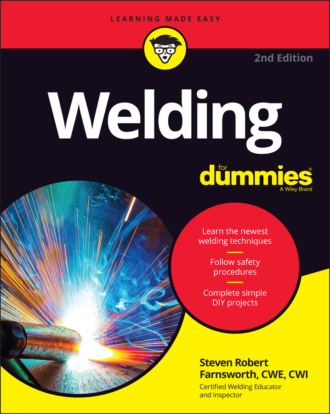
Полная версия
Welding For Dummies
❯❯ Sterile bandages of various sizes
❯❯ Cold pack
❯❯ Sterile gauze in various sizes and lengths
❯❯ Burn gel or spray
❯❯ Antibiotic ointment
❯❯ Hydrogen peroxide
❯❯ Sterile compress dressings of various sizes
❯❯ Sterile gloves
❯❯ Tweezers
❯❯ Sterile adhesive tape
❯❯ Eyewash
❯❯ Antibacterial moist towelettes
❯❯ A protective airway mask
You should be able to find a first-aid kit that includes all these items at a hardware store or home improvement warehouse. I provide a useful example in Figure 3-6.
FIGURE 3-6: A well-stocked first-aid kit.
Knowing how to handle injuries
You may not be a doctor or an EMT, but if an injury occurs, you can still take some very basic steps to begin treatment and keep the injury from becoming more serious. Below I give you an overview of some of those steps.
❯❯ Bleeding and wounds: Apply steady pressure with a clean cloth or gloved hand. If the wound isn’t severe, clean it thoroughly and dress it with sterile bandages. If the wound or bleeding is severe, call 911 or go to the hospital immediately.
❯❯ Broken bones: Don’t move the injured body part or try to reset the bone. If any section of bone is protruding from the skin, cover it with a sterile, moist cloth. Call 911 or go to the hospital immediately.
❯❯ Electric shock: If you witness someone suffering from an electric shock, don’t touch them! You’ll become part of the circuit and be shocked, too. Instead, quickly turn off the source of the power. If the victim is unconscious, not breathing, or otherwise seriously injured, call 911 immediately.
❯❯ Gas inhalation: If you or someone in your work area inhales dangerous gases, get them into the fresh air and seek medical assistance immediately.
❯❯ Poison swallowed: If someone accidentally swallows a poisonous substance from your welding shop, call your poison control center or 911 immediately and follow its instructions. Take care to note the details of the poison that has been consumed. Don’t let the victim drink anything unless you’re directed to do so by emergency personnel or someone from the poison control center.
❯❯ Heart attack: Welding can be strenuous, and heart attacks while welding aren’t unheard of. If you or someone near you begins to experience severe pain in the chest, pain in the left shoulder, aching in the left arm, shortness of breath, or a bluish color in the lips or fingernails, dial 911 immediately.
❯❯ Clothing fires: Welding causes a lot of sparks, and those sparks can ignite clothing. If your clothing catches fire, strip it off immediately if possible. If you can’t strip it off quickly, you should stop, drop, and roll to put out the fire. Don’t run around – that fans the flames and makes the fire larger.

❯❯ Burns (heat): Each one of the three different types of heat burns has its own treatment. (You can see examples of all three kinds of burns in Figure 3-7.)
● First-degree burns cause the skin to become red and tender but don’t break the surface of the skin. If you suffer a first-degree burn, run cold water over the area to cool it off and then cover it with a clean cloth and apply sterile bandages. Don’t use ice on a burn because it can damage the tissue.
● Second-degree burns occur when the skin is severely damaged; they commonly involve blisters and even breaks in the skin. If you suffer a second-degree burn, run cold water over it to decrease the pain and then cover the affected area with a sterile bandage. If a blister forms, don’t try to break it.
● Third-degree burns are the most serious type. If you suffer a third-degree burn, you likely feel very little pain in the affected area because the nerve endings have been destroyed. If you suffer a third-degree burn, seek medical attention immediately. If clothing is embedded in the burn, don’t try to remove it yourself.
❯❯ Burns (chemical): Some chemicals can cause burns; if your skin comes in contact with one of these materials, immediately flush the area with water. Remove all contaminated clothing and cover the burn with a clean, dry cloth. If the burn is serious, seek medical attention.
❯❯ Eye injuries: If a foreign object strikes or becomes embedded in your eye, place gauze over the eye immediately and secure it with a bandage. Don’t attempt to remove the object. Go to an eye doctor, call 911, or visit an emergency room as soon as possible. If a chemical comes in contact with your eye, flush out the affected area with warm running water right away and then place gauze over the injured eye and seek medical attention.

