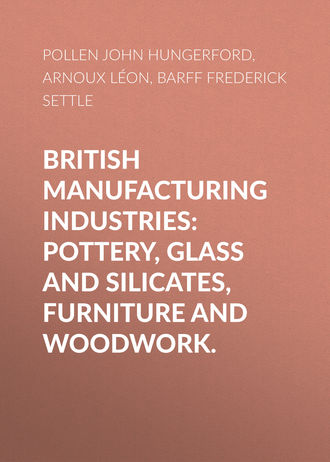
Полная версия
British Manufacturing Industries: Pottery, Glass and Silicates, Furniture and Woodwork.
We may consider furniture under two broad divisions, that which is made to be handled and moved about, and that which is for use but not meant to be handled or moved. We may add a third division in the actual fixtures of the house, made by the joiner and meant to be ornamental fittings or completions to the builder's and carpenter's work.
Under the first head will be included light tables, chairs, couches, and other movable objects; under the second, cabinets, book-shelves, frames, mirrors, and so on; under the third head come flooring, panelling, window shutters, door-frames, stair-rails, &c.
1. Chairs, Tables, etcThe essential points in a well-made chair are comfort, lightness, and strength. Of course, as men and women are pretty much of the same proportion all over the world, chairs, of which the seat is about the height of the lower process of the human knee-joints, must be of the same height, or but slightly varied, in every country. From the habit that so many persons have of throwing their whole weight back and, as we are told, in some countries, of balancing their persons on the back legs of their chairs and inclining their legs in the direction of the chimneypiece, there is often an immense strain on the back joints of chairs. Whether we lean back or swing on them, the junction of the seats of chairs with the backs is always subject to severe trials; and on no article of furniture in common use is such good joinery required. It is worth while to look at the old wall paintings of the Egyptians, as they are given in Rossellini and the great French book of the 'Description de l'Egypte,' to see what capital workmanship those most ancient carpenters bestowed on their chairs. Those of the best and oldest periods are without connecting bars to the legs before or behind, all the strength of the construction being centred in the excellence of the joints of the seat with the back and legs; and in modern workshops, the highest skill is applied to ensure strength in these points of junction. If the wood is thoroughly dry, the mortises and tenons fitting perfectly, and the glue good, the different parts are so wedded together that the whole structure becomes one piece, as if nature had made a vegetable growth in that fashion, all the fibres of which have continuous and perfect contact with each other. If, however, there is a deficiency in any of these conditions, these joints fail. If the wood shrinks, or the tenons do not fit the mortises all through, or the glue is deficient, these various portions speedily come to pieces. Sofas, couches, and stuffed chairs are so much more massive in construction that there need be no risk of such a kind of disintegration.
The members of which a chair is made up may be either turned in the lathe, or left massive enough to allow of carving on the legs, backs, or round the framework of the seat. Turned work can be lightly inlaid with ivory, as that of ancient Egypt, painted, gilt, or mounted (lightly also) with metal.
The subjects of the carving may be either figures of men, horses, lions, or the heads and legs of such animals, acanthus leaves, and arabesques. Many of these ornaments have been used from ancient times, and revived at various historical periods. For modern rooms the lightest construction is most in place, and therefore carving should be compact in composition and delicate in execution, without prominences or undercutting that would interfere with comfort or be liable to breakage.
A certain architectural character is given to chairs by cutting flutings down the legs, or by borrowing other slight details from architecture. The upholstery of chairs will always be their most noticeable decoration, and this applies still more to lounging chairs and couches of all shapes and sizes, as the framework of them is so much less observable in proportion to their upholstered surfaces.
Tables, lampstands, &c., being generally, though not always, meant to be moved about, require as light a construction as is consistent with strength. The surface of all but small tables is beyond the dimensions of a single plank of wood. The outer and inner portions of a log or plank are of different fineness of grain, contain varying proportions of sap, and shrink in different degrees. Single planks of wood, therefore, can only be exceptionally used for table tops. Generally, they are made up of portions of planks selected with great care, grooved on the edges, with a tongue or slice of wood cut the cross way of the grain, uniting the planks about the middle of their thickness; the edges are then firmly glued together. If the surface is to be of wood which can be procured in large pieces of straight or continuous grain, such as mahogany, the wood is solid throughout; if of some rare wood or rare figured graining, such as the roots or wens of oak, this ornamental surface is laid on in thin slices with glue and heavy pressure. This is known as veneering. The surface is sometimes inlaid with ivory, metal, mother-of-pearl, slices of agate and other substances, as in the Boulle or marquetry work already alluded to.
