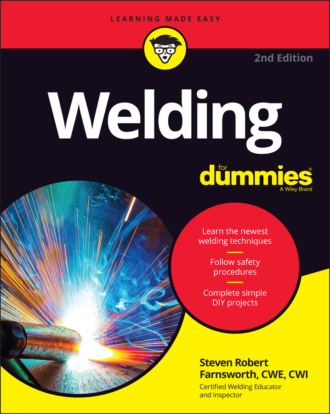
Полная версия
Welding For Dummies
Steel is a strong, versatile metal that you’ll use all the time in your welding projects. You may not realize it, but steel is really an alloy made up of iron and less than 2 percent of another material. Carbon is often used in steel alloys, and you can find three different levels of carbon steel: low-, medium-, and high-carbon steel. The more carbon in the steel, the stronger the alloy is.
You should use steel in your welding projects when you’re looking for a strong metal that’s pretty easy to weld and doesn’t break the bank when you’re buying your materials. You can use any welding process I describe in this book on steel, so versatility is also one of its strong suits. But steel also has its downsides. For one, it’s heavy. If you want your fabricated project to be light, steel probably isn’t your best bet. Steel is also prone to rusting and scaling (flaking off due to oxidation), so you have to spend a fair amount of time cleaning it up (often with a grinder) before and sometimes during welding.
Stainless steelStainless steel is amazing stuff. It has a lot of the good qualities that regular steel has (see the preceding section), but it also offers one added bonus: It resists corrosion (rust, for example) like a champ. You can put a piece of stainless steel out in the yard and let it get rained on for six weeks, and when you bring it back inside it probably won’t have a single spot of rust on it. Incredible!
How does stainless steel provide such remarkable resistance to corrosion? Its alloy contains 10 to 30 percent chromium (the rest is iron, although sometimes other metals, such as nickel, are also added to the alloy).
You can weld stainless steel with all three of the major types of arc welding (stick, mig, and tig). It’s a great choice if you want your project to resist rusting or to have hygienic surfaces (those that don’t harbor bacteria and other microscopic critters).

Like stainless steel, aluminum is great at resisting corrosion. And aluminum offers another pretty terrific characteristic: It’s lightweight. Compared to steel and stainless steel, aluminum is a real featherweight.
Pure aluminum is a popular choice for welders, but aluminum alloys are also frequently used. Copper, manganese, and zinc are just a few of the metals that are often alloyed with aluminum to produce enhanced characteristics in the finished product.
If you’re going to be welding aluminum, I recommend going with tig welding. It just makes for a cleaner, easier job. If tig isn’t an option, take mig welding; you can stick weld aluminum, but it’s not ideal – your choices for stick electrodes are going to be limited, and you’re probably going to have a difficult time maintaining the correct arc length.
Taking the Time to Understand Welding Safety
Welding utilizes some pretty extreme forces and materials. Most modern welding requires tremendous amounts of electricity, which of course can create a risk for electric shock. No matter what kind of welding you pursue, you’re always going to be working around some incredible levels of heat, too, and those kinds of temperatures can harm you, other people, and your property in myriad ways. The metals you weld are sometimes sharp and often heavy, so with them you can get that rare and unfortunate double threat for lacerations and back injuries. Finally, you can’t forget other potential hazards that welding can create, including rays that can do serious damage to your eyes and fumes that can hurt your lungs and make you very sick.


Exploring Welding Methods
You can use heat to join metals in several different ways, but by far the most common welding methods used today are the arc welding methods. Arc welding is really pretty simple in theory: A large amount of electricity creates an arc between an electrode and a base metal, and that arc generates enough heat to melt the materials in the weld area and join them together to make a weld. In practice, however, arc welding includes three different welding processes (stick, mig, and tig) and has many different variables. For example, some kinds of arc welding use a shielding gas, whereas others don’t. The electrodes that you use in arc welding may be consumable, meaning they get melted and incorporated into the weld, or they may be non-consumable. The electricity used in arc welding is the source of many other variables, including amperage (which can vary a lot) and current (either alternating current or one of a couple different forms of direct current).
Because the three main types of arc welding are the most commonly used throughout the world and the easiest to pick up, those are the three that I devote the most attention to in the following sections (and throughout the book). However, they aren’t the only game in town, so I also include some information on those other types in case you want to branch out a bit.
