можно выделить три характерных участка.
На первом участке прием воды с ростом давления увеличивается по прямой. Это свидетельствует о том, что вода движется в угольном пласте (в этом интервале изменения давления нагнетания) по природным порам и трещинам без их структурного изменения.
На втором участке восходящая ветвь кривой поднимается все круче и круче по мере роста давления нагнетания. Это связано с началом изменения структуры природных пор и трещин, что вызывает более быстрый, чем на первом участке, рост приема воды скважиной при увеличении давления нагнетания.
В пределах третьего участка прием воды увеличивается пропорционально росту давления нагнетания. Однако угол наклона прямой здесь во много раз превосходит угол наклона прямой на первом участке графика. Это объясняется движением воды в угольном пласте теперь уже в основном по новым трещинам и щелям, гидравлическое сопротивление которых значительно меньше, чем в нетронутом угольном пласте неизменяемой структуры.
Прием воды начинался только при давлении 2,5 МПа, так как в момент испытаний над горизонтом нагнетания воды был статический столб подземных вод, равный 200–220 м.
Итак, при достижении критического давления наступает структурное изменение угольного пласта. Характерно, что величина этого критического давления, названного давлением разрыва угольного пласта, зависит от глубины его залегания, механической прочности и удельного веса покрывающей толщи пород:
Pp = 0,01 H • YП + Pдоп,
(2)
где Рр – давление разрыва угольного пласта, МПа;
Н – глубина залегания угольного пласта на горизонте нагнетания воды, м;
Υп – средний удельный вес пород покрывающей толщи, г/см3;
Рдоп – дополнительное давление, необходимое для преодоления сил сцепления между отдельными слоями угля, МПа.
Как правило, дополнительное давление, необходимое для разрыва угольного пласта, равно 1,0–2,0 МПа и связано с механической прочностью угля.
В рассматриваемом случае давление разрыва равнялось приблизительно 8,0 МПа (Рр = 0,01 240 • 2,5 + 2,0 = 8,0 МПа).
Аналогичные кривые характерны для всех случаев гидроразрыва угольного пласта.
Ясно, что если рабочая жидкость гидроразрыва будет более вязкой (масло, нефть, гель и др.), чем вода, то давления разрыва угольного пласта можно достичь при меньших темпах закачки. При добыче нефти, в тех случаях, когда глубина залегания пласта достигает нескольких километров, а давление разрыва – 30,0–50,0 МПа, рабочей жидкостью служит, как правило, нефть. В угольной промышленности применяют в основном воду.
Процесс образования щели при гидравлическом разрыве угольного пласта водой можно представить себе следующим образом. В угольный пласт через забой скважины нагнетают воду, при достижении критического давления разрыва нарушается естественная структура угольного пласта. Образующаяся первоначальная щель достигает либо забоя какой-нибудь скважины, либо выгазованного пространства подземного газогенератора. В этот момент давление нагнетания воды резко падает, а вода, движущаяся по первоначальной щели разрыва, размывает уголь и промывает себе проход большого сечения (рис. 6).
Размыву первоначальной щели способствуют относительно небольшая механическая прочность угля и специфическое строение угольного пласта. В угольном пласте, особенно каменноугольном, легко различаются отдельные слои, разделенные плоскостями напластования. В процессе прокачки воды по щели разрыва уголь вымывается отдельными слоями и кусочками. Давление нагнетания постепенно снижается, а сечение щели увеличивается. При достижении минимального давления нагнетания, как правило, не превышающего 0,1–0,15 МПа, промывку щели разрыва прекращают.
1.5.2. Пневмогидравлическое разупрочнение. Межскважинная кавитация
На опытном газогенераторе № 4 на Южно-Абинской станции «Подземгаз» [36], применяя различные гидродинамические методы, удалось соединить все 5 скважин в одну щель (87 м). Пропускная способность этой щели была высокой (4800 м3/ч воздуха при давлении нагнетания 0,3 МПа), хотя естественная газопроницаемость угольного пласта на этой глубине составляла всего 4–5 мД.
Путем попеременного (по величине давления от 0,2 до 6 МПа) пневмогидравлического циклического воздействия на щель гидроразрыва «вода-воздух» на поверхность было выброшено через скважины диаметром 150 мм 10–12 т угля [37, 38]. Среднее сечение созданного искусственного коллектора, определенное по массе вынесенного на поверхность угля и по гидравлическому сопротивлению этого канала, соответствовало диаметру 0,35–0,4 м.