The frame of the table is either a deep rail not far within the edge, or a thick pillar or leg or several legs collected, mortised into a broad expanding foot and supporting a spreading framework above, to which the top itself can be fastened, and stretching far enough all round in the direction of the edges to give a firm support.
The decoration of the top can only be superficial if the table is for use, and any decoration by carving, piercing, and so on, must be confined to the framework and the supports. These parts can be, and have been at all times decorated as the framework of chairs, and by very much the same kinds of ornament.
To tables of more modern periods, little galleries of pierced work or of tiny balustrades are sometimes added. They belong to the age of porcelain collectors, hoops, broad coat-skirts, and tea-parties, and are intended to save delicate wares from being swept to the ground. Side tables, and such as are made to support heavy objects, can be treated with more massive frame work and supports, and the carving and decorations will be bolder and larger accordingly.
2. Cabinets, etcI will proceed to the second division of furniture, cabinets, bookcases, and other standing objects, which are more or less immovable. But shelves and china trays must be placed in secure parts of the room, if they are not actually fastened to the wall. The former must be strong to support the great weights laid upon them, and the supports or framework, which is all that would be seen, may be carved or decorated with surface or applied metal ornament. On a large scale, fittings of this kind belong rather to architectural woodwork. China holders, whether placed on the ground or fixed against a wall, are properly treated with shelves quaintly shaped on plain and light, pierced galleries or gilt decorations corresponding with the apparent lightness of pieces of porcelain. The wood and lac work cabinets of the Chinese; and the complicated, but not ungraceful, gilt mirror frames and flourishing acanthus work of the Italians, French, and Germans, of the last century, seem specially suited for showing off this gay and fragile material. The collector proper will probably place his treasures under glass, and with little regard to the framework of his cases. Here china and china stands are treated only as decorations.
As to cabinets, they are the most precious, if not the most useful of all pieces of furniture. They have generally been intended to hold family treasures, are not required to be moved, and have therefore been the richest and most decorated objects in the room. Cabinets are the legitimate descendants of the chests of former days containing bridal outfits and trinkets, or plate, jewellery, and other valuables. They were carried from town to country, from grange to castle. About the beginning of the sixteenth century, the personal habits of great men became less nomad, and their chests were no longer liable to be packed and moved away. These receptacles were mounted on stands at which height the lids could not be lifted, and doors were substituted. Drawers took the place of shelves or compartments, and every sort of ingenuity was applied to make these pieces of furniture quaint and splendid inside and out.
As to shape, it is contrary to their purpose of convenience and interior capacity, to make cabinets, cupboards, or other receptacles, with showy and spreading architectural details, such as cornices, architraves, columns, pediments, and the like. All these parts, which are laborious and costly in construction, are so many additions to its size, and make no more room inside to compensate for this expenditure. Cabinets should, in propriety, be as big and convenient inside as their size would lead us to expect.
On the other hand, the many fine examples made in the sixteenth and seventeenth centuries in this country, Holland, Germany, France or elsewhere, have been generally intended for rooms larger, higher, and with fewer pieces of furniture in them than those of our modern houses, not to speak of the massiveness of fireplaces and fittings with which they were in character. It is their age, and the connection, which we cannot help tracing, with old houses and bygone generations which give architectural cabinets an interest now.
In construction, the skill of the cabinet maker will be shown in the neat and convenient arrangement of drawers of various depths and sizes, shelves or repositories, so contrived as to turn the entire internal space to account. The most curious contrivances are often found in old German, English, and French cabinets, bureaux, secrétaires, and other varieties of this kind of furniture. Pediments, capitals of columns, and other parts of architectural fronts are made to open, and secret drawers stowed away with an ingenuity almost humorous. It is upon the fronts and stands that the skill of great masters of the craft has been bestowed. The large wardrobes, or "armoires," of Boulle are examples of great inventive and designing power, as well as the marquetry of Riesener and David, and the chiselled metal-work of Berain, Gouthière, and that of many English artists.
As in past times, and so in our own, it is on cabinets that the real triumphs of the cabinet maker's art are displayed.
3. Fixed WoodworkThirdly, the joiner's and cabinet maker's art plays an important part in the fixed furniture of the house, and the woodwork, such as flooring, doors and door-frames, panelling, chimneypieces, with the complementary decorations of hangings, whether tapestry, silk, or the more humble material of paper.
In this last division of furniture the work is that of joinery. There is no great demand for constructive strength, as the work is fixed to walls; but as doors and shutters are swung to and fro continually, and subject to jars and strains, their stiles and rails, upright and cross-framing members, as well as the panelling that fills them, require well-seasoned timber and the most accurate workmanship: without these conditions the joints open, the panels shrink from the grooves in which the edges are held, and split, while the frame itself, if of unseasoned material, 'buckles' or twists, so that the door or shutter will no longer shut flat in its frame.
Panelling and fireplaces are, however, opportunities for the display of carving, inlaying, and gilding. The reader has seen carved room panelling, probably, in many old houses. In some of the municipal 'palaces' in Flanders, e.g. in Bruges, and in the old rooms of the Louvre in Paris, carved panelling of the utmost grace and perfection, some of it in groups of life-sized portrait figures, may be studied by the tourist.
Of work so rich and costly as this wood sculpture, it is perhaps hopeless to speak with reference to our modern houses, and in connection with the manufacture of furniture in this country, at least on any large or general scale of application. Still as such work, confined to the composition of fireplaces or sideboard backs, is still sculptured by Italian and French carvers, and has been sent to Universal Exhibitions of recent years, it must be considered a possible effort for our great employers of skilled labour.
The panelling of wall surfaces will be divided into larger or smaller reticulations or framework, with some reference to the size of the room, that is to say, that very large and lofty rooms will not bear the smaller subdivision of space and delicate moulding lines which are so general in panelling of mediæval or very early Tudor houses, and which are in keeping on walls of moderate size. Any inlaying or variety of woods should be used on walls with great discretion.
So far, then, on the general consideration of the work, which it is the business of the furniture maker to produce. In theory, it is his object to satisfy daily wants and necessities in the most convenient, useful, and agreeable way.
The difference between rudeness and refinement in daily habits consists in putting first order and propriety, then comeliness and cheerfulness into our homes and habits. There is so much to be borne and to be done merely that we may live, so many contradictions to natural inclination meet us on all sides, that we look for repose, and some moderate satisfaction to the natural desire of the eye, in that which meets it, and must meet it, so constantly. This satisfaction is beauty, or some measure of it, or what we have grown to take for beauty. As the eye is more exercised, the mind more informed, and becomes a better monitor or corrective to the eye, so we get less satisfied with much that passes for beauty, and so, on the other hand, we find it out in objects in which it is commonly or often passed over.
ManufactureA return prepared by the Commissioners for the Paris Exhibition, in 1867, gave the following as the number of manufacturers engaged in London in "the several branches of the fancy furniture trade."
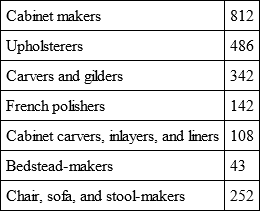
Wood and cabinet wares were exported (in 1865) to the value of 289,887l., and imported to the value of 128,925l.5
The highest efforts of the trade are concentrated in a few large establishments in London and the great cities, which have their own cabinet makers, carvers, upholsterers, &c., on their premises. In some instances, one piece of furniture may pass through the hands of several branches of the manufacture. I may choose a few names of makers who presented their works in Paris in 1867 in alphabetical order, e.g. Messrs. Collinson and Locke, Crace, Dyer and Watts, Gillow, Herring, Holland, Howard, Hunter, Ingledew, Jackson and Graham, Morant, Trollope, Wertheimer, Wright and Mansfield. The larger of these establishments are supplied with steam machinery, and all the work that can possibly be executed by mechanical agency is prepared by these engines, leaving only the most costly operations to be executed by hand.
