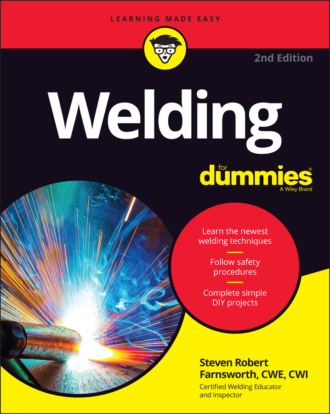
Полная версия
Welding For Dummies
Welding machine basics
Following are a few welding machine considerations that you can keep in mind when you start thinking about the type of machine you want to buy for your shop.
❯❯ Power source: Be sure to purchase a welding machine that fits the electricity power source that you have available. Most household or small shops have only single phase electricity available.
❯❯ Current: Welding machines are also sometimes classified by the type of current they require. Some machines use alternating current (AC), which is an electrical current that flows back and forth at regular intervals in a circuit. Other welding machines use direct current (DC), which flows in one direction.
❯❯ Duty cycle: Welding machines are rated on duty cycles, which indicate how many minutes out of ten the machine can run continuously at its maximum amperage output. (Most welding machines have an output of at least 200 amps.) A welding machine’s duty cycle is based on the manufacturer’s recommendation. For example, if a 200-amp machine is rated with a 60-percent duty cycle, you can use it continuously (and safely) for six out of ten minutes when you have it set to produce an output of 200 amps. You can get a constant potential (CP) welding machine that maintains a constant flow of electricity, which results in a 100-percent duty cycle.
❯❯ Material type and size: Some welding machines can weld just a couple of different types of metal, and others can weld a huge range. You should also keep the size (thickness) of the metals you’re welding in mind. If you’re welding materials that are less than 3/18 inch thick, most welding machines are powerful enough for you. If you’re welding thicker metals, you may want to get a machine that can produce more amperage.
New or used: Which welding machine is right for you?
After you understand the different types and classifications of welding machines (see the preceding section), you need to decide whether to buy a new machine or one that has been used.
The advantages and disadvantages afforded by new and used welding machines are similar to what you’d expect for most other types of machinery or equipment. New welding machines have no wear and tear, and you can often buy one with a warranty that helps protect you if the machine (or part of it) happens to break down soon after you buy it. Plus, new machines come with instructions that can be extremely helpful for a beginning welder, whereas used machines often no longer have the directions. On the downside, new machines are almost always more expensive than comparable used models. New stick welding machines typically cost at least $400, and mig welding machines are often twice that amount. A brand new tig welding machine can run you $1,200 or even more, depending on the size and features of the machine.
If you want to buy a new welding machine, you can find them at larger hardware and home improvement stores, welding supply stores, and through online retailers.
Used welding machines can be a good route for people who are just starting out with welding and don’t want to sink a lot of money in a new machine. You can find quality used welding machines for half the cost of a new machine. The good news is that most welding machines don’t wear out or become ineffective unless they’re mistreated or maintained poorly.
If you want to buy a used welding machine, you likely have three options:
❯❯ Auctions: Equipment or general auctions in your area can be a great source for used welding machines. Call ahead or look through auction listings to see whether any welding machines are up for bidding.
❯❯ Welding supply stores: Many welding supply stores offer incentives for welders to trade in their used welding machines when they’re looking to buy a new machine. The stores then sell the used machines, sometimes after carrying out some basic maintenance or making any necessary repairs to the machine.
❯❯ Individual sellers: If you have friends or family members who weld, you may ask them if they have a used welding machine that they’re interested in selling in the near future. That’s a good situation because it means you know the seller and are probably familiar with how he treats his equipment. (Although if that relative is your reckless Uncle Bob, you may want to think twice.) You can also find individual sellers looking to sell used machines in classified ads or through online listings.


Stick welding machines
Stick welding is one of the most widely practiced welding techniques. (You can read all about stick welding in Chapters 5 and 6.) One of the biggest reasons for stick welding’s popularity is the fact that it’s inexpensive – in fact, the equipment used in stick welding is the least expensive of all the electric welding processes. Stick welding machines include the machine itself, as well as the welding leads, ground clamp, and electrode holder (see Figure 4-4). That’s all! If you’re going to be doing any stick welding and you want to get your hands on a stick welding machine, the big choice you have to make is whether you want an AC or DC machine.
❯❯ DC: DC stick welding machines give you a continuous flow of electricity, and they make it easier to produce good welds because they give you a higher level of control.
❯❯ AC: AC stick welding machines have one very important advantage: price. AC stick welding machines are the cheapest welding machines you can buy, and they require little or no maintenance. However, they can be a little harder to work with than DC machines, especially for new welders.
FIGURE 4-4: Typical stick welding machine.
Mig welding machines
Mig welding machines are more complex than stick welding machines and include a welding gun, a spool of electrode, an electrode feeding unit, a power supply, cables, hoses, and a cylinder of shielding gas. (Flip over to Chapters 9 and 10 for more on those terms and other mig welding details.) You can check out mig welders at your local welding supply store, and you can also get parts (like refills for your shielding gas cylinders) there as well.
Mig welding machines (see Figure 4-5) are designed to weld a range of materials, including steel, stainless steel, and aluminum, to name just a few. However, if you want your mig welder to work on a variety of metals, you have to buy a few attachments. A mig welding machine without any additional attachments can weld steel, but if you want to weld aluminum, for example, you need a spool gun. Want to weld stainless steel? You need to change your shielding gas cylinder. Your local welding supply store can tell you all about what you need to change on your mig welder if you want to take advantage of the machine’s versatility and work on many different metals.
FIGURE 4-5: A mig welding machine.


Tig welding machines
Tig welding machines are the most versatile of all the welding machines. With a tig machine (see Figure 4-6), you can weld all ferrous and nonferrous metals. Most tig machines allow you to change polarity (the direction in which the electricity flows), and that allows you to weld a wider range of materials.
FIGURE 4-6: A tig welding machine.
Tig welding machines and stick welding machines are somewhat interchangeable with a little modification. Stick welding machines can be used for tig welding if you buy and add on a number of attachments, and vice versa. If you’re planning on working on both tig welding and stick welding projects, I suggest buying a tig welding machine and also purchasing the attachments – a stick welding electrode holder with a lead and plug on the end that matches the machine – that allow you to use it for stick welding. It’s easier to make a stick welding machine from a tig machine than the other way around.
If you want to read more about the ins and outs of tig welding machines, check out Chapters 7 and 8.
Considering a few accessories for your welding shopAs with most types of equipment, you can add a few bells and whistles to your machine in the form of accessories. These items can make your machine easier to use, so you may consider whether one or more of the following are right for your setup:
❯❯ Cable holder: A hook mounted to the side of the machine that you can use to hold your lead and ground cables, cable holders help keep your work area more organized (and safer).
❯❯ Cup holders: I know it’s hard to believe, but you can now get cup holders that mount to your welding machine. Just make sure your drink has a lid.
❯❯ Storage: You can get small drawers for some welding machines now that can helpfully store the various small parts that you need when welding.
❯❯ Welding machine carriage: These carts have wheels that make moving your welding machine easier. They’re almost always made of steel, and you can buy one for about $200. That seems like a lot, but some welding machines weigh more than 100 pounds, and spending $200 for a cart is much cheaper than spending twice or three times that amount at the chiropractor’s office!

In addition to the basic tools, welding table, welding machine, and welding machine accessories I discuss in the preceding sections, this section lists several other tools and pieces of gear you may want to buy and have on hand when you’re getting ready for a welding project or setting up your shop. You can find all these items at welding supply stores or hardware/home improvement stores.
❯❯ Air compressor: If you’re going to be using any pneumatic tools, you need a good air compressor. Cost: $160.
❯❯ Anvil: An anvil is a good tool to have around when you need to hammer or straighten out a large piece of metal. (It’s also useful, of course, if you’re a coyote and you’re trying to kill a roadrunner.) Keep in mind that you can also use a large, solid, secured piece of metal (a railroad rail, for example) in your shop in place of an anvil. Just don’t go pulling up train tracks to save money. Cost: $150.
❯❯ Creeper: A creeper (shown in Figure 4-7) is a small platform with wheels that you can lie down on and use to roll around. Creepers are helpful when you need to get up under something. Cost: $30.
FIGURE 4-7: A creeper.
❯❯ Drill press: I think having a good, small drill press on hand in the welding shop is extremely handy. Be sure you have plenty of good bits that fit the press. Cost: $100 to $1,000.