Так, еще в 1961–1962 гг. был разработан инженерный способ создания в нетронутом угольном пласте искусственных коллекторов большого сечения. Естественно, это сечение было не одинаково по длине канала, так как переменные динамические нагрузки (удары) приводили к механическим разрушениям стенок коллектора, неравнозначным по его длине.
Один из основных недостатков процесса гидроразрыва угольного пласта жидкостью – отсутствие его направленности. Как правило, процесс гидроразрыва осуществляют на участке угольного пласта, который характеризуется какими-нибудь нарушениями: выработанное пространство, свободные угольные каналы, кливажи и другие зоны угольного пласта повышенной проницаемости.
Поэтому особое значение исследований, проведенных на пласте «VI Внутренний», состояло в создании единой щели гидроразрыва протяженностью 87 м.
В качестве методов воздействия на направленность процесса гидроразрыва были испытаны: одновременное нагнетание воды в две соседних скважины и разгрузка третьей скважины, на которую необходимо было осуществить гидроразрыв угольного пласта, от статического столба подземных вод [39].
Первый метод, который заключался в одновременном нагнетании воды в две соседних скважины, обеспечивал направленное течение процесса гидроразрыва одной из нагнетательных скважин, ближайшей к участку угольного пласта, с которым необходимо было соединиться.
Второй метод воздействия на направленность процесса гидроразрыва заключался в проведении гидроразрыва на скважину, разгруженную от статического столба подземных вод на участке гидроразрыва, путем продувки уже полученной щели гидроразрыва воздушным дутьем и отводом его из этой скважины. В этом случае в определенной зоне угольного пласта давление искусственно снижалось почти до атмосферного, в то время как на угольный пласт в целом действовало давление величиной в гидростатический столб подземных вод (при проведении исследований на пласте «VI Внутренний» он равнялся 220 м).
Оба этих метода нашли широкое применение при гидравлическом разрыве угольного пласта на промышленных газогенераторах. Если на пласте «VI Внутренний» процесс гидроразрыва осуществлялся при условии отсутствия на участке испытаний наклонных газоотводящих скважин, перебуренных до их горизонта, то в дальнейшем были проведены специальные испытания возможности создания единой щели гидроразрыва при наличии наклонных газоотводящих скважин, перебуренных до горизонта создаваемого первоначального канала газификации.
Эти исследования показали, что на угольных пластах средней мощности наклонные скважины, перебуренные до горизонта розжига, не дают возможности создать единый канал методом гидроразрыва угольного пласта. Как правило, процесс гидроразрыва протекал на свободные каналы наклонных газоотводящих скважин.
Таким образом, в отличие от широко пропагандируемого на Западе метода кавитации (образование каверн) на забое вертикальной скважины (вскрытый горизонт угольного пласта), в описанном эксперименте на опытном газогенераторе № 4 имело место разупрочнение угольного пласта между скважинами. В соответствии с представленными выше результатами эксперимента, искусственно созданный коллектор (87 м) следует рассматривать как результат межскважинной кавитации.
Созданные с помощью межскважинной кавитации искусственные коллекторы обладают высокой дренирующей способностью и могут эффективно использоваться для интенсифицированной дегазации угольных пластов.
1.5.3. Технологические рекомендации. Варианты схем межскважинной кавитации
Ниже в качестве примера рассмотрен один из вариантов реализации предлагаемой технологии разупрочнения угольного пласта, который можно осуществить через серию вертикальных скважин.
Современная трактовка этой технологии применительно к проблеме извлечения угольного метана включает несколько этапов.
1. Изотермическое воздействие на угольный пласт с помощью воды и воздуха.
Главное отличие этой технологии от тех, которые уже применяют в настоящее время (для извлечения угольного метана), заключается в осуществлении процесса гидроразрыва на воде и без закрепления щели песком. Путем попеременного по давлению пневмогидравлического воздействия («вода-воздух») на щель гидроразрыва удается получить в угольном пласте необратимые деформации с выносом угольной мелочи как через скважины, так и проталкивания ее в площадные щели гидроразрыва вглубь (от нагнетательной скважины) угольного пласта. Созданные щели и каналы имеют протяженные свободные боковые поверхности и поэтому высокую дренирующую способность. Они являются эффективными коллекторами для притока к ним угольного метана в частично разгруженном угольном массиве.
После создания искусственных коллекторов в угольном пласте наступает стадия осушения газоугольного массива, которая завершается образованием депрессионной воронки в районе скважин с опущенными в них погружными насосами.