Stick weldingStick welding (also called shielded metal arc welding or SMAW) is an arc welding technique that has the distinction of being the most commonly used welding practice in the United States today. (More than 40 percent of all welding done now in the United States is stick welding.) The prevalence of stick is even stronger in construction; more than half of all construction-related welding uses stick. And the percentage is even higher in the maintenance industry.
Stick welding enjoys such popularity for three primary reasons. First off, it’s cheap. You can get into stick welding for less money than you’d spend to get started with tig welding. Secondly, stick welding is highly portable. The equipment is lightweight, and you can easily use it outdoors if the conditions allow it. Finally, stick welding is versatile. You can use it to work on metals with a wide range of thicknesses, and you can stick weld in just about any position that fits with your skill level.
Stick welding is great, but it isn’t perfect. One main reason is that it’s messy. Welding waste products, such as slag and spatter, get thrown around during a stick weld a lot more than they do when you’re tig or mig welding. Because of that, you have to plan on spending some time cleaning up your welds and weld area after you’re done stick welding. Another of stick’s imperfections is its speed (or lack thereof). You have to be pretty good at stick welding to do it quickly (especially compared to, say, mig welding).
You can read all about the stick welding process in Chapters 5 and 6, but generally speaking, stick welding utilizes a consumable electrode with a solid metal rod in its core that melts down and forms part of the weld. Small globules of molten metal flow from the tip of the electrode through the electric arc to the molten weld pool. The electrodes have a coating of flux that protects the molten metal from impurities in the air that can contaminate the weld as it cools.
Mig weldingMig welding is another arc welding technique. You may also hear mig welding referred to as gas metal arc welding (GMAW) or wire welding. Mig welding is becoming more and more popular, for several reasons. At the top of the list is the fact that most people find mig welding to be easier to pick up than stick and tig. Another big reason is the speed; done correctly, mig welding can be quite a bit faster than stick or tig welding thanks to its continuously fed wire electrode, which doesn’t require changing nearly as often as the stick electrodes used in stick welding. You can just keep right on welding without having to stop and change your electrode. Over the course of a welding project, that can definitely save you quite a lot of time.
Proponents of mig welding also cite the low amount of slag and spatter that mig produces. That makes for a more pleasant welding experience, and a much more pleasant cleanup experience. The low chance of distortion (unwanted changes in a piece of metal’s shape) is also trumpeted by those who love mig welding. Because the process is faster, you don’t need to apply as much heat to the weld area for as long, so the metal is less likely to bend and twist in nasty ways.
Of course, mig welding also has its downsides. For starters, mig welding equipment is more complex than stick welding equipment, so it’s quite a bit more expensive. The handheld part of the mig welding equipment (called the mig gun) is often big and bulky, so it’s usually tough to mig weld in tight spaces. Mig welding also relies on the use of a shielding gas to keep atmospheric contaminants away from the weld area, so the process doesn’t really work very well outdoors (especially with any kind of breeze).
I save the details of the mig welding process for Chapters 9 and 10, but generally speaking, here’s how it works: A wire feeder continuously feeds the wire electrode to the weld area at a speed you control. That produces a steady molten stream that you can easily direct however you want on the surface of the metal you’re welding. The weld is completely covered with a shielding gas (usually argon) to prevent impurities from fouling up the quality of the weld; you control the flow of the shielding gas to suit your project’s needs.
Tig weldingThe last type of arc welding is tig welding, which is sometimes called gas tungsten arc welding or GTAW. One major advantage to tig welding is that it’s extremely clean. If you’re tig welding correctly, you may very well go through an entire project without having to spend any substantial amount of time cleaning up. Tig is also extremely versatile. You can use tig welding to work on a lot of exotic metals that just aren’t in play for, say, stick welding.
Tig welding has two big drawbacks. One is cost – you can definitely spend a pretty penny on tig welding equipment and supplies, even for start-up. The second drawback is lack of speed. You get a lot of precision out of tig welding, but you pay for it with time.
The tig welding process was originally developed in the 1940s to join aluminum and magnesium, but you can use tig welding to join all kinds of different metals. The big difference in tig welding is that it uses a non-consumable electrode that’s almost always made of tungsten. It also requires the use of a water- or air-cooled torch, which holds the tungsten electrode and is connected to the welding machine by a power cable. Like stick welding (see the earlier section), tig uses an arc of electricity to heat metal to its melting point, and you manipulate the puddle to join metals together. The major difference is that tig welding uses a tungsten electrode. You can read more about tig welding in Chapters 7 and 8.
