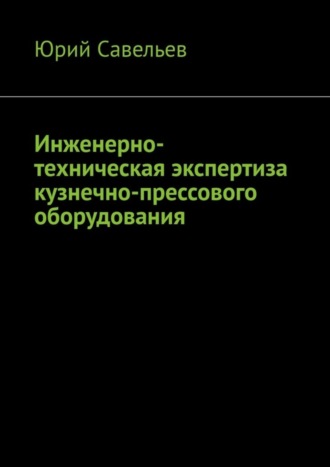
Полная версия
Инженерно-техническая экспертиза кузнечно-прессового оборудования
б) погрешности механической обработки (искажение геометрической формы деталей, следы грубой механической обработки) – поломки валов отдельных экземпляров прессов из-за недопустимого биения, искажения формы вала, подрезания галтельных переходов, рисок, шлифовальных трещин и ожогов;
в) дефекты монтажа (перекосы, неправильная посадка, неправильная фиксация и регулировка деталей и узлов, повреждения поверхности деталей и т.д.) – поломки подшипников прессов различных моделей из-за перекосов валов и колец подшипников.
3. Эксплуатационные причины включают нарушения правил эксплуатации КПО, работающего в условиях, соответствующих его назначению, и случаи эксплуатации КПО в условиях, не соответствующих его назначению:
а) неправильная наладка – поломки и повреждения из-за перегрузки главных валов (усилие, несоответствующее номинальному или при установке несоответствующего штампа, который должен устанавливаться на более мощном прессе);
б) использование пресса при постоянном тяжелом режиме работы – поломки деталей механизма главного привода, «посадки» пресса.
В качестве примеров повреждений, возникающих в результате одновременного действия нескольких причин, можно привести поломки зубчатых соединений, связанных как с дефектами термообработки зубчатого венца (технологическая причина), так и действием значительных динамических перегрузок (конструкционная причина).
Оценка изменения точности КПО в процессе эксплуатации
Вследствие износа элементов КПО (направляющих, нижней поверхности ползуна, нижней и верхней поверхностей подштамповой плиты, деталей соединения Главный вал-ползун), от которых зависит точность формообразования штампованных изделий, а также деформаций деталей пресса начальная точность КПО с течением времени снижается. Это уменьшат технологические возможности прессов, а в ряде случаев снижает их производительность и вызывает необходимость в регулировках и ремонте.
Длительность сохранения начальной точности КПО в значительной мере определяет их долговечность в эксплуатации, являясь обобщающим показателем, учитывающим влияние различных факторов (износостойкости деталей, возможности деформаций, жесткости конструкции, качества изготовления и др.).
Изменение точности КПО в процессе эксплуатации изучается путем последовательных измерений характеристик точности прессов по соответствующим ГОСТам.
Процесс изменения точности пресса является случайным по самой сути происходящих явлений, так как прессы различаются по своим свойствам (в том числе и прессы одной модели и одной партии выпуска), и, кроме того, условия эксплуатации КПО являются переменными.
Принципиально ясно, что условия эксплуатации точных прессов более постоянны, чем прессов нормальной точности, и, следовательно, объем измерений в первом случае может быть, при прочих равных требованиях к точности результатов, меньше, чем во втором. Ограничения на объем выборки могут быть установлены лишь из организационных и экономических соображений.
Периодичность измерений точности можно рекомендовать порядка 2—3 раз в год. В дальнейшем важно строго выдерживать выбранный интервал между измерениями (это существенно облегчает последующую обработку результатов). Наряду с измерениями точности КПО отечественного производства рекомендуется брать для наблюдения одну или несколько моделей лучших импортных прессов аналогичного типоразмера.
Сравнение результатов измерений потери точности позволит выяснить относительный уровень долговечности по точности отечественных прессов по сравнению с лучшими мировыми образцами. Измерение утраты точности импортных прессов проводится по тем же проверкам ГОСТа, при тех же требованиях к условиям проведения измерений, оформления результатов и т. д.