По мере снижения дебита извлекаемой воды нарастает дебит угольного метана – начинается этап его интенсифицированного извлечения.
2. Термическое воздействие на угольный массив.
Основное содержание второго этапа заключается в розжиге угольного пласта в одной или нескольких скважинах и нагнетании в них воздуха от передвижных компрессоров высокого давления.
Образовавшиеся горячие продукты горения угля проникают в искусственные коллекторы, созданные на первом этапе предлагаемой технологии, а через их боковые поверхности – и в угольный массив в целом, содействуя десорбции метана.
Прогрев угленосного массива горячими продуктами содействует также существенному (кратному) увеличению коэффициента его газопроницаемости, а следовательно, прямопропорциональному возрастанию дальнейшего притока к нему угольного метана.
Снизившийся дебит метана после первого (холодного) этапа технологии вновь возрастает, и начинается второй этап технологии интенсифицированного извлечения угольного метана.
3. Материальное обеспечение предлагаемой технологии.
1.1. Количество экспериментальных вертикальных скважин должно быть не менее двух, расстояние между ними – 80–100 м.
На рис. 8 представлены три варианта. Первый (а) – две скважины, второй (б) – четыре скважины, третий (в) – семь скважин.
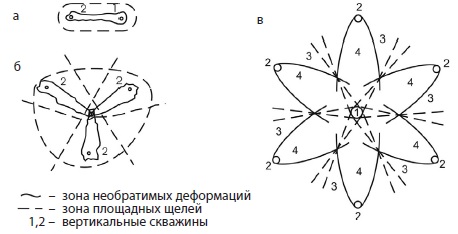
Рис. 8 – Схемы реализации новой технологии извлечения угольного метана (путем межскважинной кавитации): а – двухскважинная; б – четырехскважинная; в – семискважинная
Детальный технологический регламент является самостоятельной задачей и подробно описан в патентах на изобретения ОАО «Промгаз» [37–39].
1.2. Количество водяных насосов для осуществления процесса гидроразрыва угольного пласта обусловлено количеством экспериментальных скважин.
В варианте (а) должно быть 2 насоса с темпом закачки 1,5–2,0 м3/мин, в варианте (б) желательно иметь 4–5 насосов с темпом закачки 4–5 м3/мин, в варианте (в) – 8–10 насосов с темпом закачки до 10 м3/мин
Гидравлический напор водяных насосов обусловлен глубиной скважин. Например, при глубине 1000 м давление нагнетания воды должно быть 32,0–35,0 МПа.
1.3. Передвижной воздушный компрессор должен работать при давлении 12,0–13,0 МПа (при глубине скважины 1000 м) и расходе воздуха 600–1000 м3/ч.
В вариантах (б) и (в) желательно иметь два воздушных компрессора.
1.4. Погружные насосы для откачки воды (по количеству скважин).
Новая технология интенсифицированного извлечения метана из угленосных массивов может быть реализована различными способами. Рассмотренные выше варианты (рис. 8) – далеко не единственные [40, 41].
Рассмотрим на примере семискважинной схемы технологический регламент пневмогидродинамического разупрочнения угольного пласта.
На рис. 8 (в) представлена принципиальная схема участка угольного пласта с пробуренными семью скважинами. Количество скважин на периферии может быть снижено до трех, соответственно, с меньшей зоной разупрочнения (рис. 8 (б)).
Предлагаемый способ разупрочнения угольного пласта реализуют следующим образом.
На угольный пласт бурят несколько скважин: одну центральную 1 и несколько периферийных, удаленных от центральной скважины на одинаковое расстояние. На рис. 8 (в) в качестве примера представлены шесть периферийных скважин 2.
В начале технологической последовательности осуществляют гидравлический разрыв угольного пласта через центральную скважину 1, периферийные скважины 2 закрыты. На периферийных скважинах непрерывно измеряют статическое давление. После его стабилизации, в течение некоторого времени начинают нагнетать воздух высокого давления. Многократное повторение цикла «вода-воздух» содействует расширению естественных микротрещин и их соединению в единую систему. В результате происходит откалывание слоев угля, расширение щели гидроразрыва и вынос угольной мелочи за пределы зоны воздействия. Давление нагнетания воды и воздуха в скважину 1 постоянно снижается, что свидетельствует о заметном снижении сопротивления созданного искусственного коллектора. На рис. 8 (в) эти зоны показаны пунктиром.