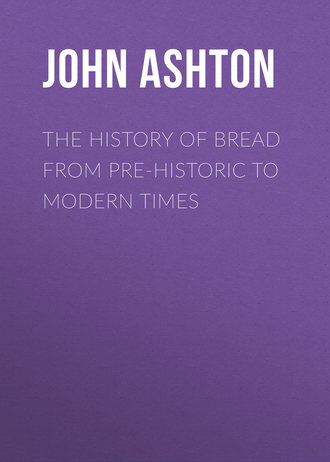
Полная версия
The History of Bread From Pre-historic to Modern Times
‘On reaching the ground floor again, our now clean wheat is first passed through the “grading” or “sizing” reels, which separate it into two sizes, and then it enters the mill proper. It should be said here that the milling industry of the world has been revolutionised within the past few years by the substitution of steel rollers for the old millstones. The process of crushing or grinding, however, by steel rollers is accomplished in a very gradual manner, as will be explained: First come the “break rolls.” These are solid steel rollers set in pairs, with corrugated surfaces; this gives them a cutting action. Wheat is passed through five successive pairs of these rollers. The first are about 1/16th inch apart, and only break or bruise the grain slightly. Each successive pair is set closer, and carries the bruising a step further. But this is only half the business. After each set of rollers the grain goes through a “purifier,” which is either a sieve of some kind or an aspirator, or both together, and the object is always the same – namely, to separate the solid particles of the broken wheat from the lighter ones. The former are, or rather will eventually be, flour; the latter constitute “offal.” And the whole art of milling is merely an extension of this process; first reduction, then separation, repeated over and over again. As the grain passes through each successive set of rollers it is broken up finer and ever finer, and the separating action of the “purifier” accompanies it step by step. The solid particles grow smaller and smaller, the “offal” correspondingly finer and finer. This is the process in brief, but there are endless complications and refinements on the way. For instance, the solid particles are not only separated but are themselves divided into groups according to size. Then the offal often undergoes a further purifying process. Then the purifiers differ – some are complex, others simple; some of wire, others of silk; some revolve, others oscillate; some are “aspirated,” others not; and so forth. Meanwhile, at the end of the five rolls and five purifiers, which make up our breaking department, we have got three products: (a) semolina; (b) middlings; (c) offal. The first two are practically varieties of the same —i. e., both solid particles, which will afterwards be flour, but of different sizes. They are half way between grain and flour – hence the term “middlings.”
‘Grinding is only a continuation of the above process, but the rollers are different; their surfaces are smooth, and they are set closer together. The purifiers, too, are, for the most part, more elaborate. A look at one of them will show the extreme ingenuity expended on these operations. It consists primarily of an oscillating sieve made of silk, through the meshes of which the particles of flour fall into a wooden bin. On the floor of the bin is a “worm” which continually works the flour along to one end; on the under surface of the sieve is a travelling brush which brushes off the adhering flour and prevents the meshes from getting clogged. Above the sieve is an apparatus which, with the aid of currents blown by an aspirator, catches the volatile offal; and above that again a travelling blanket which arrests the still more volatile particles. Finally, the blanket, as it reaches the end, is tapped automatically to knock out what has stuck to it. By the time a handful of grain has been converted into a handful of fine flour it has gone through some 50 different machines, including 18 sets of rollers and 18 purifiers.
‘The following points may be of interest: A first-class London mill working 100 sets of rollers can turn out 45 sacks of flour per hour. Offal, according to its fineness or coarseness, forms bran, pollard, etc., and is worth from 5l. to 6l. a ton. The qualities of flour are whiteness and strength. The former is tested by the eye, the latter only really by baking capacity. There seems to be a general consensus of opinion in favour of flour made from Hungarian wheat. The best English is of sweeter flavour, but lacks “strength.” It has been reckoned that 300 sacks are made per hour in London mills, all of which is consumed in London. The flour mill industry owes nothing to American inventive genius; on the contrary, that country is behind the times. The steel rollers came originally from Hungary – always a great milling country.’
CHAPTER IX
THE MILLER AND HIS TOLLS
In old times corn mills were always important factors in manors, and a source of considerable profit to the lord of the same. All the tenants of the manor were bound by custom to have their corn ground at the manor mill, paying a toll to the lord, for the mill was part of his demesne. The tenants owed suit to the mill in the same manner as they owed suit and service at the Manor Court. This, however, did not apply to the grinding or bruising of malt, and there were probably two good reasons for it – one, that the tenants could perform the operation on their own premises; and the second, that if it were done at the mill it would be likely to spoil the flour next ground.