На основе методики разрабатывается календарный план-график эксплуатационных испытаний, определяющий объем работ и предусматривающий сроки проведения периодических проверок точности. При этом, исходя из производственных возможностей каждого производственного объединения, уточняются сроки и порядок проверок точности КПО. Одновременно подготовляются необходимые приборы, формы технической документации и журналы наблюдений. Если измерения точности КПО производятся не с момента установки на заводе-потребителе, то необходимо точно знать его срок службы до момента первого измерения.
Анализ эксплуатационных разрушений металлических деталей КПО возможен после проведения предварительно подготовленных мероприятий по изъятию разрушенных деталей разобранного узла, элемента гидравлической или пневматической схемы и фрактографического исследования, предложенного авторами Гордеевой Т. А., Жегиной И. П.
Категоричными в данном случае являются требования к качеству и достаточной для достоверности (воспроизводимости другими исследователями) полноте объема диагностических мероприятий по установлению причины поломки или аварии.
По данным Кальнера В. Д. и др. при применении методов неразрушающего контроля при арбитражном и экспертном анализе видов дефектов стальных деталей, разрушенных в процессе эксплуатации следует руководствоваться следующими рекомендациями:
трещины (усталостные и др.):
открытые с поверхности – магнитный (желательно люминисцентный); токовихревой; ультразвуковой; капиллярный; рентгеновский;
внутренние – токовихревой; ультразвуковой; рентгеновский;
точечные коррозионные или эрозионные поражения; фреттинг-коррозия – магнитный (только люминисцентный);ультразвуковой; капиллярный; рентгеновский;
механические повреждения поверхности – ультразвуковой; визуально-оптический;
растрескивание и межкристаллитная коррозия – токовихревой; ультразвуковой; капиллярный; рентгеновский;
флокены в изломе – магнитный; токовихревой; ультразвуковой.
Согласно данным Шестопаловой Л. П., Лихачевой Т. Е. для исследования изломов применяют как традиционные методы макро- и микроанализа, так и методы физического металловедения с использованием сложнейшего электронно-вакуумного оборудования. Значительное развитие получили методы количественного автоматического исследования изломов с использованием компьютеров. Эти исследования позволяют дать сравнительную оценку характера разрушения и вида излома, выяснить причины и природу отклонения вида излома от оптимального, определить способы предупреждения этих отклонений.
Известны следующие методы изучения поверхностей разрушения и зон материала, непосредственно примыкающих к излому:
1) макро- и микроскопическая фрактография – изучение поверхности разрушения невооруженным глазом или с применением увеличения до 20—60 раз, а также изучение поверхности излома с применением оптического микроскопа при увеличении от 100 до 1500 раз и электронного микроскопа при увеличении от 20 до 2000 раз и более;
2) непосредственное измерение и фотометрирование геометрии поверхности разрушения, т.е. измерение шероховатости и ориентации элементарных участков на поверхности изломов;
3) измерение твердости, определение химического состава металла и распределения химических элементов с помощью рентгеноспектрального микроанализа;
4) электрохимические, рентгенографические, электроиндукционные, магнитные, микромеханические и другие методы для локального исследования фазового состава, искажений кристаллической решетки, механических и физических свойств материала;
5) анализ микроструктуры с целью определения соответствия материала разрушенной детали заданным требованиям, определения глубины обезуглероженного слоя.
Примерный перечень последовательности действий при проведении фрактографического исследования:
1. Составление схемы разрушения, выявление первичного разрушения; определение на детали места расположения излома, в частности, не совпадает ли место разрушения с зоной действия наибольших напряжений, имеются ли в детали конструктивные концентраторы напряжений, как взаимно расположены концентраторы и место излома, а также очаг излома.
Выявление в изломе металлургических дефектов, очага излома с дефектами, коррозионными, эрозионными и другими видами повреждений.
2. Определение соответствия детали размерным требованиям чертежа.