It is the province of the carpenter to put together simple woodwork; that which is an actual part of architecture, such as boxes, chests, benches, seats, shelves, and so forth as require only good material and neatness of hand in execution. The joiner and cabinet maker include this amount of skill as a foundation for their accomplishments, as a sculptor can block out a statue and a painter grind his colours, work, however, which in ordinary practice is handed over to assistants or apprentices.
Before discussing the materials and the methods of execution now in use, it would be well to notice a great change which has taken place both in the status of the workman, the division of labour, and the mechanical appliances now at his command.
Down to recent times, joinery and cabinet making were in the hands of a number of masters in the trade, far greater in comparison to the pressure of the demand on the part of buyers than is the case at present. We have a larger society of buyers, a greater demand for the execution of large orders at a rapid rate, than was the case in former generations. On the other hand, the trade is gathered up into fewer master hands. The masters then employed a less amount of labour. They took in apprentices, many of whom remained for years with them as assistants, and the establishment was more of a family. It followed, that all members of this smaller society worked together and took part in the particular sets of chairs, the tables, cabinets, and so forth, turned out from their own house. They were, moreover, animated in a closer and truer degree by the spirit, and adopted the ideas, of a master who worked with or overlooked and advised them constantly, than could be the case in our great modern establishments. Again, though, as I have already said, the old operations by which boards, bars, and other members of wood construction are joined together, have not substantially varied since the days of Egyptians and Romans, the methods of execution have undergone a great change, owing to the introduction of machinery. The skill and training of the hand of the workman must necessarily undergo a change as well, whether for the better or the worse. The workman is relieved from the necessity of attaining an absolute accuracy in much of the ordinary but essential work of joints, mortises and other operations which can be produced with an uniform exactness by mechanical means.
The fact, also, that different engines or lathes can produce at a prodigious rate certain separate parts of many pieces of furniture, has made skilled mechanics less universal "all round" men than they were. If this combination of qualities is to be met with in provincial towns or villages, there, without doubt, the standard of excellence is a lower one.
Materials and Execution.– The woods used for making furniture besides pines and deals, are birch and beech (used for stuffed chair-frames, couches, &c.) walnut, letter wood, Spanish and Honduras mahogany, sycamore, lime, pear, cherry of several kinds, and maple; ash, English, American, and Hungarian; oak, English, foreign, and pollard, with pieces cut from wens and sweet cedar. Turners use also plane, laburnum, yew, holly, and box. More precious woods are also used in furniture: rose-wood, satin-wood, ebony, and sandal-wood. Other rare woods are used in inlaying and marquetry.
Some of these materials, mahogany and walnut, which are much in use, are imported in vast logs, the former sometimes three feet square; when of very fine grain suited to veneers, worth 1000l. or more, per log.
The woods are stacked in yards, or, in London, where the space cannot otherwise be had, on platforms resting on the walls of the workshops, and fully exposed to the weather. Woods are dried after a year, or two years, according to the size of the log and nature of the wood. Oak is sometimes kept for eight or more years. When sawn into the scantlings required, it is further dried by placing the logs and planks in rooms heated by the waste steam from the engine. An American patented method of drying is to place a coil of pipes, through which exceedingly cold water is passed in the drying room, which condenses and carries off the vapours from the wood exposed to this heat. Some firms have tried this method, but, I believe, without much success.
Logs are cut up by the engine with three or more perpendicular saws at once, the teeth being set to the right and left alternately, to open a passage for the blades. More valuable woods, e.g. mahogany, are cut into thin plank by an horizontal saw. In this case the teeth are not bent, but a labourer opens the passage for the blade by lifting the plank with a wedge. As little waste of the material as possible is thus secured.
Further cutting up of the material is done by means of circular saws. Part of the saw rises through a metal table. A moveable bar is firmly screwed at one, two, or more inches from the blade, and the wood is pushed by the workman against the saw, keeping one surface against the fixed bar, so as to secure a straight cut of the thickness required. Most modern planing is done by a revolving cutter, brought to bear upon the wood, which is drawn under it on an iron table, with more or less pressure, according to the quantity to be taken off the surface. Messrs. Howard have contrived a tube with a blast down it, which carries the shavings at once to the furnace, otherwise the dust made by the flying particles of wood would be unendurable.