Very many instances of these mills may be given, but one will suffice, more especially as in this case it was carried down to modern times. There was at Wakefield, Yorkshire, a corn mill which was a franchise of the Pilkington family, of Chevel Park, by charters from one of the Edwards. The monopoly of grinding the corn at this mill was a great sore to the inhabitants, and the cause of much litigation, but the holders of the rights always came off the victors. They claimed the right of grinding not only for the town of Wakefield, but for some miles round, including the villages of Horbury, Ossett, Newmillardam, and others; so that all the corn used in this district was obliged to be ground at the ‘Soke Mill,’ or, as it was otherwise called, the ‘King’s Mill,’ and neither meal nor flour could be sold unless it were ground there. The tenant of the mill demanded a ‘mulcture’ of one-sixteenth – that is, out of 16 sacks of corn he kept one for himself for grinding the other 15.
Some time about 1850 the inhabitants of Wakefield and the adjacent villages determined to purchase the rights, and this was done by a rate spread over a series of years, and called the ‘Soke Rate.’ The purchase money amounted to about £20,000. The same kind of property existed at Leeds and at Bradford; but from neglect on the part of the owners, and lapse of time, the inhabitants turned restive and independent, and ‘broke the Soke,’ without compensating the Lords of the Manors. These mills are still called the King’s Mills.
Nor was this custom confined to England. In Scotland, in feudal times, it was common for the tenants of a barony to be bound to have their corn ground at the barony mill. Centuries ago the erection of a substantial building, with the millstones, driving machinery, and other plant necessary for a mill, together with the drying-kilns, mill-dams, lades, weirs, and watercourses requisite for a corn mill involved the expenditure of a considerable sum of money, such as only the baron could find. He, therefore, assured himself of a return for his capital invested by binding his tenants to use his mill. Of course, he got a good rent for his mill, which was the manner in which the benefit arising from the bondage of his tenants found its way into his coffers.
Sir James A. Picton, in his City of Liverpool selections from the municipal archives and records, states that in 1558 the Corporation of the Borough ordered that ‘every miller, on warning, shall bring his toll-dish to Mr. Mayor, to a lawful size thereof sealed, under a penalty of 6d.’ That this toll-taking on the part of millers was occasionally perverted there can be but little doubt, and it was sometimes very severely commented on, as we may see in this passage from a tragedy by Wm. Sampson (1636), called The Vow-Breaker; or, the Fair Maid of Clifton. ‘Fellow Bateman, farewell; commend me to my old windmill at Rudington. Oh! the mooter dish – [Multure or Toll-dish] – the miller’s thumbe, and the maide behind the hopper!’
In the Roxburghe ballads (vol. iii., 681) we have The Miller’s Advice to his Three Sons in Taking of Toll:
‘There was a miller who had three sons,And knowing his life was almost run,He called them all, and asked their will,If that to them he left his mill.He called first for his eldest son,Saying, “My life is almost run,If I to you this mill do make,What toll do you intend to take?”“Father,” said he, “my name is Jack.Out of a bushel I’ll take a peck,From every bushel that I grind,That I may a good living find.”“Thou art a fool,” the old man said.“Thou hast not well learned thy trade.This mill to thee I ne’er will give,For by such toll no man can live.”He called for his middlemost son,Saying, “My life is almost run.If I to thee the mill do make,What toll do you intend to take?”“Father,” says he, “my name is Ralph.Out of a bushel I’ll take it half,From every bushel that I grind,So that I may a good living find.”“Thou art a fool,” the old man said;“Thou hast not learned well thy trade.This mill to you I ne’er can give,For by such toll no man can live.”He called for his youngest son,Saying, “My life is almost run.If I to you this mill do make,What toll do you intend to take?”“Father,” said he, “I am your only boy,For taking toll is all my joy.Before I will a good living lack,I’ll take it all, and forswear the sack.”“Thou art my boy,” the old man said,“For thou has well learned thy trade.This mill to thee I’ll give,” he cried,And then he clos’d his eyes, and died.’To show the popular idea of a miller’s integrity, I may mention that the children in Somersetshire, when they have caught a certain kind of large white moth, which they call a Miller, chant over it this refrain:
‘Millery! millery! Dousty Poll!How many sacks of corn hast thou stole?’and then they put the poor insect to death on account of its imaginary misdeeds.