Наличие признаков механических повреждений поверхности и др.
3. Определение макроориентированности излома относительно направления действия главных напряжений (если они известны).
4. Определение вида и степени макропластической деформации и ее локализации в целом и вблизи излома.
5. Характер разрушения в изломе – пластичный, хрупкий, усталостный, внутризеренный, межзеренный.
6. Определение на поверхности излома достаточно резко разграниченных макроскопически различимых по строению и цвету зон и участков, свидетельствующих о протекании разрушения во времени; различных макроскопических знаков – рубцов, ступенек, усталостных линий и т. д.
7. Выявление на изломе продуктов коррозии, окислов и других, связь их с очагом.
8. Выявление трещин вблизи и вдали от излома, оценка их расположения, количества, направления.
9. Соответствие химического состава и механических свойств техническим условиям.
10. Исследование макро- и микроструктуры, соответствие их данному полуфабрикату сплава, выявление дефектов структуры.
11. Применение методов микроанализа для идентификации неметаллических включений, присутствующих в очаге разрушения; анализа включений, на которых образуются микропоры в вязких изломах, а также сегрегаций по границам зерен и пленочных выделений; изучение состава пленок, образованных в результате коррозии и окисления, и ряда других вопросов.
12. Изучение тонкой дислокационной и фазовой структуры материала для установления их аномалий, возникших в результате эксплуатации оборудования, или процессов при его изготовлении.
13. Определение причины выхода из строя КПО и выдача рекомендаций.
В заключении дается: оценка качества материала (химический состав, макро- и микроструктура, механические свойства); характер разрушения детали; факторы, способствующие разрушению (уровень напряжений или температуры); концентраторы напряжений (риски, отсутствие радиусов перехода, перепад жесткости); качество материала, среда и т. п.
В соответствии с заключением предлагаются рекомендации по устранению преждевременного разрушения деталей или узлов КПО.
Мероприятия по организации консервации, упаковки, хранения, перевозки и т. д.
Согласно ГОСТ 7600—90 требования к упаковке КПО сводятся к следующему:
Упаковка КПО, изготовленного для нужд народного хозяйства, а также их отдельных частей (в случае многоместной отгрузки) и принадлежностей должна производиться в соответствии с требованиями действующих нормативно-технических документов.
Для районов Крайнего Севера и труднодоступных районов тара и упаковка – по ГОСТ 15846—2002 (Продукция, отправляемая в районы Крайнего Севера и приравненные к ним местности. Упаковка, маркировка, транспортирование и хранение).
Упаковка КПО, изготовленного для экспорта, – по ГОСТ 24634—81 (Ящики деревянные для продукции, поставляемой для экспорта. Общие технические условия (с Изменениями N 1—5)).
Применяемый для КПО вид упаковки должен быть указан в технических условиях на конкретные виды КПО и обеспечивать сохранность КПО на период транспортирования и хранения.
Способы крепления КПО, его отдельных частей и принадлежностей в таре должны быть указаны в технических условиях или рабочих чертежах на конкретные виды КПО.
Перед упаковкой КПО должно быть законсервировано. Выбор метода консервации определяется техническими условиями на конкретный вид КПО в соответствии с ГОСТ 9.014—78 (Единая система защиты от коррозии и старения (ЕСЗКС). Временная противокоррозионная защита изделий. Общие требования (С Изменениями N 1—6)) с учетом методов консервации комплектующих изделий, указанных в руководстве по эксплуатации на эти изделия.
Перед упаковкой и транспортированием масло и охлаждающая жидкость должны быть удалены из баков КПО, все подвижные части КПО должны быть приведены в положение, при котором КПО имеет наименьшие габаритные размеры, и закреплены. Элементы крепления подвижных частей и дополнительные опоры, используемые при транспортировании и удаляемые при установке КПО, должны быть окрашены в красный цвет. Схема элементов крепления должна быть приведена в эксплуатационной документации, разработанной в соответствии с требованиями ГОСТ 26583—85 (Система технического обслуживания и ремонта технологического оборудования машиностроительных предприятий. Металлорежущее, кузнечно-прессовое, литейное и деревообрабатывающее оборудование. Порядок разработки и правила составления руководства по эксплуатации и ремонтных документов (с Изменением N 1)).
