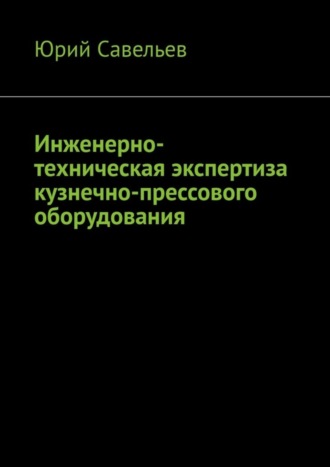
Полная версия
Инженерно-техническая экспертиза кузнечно-прессового оборудования
Эксперт должен иметь определенную квалификацию и желательно значительный стаж работы, уметь хорошо ориентироваться в конструкции, технологии и метрологическом обеспечении разработки, производства и испытаний изделия. Он должен давать квалифицированное заключение по результатам экспертизы, конкретные рекомендации разработчикам изделия, эксплуатационно-ремонтному, производственному персоналу по устранению метрологических, конструкторских, технологических ошибок, не ограничиваясь критическими замечаниями.
Все это выдвигает особые требования к эксперту, который должен быть квалифицированным специалистом не только в машиностроительной, электротехнической областях, но также в областях, содержание которых отражается в подвергаемой экспертизе документации, договорам на покупку и ремонт КПО, различной технологической документации.
Анализ выработки ресурса и аварий КПО
Эксплуатация КПО
Планово-предупредительное обслуживание КПО
Надежность – это свойство объекта сохранять во времени в установленных пределах значения всех параметров, характеризующих способность выполнять требуемые функции в заданных режимах и условиях эксплуатации.
Согласно данным Платонова Г. Н. и других источников кузнечно-прессовое оборудование относится к восстанавливаемому оборудованию и поэтому его надежность характеризуется долговечностью, безотказностью, ремонтопригодностью и сохраняемостью.
Под восстанавливаемым изделием понимается изделие, для которого после любого из возможных отказов предусматривается проведение ремонта, в отличие от невосстанавливаемого изделия, для которого проведение ремонта не предусматривается.
Долговечность – свойство объекта сохранять работоспособное состояние до наступления предельного состояния в течение некоторого времени или наработки.
Предельные состояния в целом КПО и узлов следующие:
списание в лом;
капитальный ремонт.
Предельное состояние деталей определяется предельно-допустимыми при эксплуатации отклонениями их размеров ‚ являющимися суммой отклонений, полученных при изготовлении деталей и их износа в процессе эксплуатации.
Предельное состояние соединений деталей определяется предельно-допустимой величиной зазора, являющейся суммой величин зазора, полученного при изготовлении и его увеличении вследствие износа деталей.
После достижения деталями предельных состояний они заменяются новыми или ремонтируются.
Безотказность – свойство объекта непрерывно сохранять работоспособное состояние в течение некоторого времени или наработки. Потеря работоспособности происходит в результате отказа.
Под наработкой понимается продолжительность или объем работы изделия (часы, циклы).
Отказ – нарушение работоспособности технического изделия.
Поскольку для кузнечно-прессового и металлообрабатывающего оборудования обязательно применение системы планово-предупредительных ремонтов (ППР) и технического обслуживания под отказом следует понимать потерю работоспособности в периоды между запланированными периодами технического обслуживания и плановыми ремонтами.
Признаки (критерии) отказов согласно ГОСТ 27.002—2015 (Надежность в технике (ССНТ). Термины и определения) должны оговариваться в технической документации на изделия данного типа. Правильный выбор признака (критерия) отказа чрезвычайно важен. Поставщик оборудования, как правило, не несет ответственности за отказы, происходящие в результате нарушений регламентированных правил эксплуатации, за отказы, являющиеся следствием брака заготовок, изготовляемых вне комплекса, и другие отказы, не зависящие от качества поставляемого оборудования.
Ремонтопригодность – свойство объекта, заключающееся в приспособленности к предупреждению и обнаружению причин возникновения отказов, повреждений и поддержанию и восстановлению работоспособного состояния путем проведения технического обслуживания и ремонтов.
Сохраняемость – свойство объекта сохранять значения показателей безотказности, долговечности и ремонтопригодности в течение и после хранения и транспортирования.
Для расчета и оценки показателей надежности КПО принимается следующая модель утраты и восстановления работоспособности и исправности.
Период работы оборудования от начала эксплуатации до капитального ремонта называется ремонтным циклом. Календарная продолжительность ремонтного цикла измеряется в годах и называется сроком службы до капитального ремонта. Наработка в часах за этот срок службы называется ресурсом до капитального ремонта.
