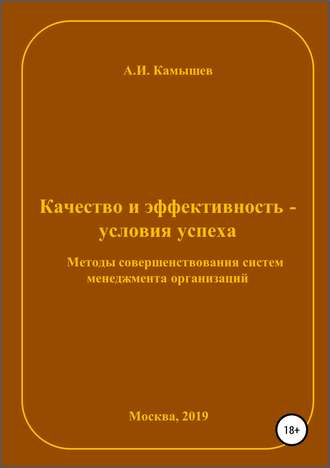
Полная версия
Качество и эффективность – условия успеха. Методы совершенствования систем менеджмента организаций
Другой вопрос – почему совершенствованием нужно заниматься постоянно? Нельзя ли, хорошенько подумав, сразу сделать совершенный процесс? И каким представляется совершенный процесс?
Очевидно, что совершенный процесс – это не наилучшее достижение конкурента, хотя и его нужно принимать во внимание.Совершенный процесс – это идеальная модель процесса создания ценности продукта, к которой следует стремиться, хотя она может казаться недостижимой [4].
В самом начале и периодически в дальнейшем, необходимо заново вырабатывать видение совершенного процесса. Как только поток создания ценности продукта будет улучшен, надо формировать новое видение совершенного процесса. И не только потому, что процесс изменился изнутри и открылись новые возможности для его улучшения, но и потому, что изменились внешние условия и потребности.
1.1.3. Внедрение Бережливого производства
Психологически самое сложное – это начать двигаться по пути преобразований, преодолевая инерцию, свойственную любому предприятию. Для начала движения необходимы следующие условия [4]:
• назначение Уполномоченного по Бережливому производству;
• обладание знаниями о принципах и методах построения Бережливого производства;
• возникновение сложной ситуации в бизнесе организации, вынуждающей ее к проведению преобразований.
Функции Уполномоченного по Бережливому производству может взять на себя руководитель организации, если это небольшая или средняя по размеру организация. В крупной организации Уполномоченным по Бережливому производству целесообразно назначить исполнительного директора или другое должностное лицо, руководящее производством. Уполномоченному нужна группа (команда) помощников – экспертов, работающих в данной организации, и внешних консультантов.
Для успеха дела необходимо, чтобы руководитель организации, Уполномоченный по Бережливому производству и другие высшие руководители прониклись идеями Бережливого производства. Необходимо также, чтобы они принимали личное участие в мероприятиях по улучшениям.
Знаниями о принципах и методах построения Бережливого производства должен обладать весь персонал, принимающий участие в преобразованиях. Эти знания они могут получить с помощью учебно-консалтинговых организаций и собственных специалистов. Практические знания можно получить в организациях, уже внедривших Бережливое производство.
Состояние кризиса и упадка – это самое подходящее время для начала преобразований. Как правило, именно в этом состоянии организации быстро и решительно начинают переход к Бережливому производству. Переход к Бережливому производству не требует больших затрат, хотя желаемый результат не может быть получен мгновенно. Пройдет, примерно, от полугода до года, прежде чем организация сможет устранить потери в процессах разработки, продаж, планирования и производства продукции, и обнаружит, что ее перспективы значительно улучшились.
Преобразование структуры предприятияПолучив положительные результаты в нескольких критических областях деятельности организации, руководству нужно разработать стратегию по дальнейшим преобразованиям.
При этом в число новых задач целесообразно включить [4]:
• создание новой организационной структуры предприятия, ориентированной на семейства выпускаемых продуктов;
• создание специального отдела обучения и консалтинга по Качеству и Бережливому производству;
• разработку и реализацию кадровой политики по перераспределению персонала.
Создание новой организационной структуры предприятия должно быть подчинено главной цели – организации экономичного потока создания ценности продукции до ее потребителя. Это можно сделать путем группирования персонала вокруг семейств выпускаемых продуктов, например, так как показано на рис. 1–2.