Other welding methodsThere’s more than one way to skin a cat, and there are more welding processes beyond the big three arc welding techniques (see the preceding sections). Here are a few to consider; check out Chapter 13 for more info.
❯❯ Brazing is unique among the welding processes because you can use it to join different materials (two different metals, for example). It uses gas rather than electricity, and the heat used in brazing surpasses 800 degrees Fahrenheit.
❯❯ Soldering is a form of welding that uses (relatively) low amounts of heat. You can solder at temperatures below 800 degrees Fahrenheit. (That’s downright chilly when it comes to welding.) You can solder with gas or electricity, but the electricity you use in soldering isn’t the same as the type of electricity you use in arc welding. Instead, soldering uses an electric soldering iron that heats up and melts the filler materials you’re adding to the project you’re working on.
❯❯ Oxyfuel/oxyacetylene welding is probably the most common gas welding process. You do it with a gas-powered flame that melts the base metal and any filler materials necessary to make the weld. The equipment used for this type of welding is the most portable and low cost in the welding world.
Looking at the Future of Welding
The need for skilled welders is huge right now, and it’s only going to continue to grow. New metal alloys are being created and used for a wide range of purposes every day. The industries that rely on welding are expanding rapidly across the globe, and the need for metals to be joined in skillful ways isn’t going anywhere in the near future. Welding is a versatile field that you can study in a number of different ways, from on-the-job training to education at a vocational or technical school. If you practice and develop your welding skills and work hard, you can more than likely make a career out of welding. And after you’ve been a welder for a while, you can very easily transition into a position as a welding supervisor, on-site supervisor, or inspector, just to name a handful of the possibilities.
But don’t think that you need to make a career out of welding in order to enjoy and appreciate the process. You can weld to fix things around your house, yard, or farm. You can weld to create things that you use in your personal or professional life. You can weld to create works of art or gifts for friends and family. Or you can weld just because it’s fun and rewarding (and there are few better reasons to weld than that).
Chapter 2
Considering Commonly Welded Metals
IN THIS CHAPTER
❯❯ Understanding steel
❯❯ Getting a grip on stainless steel
❯❯ Taking a look at aluminum
❯❯ Reflecting on a few other metals
Good chefs know food, good carpenters know wood, and any good welder really knows metal. I know that sounds painfully obvious, but I’m sometimes surprised to learn that many seasoned welders aren’t all that familiar with the metals they work with on a daily basis. I think having a nice, rounded understanding of the metals you weld is important, and that’s what this chapter is all about.
If I had to pick three metals that most new welders want to begin working on as soon as possible, I’d have to go with steel, stainless steel, and aluminum. If you can familiarize yourself with those three metals and understand their characteristics as they pertain to the various types of welding, you’re well on your way to figuring out how to work with three of the most common, versatile metals out there. With that in mind, I start this chapter by devoting individual sections to each of those three metals. After that, I close the chapter with a quick look at some of the other metals that you may want to consider welding, just to clue you in on some basics and give you a feel for what’s possible beyond the old standbys.
Steeling Yourself for Using Steel
Steel is an extremely common metal. It’s all around you – chances are, you’re probably not more than a few feet away from something made of steel. For that reason alone, it’s a very important metal for welding.
Steel is an alloy that’s made up primarily of iron, along with less than 2 percent of another material. That material is usually carbon, and the amount of carbon present in the steel is an important feature. Here’s a quick look at the three different levels of carbon steel:
❯❯ Low carbon or mild steel has less than .2 percent carbon. This category of steel is extremely easy to work with; you can cut and form low carbon or mild steel a lot easier than many other metals. Lots of objects, including screws, bolts, nuts, and washers, for starters, are made of low carbon steel. Sheets of low carbon or mild steel are often used to make automobile bodies and other familiar products.
❯❯ Medium carbon steel has .25 percent to .55 percent carbon, and it’s more difficult to work with and form than low carbon steel. You can find medium carbon steel in some of the same products made of low carbon steel, but the medium carbon versions are stronger. Machine parts (gears, axles, levers, and so on) are also often made out of medium carbon steel because of its strength and durability.
❯❯ High carbon steel is the really tough stuff. More precisely, it contains between .55 percent and 2 percent carbon. It’s the hardest and strongest type of steel, but it can be a real pain to cut and form. Manufacturers use high carbon steel to make things like cutting tools, files, and hammers because those items need to be strong enough to keep their shapes and integrity through years of heavy abuse.
Getting a handle on forms of steelSteel is manufactured in many different forms, and each form has its own use for welding projects. Here are a few of the more common forms that you’re likely to run into as you weld:
❯❯ Flat steel is exactly what it sounds like – a flat piece of steel. It’s also called sheet steel. It comes in a range of thicknesses and sizes, but when it’s larger than 12 inches wide, it’s called plate steel.
❯❯ Steel bars are made in an array of shapes, but the most common are round, square, or flat. You can see some examples of steel bar shapes in Figure 2-1.
FIGURE 2-1: Square (a), flat (b), and round (c) steel bar shapes.
❯❯ Rolled steel comes in two forms.
● Hot rolled steel is made to its finished size while the steel is still red hot. Iron oxide forms on the hot steel after it’s rolled. It’s a grayish-black coating that helps protect the steel from rusting. Hot rolled steel is used for piping, tubing, tanks, and other products.
● Cold rolled steel is made by rolling the steel to its finished size after it’s cooled to room temperature. It doesn’t get the iron oxide that hot rolled steel gets, so cold rolled steel is smooth and bright looking. It’s used for making things like nails and screws.

Steel is such a ubiquitous metal that it’s hard to imagine life without it. It has become an important part of everyone’s life, and the ways you live, play, and travel certainly wouldn’t be the same if steel was no longer available.
You can use steel for a wide variety of welding projects; it’s cheap, readily available, and pretty easy to weld. If you’re looking to weld objects such as farm equipment, tools, cars, automotive equipment, specialty containers (drums, pipes, and boilers), or even bridges and parts of buildings, you should strongly consider steel as your metal of choice.
When is steel not appropriate for welding? Well, if you’re working on or repairing a piece of metal that’s definitely not made of steel, such as repairing an aluminum piece on a boat, using steel won’t work for that project.
If you’re starting a new welding project from scratch and really need to end up with a lightweight product, steer away from steel. Steel is durable and cheap, but it’s also pretty heavy compared to many other metals. Steel also doesn’t work if you’re welding something to be used for any sort of food service application; food almost always involves water of some sort, and water rusts steel, creating an unsanitary environment. For the same reasons, using steel for anything in a medical setting is also a bad idea.
THE MANY PROPERTIES OF METALSIt’s a little hard to believe how many different kinds of metals are out there. Metals run the gamut from tungsten, which is one of the hardest materials on Earth, to mercury, which is a liquid at room temperature. Here are a few of the physical properties of metals that combine in different ways to make metals unique.
● Strength: How much external force the metal can take without breaking.
● Ductility: The ability to change shape without breaking.
● Magnetism: Some metals (like steel) are magnetic; others (like aluminum) aren’t.
● Hardness: The resistance of a metal to being damaged when another metal is applied to it.
● Resistance to oxidization: When metals combine with oxygen, they become oxidized. That’s what causes steel to rust, for example. Some metals – tungsten, for instance – are very resistant to oxidization.
● Electrical conductivity: Some metals conduct electricity much more efficiently than others. For example, silver is an incredible conductor of electricity, but stainless steel doesn’t conduct well at all.
● Melting point: Every metal has a melting point – the temperature at which the metal turns from a solid to a liquid. This property is critical in welding because, of course, you’re trying to melt metal. Tungsten has the highest melting point; you need temperatures of 6,170 degrees Fahrenheit to melt tungsten. That’s remarkably high compared to, say, tin, with a melting point of only 450 degrees Fahrenheit.

All metals have to be cleaned and prepared before you weld them, and steel is definitely no exception. Quality welds aren’t going to happen if your steel is covered with surface contaminants. And some of those contaminants can be downright dangerous to your health if they’re heated up and converted to fumes while you’re welding. (Flip to Chapter 3 to read all about the safety gear you can get to protect yourself from fumes.)
You especially need to do your best to remove rust from the surface of your steel. Rust is especially common on mild steel (covered earlier in this chapter), and it can wreak havoc when you’re trying to produce a high quality weld. The most common defect you experience as a result of rust is porosity (the presence of lots of little holes) in your welds, and porosity can really ruin a good weld joint.

You can use one of two methods for cleaning your steel prior to welding: chemical or mechanical. The method you choose depends on the metal type, the condition of the metal, the welding process you’re planning to use, and the equipment available.