Even Chaucer must have his gird at the miller:
‘The millere was a stout carl for the nones,Ful byg he was of brawn and eek of bones;That proved wel, for over al ther he camAt wrastlygne he wolde have alwey the ram8.He was short sholdred, brood, a thikke knarre9,There was no dore that he ne wolde heve of harre10.Or breke it at a reunying with his headHis berd, or any sowe or fox was reed,And ther to brood, as though it were a spadeUpon the cope right of his nose he hadeA werte, and ther on stood a toft of herys,Reed as the brustles of a sowes crys;His nose thirles11 blake were and wyde;A swerd and a bokeler bar he by his syde;His mouth as greet was as a greet forneys,He was a janglere and a goliardeys12,And that was moost of synne and harlotries,Wel konde he stelen corne and totten thries13,And yet he hadde ‘a thombe of gold’ pardeeA whit cote and a blew hood wered he,A bagge pipe wel konde he blowe and sowne,And ther with al he broghte us out of towne.’The ‘thombe of gold’ has somewhat puzzled commentators on Chaucer. One thing is certain: that a miller has been traditionally credited with a broad thumb, and the little fish the Bullhead is called The Millers’ Thumb, from a fancied resemblance. Every one connected with the navy knows what the ‘purser’s thumb’ is, from the legend that, when serving out their tots of rum to the men, his thumb was invariably inside the measure (doubtless necessitated by the rolling of the old men-of-war), which resulted in a large profit to himself during a long cruise, and this seems to illustrate Chaucer’s meaning, especially as it occurs immediately after the miller’s ill-gotten gains, that by putting his broad thumb into every measure he made thereby gold during the year.
But there is another and a kindlier explanation of the term, which rests on the authority of Constable, the painter, according to Yarrell, in his History of British Fishes, when writing of the Bullhead. ‘The head of the fish is smooth, broad, and rounded, and is said to resemble exactly the form of a miller’s thumb, as produced by a peculiar and constant action of the muscles in the exercise of a particular and most important part of his occupation. It is well known that all the science and tact of a miller are directed so to regulate the machinery of his mill that the meal produced shall be of the most valuable description that the operation of grinding will permit, when performed under the most advantageous circumstances. His profit or his loss, even his fortune or his ruin, depend upon the exact adjustment of all the various parts of the machinery in operation. The miller’s ear is constantly directed to the note made by the running-stone in its circular course over the bed-stone, the exact parallelism of their two surfaces, indicated by a particular sound, being a matter of the first consequence; and his hand is as constantly placed under the meal spout to ascertain, by actual contact, the character and qualities of the meal produced. The thumb, by a particular movement, spreads the sample over the fingers; the thumb is the gauge of the value of the produce, and hence have arisen the saying of worth a miller’s thumb, and an honest miller hath a golden thumb, in reference to the amount of profit that is the reward of his skill.’
Any notice of flour would, of course, be valueless without an analysis of its constituent parts, which, as anyone can understand, will vary in different wheats; there can be no standard, because of the difference of the soils on which it grows, a fact which is fully borne out by the following tables by famous analysts. Jago (The Chemistry of Wheat, Flour, and Bread, &c. Brighton, 1886), quoting Bell, says: —
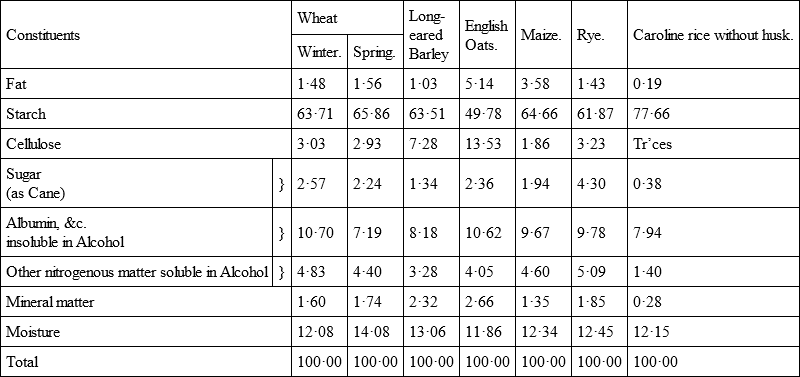
Professor Graham, in a lecture delivered at the International Health Exhibition, London, July 3, 1884, quoting Lawes and Gilbert, says: —
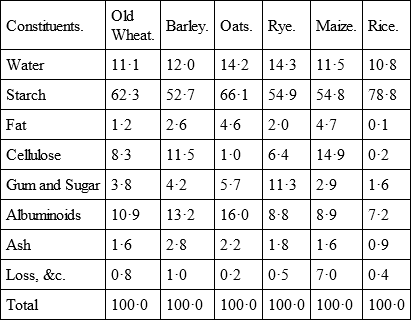
Messrs. Wanklyn and Cooper (Bread Analysis, &c., London, 1881) say that, according to their analysis, this wheaten flour, which is the flour commonly to be bought in this country, has the following composition: —
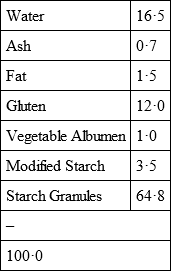
A comparison of these tables by well-known analysts shows us, if we only take the single article of wheat, how the grain varies. Let me now say something about the constituents of wheat in as simple a form as possible.