Mouldings for panelling, cornices, skirtings, &c., are cut by revolving cutters or chisels, filed to any desired shape and case-hardened. They are set in a perpendicular axle and cut horizontally, the wood being firmly pressed against the tool. The workman can gear the cutter or reverse the action, so as to make a neat finish to his work.
Formerly all such work was done with a plane, cut to the required figure, and the finishings of lines of moulding had to be carved with the hand.
Mortising is done by a revolving boring tool, against which the wood to be mortised is moved by a gradual action, from side to side, and backwards and forwards, till the exact depth and width are bored out; tenons fitting these cavities are cut in another lathe, also by mechanical action.
Turning lathes.– The legs of chairs and tables are made in lathes, the general outline being obtained by turning in the simple form. Portions of the legs are sometimes squared, and the square faces must be evenly graduated. These parts are cut as follows: the lathe and the leg in it are kept at rest, and a revolving tool – in fact, a small lathe with a perpendicular cutter in it, connected by a leather band with a spindle overhead – set in motion by the steam-engine. The workman passes this cutter carefully down the four surfaces of the portions to be squared, cutting to a given depth all down, but never losing the angle outlines originally found by the first turning. When flutings have to be cut down the legs, whether they are round or square, this is done by using a revolving cutter set with horizontal action, which passes carefully along at one level, and is geared by the joiner so as to graduate the width of each fluting, as it descends, if the diminishing size of the support or leg requires it.
Bars of chairs, edges of shelves, the stretchers (or connecting bars) under some kinds of tables, are cut into carved or other shapes by an endless band saw revolving on two rollers. The workman passes his wood along an iron table against the saw, gearing the former according to the pattern drawn on the surface.
Fretwork is done with a still finer hair or watch-spring saw, of which one end can be detached from the holder and passed through a small hole in the piece of wood where the piercing is to be cut out by the saw. This could not be done by an endless saw, which can only be used to shape out edges. The best saws of this description are made by Perin, in Paris.
Watch-spring saws strained in frames have long been in use. In the steam-engine it is the wood only that is moved, and as it rests on a steady table, it gives the workman a great advantage, and should enable him to shape out his design with a delicacy only attainable with greater difficulty by the old method.
The process of mitreing pieces of moulding, where they meet at an angle at a corner, is done by machinery in some houses. In the works of Messrs. Jackson and Graham, this is done by setting the pieces in a metal T square. They are carefully cut by hand, and as each piece is set in a frame geared to the angle required, and under the hand of an experienced workman, no inaccuracies are likely to occur. In cabinet-making and joinery of all kinds, the number of angles round which mouldings have to pass is very great, as anyone will see who is at the pains to notice the construction of furniture of the most ordinary kind. Any staring or opening of an oblique joint is destructive of the effect of such workmanship, as it is of the strength of the joint which is glued together, and requires absolute contact of the parts to be joined.
Much work, such as chair rails, table legs, balusters for little galleries or on a large scale, is turned and cut in the steam lathe by hand, using steam power only to turn it.
Joinery.– The pieces of wood thus prepared are made up in many different combinations. This is the work of the joiner. In the joiners' shop of Messrs. Jackson and Graham, for instance, several benches were shown to me occupied by lengths of wall-panelling in ebony, some of the work being intended to cover the wall of a staircase; it was therefore framed in sloping lines. Each panel was a rhomboid, and none of the sides or mouldings were at right angles to each other. The mouldings had several fine strings, ovaloes, &c., all specially designed by the architect of the house – as the fittings of well-furnished houses should be. For these, special cutters had been made and fitted to the steam-moulding machine. To show the back of the panelling, the workmen turned it over. Instead of each panel being held in a groove provided in the stiles and rails, a rebate only has been cut in the frame, and the panel fits into it from the back (as the stretcher of a picture fits into a picture-frame), while iron buttons screwed into the frame pieces hold the panels firmly in their places. The object of this is to allow for the contraction of the wood with the alterations of temperature. With some woods, however well seasoned, this provision is requisite, and it is the more necessary, when more than one material is employed. In using ebony over large surfaces, it is found that the lengths required for the continuous rails cannot be procured free from knots or faults; and particular kinds of wood (pear and other material) are stained and prepared, to supplement the ebony in these instances.