Согласно ГОСТ 7600—90 требования к транспортированию и хранению КПО сводятся к следующему:
Вид транспорта и условия транспортирования, соответствующие правилам перевозки грузов, действующим на конкретном виде транспорта, должны быть указаны в технических условиях на конкретные виды КПО.
Условия транспортирования в части воздействия климатических факторов – по ГОСТ 15150—69 (Машины, приборы и другие технические изделия. Исполнения для различных климатических районов. Категории, условия эксплуатации, хранения и транспортирования в части воздействия климатических факторов внешней среды (с Изменениями N 1, 2, 3, 4, 5)), в части воздействия механических факторов – по ГОСТ 23170—78 (Упаковка для изделий машиностроения. Общие требования (с Изменениями N 1, 2)).
В эксплуатационной документации на КПО должны быть указаны условия размещения и хранения изделий по ГОСТ 15150—69.
КПО и их части, не упакованные в ящики, следует хранить в крытых складах в сухом месте с учетом требований хранения комплектующих изделий (измерительных, электронных и др.).
Нарушения технологии ремонта КПО
Нарушениями в организационо-распорядительной работе при осуществлении ремонта силами владельца являются: (несвоевременная и непроводящаяся в установленном эксплуатационными документами порядке диагностика технического состояния КПО; непривлечение для ремонта соответствующих квалифицированных специалистов из сторонних организаций).
Отсутствие квалифицированных кадров для осуществления ремонта КПО, его узлов и т. д.
Мероприятия по устранению нарушений технологии изготовления, термической обработки и т. д. деталей КПО, переданного в ремонт.
Коленчатые валы применяются в механических прессах, в горизонтально-ковочных машинах для перемещения ползунов, в поршневых насосах. Коленчатые валы относятся к классу эксцентриковых валов. Они подразделяются на одно-, двух- и трехколенчатые. У двухколенчатых валов кривошипные шейки расположены под углом 180°, а у трехколенчатых – под углом 120° друг к другу.
При работе в коленчатых валах возникают сложные напряжения. Коленчатые валы изготовляют из сталей марок 35, 40, 45,35Г2, 45Г2. Коренные и шатунные шейки должны обладать достаточной износостойкостью, и поэтому их подвергают поверхностной закалке на глубину 3—5 мм до твердости Rс = 48—58, а у сталей 45 и 50 до Rс = 50—62. Галтели закалке не подвергаются.
Для сильно напряженных валов применяются легированные стали 40ХН, ЗОХМА.
После механической обработки коленчатые валы должны удовлетворять следующим техническим условиям:
1. Оси коренных и шатунных шеек должны иметь параллельность между собой с отклонением в пределах 0,1 мм на 1 м длины.
2. Точность исполнения размеров коренных и шатунных шеек должна находиться в пределах 2 и 3 класса, эллиптичность и конусность их не должна быть более 0,02—0,05 мм.
3. Точность разворота колен должна быть выдержана в пределах 15 минут.
4. Допуски на несопрягаемые диаметральные размеры выполняются по 5 классу, а на линейные – по 7 классу точности.
5. Шатунные и коренные шейки и их галтели должны иметь чистоту 9 класса для диаметров до 80 мм и 8 класса для диаметров свыше 80 мм.
6. Быстроходные валы должны быть динамически уравновешены.
Коленчатые валы в процессе изготовления после каждой операции подвергаются проверке. Проверка начинается с выяснения соответствия геометрических размеров заготовки, правильности распределения припусков, отсутствия внешних пороков раковин, волосовин, заковов и т. д.
После прорезки шатунных шеек производят проверку механических свойств металла. После каждой операции на контрольных пунктах проверяют геометрические размеры и чистоту поверхности. Проверка производится на плите с использованием установочных призм, шаблонов и т. д.
После окончания обработки вал поступает на окончательный контроль, при котором проверяют все геометрические размеры, обозначенные на чертеже, чистоту посадочных мест, соответствие прочим техническим условиям, указанным на чертеже, и соответствие ГОСТ и др. НТД.
После окончания осмотра производится клеймение на месте, указанном конструктором на чертеже. Коленчатый вал является ответственной деталью, и на его приемку обычно составляют паспорт, где указываются основные данные приемки.
В зависимости от типа производства характер оснащения операций контроля будет различным. При мелкосерийном производстве ограничиваются применением нормального мерительного инструмента и типовых установочных устройств; при крупносерийном производстве большинство операций контроля производится специальными установочными приспособлениями, а мерительный инструмент также специализирован.
Ползуны в кузнечно-прессовых машинах служат для направления рабочих органов при возвратно-поступательном перемещении, например, в кривошипных прессах, винтовых прессах, насосах гидропрессов. В гидравлических прессах роль ползунов играют поперечины. Ползуны обычно изготавливаются из стали 45 с твердостью HB 163—262.
Заготовки для ползунов небольших размеров – поковки, для больших – стальные отливки. Ползуны с относительно небольшой нагрузкой изготавливают из серого чугуна.
Технические условия на изготовление ползунов:
непараллельность направляющих поверхностей в пределах 0,1 мм на длине 1000 мм;
чистота обработки направляющих поверхностей 6—7, остальных 4—5 класса;
посадочные места выполняются по 2 и 3 классу точности.
После выполнения каждой отдельной операции ползуны проходят проверку в соответствии с технологией их изготовления, а по окончании всех операций производится контроль ползуна по техническим условиям, указанным на чертеже. Проверяются прямолинейность, плоскостность, перпендикулярность, геометрические размеры основных базовых плоскостей и основных отверстий, а некоторых случаях соосность осевых отверстий и их параллельность, а также чистота обработки.
Проверка прямолинейности производится при помощи уровня и поверочной линейки. Взаимное расположение поверхностей определяется при помощи угломеров, шаблонов или фасонных плит.
Диаметральные размеры, овальность и конусность проверяются предельными калибрами и нутромерами. Соосность отверстий проверяется при помощи гладких или ступенчатых оправок, выполненных по посадке С или С1, свободно проходящих через соосно расположенные отверстия. Проверка параллельности осей и их межосевых расстояний проводится с помощью контрольных оправок, вставленных в отверстия. При точности измерения до 0,02 мм расстояние между оправками измеряется микрометрическими или индикаторными приборами, при точности свыше 0,05 мм – непосредственно штангенциркулем.
Чистота обработки ползуна до 8 класса проверяется сравнением эталонами, а свыше – профилометром.
От точности изготовления направляющих зависит точность работы пресса.
Направляющие могут быть выполнены за одно целое со станиной или в виде сменных планок, которые при ремонте легко заменяются новыми. Сменные направляющие могут быть нерегулируемыми и регулируемыми. Регулирование производится с помощью перемещающегося клина. Регулируемые направляющие имеют большое преимущество перед нерегулируемыми, так как у них можно изменять зазоры в случае неточности обработки или при износе.
Размеры направляющих зависят от мощности пресса и колеблются по ширине в пределах 100—300 мм и по длине в пределах 300—900 мм. Направляющие изготовляются из углеродистых сталей с твердостью НB 180—220. Направляющие простой формы изготавливаются из поковок, а направляющие сложной конфигурации и значительной длины – из стальных отливок.
Разметку заготовки направляющей в серийном и крупносерийном производстве производят с помощью разметочных шаблонов, в единичном – при помощи универсального инструмента.