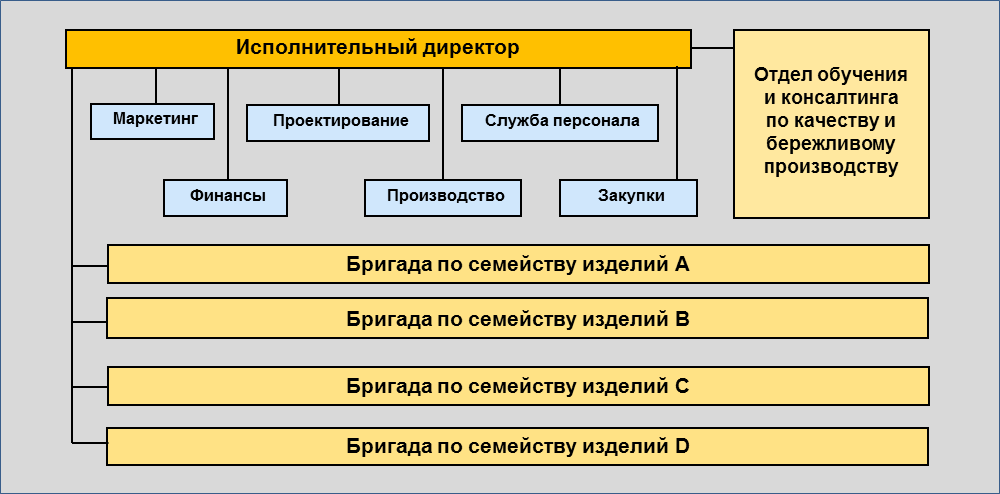
Рис. 1–2. Пример построения структуры организации, внедрившей бережливое производство
Ключевое место в структуре занимают бригады, обеспечивающие выполнение всего комплекса операций по выпуску определенных семейств изделий, включая функции маркетинга и продаж, разработки продукции, планирования, производства и закупок. В таких бригадах можно оперативно решать все вопросы взаимодействия специалистов различного профиля на основе достижения общей цели – выпуска продукции нужного качества, в нужные сроки, с минимальными потерями.
В таких комплексных бригадах сосредотачивается большая часть персонала организации. Централизованные функциональные службы занимаются только общими для предприятия вопросами и существенно сокращаются. Соответственно, сокращаются приходящиеся на них накладные расходы.
Создание отдела обучения обусловлено необходимостью обеспечения нужной квалификации персонала, обобщения и передачи опыта, постоянного улучшения системы менеджмента. Целесообразно совместить функции обучения и консультирования по Бережливому производству с функцией обеспечения Качества. В этом случае улучшение качества и повышение производительности, а также сокращение различных потерь будут осуществляться одновременно и согласованно. Работая совместно, специалисты по Качеству и Бережливому производству смогут говорить на одном языке и давать советы, не противоречащие друг другу.
Разработка и реализация кадровой политики необходима для своевременного перераспределения высвобождающегося персонала. При внедрении Бережливого производства выработка на каждого человека увеличивается, примерно, вдвое. Организации нужно либо вдвое увеличить объем выпускаемой продукции (если есть рыночная потребность), либо освоить выпуск новой продукции, либо взять на себя дополнительные функции по обслуживанию и дистрибьюции продукции, по выполнению части функций, выполняемых поставщиками. Важно, чтобы персонал понимал, что внедрение Бережливого производства необходимо для выживания, последующего развития и процветания организации, что каждому сотруднику, желающему остаться в организации, будет найдено место в новых условиях. Только в этом случае сотрудники станут активными участниками внедрения Бережливого производства.
1.1.4. Итоговая оценка
Ключевые особенности Бережливого производства:
1) Принципы, методы и практика Бережливого производства сфокусированы на создании потребительской ценности продукции – это главная цель деятельности.
2) Создание потребительской ценности продукции осуществляется при минимизации всех видов затрат на всех этапах работ, начиная от создания концепции продукта и кончая его поставкой потребителю.
3) Реальный спрос потребителя на продукцию регулирует объем и время ее производства и поставки.
4) Деятельность по совершенствованию создания и выпуска продукции никогда не останавливается, реагируя на изменения внешней и внутренней среды.
5) Критическое состояние предприятие – подходящее время для внедрения Бережливого производства, т. к. создает условия для решительных действий руководства и изменения менталитета персонала предприятия.
Девиз Бережливого производства [4]: «Стремиться делать только то, что создает ценность, и не делать ничего, что ее не создает».
Оценка научного редактора русского издания «Бережливого производства» Ю. П. Адлера и соавтора [5] В. Л. Шпера: «Идеи и методы <Бережливого производства> могли бы сыграть решающую роль в трансформации российской промышленности и приближении ее к уровню современных развитых стран».
1.2. Развертывание функции качества
1.2.1. Из истории вопроса
1972-ой год. В Японии, г. Кобэ, на судостроительной верфи фирмы «Мицубиси» ведется проектирование нефтеналивного танкера. При проектировании используется диаграмма К. Исикавы [6] (причинно-следственная диаграмма, известная также под называнием «Fishbone», т. е. «Рыбий скелет»). Путем построения диаграммы пытаются определить проектные технические характеристики танкера, благодаря которым должны получиться его желаемые потребительские свойства. Однако эти попытки терпят неудачу. Танкер оказывается слишком сложным объектом, а диаграмма – слишком громоздкой.
Тогда фирма «Мицубиси» использует новый метод, разработанный д-ром Ё. Акао (Yoji Akao), суть которого состоит в создании механизма обеспечения качества продукции еще на стадии ее проектирования[7]. В развитии метода принимает участие д-р С. Мидцуно (Shigeru Mizuno), который разрабатывает таблицу функциональной взаимосвязи потребительских характеристик и технических характеристик будущего изделия. Метод оказывается успешным.
Так, 1972-ой год становится датой практического применения и поворотной в судьбе новой методологии, названной впоследствии «Quality Function Deployment, QFD». На русском языке этот термин означает «Развертывание функции качества, РФК», хотя встречается и другой перевод – «Структурирование функции качества, СФК».
Разработка РФК имеет предисторию [8]. Еще за шесть лет до событий 1972 г. д-р Акао разработал свою концепцию, обучал и вел работы по ее практическому использованию на японских предприятиях. Некоторые из них были довольно успешными, например, на автомобильных фирмах «Hino Motors» и "Toyota Auto Body", но широкую известность они тогда не приобрели.
Важно отметить, что методология РФК возникла не на пустом месте. Ей способствовала общая атмосфера возрождения и подъема японской экономики, разрушенной войной, а также усилия многих специалистов, внесших свой вклад в создание этой методологии. В 50-х в Японии работали и читали лекции американские эксперты Дж. Джуран и Э. Деминг. В 60-х годах страну охватило всеобщее движение за качество. Д-р К. Исикава активно пропагандировал движение от статистического контроля в производстве к «Всеобщему управлению качеством». Происходили и другие события, ставшие вехами в развитии и применении метода РФК (табл. 1–1).
Таблица 1–1. Предпосылки и вехи развития РФК в Японии и США
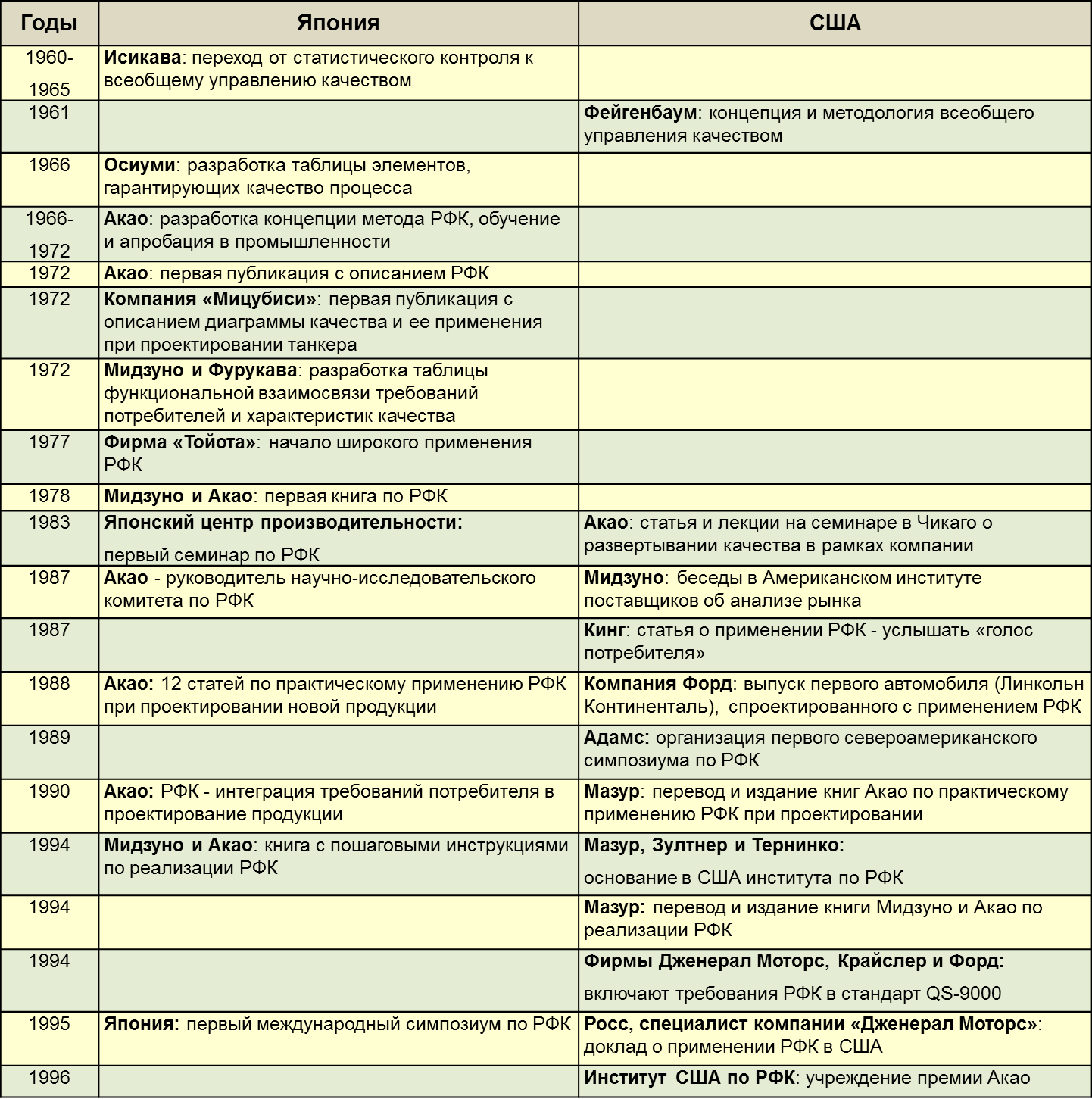
Распространению и внедрению всеобщего управления качеством способствовала монография А. Фейгенбаума [9]. Согласно его философии Total Quality Control (или Total Quality Management, TQM) качество продукции определяется степенью реализации требований клиентов.
В Японии стремление в максимальной степени реализовать требования потребителей становится самым главным. Причем Акао и Мидзуно ставят задачу разработки метода, позволяющего обеспечить удовлетворение требований потребителя еще до того, как продукция будет изготовлена.
Такой подход охватывает не только стадию проектирования, но и производственные процессы, включая организацию контрольных точек в производстве, гарантирующих достижение заданных параметров. Для организации контрольных точек используются таблицы элементов К. Осиуми (Kiyotaka Oshiumi), гарантирующих качество процесса.
С 1977 году метод РФК активно применяет фирма «Тойота», предварительно обучив своих сотрудников. Ее дочерняя компания "Toyota Auto Body" к 1984 г., т. е. в течение 7 лет, выпускает четыре новых модели автофургонов [10]. Обеспечив при этом сокращение времени циклов их разработки и выхода на рынок на 1/3, а сокращение затрат – на 61%.
Вслед за Тойотой РФК начинают применять все ее поставщики и тоже добиваются успеха. Компания «Аисин Варнер», обеспечивающая поставку 98% коробок передач для Тойоты, благодаря РФК вдвое сокращает количество конструкторских изменений в период технологической разработки изделия и вдвое сокращает сроки разработки и освоения производства. В результате Тойота получает возможность быстро выводить на рынок новые марки своих машин.
В 1978 году Мицуно и Акао выпускают первую монографию о своем методе, в которой метод назван «Quality Function Deployment» [11]. Это приводит к быстрому росту применения в Японии нового подхода, в котором все операции компании приводятся в движение "голосом потребителя". Роль потребителя становится доминирующей.
В 1979 году сотрудник фирмы "Toyota Auto Body" Ц. Савада (Tsuneo Sawada) строит диаграмму качества, по форме напоминающую дом с крышей, которая получает название «Дом качества» [12]. Это название оказывается очень популярным и способствует широкому распространению нового метода.
До 1983 года, как это ясно показывает табл. 1–1, американцы почти ничего не знают о разработке в Японии нового метода. В 1985 г. хлынувший на их рынок поток дешевых и надежных японских машин застает их врасплох. Потом они назовут этот метод «секретным японским оружием» [2], которому они ничего не смогли противопоставить. Японцы, действительно, как можно дольше не хотели раскрывать свои секреты. Этому также способствовало то, что все публикации о методе шли на японском языке, малодоступном для американцев.
В 1983 году д-р Акао по приглашению Американского общества качества едет в Америку и читает там несколько лекций о новом методе. В определенной степени эту поездку можно рассматривать как маркетинговую, рекламную акцию. Все равно, до 1985 г. американцы уже ничего не успевают сделать. Японцы уверены, что они не скоро освоят новую технологию, но просят не передавать ее корейцам, обладающим близким менталитетом и способностью к кропотливой работе.
В 1987 году под редакцией Акао в Японии выходит сборник, содержащий 12 статей о применении нового метода в различных отраслях промышленности [13]. Сборник тут же переводится и издается в США. Затем, в 1990 г. Акао выпускает монографию по применению РФК для проектирования продукции на основе требований потребителей [14], которая в этом же году переводится и впоследствии становится учебником, по которому готовят специалистов в США, Германии и других странах мира. Таким образом, с момента возникновения идеи в 1966 году до начала распространения методологии РФК по всему миру проходит 24 года.
С 1993 года регулярно проводятся национальные и Международные симпозиумы по РФК в США, Японии, Швеции, Германии, Австралии, Бразилии, Турции и других странах [8].
В 1994 году группа энтузиастов по внедрению РФК в США (Г. Мазур, Р. Зултнер и Дж. Тернинко) основывают институт по РФК. А в 1996 году этот институт учреждает премию Акао.
В 1994 году «Большая тройка» американских автопроизводителей (Дженерал Моторс, Крайслер и Форд) выпускает стандарт QS-9000, устанавливающий требования к своим поставщикам автомобильных компонентов, куда входят важнейшие положения РФК. В 2006 году этот стандарт преобразуется в международный стандартISO/TS 16949.
И все же для американских производителей автомобилей последствия захвата рынка японскими автомобилями оказываются разорительными даже в отдаленной перспективе. В 2013 году бывшая столица американского автомобилестроения город Детройт из-за непомерных долгов объявляется городом-банкротом.
В 2000 году Международная организация по стандартизации (ИСО) издает новую версию стандартов серии ИСО 9000, в которой первым основополагающим принципом систем менеджмента качества определяется принцип ориентации на потребителя.
В Россию сведения о РФК проникают благодаря усилиям, главным образом, Ю. П. Адлера. В 1992 году он публикует в журнале «Курс на качество» переводы американских статей о применении РФК в автомобильной промышленности [15], а в 2000 году – свою статью с подробным описанием этого метода [16]. В то время Россия еще только входит в рыночные отношения и не готова к полноценному восприятию и применению РФК.
1.2.2. Фазы развертывания функции качества
Анализ известных публикаций [16–19] позволяет выделить следующие основные фазы развертывания функции качества:
1) Переход от потребительских требований к техническим характеристикам изделия.
2) Переход от технических характеристик изделия к техническим характеристикам его компонентов.
3) Переход от технических характеристик компонентов к характеристикам технологических процессов.
4) Переход от характеристик технологических процессов к контролю ключевых операций.
Фаза 1. Переход от потребительских требований к техническим характеристикам изделия
Целью РФК в первой фазе является определение технических характеристик будущего изделия. Это наиболее сложная и ответственная часть работы, определяющая успешность или неуспешность всей остальной деятельности по проектированию и производству изделия.
В первой фазе можно выделить две стадии:
1) Определение потребительских требований к изделию.
2) Определение технических характеристик изделия.
Определение потребительских требований к будущему изделию (их также можно назвать потребительскими свойствами [16]) начинается с анализа рынка. Для этого организация выявляет на рынке один и или несколько сегментов потенциальных покупателей-потребителей.
Затем она анализирует, сколько эти покупатели уже купили изделий, аналогичных своему проектируемому изделию. Из этого количества изделий – сколько купили у нее и сколько у ее конкурентов, и, соответственно, сколько при этом заработали она и сколько ее конкуренты. Этот анализ позволяет организации выявить основных конкурентов и определить свое место на рынке [17].
Далее, определяются желательные потребительские свойства будущего изделия. Это делается путем опроса. Опрос производится в рамках репрезентативной выборки потенциальных потребителей выбранного рыночного сегмента.
Важно правильно составить опросную анкету. Анкету составляет группа, включающая специалиста по данной продукции, психолога или лингвиста, умеющего правильно задавать вопросы, и статистика, который будет обрабатывать данные. Вопросы формулируются на языке потребителя, чтобы точнее выявить его мнение.
Список выявленных потребительских требований может составлять несколько десятков или даже сотен. Все их реализовать невозможно. Поэтому потребительские требования укрупняются и ранжируются по степени их важности. Для группировки и сокращения числа однотипных потребительских требований применяются диаграммы сродства, связей и древовидная диаграмма, а для ранжирования – метод парных сравнений [16, 17, 20].
При использовании метода парных сравнений, каждое требование сравнивается с каждым из остальных требований. Требованию, более важному из двух, присваивается один балл, а менее важному – 0. Все баллы, набранные каждым требованием, суммируются. Размер суммы набранных баллов определяет рейтинг каждого требования.
Для удобства рейтинг может быть пронормирован путем определения его доли в общей сумме всех баллов. Потребительские требования выстраиваются в соответствии со своими рейтингами. Полученные данные позволяют начать построение диаграммы «Дом качества» будущего изделия, и заполнить два столбца ее «левого крыла» (рис. 1–3).
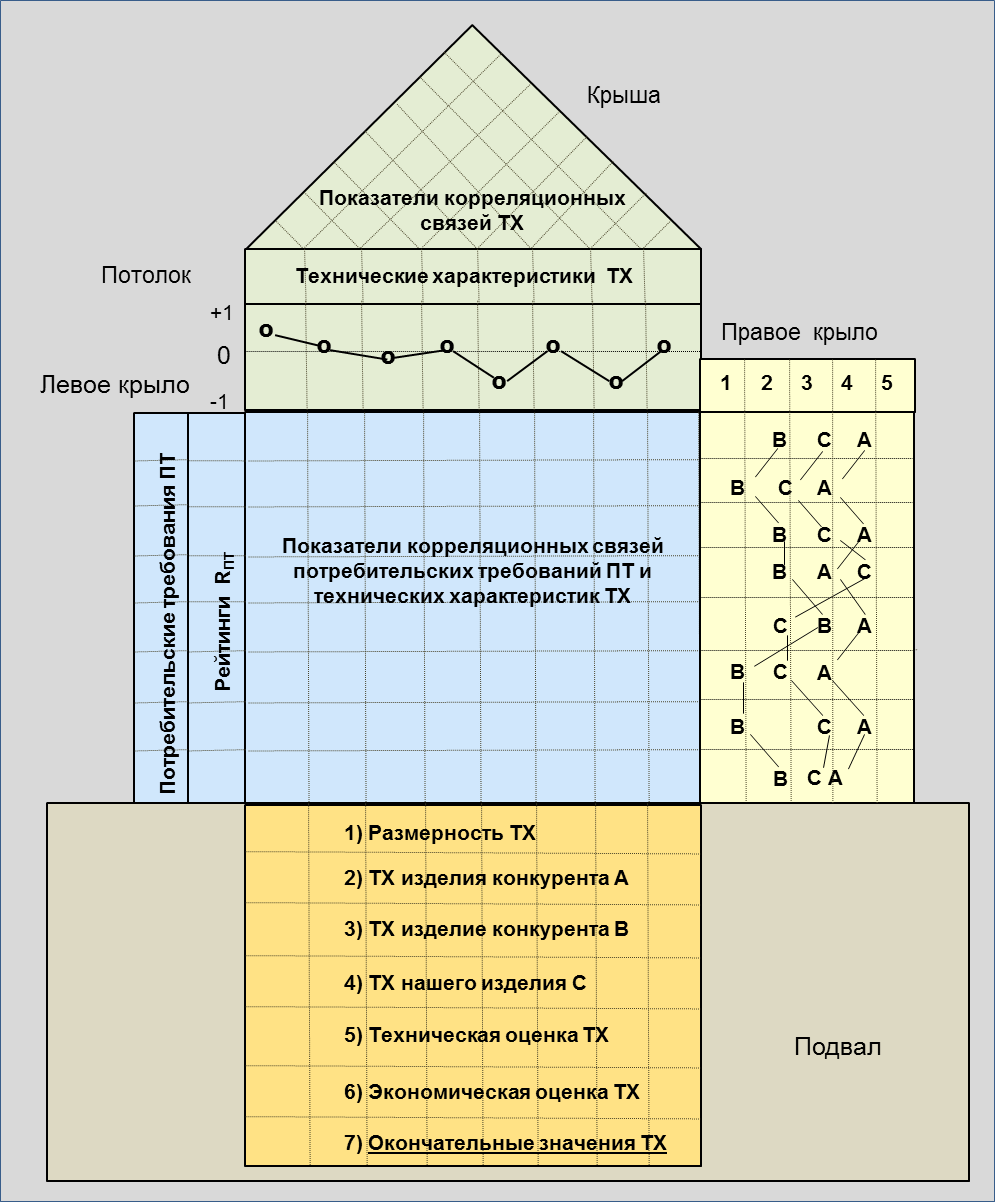
Рис. 1–3. Диаграмма «Дом качества», представляющая формирование технических характеристик будущего изделия
При окончательном формировании технических характеристик будущего изделия принимаются во внимание следующие соображения:
Во-первых, стремление сформировать идеальную модель будущего изделия, в максимально возможной степени, отвечающей обобщенным требованиям потребителей.
Во-вторых, учет реально достигнутого уровня технических характеристик изделий, предлагаемых конкурентами и нашей фирмой.
В-третьих, учет предельных технических и экономических возможностей, имеющихся у нашей фирмы на определенном временном отрезке.
Последовательный анализ и учет этих соображений позволяет создать оптимальную модель будущего изделия, обладающего конкурентоспособностью, экономичностью и реализуемостью.
Еще одна важная сторона касается технологии формирования технических требований. Есть целый ряд важных переходов, решения по которым принимаются экспертно. Это:
1) формирование анкеты для опроса потенциальных потребителей;
2) определение рейтинга потребительских требований;
3) выбор технических характеристик для реализации потребительских требований;
4) установление уровней реализации потребительских требований и оценка по ним удовлетворенности потребителей существующими на рынке изделиями;
5) и, наконец, самое важное, выбор и установление окончательных технических требований для проектирования будущего изделия.
Столь значительный перечень экспертных решений указывает на важную роль экспертных групп, обосновывающих принятие этих решений. Необходим тщательный подбор их составов, поскольку от их квалификации зависит выявление, учет и согласование разнообразных влияющих факторов. Члены группы должны пройти подготовку и, в частности, владеть инструментами управления качеством [17, 20].
Как показано выше, главным инструментом для принятия решений в РФК является диаграмма «Дом качества». Ценность этой диаграммы состоит в том, что в ней последовательно и компактно собраны все важнейшие факторы, влияющие на итоговые технические характеристики, и показана степень их взаимозависимости. В рамках «Дома качества» специалисты разного профиля (маркетологи, проектировщики, технологи, производственники и экономисты), совместно со своим руководителем, могут обоснованно анализировать сложные взаимосвязи между различными параметрами изделия и принимать взвешенные согласованные решения.
Надежность установления взаимосвязей в «Доме качества» подкрепляется знанием причинно-следственных связей и корреляционных зависимостей между различными характеристиками. Такие сведения необходимо постоянно выявлять, собирать и накапливать в виде баз данных фирмы. Это сокращает сроки и повышает качество разработки изделий.
Наличие «узких мест», выявленных при поиске оптимальных технических характеристик, указывает на то, в каких направлениях нужно вести научно-исследовательские работы по разработке новых материалов и конструкций.
Квалифицированное выполнение работ первой фазы уже само по себе в значительной мере гарантирует, что будет спроектировано конкурентоспособное изделие. Однако возможности РФК этим не исчерпываются. Дальнейшее развертывание функции качества продолжается во 2-й и последующих фазах.
Фаза 2. Переход от технических характеристик изделия к техническим характеристикам его компонентовЦелью РФК во второй фазе является определение технических характеристик компонентов будущего изделия. Для решения этой задачи, так же как и раньше, используется диаграмма «Дом качества». По-прежнему с ее помощью нужно превратить задание «что сделать» в решение «как сделать» [16].
Отличие состоит в том, что во второй фазе входными данными являются не потребительские требования, а технические требования к изделию, уже определенные в первой фазе (рис. 1–4) [17–19]. В определенной степени это облегчает задачу, поскольку требования уже сформулированы на техническом языке.
На выходе второй фазы получаются технические характеристики компонентов, т. е. узлов, комплектующих и материалов, подлежащих дальнейшей обработке. Имея технические характеристики компонентов, организация может распределить значительный объем работ по их разработке и производству среди своих партнеров-поставщиков.
В роли партнеров-поставщиков могут выступать и собственные подразделения организации. Однако экономически выгоднее большую часть работ разместить в виде заказов внешним специализированным организациям. Организационно это делается по аутсорсингу, который предусматривает контроль процессов по выполнению заказов. При этом целесообразно, чтобы партнеры-поставщики также применяли методологию РФК, соответствующую фазам 2, 3 и 4, т. е. разрабатывали свои «Дома качества».
Благодаря аутсорсингу организация получает возможность существенно сократить время проектирования и производства и быстро вывести новое конкурентоспособное изделие на рынок.
Фаза 3. Переход от технических характеристик компонентов к характеристикам технологических процессовЦелью РФК в третьей фазе является определение характеристик технологических производственных процессов. Для этого также используется диаграмма «Дом качества» (рис. 1–4).