В ГОСТ 7600—90 (Оборудование кузнечно-прессовое. Общие технические условия (с Изменением N 1)) установлены средние значения ресурса или сроков службы.
Ремонтный цикл включает в себя заданное количество средних и текущих ремонтов, проводимых через установленные сроки службы или наработку в часах. Чередование этих ремонтов составляет структуру ремонтного цикла.
Между текущими или текущим и средним ремонтом должно проводиться техническое обслуживание (ТО), которое заключается в проведении регулировок механизмов, промывке и очистке оборудования, смазке, планово-предупредительной замене быстроизнашивающихся деталей. НПО «ЭНИКМАШ» рекомендуются следующие виды планового ТО: ежедневное (заявочное), первое, второе и третье плановые ТО, проводимые соответственно еженедельно, ежемесячно и ежеквартально.
Важнейшей задачей ТО является предупреждение зарождающихся отказов. Однако некоторые виды отказов предупредить заранее невозможно и они случаются во время работы оборудования. Для устранения отказов проводятся внеплановые ежесменное ТО и ремонты.
С целью более полного использования фонда рабочего времени оборудования системой ППР предусмотрено проведение планового ТО в незапланированное для работы время (третья смена, выходные дни, специальные перерывы в работе).
Наиболее предпочтительным режимом работы считается двухсменная работа КПО. При этом плановое техническое обслуживание как правило проводится в третьей смене.
Система ТО является одним из важнейших факторов, оказывающих влияние на надежность и производительность КПО, и поэтому при разработке и согласовании технического задания с заказчиком КПО должны быть согласованы режим работы и система технического обслуживания.
Согласно данным Анисимова М. И., Кудинова О. В., Украинцева Б. П. срок службы быстроизнашивающихся деталей составляет:
для пресса механического:
накладка тормозной ленты; пружина кулака поворотной шпонки; поворотная шпонка; хвостовик рабочей шпонки – 4—5 месяцев;
кулачок рабочей шпонки; пружина тормоза – 6 месяцев;
автомат включения; втулка включения (маховик) – 1 год;
втулка станины; втулка шатуна – 18 месяцев;
муфта эксцентрика; эксцентриковый шкив; тормоз – 2—2,5 года;
для пресса гидравлического:
манжета поршня рабочего хода – 6 месяцев;
манжета поршня обратного хода – 3 месяца;
штуцер цилиндра выталкивателя – 6 месяцев;
штуцер главного цилиндра; штуцер поддерживающего цилиндра клапана – 6 месяцев.
Номенклатура и ориентировочный срок службы запасных деталей кривошипных прессов простого действия с пневматической муфтой включения и пневматическим тормозом:
кривошипный вал (Сталь 45, 40Х; HB≥230) – от 2 до 5 лет в зависимости от первоначального зазора в опорах скольжения;
эксцентрик регулировки величины хода ползуна (Сталь 45; HB≥230) – от 2 до 5 лет;
ступица муфты включения (Сталь 45; HRC 40—50 поверхности зубьев) – до 5 лет;
ступица тормоза (Сталь 45; HRC 40—50 поверхности зубьев) – до 5 лет;
зубчатый венец муфты включения (Сталь 45; HRC 40—50 поверхности зубьев) – до 5 лет;
зубчатое колесо привода пресса (Сталь или чугун; HRC 40—50) – до 5 лет;
шестерня (Сталь 45; HRC 40—50) – до 5 лет;
червяк механизма регулировки закрытой высоты (Сталь 45; HB≥230) – от 5 до 15 лет в зависимости от характера производства;
червячное колесо механизма регулировки (чугун или бронза; -) – от 5 до 15 лет в зависимости от характера производства.
Эксплуатационные наблюдения за нарушениями при работе КПО.
Эксплуатационные испытания (наблюдения) входят в комплекс испытаний, проводимых производителями и эксплуатирующими КПО предприятиями с целью обеспечения высокого качества, в том числе надежности прессов.
Изучение надежности КПО в эксплуатации проводится
в следующих трех направлениях:
1.Эксплуатационные испытания надежности прессов данной модели, выпущенных производителем КПО:
а) выявление дефектов пресса, снижающих его надежность (повышенный износ, поломки деталей, нарушение регулировки);
6) определение фактических сроков службы основных деталей пресса, а также наименее долговечных деталей;
в) определение скорости (или интенсивности) изнашивания основных наиболее изнашиваемых деталей;
г) установление причин повышенного износа и поломок деталей;
д) оценка влияния износа деталей на точность пресса;
в) оценка фактической эффективности отдельных мероприятий, направленных на повышение надежности прессов;
ж) определение фактических сроков службы прессов до ремонта;
з) выявление элементов и узлов, для которых необходимы специальные испытания на надежность;
и) уточнение требований (технических условий) к конструкции и изготовлению деталей, уточнение инструкций по уходу и обслуживанию прессов;
к) определение изменения точности (в том числе жесткости) пресса во времени в процессе эксплуатации;
л) определение показателей надежности прессов.
2. Изучение и обобщение опыта заводов по эксплуатации и ремонту прессов.
Сбор и систематическая обработка информации о надежности прессов, поступающей в результате кратковременных обследований прессов сотрудниками испытательных групп, а также в отдельных случаях в виде ответов заводов-потребителей на запросы предприятий, эксплуатирующих КПО.
3. Контрольные эксплуатационные испытания прессов.
Целесообразно ежегодно проводить контрольную эксплуатацию (сроком примерно на один-два года) нескольких прессов из текущей продукции завода. Основные наиболее изнашиваемые детали предварительно измеряются, фиксируется геометрическая точность пресса. За КПО ведется постоянное наблюдение.
Цель проводимых испытаний – определить фактический уровень качества (в том числе надежности прессов) и дать оценку эффективности новых конструктивных и технологических решений, направленных на повышение надежности прессов.
Сочетание информации, получаемой от потребителей, с результатами эксплуатационных наблюдений за группами (выборками) прессов на заводах обеспечивает достоверность информации и выводов.
Анализ поломок и аварий КПО
Методология диагностики причин разрушения деталей и узлов оборудования представлена в работах таких авторов, как: Чижмаков М. Б., Шапиро М. Б., Белинкий А. Л., Лапидус А. С., Марголин Л. В., Портман В. Т., Пратусевич Р. М. и др.
Согласно существующих в технической литературе описаний физико-химических методов исследования и их возможностей применительно к анализу разрушений основного металла и сварных соединений, направление исследования и выбор методов определяется особенностью разрушения материала и условиями эксплуатации оборудования.
Начинать исследование необходимо с визуального осмотра поврежденного узла КПО,– это требуется для определения участков с очагом разрушения коррозионного поражения, трещин, последовательности этапов разрушения и др. В большинстве случаев приходится определять химический состав стали и его соответствие ГОСТу, при этом следует обращать внимание на содержание в стали вредных примесей и газов. Проверка прочностных и пластических характеристик металла необходима для установления соответствия свойств нормам технических условий. При контроле механических свойств важно оценить их однородность в различных участках разрушенной детали в различных сечениях (в сердцевине и в поверхностных слоях детали).
Во многих случаях полезно определять в материале уровень остаточных напряжений, опасных при коррозионном растрескивании, коррозионной усталости и сложнонапряженном состоянии, их характер, в частности, важно оценить уровень и распределение растягивающих напряжений.
Кроме того, можно провести цветную дефектоскопию разрушенных деталей и узлов КПО (для немагнитных материалов можно применять метод люминисцентной дефектоскопии). Дефектоскопия позволяет установить наличие в металле трещин и характер их расположения в детали, а также в ряде случаев получить важные сведения об особенностях повреждения металла. Кроме того, дефектоскопия металла необходима в тех случаях, когда основной излом детали испорчен или поврежден в результате контакта с другими кусками металла и с агрессивной средой; в этом случае определенную информацию о характере разрушения можно получить по дополнительным трещинам.
Металлографическое исследование структуры детали или поврежденного узла дает ценную информацию о металле. Так, в процессе эксплуатации металла могут происходить существенные изменения в структуре, вызванные наклепом металла, рекристаллизационными процессами.
На поверхности деталей могут образовываться слои, обедненные или обогащенные рядом элементов, что, естественно, должно отразиться на особенностях структуры металла.
Контроль изменений в структуре металла детали или узла после эксплуатации по сравнению с исходной позволяет оценить, в какой мере эти изменения структуры могли вызвать повреждение материала при эксплуатации. Кроме того, анализ микроструктуры дает информацию о дефектах металлургического характера (например, крупных неметаллических включениях, строчечных выделениях, наличии феррита в аустенитной фазе); дефектах сварного соединения и других, а также их возможном влиянии на разрушение деталей и узлов КПО. Металлографически можно также выявлять дефекты сварных швов изделий. Описанные методы исследования металлов детально изложены во многих работах и широко применяются в ряде металловедческих лабораторий НИИ и заводов различных отраслей промышленности.
Иногда проведение анализа аварийного металла с помощью этих методов позволяет выяснить причину разрушения.
Изучение причин поломок и других повреждений деталей КПО состоит из следующих трех этапов:
выявление разрушений;
изучение и фиксирование условий разрушения;
установление причин разрушений.