Черновая обработка всех поверхностей, подлежащих обработке, может быть произведена на продольно-строгальных, продольно-фрезерных, вертикально-фрезерных, горизонтально-фрезерных станках. В серийном производстве на продольно-строгальных и продольно-фрезерных станках одновременно обрабатывают несколько деталей с использованием двух-трех суппортов.
Чистовая обработка плоскостей направляющих с оставлением припуска под отделочную обработку (шлифование или шабрение при сборке) выполняется на строгальных или фрезерных станках.
Величина припуска под отделочную обработку зависит от размеров детали.
Обработка всех крепежных отверстий, нарезка резьбы, сверление отверстий под смазку выполняются в единичном производстве по разметке, а в серийном – по кондукторам. Если отверстия – расположены в разных плоскостях, то для сокращения времени переустановку детали применяются поворотные приспособления. Фрезерование смазочных канавок на направляющих выполняется по разметке или по шаблонам на вертикально- или горизонтально-фрезерных станках фрезами, профиль которых соответствует профилю смазочных канавок. Отделочная обработка плоских поверхностей трения заключается в шлифовании или тонком строгании, реже в тонком фрезеровании. При тонком строгании или фрезеровании оставляется припуск не свыше 0,05 мм для взаимного пришабривания направляющей и сопрягаемой детали при сборке. Обработка параллельно расположенных плоскостей выполняется на фрезерном станке набором фрез или на строгальном набором фасонных резцов, закрепленных в одной державке; расстояние между режущими кромками фрез или резцов соответствует величине шага. Установка их производится по шаблону на просвет.
Назначение подштамповой плиты, или, иначе, штамподержателя, в различных видах КПО – удерживать нижнюю половину штампа. Верхняя половина штампа крепится к нижней части ползуна (у кривошипных прессов).
Подштамповые плиты изготовляются из хромистой стали 40Х и углеродистой стали 50. Поковки не должны иметь на поверхности дефектов: волосовин, закатов, плен, трещин. Перед механической обработкой их подвергают отжигу.
Механическая обработка штамподержателя производится в следующей последовательности. Сначала производят обдирку с поверхностей с оставлением припуска 5 —10 мм на последующую обработку; торцовые поверхности, не подвергающиеся дальнейшей обработке, обрабатываются в окончательный размер. После обдирочной операции заготовки подвергают термической обработке: закалке и отпуску до твердости НB 269—321 для верхней и НB 207 для нижней опорной части. Затем заготовки обрабатывают на продольно-строгальных или на продольно-фрезерных станках. Сначала обрабатывают поверхности, непосредственно соприкасающиеся с нижней частью штампа, после этого заготовку переустанавливают и обрабатывают основание подштамповой плиты с соблюдением требований к параллельности поверхностей в пределах ±0,15 мм на 500 мм длины. Затем обрабатывают в размер торцовые плоскости подштамповой плиты с допустимой погрешностью по углу ±5 минут и с оставлением припуска на дальнейшую обработку плоскостей под Т-образные пазы, причем эти плоскости должны быть параллельны нижней плоскости подштамповой плиты. Последняя операция механической обработки штамподержателя – сверление двух отверстий диаметром 20—40 мм и глубиной 50—100 мм на торцовых частях для удобства транспортировки и монтажа подштамповой плиты.
После окончания механической обработки на подштамповой плите наносят осевые линии О – О и О (1) – О (1) в двух взаимно перпендикулярных направлениях. Они необходимы для правильной установки штамподержателя на станину пресса.
Нарушения технологии и требований к сборке КПО.
Согласно ГОСТ 7600—90 при сборке машин или сборочных единиц не допускается установка на стыках прокладок, не предусмотренных рабочими чертежами.
Между обработанными сопряженными поверхностями деталей неподвижных соединений, определяющих точность кузнечно-прессовых машин (КПМ), не должен проходить щуп толщиной более указанной ниже, если более высокие требования не установлены к качеству соединяемых поверхностей.