❯❯ Plume poisoning: If your welding area isn’t well ventilated and you’re not wearing a respirator, you can suffer from plume poisoning, which is sickness or injury that results from inhaling dangerous welding byproducts. If you accidentally inhale those substances, you should immediately get away from the plume and into some fresh air. Then seek medical assistance right away. For more on respirators, check out “Watching health hazards: Using a respirator and Material Safety Data Sheets” earlier in the chapter.
FIGURE 3-7: The three different kinds of heat burns.
Chapter 4
Setting Up Your Welding Shop
IN THIS CHAPTER
❯❯ Selecting and setting up your welding location
❯❯ Making sure you have all the necessary equipment
If you want to succeed with any welding endeavor, you need to cover two bases: location and equipment. You can’t get very far with welding – particularly good welding – if you don’t have the right kind of setup, from the building itself to the tools and other gear you need to equip the space properly.
Some folks who are new to welding think they can simply clear out a space in their garages, buy a welder from an online retailer at a deep discount, and start making high-quality welds in no time. Not so fast! You need to think through all the requirements necessary for a welding space that allows you to do good work and do it safely. And when you’re talking about welding equipment and tools, you need to make sure you have all the basics (and maybe a few extras as well).
In this chapter, I tell you how to get set up for welding. I start by filling you in on the details of how you can identify a suitable location for welding. No two welding methods or jobs are the same, but even with all that variety, all good welding sites share a number of characteristics that you need to maintain if you want to ensure a productive and safe working environment. After that, I move on to a discussion of welding equipment, which you need to choose carefully so you end up with gear that fits your welding needs.
Choosing a Location
You can’t find too many hobbies or jobs that are more versatile than welding. Welders with lots of experience are able to make welds in some pretty amazing places (underwater and in space, for example). But if you’re just starting to weld, you can get set up in a relatively simple, straightforward way. You don’t have to have a massive, state-of-the-art facility for your welding endeavor; you really just need to make sure your welding space has a few basic features, including the following:
❯❯ Adequate lighting: Like all other trades, welding requires ample lighting so that you can clearly see what you’re working on. Make sure your welding space has plenty of light, whether that’s natural, electric, or some combination of the two.
❯❯ Flame retardant floors and walls: Many welding tasks create sparks, so you certainly can’t fire up the old welding machine in a room with shag carpeting and wallpaper. Instead, try to find a space that has, for example, concrete floors and cinder block walls (or something equally resistant to catching fire).
❯❯ Large doors: If you’re going to be welding any large items, you need to be able to get them into and out of the welding area safely and smoothly. Keep in mind that you may limit yourself in terms of the range of welding projects you can tackle if you can’t fit certain items into the space. A large overhead or roll-up door is necessary if you want to work on bigger projects indoors.
❯❯ Sufficient electrical service: Welding machines and other equipment used in cutting, grinding, and welding can use quite a lot of electricity, so be sure that your welding location is properly serviced. Generally speaking, you should be in good shape if you have 220 single phase service (the kind of electrical outlets you use to plug in an electric clothes dryer) or 110 single phase service (the kind of outlets located all throughout your home, used for plugging in lamps and small electrical appliances) with 20-amp circuit breakers. (Those are some of the most common circuit breakers out there.)
❯❯ Ventilation: You can read more about safety-related issues like ventilation in Chapter 3, but for this part of the discussion, just make sure your welding space is properly ventilated so that you (and any other people nearby) don’t suffer any negative health effects from the gases and smoke that welding can produce.
Deciding how much space you needThe amount of space you need in order to weld safely and successfully is always important. Because of the potentially hazardous nature of many welding processes, you need to make sure you have enough space; otherwise, you put your health and the quality of your work at risk.
Many people who are new to welding assume that they can set up a little welding shop somewhere in their home. (A garage or shed is usually the first choice.) That can be okay, but only if the space you’re considering fits the criteria in the preceding section and also doesn’t compromise your safety. (Be sure to read Chapter 3 carefully if you have any doubts or questions about the safety precautions you need to take before you begin welding.)

When you’re considering a potential space for your welding work, think hard about the kinds of items you plan to work with. Is your space big enough to allow you to move those objects around without banging into other projects, your tools, or – worse yet – your body? Keep in mind that the equipment you’re working with may very well be heavy, sharp, and/or hot. Those aren’t the kinds of items you want to be trying to manipulate and move in a cramped environment.
Another important factor to consider is the amount of space your welding equipment takes up. Most welding machines – more about those later in this chapter – are only about three feet by four feet, but you may end up eating up quite a bit of space after you factor in all the other gear and supplies you need. Be sure to allow plenty of room for your equipment, or your welding projects may suffer from a cumbersome and disorganized workspace.
Contemplating indoor versus outdoorSometimes the welding project you’re working on dictates the location in which you’re forced to work. If you’re welding a big piece of equipment that has broken and become immobilized outdoors somewhere, you may very well be forced to do your welding outside. If that situation (or something similar) arises, don’t automatically think that it presents a difficult challenge. Welding outdoors can actually be just as enjoyable and productive as welding in an indoor welding shop, and in some cases even more so. Indoor and outdoor welding each have a number of advantages and disadvantages you want to bear in mind when you find yourself in a situation that allows you to make that choice on a particular welding project.
When you weld indoors, you often have the advantage of regulating the temperature in the building. That can be a huge plus, as anyone who has been forced to weld outside in the sweltering heat of summer can attest. You can also control the lighting to fit your needs and the needs of the job, and when you weld indoors, your equipment isn’t exposed to the damaging effects of the weather.
However, welding indoors isn’t all positive. No matter how big your welding space is, some jobs just don’t fit indoors. Welding inside a building can also be more difficult if you’re doing the kind of welding that produces an unusually large amount of smoke and dangerous fumes. Your indoor welding space has ventilation, of course, but chances are your indoor ventilation system isn’t as good at whisking away the fumes and smoke as a spring breeze can be when you’re welding outside.
As you can imagine, the biggest challenge presented by outdoor welding is the elements. The weather can wreak havoc on the quality of your work and the integrity of your equipment. Precipitation can make welding unnecessarily dangerous, and forget welding successfully when the temperature is below 40 degrees Fahrenheit if you don’t preheat the materials. And even sunshine, which is usually a pleasant part of welding outside, can pose a problem: Sometimes direct sunlight makes certain types of welding helmets function poorly. (Read more about welding helmets in Chapter 3.) Finally, if you’re welding outside where other people will be present, you really need to set up a safety screen so your audience’s eyes aren’t harmed by the welding process if they happen to look at it.
Equipping Your Welding Shop
You’d be hard pressed to find a skilled trade or craft that doesn’t require some specialized equipment, and welding is definitely no exception. But hey, you’re talking about joining metals, not making ham sandwiches, so I’m sure it comes as no surprise that you need some specific gear in order to get the job done right. You can get a look at some of the necessary equipment in Figure 4-1.
In this section, I let you know what kind of general equipment you need for a welding project. Keep in mind that plenty of other types of gear are necessary for certain kinds of welding, and I tell you about those tools and materials in the parts of this book that dig into the details of specific welding types. (For example, you need certain items for flux core arc welding that you don’t need for the other kinds of welding, and I cover those specific items in Chapter 9.)
FIGURE 4-1: A well-equipped welding area setup, this one for stick welding.

You have plenty of options when you’re looking to obtain your welding equipment. A lot of different manufacturers are producing tools and materials now; if you do a quick Internet search for a chipping hammer – one of the most basic welding tools – you find dozens of options from many different suppliers in a range of prices.
So which equipment is right for you? In many cases, you can let your budget be your guide; look around (at hardware or home improvement stores, on the Internet, in welding catalogs, and so on) at the various options and find some that fit both your needs and your price range. Then, to narrow your choices, read some online reviews of the various products and talk to knowledgeable salespeople at the retailers you’re considering. If you have friends, family members, or co-workers who weld, pick their brains about the tools and materials they use.

Some of the tools you need for your welding projects are basic hand tools. Several of these items are pretty common, so you may very well already have one or a few of them in your toolbox now. If you don’t, though, you’re going to have to get your hands on them, because you can’t do without them.

Following are the basic tools you need, some of which are shown in Figure 4-2:
❯❯ Ball-peen hammer: Ball-peen hammers are used for striking chisels and punches. They’re also handy for straightening metal. The rounded head is used for peening, which relieves the stress in a joint that you’ve just welded. You can pick up a good ball-peen hammer at a hardware store for around $15.
❯❯ Chipping hammer: A chipping hammer is a specialty hammer you use to remove excess material (called slag) from your welds. Chipping hammers come in a range of sizes, but they’re typically a foot long and weigh about a pound. If you’re buying a new chipping hammer, you can expect to spend between $10 and $30.
❯❯ Crescent wrench (12 inches): Keeping a 12-inch crescent wrench on hand when you’re welding is always a good idea. It fits the majority of the nut and bolt sizes you encounter in welding.
❯❯ Level: A level is necessary to make sure the pieces you’re welding are at the correct horizontal or vertical position and also to test the accuracy of completed projects. Make sure you have an extremely durable level because they take a lot of abuse.
❯❯ Pliers: You definitely need a good pair of pliers for welding, and the run-of-the-mill pliers most people have in their toolboxes don’t really get the job done. You need slip joint pliers (pliers that let you increase the range of their jaws) with compound lever action to handle hot metal. You can also use tongs. Depending on the size of the pliers and the number of bells and whistles involved, you can expect to spend anywhere from $7 to more than $20.

❯❯ Soapstone or silver pencils: You can’t use regular pencils or pens to write on metal, so you need to use soapstone or silver pencils. You can find both at your local hardware store for only a few dollars.
❯❯ Steel square: The steel square is a durable tool that you can use to keep your project in square during assembly. It’s essentially a right angle made out of steel, with one side 16 inches long and the other side 24 inches long. The face side of a steel square has a ruler that marks whole, half, quarter, and eighth inches. The back side is divided into whole inches, halves, and quarters.
❯❯ Straightedge: A straightedge is a must for drawing straight lines, transferring measurements, and double-checking for straightness. After all, nobody wants a crooked weld.
❯❯ Tape measure: You have to be able to measure and mark your materials to cut at the right dimensions, so a tape measure is a must. Luckily, tape measures are one of the most common tools out there. You can handle most jobs with a 25-foot-long, 1-inch-wide tape measure.
❯❯ Vise grips: These wrenches are combination tools that function as pliers, wrenches, portable vises, and clamps. They aren’t intended to replace box-end wrenches because of the damage they do to the fittings you’re working on. Most people prefer to also have a pair of pliers (as mentioned earlier in this list) in addition to vise grips.

❯❯ Wire brush: You use wire brushes to clean up welds after you’ve chipped away at them. I recommend getting a brush with a nice long handle. If you want to kill two birds with one stone, some manufacturers sell a combination chipping hammer/wire brush. You can get a good wire brush for $10 to $20.
FIGURE 4-2: A typical ball-peen hammer (a), chipping hammer (b), crescent wrench (c), level (d), steel square (e), and straightedge (f).
Choosing a welding table
You need a very sturdy, reliable surface to use as a foundation for welding practice as well as many of your welding projects, especially the smaller jobs. The best option is a welding table. Don’t try to use a normal table or work bench, because the wood or metal construction will soon be spattered with (and probably burned by) welding materials.
A good welding table includes a steel top and angle iron or sturdy pipe for legs. (Check out the welding table in Figure 4-3 to get a feel for what one looks like.) Your local welding shop can build you a welding table, or you can buy one at a hardware or home improvement store. The table size you need is determined by the size of the projects you plan to work on. I recommend getting a table that is ⅜ inch thick, with a top that is 36 inches by 48 inches. Expect to spend at least $50, and remember that after you get the hang of welding, you can make your second table instead of buying it.
FIGURE 4-3: A typical welding table.

One of the most important pieces of welding equipment you buy is your welding machine, the apparatus that provides the energy you use to make your welds and complete your welding projects. The machines come in many types, sizes, and prices to fit the needs of any welder. You can find inexpensive machines for small shops and projects, and expensive, more powerful welding machines for big shops and huge projects.
One of the most important considerations you need to keep in mind when you’re deciding which welding machine to acquire is the type of welding you plan on doing. Welding machines are available for all the various types of welding: stick welding, mig, tig, and more. (You can read more about the various types of welding in Chapter 1, and in the chapters that make up Parts 2, 3, and 4, where I dive into the details of each welding type.)