Выявление причин и изучение условий поломок пресса начинается на месте возникновения разрушения. В ряде случаев собранной информации оказывается достаточно для установления действительной причины повреждения. Однако в большинстве случаев приходится проводить дополнительные исследования: лабораторный анализ деталей, уточненные расчеты на прочность специализированные испытания и т. д.
Выявление разрушений
Поломки и другие повреждения деталей и узлов обследуемого КПО выявляются при авариях, текущем техническом обслуживании пресса, предупредительных осмотрах и разборках механизмов, а также при появлении признаков ненормальной работы пресса.
Повреждение можно обнаружить по двум признакам:
либо непосредственно по прекращению работы механизма пресса, либо по косвенным показателям: повышению шума, появлению ударов, вибрации, течи, повышению температуры узла, отказу органов управления, ухудшению качества обрабатываемых изделий, появлению брака и т. д.
Установив поломку или ненормальную работу, необходимо по возможности определить конкретную деталь и узел, вызвавшие неисправность или аварию пресса.
Работа по выявлению поломок и установлению причин разрушений предъявляет высокие требования к квалификации персонала, который должен знать наблюдаемые прессы; слабые места и типичные неисправности механизмов.
Изучение и фиксирование условий разрушения
Изучение условий поломок включает опрос персонала, обслуживающего пресс (рабочий-штамповщик, сменный мастер, механик цеха и т.д.), а также лиц, присутствовавших при аварии; тщательный осмотр и исследование характерных особенностей разрушенных и поврежденных деталей; установление общей продолжительности работы пресса с начала эксплуатации, номенклатуры обрабатываемых деталей и характерных режимов обработки. Особое внимание обращается на перегрузочные режимы и режим обработки при возникновении аварии. Проводятся также необходимые измерения и проверки: зазоров в зубчатых передачах и шлицевых соединениях, муфте, тормозе; проверяется качество изготовления отдельных деталей, температура узла, регулировки механизмов и т. д. В случае необходимости производится полная разборка поврежденного узла КПО.
Если результаты проведенного исследования позволяют установить причину поломки и повреждений, то составляется технически точное объективное описание разрушения, в котором приводится предполагаемая причина разрушения и дается предварительное заключение. Если причину поломки не удалось выяснить – необходимо более основательно исследовать разрушенную деталь, провести дополнительные лабораторные измерения, исследования (металлографические, химические) и испытания, а также рекомендуется использовать результаты расчетов на прочность и данные испытаний опытных образцов КПО изучаемой модели.
К описанию разрушения рекомендуется прилагать эскиз и фотографию излома или поврежденного участка детали, а в необходимых случаях – схему расположения обломков и повреждений в механизме.
При поломках и повреждениях деталей, требующих разборки узла и замены разрушенных элементов новыми, разрушенные детали сохраняются с бирками, на которых должно быть указано наименование детали, модель и инвентарный номер КПО, дата аварии; предполагаемая причина и номер документа, в котором зафиксированы подробные сведения об аварии. В дальнейшем эти детали осматриваются представителями завода-изготовителя и в случае необходимости подвергаются дополнительным лабораторным исследованиям.
Для определения первоначально разрушившейся детали, последовательности повреждения других деталей и выявления причин разрушения важное значение имеет анализ обнаруженных изломов и повреждений. В связи с этим повреждения и дефекты деталей исследуемого механизма необходимо разделить на две группы. К первой группе относятся повреждения, возникшие при изготовлении или эксплуатации КПО до аварии: износ рабочих поверхностей, следы контактной коррозии, забоины и т. п. Изучение этих повреждений облегчит определение непосредственных причин поломок. Ко второй группе – повреждения, возникшие при разрушения деталей. Анализ повреждений этой группы позволит восстановить ход процесса разрушения.
Изучение строения излома позволяет определить вид разрушения, получить дополнительные данные об условиях нагружения, оценить концентраторы напряжений, снижающие сопротивление детали разрушению.
Для установления вида разрушения важно определить характер излома. Признаками усталостного излома являются характерные зоны, линии и ступеньки на поверхности излома, блеск и мелкозернистая структура этой поверхности, зигзагообразные трещины на участках разрушенной детали или аналогичных деталях механизма, а также определенный срок службы детали до разрушения (не менее десятков тысяч нагружений, а чаще – сотни тысяч и миллионы циклов).
Характер и величину нагрузок определяют по расположению поверхности излома относительно действующих сил и контура детали, расположению и количеству различных зон на поверхности излома и т. п. Например, при скручивании вала от действия однократной перегрузки большой величины или от крутильных колебаний большой амплитуды поверхность излома располагается под углом 90° к оси вала. При развитии усталостного разрушения от длительного действия циклических перегрузок небольшой величины поверхность излома направлена либо под углом 45° к оси вала, либо частично параллельно оси вала и частично под углом 45°. При наличии на поверхности вала источников концентрации напряжений, расположенных перпендикулярно оси (например шлицевых, шпоночных соединений, резьбы), трещина может развиваться также перпендикулярно поверхности вала даже при действии‚ незначительных перегрузок. При анализе изломов необходимо учитывать, что перегрузка, вызвавшая усталостное разрушение, тем выше, чем большую площадь усталостного излома занимает доломленная зона и чем ближе к центру она смещена; чем больше в изломе ступенек и рубцов; чем дальше они расположены друг от друга; чем меньше выражены притертость и блеск поверхности излома.
Концентраторы напряжений обнаруживаются обычно в очаге разрушения или в местах изменения направления развития трещины.
Фокус излома располагается в зоне концентраторов, связанных с резким изменением контура детали (например дно кольцевой выточки или резьбы вала, основание шлицев и зубьев шестерен и т.д.), с плохим качеством поверхности (следы грубой обработки, шлифовочные трещины и ожоги, забоины, коррозионные раковины и т.д.). Иногда повреждение развивается из начальных (зародышевых) дефектов материала: раковин, волосовин, флокенов, включений.
При оценке влияния концентратора напряжений на разрушение необходимо иметь в виду, что он является обычно фактором, способствующим разрушению, но не всегда единственным и главным. Сопоставляя случаи поломки аналогичных деталей, иногда можно выяснить степень влияния концентратора напряжений и других факторов на возникновение излома.
Установление причин разрушения деталей КПО
После того, как определен вид разрушения и выявлены характерные обстоятельства поломки, на основе обобщения всей собранной информации устанавливаются причины разрушений.
Разрушение деталей объясняется, с одной стороны, неполнотой и неточностью данных о нагрузках, с другой – отклонением фактической прочности деталей от расчетных значений под влиянием различных факторов, недостаточно учитываемых при проектировании. Причины снижения прочности могут быть связаны с конструкцией и расчетом, технологией изготовления, эксплуатацией и ремонтом как самих деталей, так и механизма пресса, в состав которого входят эти детали. Классификация причин по признаку этапов создания и эксплуатации КПО облегчает накопление и систематизацию данных о поломках, определяет направление работ по устранению дефектов и повышению надежности КПО. В конечном счете действие различных причин приводит к возникновению дополнительных усилий, концентраций напряжений, неблагоприятному распределению остаточных (внутренних) напряжений, снижению механических свойств материала и искажению геометрической формы детали, ослабляющим опасное сечение.
При отнесении причины разрушения к той или иной группе или подгруппе следует иметь в виду возможность совместного действия и взаимозависимость различных причин. Поэтому предлагаемая классификация является условной и в зависимости от конкретных обстоятельств может быть уточнена. Поскольку невозможно установить общие правила определения истинных причин аварий по предварительно собранным данным о разрушениях, ниже приводится ряд характерных примеров поломок деталей прессов и причин их возникновения.
1. Конструкционные причины связаны с недостатками конструкции КПО, отдельного механизма или детали, а также с неправильным выбором материала детали и способа ее упрочнения:
а) расположение геометрических концентраторов напряжений и ослабление сечения на наиболее нагруженных участках детали – поломки главного вала (шатунная шейка); разрушение тела маховика, установленного на главный вал (коленчатый или другой в зависимости от конструкции пресса) по шпоночному пазу;
б) неправильный выбор материала и способа упрочняющей термообработки, приводящий к несоответствию прочности или износостойкости детали условиям ее нагружения – поломки главных валов КПО, изготовленных из стали 40Х.
в) использование в проектировочных расчетах характеристик прочности материала деталей, полученных по результатам стандартных испытаний образцов, а не соответствующих характеристик реальных деталей, выявленных при натурных испытаниях.
2. Технологические причины связаны с несовершенством принятых технологических процессов и с недостатками изготовления и монтажа деталей и узлов:
а) дефекты материала, нерациональные схемы и режимы термообработки, ведущие к невыполнению заданных при проектировании технических условий и т.д.; поломки кронштейнов и корпусных деталей КПО из-за дефектов литья; поломки «по телу» крепежных соединений узлов прессов (муфта): шпильки, болты и т.д., не прошедших термообработки; поломки пружин из катанки, прутка в конструкциях муфт некоторых прессов из-за попадания на обработку деталей холодно- или горячедеформированным способом без предварительной и последующей термообработки;