❯❯ Grinder: Grinders are useful for grinding down rough surfaces. If you get a grinder, make sure to also pick up some ferrous and nonferrous grinding discs that fit the machine. Cost: $85 to $125.
❯❯ Hacksaw: Hacksaws are extremely useful for cutting metal. Cost: $8 (includes a package of blades).
❯❯ Portable welding curtain: These items (see Figure 4-8) are usually made of vinyl, and they can help to shield bystanders from the dangerous rays created while welding. Cost: $10.
❯❯ Vise: Consider mounting a small vise to your welding table. It can be very helpful when you’re trying to work on small projects that are tough to manipulate while welding. Cost: $25.
❯❯ Wall clock: It may sound simple, but having a clock mounted on the wall is a much easier way to keep track of the time while welding than having to take off your gloves and push up your sleeves to check your watch. Welding is fun, and time flies when you’re having fun, so why not have an easy way to keep track of it? Cost: $3.
FIGURE 4-8: A standard portable welding curtain.
Part 2
Welding on a Budget: Stick and Tig Welding
IN THIS PART …
Understand and practice stick welding, the most common type of welding done in the world today.
Find out all about tig welding, a lesser known but still very widely practiced welding technique.
Chapter 5
Getting on the Stick: Understanding Stick Welding
IN THIS CHAPTER
❯❯ Considering stick welding’s advantages and disadvantages
❯❯ Figuring out when you should use stick welding rather than other processes
❯❯ Knowing important stick welding factors
❯❯ Perusing the equipment you need for successful stick welding
No matter what level of welding you consider – from industrial and commercial applications to tinkering around with a small project or two on the weekends – stick welding is always one of the most prominent and dynamic welding techniques, partially because it’s one of the more inexpensive welding types.
Regardless of what you want to do with your welding skills, you need to understand the basics of stick welding so that you can make it a key aspect of your welding repertoire. In this chapter, I offer an overview of many critical stick welding basics.
Looking at the Pros and Cons of Stick Welding
As with any welding technique, stick welding offers distinct advantages and disadvantages. The beauty of stick welding (also known as shielded metal arc welding or SMAW) is its versatility and portability. Using stick welding you can weld metals in a wide variety of thicknesses and from a range of positions. (In Chapter 6, I go into detail about how you can stick weld in multiple positions.)
You can also stick weld just about any kind of metal, including steel, stainless steel, aluminum, and just about anything in between. If you’re just getting started with welding as a hobby and you know that you’re going to want to weld a lot of different materials, stick welding is a solid choice for you.
Following are a few more characteristics that have helped make stick welding one of the most commonly used welding processes.
❯❯ Stick welding equipment is less expensive than the equipment you need for any other welding process, in some cases costing half or a third as much.
❯❯ Stick welding equipment is lightweight, and it isn’t as complex as the gear you need for other welding processes.
❯❯ A range of stick welding electrodes allow you to tackle many different welding applications.
❯❯ Stick welding allows you to weld in confined spaces.
❯❯ Stick welding operations are very portable. If you know that you’re going to have to weld outside of the friendly confines of your welding shop, stick welding is probably a good choice.
❯❯ You don’t have to prepare the surfaces of the metal you plan to weld as much as what you’d have to do to get the metal ready for other welding processes.
Stick welding sounds great, doesn’t it? It really is a great technique, but it’s not without flaws or drawbacks. Here are a few of the cons associated with stick welding:
❯❯ Stick welding can be very labor intensive, which can result in high labor costs.
❯❯ You always waste part of your stick-welding electrodes when you’re working on a stick-welding project because you have to stop using an electrode when two inches of it remain. (More about that in Chapter 6.)
❯❯ Stick welding requires that you do a lot of cleanup as you work your way through a weld. You must clean the weld after every pass and after every pause or stop.
❯❯

❯❯ As compared to the other welding processes, stick welding is the least efficient in terms of converting electricity to useful welding heat.
❯❯ The welds that result from stick welding often have to be chipped and ground down, which can create harmful dust.
❯❯ The chipping and cleaning necessary with stick welding can be extremely noisy, and that poses a risk for hearing damage.
❯❯ Although stick welding equipment is pretty simple, the technique you need to master to stick weld successfully can be difficult to pick up.
❯❯ Stick welding electrode stubs are short and round, and they can cause a slipping hazard if you accidentally step on one.
❯❯ Stick welding can be slow because you have to stop welding when you work your way through an electrode. You also have to stop often to chip away at accumulated slag on your welds.
Understanding the Factors That Influence Stick Welding
When you’re stick welding, you can control several key factors that determine how your weld comes out. These welding variables allow you to change the finished product of the weld, including the height and width of your welding bead, the amount of spatter, and the penetration. (Penetration is how deep the weld goes below the surface of the metal you’re welding.) I find that new welders really benefit by thinking about these factors before they dig in to the details of stick welding. Here are some pointers that may help improve your welds:
❯❯ You can increase or decrease the amperage of your weld by using the controls on your stick welding machine.
❯❯ You can increase or decrease the speed of travel (the speed at which you move the electrode along the weld joint) of your weld.
❯❯ You can increase or decrease the arc length (the distance from the end of the electrode to the metal you’re welding) of your weld. Your arc length should be the same distance as the diameter of the electrode core wire you’re using.
❯❯ You can change the angle at which you hold the electrode to affect penetration. If you hold the electrode so it’s basically perpendicular (at a 90-degree angle) to the parent metal, you get maximum penetration. If you hold it at a tighter angle – 45 degrees, for example – you get less penetration.
❯❯ You can use a side-to-side motion with the electrode to control the width of your weld.
❯❯ You can use a variety of electrode types and sizes. Check out Chapter 6 for details.
❯❯ You can use different kinds of polarity (the direction electricity flows in direct current or DC). Check out the “Polarity” section later in the chapter for more on this topic.
If you control these factors correctly, you end up with a good, solid stick weld. If you can’t, you end up with a poor, weak weld. You can see examples of both in Chapter 6.
Getting Familiar with Stick Welding Equipment
Конец ознакомительного фрагмента.
Текст предоставлен ООО «ЛитРес».
Прочитайте эту книгу целиком, купив полную легальную версию на ЛитРес.
Безопасно оплатить книгу можно банковской картой Visa, MasterCard, Maestro, со счета мобильного телефона, с платежного терминала, в салоне МТС или Связной, через PayPal, WebMoney, Яндекс.Деньги, QIWI Кошелек, бонусными картами или другим удобным Вам способом.