The fat is of a yellow colour, and, as far as is known, is not a particularly valuable component part; but as all fats are foods, of course, it is of service.
The starch in wheat is the ordinary starch (of the best kind) of commerce; and, seeing that it forms the greater part of all breadstuffs, it naturally is an important element in them. In good, sound wheat the starch granules are whole; in sprouted wheat, or that heated by damp, they are rotted, and, consequently, the starch they contain is changed, more or less, into dextrin and sugar, and, consequently, a difference is made in the food value of the wheat.
Dextrin and sugar are small components of good wheat. The dextrin, no doubt, has a beneficial effect in small quantities, but not in large. Sugar, such as is found in wheat, affords the necessary amount of saccharine matter for fermentation.
Cellulose is more useful to the plant than to the miller, to whom it is as so much bran.
There are two kinds of albuminoids, or gluten, present in wheat – one insoluble, the other soluble in alcohol. The former makes what is called a ‘strong bread,’ and the latter acts, in bread-making, on the former, and, under the influence of yeast, it attacks the starch, converting it into dextrin and maltose.
The ash of wheat contains principally phosphoric acid and potassium; magnesium ranks next; then lime, silica, phosphate of iron, soda, chlorine, and sulphuric and carbonic acids.
CHAPTER X
BREAD MAKING AND BAKING
The ordinary method of bread-making in London is as follows: The first process, when the bread is made with thick yeast, being to prepare a mixture of potatoes, yeast, and flour, by which the process of fermentation is to be produced in the dough.
Mr. George W. Austin, in his pamphlet on Bread, Baking, and Bakers,’ says about the ferment: ‘For each sack of flour (280 lbs.) about 8 lbs. or 10 lbs. of dry, mealy potatoes are taken, well boiled and mashed and washed through a strainer to take away the skin; to this is added 12 or 14 quarts of water, at a temperature varying from 80 deg. to 90 deg., and a quart of thick brewers’ yeast, or 1 lb. of compressed yeast – which is equal. Having well dissolved the yeast, and added 2 lbs. of flour, the mass is allowed to stand some three or four hours, until the head falls in through the escape of gas.’ The next process is the preparation of the sponge. The trough and flour being ready, the ferment is taken, and, with the addition of 28 quarts of clear water, at a temperature of 80 deg. to 90 deg., is passed into the trough through a sieve or strainer, and the mass, being kept well together, is made up into a nice dry sponge. It is allowed to remain thus and ferment for another five or six hours, when it will have risen and formed a head, which is allowed to break. As soon as this head is broken it commences to rise again, and as soon as it has broken the second time the remainder of the flour is added, and the dough made as follows:
Two and a half pounds of salt dissolved in 28 quarts of clear water, at a temperature of 80 deg., and mixed well into what is termed ‘the sponge,’ with the remainder of the flour, the whole being broken up and well and thoroughly mixed and kneaded until the dough is uniform in material and consistency. It is then left to rise for another hour or more, when the dough is weighed out in pieces of the requisite size and speedily manipulated into the required shape. As the loaves are moulded they are placed on trays, covered with a light cloth (to prevent the dry and colder air forming a dry crust on the surface), and left to dry sufficiently before being placed in the oven. Before this is done the loaves are slightly brushed over with a small quantity of milk and water to improve the appearance of the outside of the loaf when it comes from the oven.
The oven is, for the purpose of baking bread, brought up to a heat of 400 deg. Fahr., and the bread, although seemingly baked by dry heat, is in reality boiled in the steam of the water which the bread contains.14
Salt is added to make the bread more palatable; but it has also another effect. With inferior flour dextrin is formed inside the loaf to some extent as well as on the outside, consequently bread made from inferior flour rises badly and is darker in colour. This inferior flour is made sometimes from wheat that has been damp, the dampness causing the soluble albumenoids which the grain contains to act on the insoluble gluten, decomposing it into soluble bodies, and producing dextrin by their action on the starch in the grain. The further decomposition of these albumenoids is checked by the action of the salt during the fermentation of the bread.
