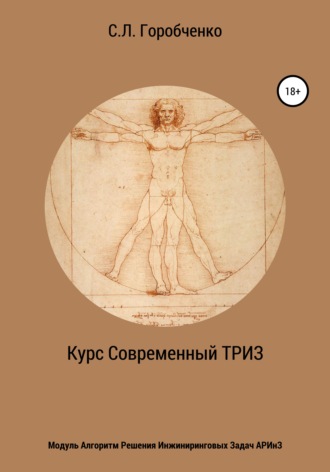
Полная версия
Курс «Современный ТРИЗ». Модуль «Алгоритм решения инжиниринговых задач АРИнЗ»
Как правило, задача заключается в нахождении путей изменения изделий так, чтобы создать функциональную модель изделия, максимально соответствующей выполняемой функции, либо включая полезные, либо исключая излишние функции. Опросам и прямым дискуссиям со специалистами предприятия здесь отведена ведущая роль. Именно они позволяют выявить оптимальный набор функций, ранжировать их по значимости. Приведем пример. Если только 15% специалистов отметили функцию как важную, то ее полное исключение позволит избежать до четверти издержек на производство и сбыт. Такую функцию желательно исключить. Правда, нужно быть весьма осторожными, поскольку важность функции может быть неосознанна, пока ее не исключили. Примеров тому множество.
Основой функционального подхода является заранее выполненная структурная схема объекта. Функции должны быть разделены на основные, второстепенные и вспомогательные. Полезно выделить также и надсистемные функции. Выполнение основных функций обеспечивается вспомогательными, а последних – вспомогательными низших порядков. В конечном итоге должна быть построена схема функционирования объекта с деревом функций. Если это технологическая схема, то может быть построена структурно-процессная диаграмма, напоминающая «рыбий скелет». При использовании таких простых инструментов анализа объект рассматривается системно, не пропускаются важные элементы и их связи. В частности примерно так разрабатываются схемы надежности технологических схем и выявляются «танцующие» контуры в технологических процессах.
Второстепенные функции связаны с выполнением основных, и поэтому являются полезными. Задача состоит в том, чтобы определить, как новое изделие, устанавливаемое в объект, позволяет усилить полезную функцию и уменьшить вредную. Часто вредные эффекты являются следствием полезных. Анализ сочетаний полезных и вредных функций дает возможность спрогнозировать получение максимально возможного эффекта, разрешить технические противоречия, найти способ устранения или уменьшения вредных функций при сохранении полезных.
Ранжирование функций по степени важности позволяет выделить долю вклада их в выполнение главной функции и общий полезный эффект. Если один и тот же элемент позволяет выполнить разные функции, то мы находим поле для синергии, или если имеются варианты выполнения разных функций, то получить альтернативы. Степень детализации предстоит определить в процессе анализа и выделения иерархии структуры объекта.
На этом этапе полученные схемы и матрицы отразят внутренние взаимосвязи в выполнении функций системы. Также важно построить функциональные схемы, отражающие и внешние связи с другими системами, получив отдельные взаимосвязи с жизнью объекта на стадиях проектирования, производства, транспортировки, монтажа, эксплуатации, ремонта, модернизации и утилизации. К примеру, для арматуры основными факторами, ограничивающими применение ее как изделия, являются нормативные документы, стандарты, а также руководящие технические материалы (РТМ) надзорных органов.
Чтобы определить очередность внедрения и направления использования тех или иных изделий, можно составить диагностическую таблицу. В ней суммируются разные оценки системы, выделяются наиболее важные противоречия и проблемы. Обычно значимость может быть присвоена методом экспертных оценок, а также анализом частоты появления проблемы, степени головной боли, аварийности и т.п. Дополнительными показателями должны стать экономические затраты и стоимость выполнения функций данным узлом и его роль в выполнении функций всем объектом в целом. Если значимость узла велика при относительно малых издержках, его можно считать благополучным, и при отсутствии особых причин он рассматривается в последнюю очередь. Если малозначащий узел имеет повышенную стоимость, заниматься им необходимо. В дополнение необходимо определить степень организационных трудностей, связанных с этим узлом. Для этих целей полезно обратиться к разным специалистам, от диспетчера, работников ОТК, лабораторий, до снабженцев и специалистов по ремонту.
Вместе с такой диагностической таблицей по структуре объекта может быть построена таблица значимости и по технологическим процессам, учитывающая значимость операций, материальные и трудовые затраты, уровень беспокойства, степень брака и т.п. Стоит учесть особенности разных процессов.
Пример. Для непрерывных технологических процессов важность аварийности и брака нарастает к концу процесса. Так, стоимость бумажной массы, и соответственно стоимость поддержания точной концентрации на мокром конце бумагоделательной машины перед напорным ящиком и сеточной частью значительно выше, чем после гидроразбивателя. Такие же способы материальной оценки в целом по технологической схеме применимы и для энергетики (стоимость энергетической воды возрастает к клапану питательной воды), в схемах водоочистки (стоимость очищенной воды наиболее высока на последних ступенях технологических схем очистки). Клапаны, установленные в конце процесса, должны быть значительно больше вовлечены в технологический процесс или иметь более высокую надежность.
Полученные таблицы, схемы и диаграммы полезно проанализировать с помощью таблиц выявления резервов, составленных по результатам многочисленных анализов внедрения изделий в сложные объекты. Также полезно использовать методики прогнозирования развития технических систем.
Оценка правильности постановки, преобразование и отбор задач для решения – это окончательная стадия аналитического этапа. Бесполезно применять наиболее эффективные инструменты анализа и решения задачи при установке нового изделия, если сама задача является надуманной. В конечном итоге и потребитель это поймет.
Причины неправильной формулировки кроются в сложностях и самого объекта. Болезнь может проявляться не там, где «болит». Могут даваться неправильные, надуманные причины и объяснения, и следующие из них надуманные решения проблемы.
Чтобы четче определить проблему, необходимо определить ее симптомы и показать нежелательные эффекты, возникающие при ее развитии. Нежелательными эффектами могут быть: недостаточная эффективность полезных функций; наличие вредных или ненужных функций; сложность системы; потребность в дорогих и дефицитных материалах; высокая трудоемкость; большая доля ручного труда; несоответствие реакции человека производственным скоростям; недостаточная надежность конструкции и т.п. Проблемы описываются вместе с ее владельцем – определенной деталью, узлом, агрегатом, участком технологического процесса.
Из определения нежелательного эффекта следуют две задачи – на «исправление» и на «недопущение». Новое изделие должно по возможности не допускать нежелательные эффекты. Исправление нежелательного эффекта, как менее эффективное решение, должно относиться к задачам второго эшелона, т.е. желательно их решать, если решение задачи на недопущение по каким-то причинам невозможно или нецелесообразно.
Также из множества выявленных проблем и вытекающих из них задач нужно выбрать наиболее приоритетную, т.е. дающую максимальный эффект. Такая задача:
– снижает максимальное число нежелательных эффектов;
– устраняет максимальное число исправительных операций и вспомогательных элементов для их выполнения;
– исключает подготовительные и вспомогательные операции, не связанные с конечным продуктом или главной функцией.
Эффективным приемом является функционально-идеальное моделирование – свертывание. (Подробнее см. ГоробченкоС. Л., Как происходит свертывание арматуры, ТПА 5\2012 стр.115–118). В этом случае предполагается формирование объекта с минимальным количеством элементов, но выполняющих основные функции и максимально приближенных к идеальному выполнению. Это достигается путем ликвидации всех вспомогательных элементов, всех вспомогательных операций и второстепенных функций. Последние передаются элементам, выполняющим основные функции и не подлежащим свертыванию.
Свертывание происходит по следующей схеме:
– для конструкции наиболее эффективно свертывать соседние по отношению к свертываемым элементам подсистемы;
– для технологических процессов – операции, предшествующие свертываемой, вплоть до поставки материалов, либо последующие, включая сборку и транспортировку.
Этап подготовки предложений
На этом этапе вырабатываются предложения по совершенствованию объекта с применением изделий поставщика. Сначала задачи сортируются с выделением нескольких основных групп:
– Задачи, не содержащие противоречий, т.е. решаемых обычными средствами с минимальными изменениями в системе. Это задачи на устранение излишков неоправданных усложнений, завышенных параметров, нерационального использования материалов. Такие задачи легче всего решаются, и изделие легче всего внедряется с быстрой экономией.
– Задачи с противоречиями, допускающими компромиссное решение, и частично удовлетворяющее противоречивым требованиям. Основная проблема и техническое противоречие не устраняется, но его последствия сглаживаются. Такие задачи – это снижение массы конструкции при сохранении прочности и надежности, подбор оптимальных материалов, формы, химического состава и т.д. Решения требуют трудоемкого обоснования, применения специальных методик оптимального проектирования, проведения экспериментов по выбору наилучшего варианта.
– Задачи с противоречиями, не допускающими компромиссных решений. Такие задачи можно решать с применением всего опыта в т.ч. и из других отраслей, являющимися надсистемами, где подобные задачи могут быть уже решены. Внедрение решений является весьма трудоемким делом, зато эффект будет максимальным.
В результате поиска появятся решения с разной степенью достижения идеального конечного результата, разрешения проблемы, противоречия, соответствия закономерностям развития продукта, экономической эффективности и т.п. Они должны быть окончательно оценены экономистами.
Особенно важно выделить сверхэффекты, вредные эффекты и системные свойства, проследить возможные изменения по всей технологической цепочке, которые произойдут при внедрении изделия.
Сверхэффектам нужно найти применение, и развить их с получением максимальной пользы. Для вредных эффектов, возникающих в процессе внедрения, необходимо найти способы их недопущения и, в крайнем случае, исправления. Чтобы выявить их еще до внедрения, полезно использовать «диверсионный» и «инверсный» подход. Не вдаваясь в подробности методов, скажем, что при их применении задача решается как бы наоборот, т.е. ищутся проблемы, которые могут возникнуть при внедрении изделий.
Экспертиза предложений
После выработки предложений необходимо провести их экспертизу. При этом все предварительные предложения разбиваются на 3 группы:
– не требующие при внедрении серьезных изменений конструкций и технологии, в частности перепланировок, замены дорогостоящего оборудования, изготовления сложной оснастки, деталей трубопроводов и пр. Такие предложения быстро внедряются, особенно те, которые направлены на отмену операций и устранение деталей, например, при унификации.
– предусматривающие значительные изменения в технологии, но не требующие переутверждения технических условий, внесения изменений в стандарты, нормативные документы, регистрации в поднадзорных органах и т.п.
– серьезно изменяющие конструкцию, технологию, внедрение возможно только при серьезной модернизации.
На основании выбора того или иного предложения необходимо разработать план-график внедрения, определить ответственных со стороны поставщика и потребителя и включить предложения в план организационно-технических мероприятий по повышению эффективности производства, планы по новой технике, планы по экономии материалов, снижению трудоемкости и т.п.
Этап внедрения
Подразделения и службы предприятия, получившие плановые задания по внедрению изделия поставщика, выполняют его. Контроль осуществляется в плановом порядке.
Хочется сказать, что скептиков всегда будет много. Их основные высказывания сводятся к следующему:
– улучшать ничего не надо, все и так отлично и проблем у нас нет;
– улучшать нужно, но все равно не удастся;
– возможно, внедрение вашего продукта что-то и даст, но кто его захочет внедрять;
– захотеть, может, и захотят, но все равно не внедрят;
– если внедрят, то все равно экономического эффекта не будет;
– это работает на других предприятиях, а у нас особые условия;
– мы и без вас совершенствовали агрегаты, технологические схемы и т.п.;
– сначала докажите, что это реально, потом и внедрим;
– для внедрения вашей продукции нужны специально обученные особенные специалисты. У нас таких нет.
– Денег нет.
– Это слишком ново для нас.
– Дайте в опытную эксплуатацию, потом и решим.
По традиции и трудностей хватает. Ниже приведен их перечень на примере арматуры.
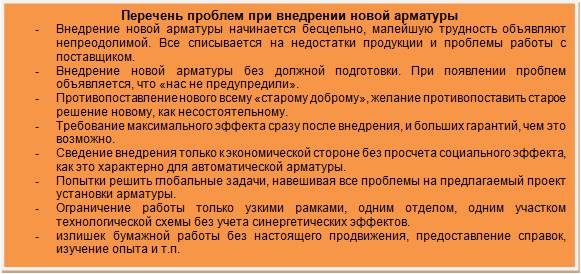
Этап мониторинга
По сути, этот этап является уже «последействием» продажи. Однако от его прохождения зависит, станет ли этот клиент для вашей компании постоянным, а ваше решение – стандартом для отрасли. На этой стадии резко возрастает роль сервиса, как с точки зрения оперативного реагирования на технические вопросы, дополнительного обучения, снижения возможных претензий и пр.
Хорошо проведенный мониторинг при первоначальном внедрении продукции зачастую дает одновременно и ответы на вопросы первоначальной эксплуатации и хорошие референцы и сторонников решения. Это оказывает большую поддержку продавцам в дальнейшем.
Мы подробно рассмотрели возможности применения одного из главных инструментов АРИнЗ – инженерно-экономического анализа для целей выбора наиболее эффективной продукции, способной быть и технически, и экономически состоятельной. Основой анализа является создание функциональной модели, отображающей неудовлетворенные и прогнозируемые потребности потребителей в инжиниринговом продукте, и нахождение технических решений, которые по своим потребительским свойствам будут превосходить существующие решения.
Для этих целей важно не только не пропускать ни одного основного этапа в разработке сложных технико-коммерческих предложений, но и внимательно изучать «расстановку сил» и организационно-технические трудности на предприятии. Важно и чаще практиковаться, как показано, например, в статье Горобченко С. Л. (см. ГоробченкоС. Л., Как разработать технико-коммерческое предложение с применением инженерно-стоимостного анализа в журнале ТПА экспресс №1\2013 стр. 53–59).
Чтобы добиться успеха в условиях конкуренции, анализ применимости предлагаемых решений по представленному механизму должен стать неотъемлемой частью подготовки внедрения сложных инжиниринговых решений.
Использованная литература
1. АльтшуллерГ. С., ЗлотинБ. Л., ЗусманА. В.. Поиск новых идей: от озарения к технологии (теория и практика решения изобретательских задач). – Кишинев: Картя Молдовеняскэ, 1989.
2. Герасимов В., ЗлотинБ. Л., ФСА в действии в журнале техника и наука, 1982 №11, с.10–12.
3. Горобченко С. Л. Как разработать технико-коммерческое предложение с применением инженерно-стоимостного анализа в журнале ТПА экспресс №1\2013 стр. 53–59.
6.1.2. Кейс. Практикуемся в разработке технико-коммерческого предложения на проектную спецификацию арматуры с применением инженерно-стоимостного анализа
Множество разработок комплексных и сложных технико-коммерческих предложений начинается с получения обычного запроса на предложение. Иногда даже не прилагается опросных листов. Как правило, специалисты равняются на известные им решения и вообще-то проверяют этим, а знаешь ли ты таковые решения. Конечно, есть и другой вариант «послушать, как у них там за бугром делается».
Часто советником является проектный институт, однако, он не является знатоком многих участков использования арматуры, и мы можем сказать, что проектные институты в свою очередь равняются на решения, разработанные еще в советские времена уже не существующими НИИ. За последнее время опыт применения арматуры уже во многом переместился в инжиниринговые и арматурные компании. С учетом растущей конкуренции инженерных решений, предлагаемых разными фирмами, и накопления опыта их внедрения, старые разработки институтов не могут быть и вовсе применены.
Тем не менее, на этом первом этапе уже ставится задача «как есть», и с этого момента начинается работа по проведению инженерно-экономического анализа с целью разработки наиболее конкурентного предложения (подробнее см. Горобченко С. Л. Практический маркетинг. Применение комплексного инженерно-экономического анализа для маркетинговых целей ТПА – экспресс, 1\2013). Ниже мы приводим пример разработки сложного коммерческого предложения, проведенного специалистами компании Метсо для одного из предприятий содовой промышленности.
После опроса специалистов немного кристаллизовались первые задачи.
ИСХОДНЫЕ ДАННЫЕ
Проект, включает в себя следующие задачи:
1. реконструкция цеха абсорбции и дистилляции по регулирующей арматуре
2. приведение в соответствие с требованиями Ростехнадзора по безопасности
3. замена запорной арматуры.
4. установка интеллектуальных позиционеров
Двигателем прогресса стали требования Ростехнадзора – не часто встретишь…
В рамках действующей реконструкции ставятся следующие задачи:
1. выполнение предписаний Ростехнадзора по повышению уровня безопасности.
2. установка современной системы АСУТП.
3. установка приборов КИП и А в рамках действующих проектов реконструкции.
4. снижение выбросов в т.ч. и по арматуре.
Важно, что в комплексе с КИП и А и вместе с системой АСУТП. Из этого следует, что требования к качеству регулирования и исполнительным механизмам будут на уровне.
Требования к запрашиваемой арматуре:
1. подготовка исполнения арматуры в соответствии с опросными листами (для бюджетного предложения).
2. применение современной арматуры
3. работоспособность в современных системах автоматизации управления и контроля техпроцессов.
4. смарт клапаны с интеллектуальными контроллерами, работающими на сигнале 4–20mA на основе HART-протокола.
5. V класс герметичности для 80% отсечных клапанов.
6. фланцевое исполнение.
Ключевое для нас слово смарт клапаны с интеллектуальными контроллерами прозвучало. Хотя и жаль, что «на основе HART протокола»…
Дополнительные положения, принятые во внимание.
1. Высокая экспортоориентированность (80% продукции идет на экспорт).
2. Сложность, непрерывность и взаимозависимость производств между собой.
3. Необходимость снижения потерь сырья и химикатов за счет повышения точности регулирования.
4. Необходимость уменьшения объема обслуживания арматуры и КИП.
5. Перспективность освоения современной смарт арматуры для дальнейших новых проектов.
Экспортоориентированность – первый признак того, что предприятие – серьезное. За рубежом не любят брака. Следовательно, и требования к качеству регулирования будут, по всей видимости, немаленькие…
На первом этапе нами была проведена большая информационно-аналитическая работа по поиску основных тенденций и типовых решений и цифр, отражающих современное состояние производств содовой промышленности. Для этих целей были привлечены консультанты КЦ Промконсалт ВШТЭ СПбГУПТД Санкт-Петербург. Выдержка из отчета приведена ниже.
Особенности содового производства
Производство кальцинированной соды по аммиачному способу включает в себя восемь основных переделов (отделений):
1. Получение карбонатного сырья на ГОКах.
2. Переработка карбонатного сырья: обжиг, охлаждение и очистка диоксида углерода, гашение извести с получением известковой суспензии.
3. Очистка рассола: взаимодействие сырого рассола с реагентами в реакторах и отстой рассола.
4. Абсорбция: отмывка в промывателях газов, выделяющихся на других стадиях от аммиака, двухстадийное насыщение раствора хлорида натрия (рассола) аммиаком и частично диоксидом углерода, поступающим со стадии дистилляции, охлаждение аммонизированного рассола.
5. Карбонизация: отмывка от аммиака газа, покидающего стадию карбонизации (сопровождается улавливанием небольших количеств диоксида углерода), предварительная карбонизация; карбонизация с выделением гидрокарбоната натрия в осадительных колоннах, компримирование перед подачей в карбонизационные колонны, диоксида углерода, поступающего со стадий переработки карбонатного сырья и кальцинации.
6. Фильтрация отделение гидрокарбоната натрия на фильтрах и отсос воздуха вакуум насосами.
7. Кальцинация: обезвоживание и разложение гидрокарбоната натрия в содовых печах, охлаждение и очистка диоксида углерода после содовых печей.
8. Регенерация аммиака (дистилляция) предварительный подогрев и диссоциация содержащихся в фильтровой жидкости карбонатов и гидрокарбонатов аммония в конденсаторе и теплообменнике дистилляции, смешение и взаимодействие нагретой жидкости с известковой суспензией в смесителе и отгонка аммиака.
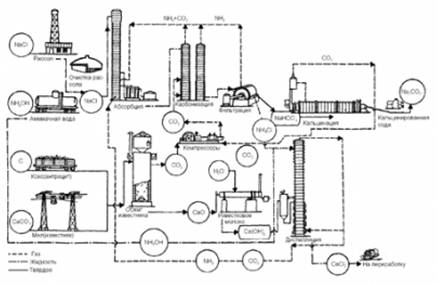
Рис. 1. Технологическая схема производства кальцинированной соды
Что ж, специализация по химии в полном объеме. Нас ждет масса регулирующих и отсечных клапанов, способных работать в полупериодическом режиме и кристаллизующихся средах…
Технико-экономические показатели процесса получения соды.
Экономические показатели производства кальцинированной соды характеризуются следующими данными (данные по литературным источникам):
1. На 1 т продукта расходуется:
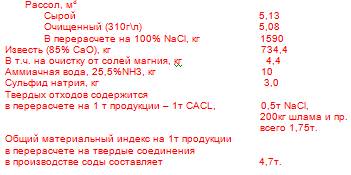
Начнем считать. В первую очередь по массовым технологическим потокам. Выделим, что в своем большинстве среда – рассольная и с наличием извести, а также наверняка и с абразивными шламами.
2. Энергетические затраты.
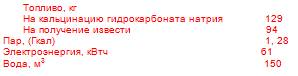
Как следует из описания – самый дорогой процесс – кальцинация. Здесь и будут лежать источники окупаемости клапанов и энергосбережения.
3. Фондоемкость производства соды
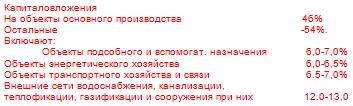
Надежда на энергетику не оправдается. Затраты не велики. Основная эффективность будет лежать в собственно регулировании параметров технологического процесса.
4. Сумма капитальных затрат по объектам основного производственного назначения распределяется следующим образом:
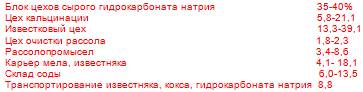
Основные капитальные затраты также лежат в собственно технологических линиях, а не вспомогательных, добычных или транспортных процессах. На таких предприятиях Технологи «правят бал».
5. Структура себестоимости соды кальцинированной характеризуется следующими данными, %:

Примерно также распределится и эффективность от работы арматурного хозяйства в целом. С учетом того, что "технология превыше всего", то задачей для арматуры будет не снижение расходов на содержание и ТО, а на снижение потерь в технологии (графа «сырье и материалы»).
6. Общая сумма затрат на 1 т соды распределяется по стадиям производства следующим образом, %:
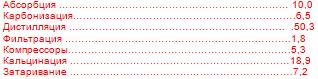
Основные процессы – адсорбция, карбонизация, дистилляция и кальцинация занимают все эксплуатационные затраты на производство. И еще раз мы правы в том, что основное внимание при подготовке предложения нужно будет направлять на технологические эффекты и сверхэффекты.
7. Использование тепла в основных отделениях производства соды составляет в долях от общего теплопотребления, %
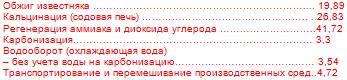
Если отдельно заняться клапанами для обеспечения подачи технологического пара и газа, то нас ждут обжиговые печи, кальцинация и регенерация аммиака и диоксида углерода. Остальные не интересны. Хотя в последнее время и охлаждающей водой можно заниматься, особенно там, где переводят охлаждение на испарительное охлаждение. Экономия воды – в 40 раз!
8. Определение технико-экономических показателей (ТЭП) в содопоташном производстве.
Выделяются до 100 технико-экономических показателей. Выделим наиболее существенные. Сопоставление отдельных видов технологических затрат для различных аппаратов показало, что при выпаривании стоимость пара составляет 81–87% от суммы технологических затрат на переработку растворов; при сушке 81–87% затрат приходится на долю мазута, при вакуум кристаллизации основной статьей расхода является стоимость воды (71–76%).