And now it will be well to say something about the leaven of bread. We have already seen the modern method of making a ferment with flour, potatoes, and brewer’s yeast; but there are other substances which do not cause fermentation, and yet lighten the bread, such as the different baking powders, and the American sal eratus, a mixture of bi-carbonate of soda and salt. Carbonate of ammonia, which entirely evaporates in baking, is used in confectionery to raise the paste by the bubbles it forms in its volatilisation. The unfermented breads, such as those made by the late Dr. Dauglish’s patent (of which more anon), are rendered light upon the same principle, the usual method being to mix soda with the flour, and hydrochloric acid with the water, in the proportions in which they unite to form chloride of sodium, or common salt. The effervescence, like that produced in mixing seidlitz powders, converts the paste into a porous sponge, which, however, requires to be very quickly placed in the oven. The salt formed by the mixture replaces that ordinarily added to the dough in making bread; but this method is seldom used by practical bakers. Whatever, therefore, be the method by which bread is made light, the object to be attained is to pervade the dough with numerous cavities, which keep the particles of flour asunder, instead of forming a compact and unyielding mass.
The science which gave an insight into the cause of the ‘rising’ of bread, and suggested substitutes for the ordinary fermenting materials, is but of recent date. These ferments operate by generating an infinity of gas bubbles, which honeycomb the dough. The earliest process was to employ leaven, which is still largely used in the manufacture of the black rye bread of the Continent, and consists of dough which has become more or less sour by over-fermentation. This is kept from one baking to another, to inoculate a fresh bulk of paste with its fermenting influence. No sooner does it come into contact with the fresh dough than it communicates its own properties, as by contagion. Probably the discovery of leavening has, in many countries, been owing to accident, through neglected paste having been attacked by the fungus which is the cause of fermentation.
Many of my readers probably do not know that yeast is a plant. It belongs to the class of fungi, and, in accordance with the general habit of its kind, it differs from the green forms of vegetable life by feeding upon organic substances. The yeast plant represents one condition of a species of fungus remarkable for the diversity of forms it exhibits, its wide, nay, universal distribution, and the magnitude of the effects, sometimes beneficial, sometimes mischievous, which it is capable of producing. The forms in which it is familiar to most persons, although its nature may be unsuspected, are yeast, the gelatinous vinegar plant, the ‘mother’ of vinegar, and many decomposing vegetable infusions, and the common blue or green mould (penicillium glaucum) which occurs everywhere on sour paste, decaying fruits, and, in general, on all dead organic matters exposed to combined moisture and moderate heat.
Yeast and the vinegar plant are the forms in which it vegetates under various circumstances when well supplied with food. Mildew is its fruit, formed on the surfaces exposed to air at certain epochs, like the flowers and seeds of the higher plants, to enable it to diffuse itself, which it does most effectually, for the microscopic germs, invisible singly to the naked eye, are produced in myriads, and are so diminutive that ordinary motes floating in the atmosphere are large in comparison.
Yeast, when examined under the microscope, is found to consist of globular vesicles about 1/2300th part of an inch in diameter when fully grown. They are multiplied by little vesicles budding out from the sides of the parent. These soon acquire an equal size, and repeat the reproduction, either while attracted to the parent globule or after separating from it. The multiplication goes on to an indefinite extent with a fitting supply of food and at a moderately warm temperature (70 deg. -90 deg. Fahr.). The vesicles are nourished by sucking in a portion of the organic liquid in which they exist, decomposing this chemically, and either actually giving off, or causing the separation of their outer surface, of carbonic acid in the form of gas. To give a familiar illustration of the action of the carbonic acid which is evolved from yeast on the dough, I may say that it is analogous to the froth formed on a tumbler of bottled ale or ginger-beer. The cavities or bubbles in the dough are produced in an exactly similar manner; but two circumstances occur in bread to render them permanent – first, the fact that they are slowly formed; secondly, that they are generated in a substance which, while it is soft enough to allow the bubbles to expand, is tough enough to retain them.
There are several kinds of yeast besides barm, or brewer’s yeast, which, in spite of its bitter taste, is generally used by bakers because it is the least expensive. Next in consumption is what is termed press yeast, in German press hefe or pfund hefe, commonly known in commerce as German yeast, so called because it originally was a monopoly of that country, but it is now largely manufactured in Scotland. Of these yeasts Mr. Austin says: