
Полная версия
Технический углерод. Процессы и аппараты. Дополнительные материалы
Основным условием, обеспечивающим полное сжигание отходящих газов, является тщательное перемешивание газов с воздухом. Эффективность перемешивания в значительной степени зависит от конструкции горелок, применяемых для сжигания отходящих газов производства техуглерода. В конструкциях горелок для сжигания низкокалорийных отходящих газов производства техуглерода применён метод закручивания струй. Для закручивания струй в горелках используют тангенциальный подвод и применяют лопаточный закручиватель. На заводах техуглерода применяются горелки, как с тангенциальными подводами, так и с лопаточными завихрителями.
На Рис. 3.2. показан разрез горелки с тангенциальными подводами воздуха и газов.

Подача воздуха производится по патрубку 500x950 (М), отходящие газы поступают по патрубку 450x900 (Л). В результате такого направления движения газов и воздуха происходит их интенсивное перемешивание и из горелки выходит подготовленная к сжиганию газовоздушная смесь, которая сразу же воспламеняется в туннеле горелки. Огнеупорный туннель является обязательным элементом горелки с предварительным смешением газов с воздухом. /3.7.2./стр.41.
На Рис.3.3. показан разрез предтопка котла ПКК–75. Фактически это топка котла. (1– горелка, 2– топка, 3– туннель, 4– огнеупорный столб). Для стабилизации процесса горения отходящих газов помимо горелочного туннеля в топке имеются огнеупорные столбы, раскалённая поверхность которых способствует стабилизации пламени.
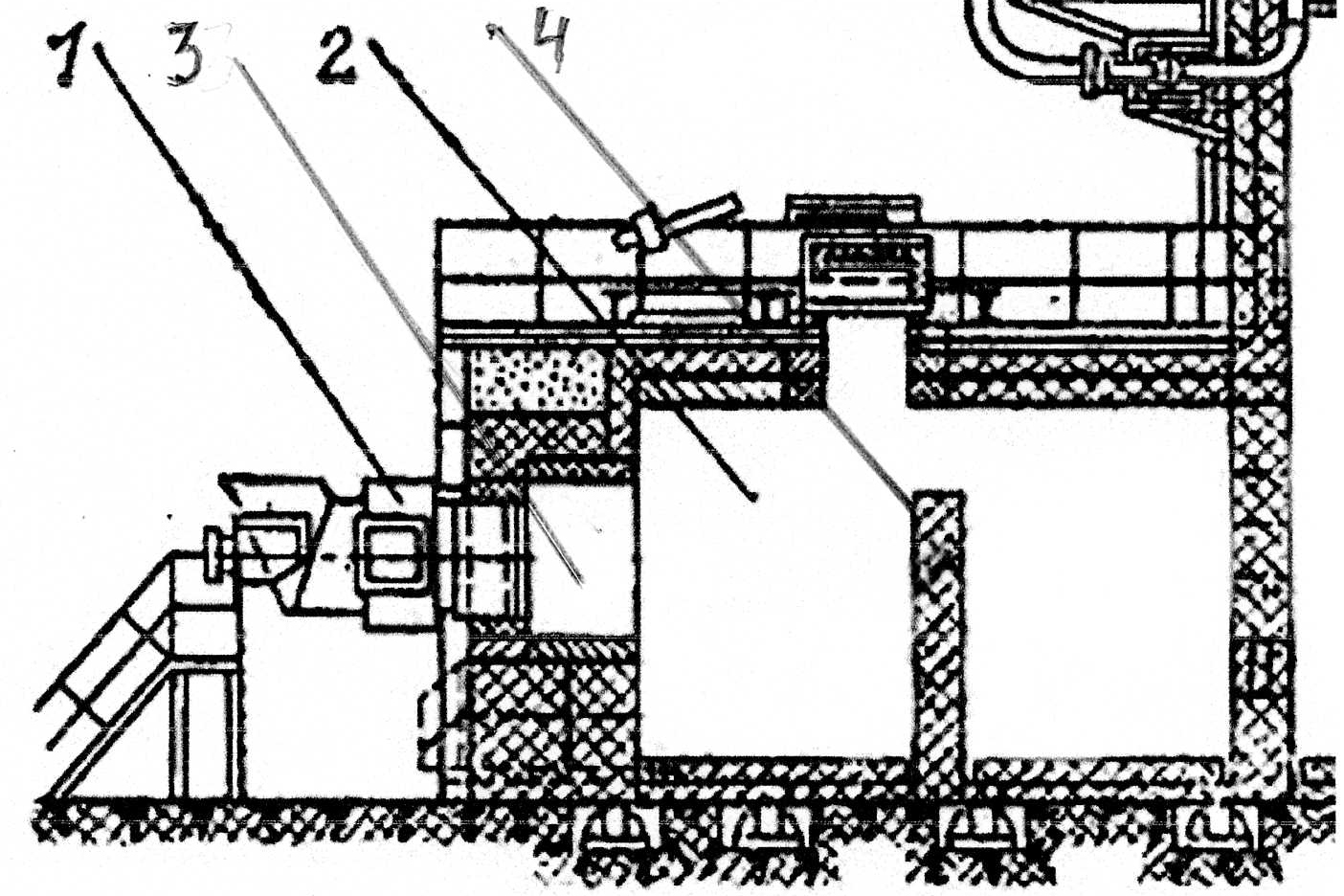
Помимо того, что столбы имеют раскалённую поверхность, наличие их придаёт дополнительную турбулентность сжигаемой газовоздушной смеси, что способствует более полному сгоранию газов.
3.2.4. Сушка гранулированного техуглерода с использованием продуктов сгорания отходящих газов процесса производства техуглерода.
Сушку гранул техуглерода с использованием в качестве теплоносителя продуктов сгорания отходящих газов производства техуглерода начали проводить с конца 60-х годов прошлого столетия на Омском заводе технического углерода одновременно с внедрением процесса гранулирования техуглерода ПМ–50(П514). Сушка гранул техуглерода осуществлялась продуктами сгорания отходящих газов, образующимися при их сжигании в специальной топке. Из топки газы непосредственно подавались в сушильный барабан, расположенный соосно с топкой /3.7.2./ стр.207. Процесс сушки был стабилизирован только после усовершенствования сушильного барабана МАС–1200. /7.3.2./ Стр.203. Применение в качестве топлива отходящих газов объяснялось не только экономическими причинами – отходящие газы при такой схеме сушки были более безопасным топливом по сравнению с жидкими видами топлива, при применении которых происходило загорание техуглерода в барабане (природный газ был подведён к заводу только в 1991-м году). С этой технологией сушки потоки производства П514 проработали 15 лет без замены сушильных барабанов.
В связи со строительством на Омском заводе техуглерода новых цехов на всех технологических потоках были внедрены новые схемы сушки с использованием сушильных барабанов БСК–40 с камерами наружного обогрева. Проект отделения обработки техуглерода оказался неудачным, что потребовало внесения существенных изменений в процессы грануляции и сушки техуглерода. Эти изменения были разработаны и внедрены специалистами Омского завода технического углерода/3.7.2./ /стр.182; стр.208-209/ и затем внедрены и на других отечественных заводах техуглерода. При разработке и проектировании процесса сжигания газов и их эвакуации из камеры обогрева сушильного барабана также были допущены ошибки. Так, для удаления отработанных газов из камеры обогрева была предусмотрена выхлопная труба диаметром 720мм, что было совершенно недостаточно. В результате в камере обогрева и сушильном барабане создавался подпор, что приводило к выделению газов в зону обслуживания. Ситуацию усугубила ещё и подача воды в боров топки для снижения температуры топочных газов, хотя в этом не было никакой необходимости. Это ещё больше увеличило объём газов в камере обогрева. И хотя проблема эвакуации газов из камеры обогрева была решена за счёт замены выхлопных труб камер обогрева трубами DН=1050мм, в связи с пуском участка сжиженного газа было принято решение о переводе сушильных барабанов на сжиженный газ. Однако это не способствовало улучшению процессов сгорания газов в камерах обогрева сушильных барабанов. Для сжигания сжиженных газов (пропан-бутан) в камере обогрева были использованы только 4 горелки, тогда как при применении природного газа использовалось 13 горелок, за счёт чего обеспечивалось беспламенное горение газов. . Понятно, что при использовании 4-х горелок условия эксплуатации барабанов значительно ухудшились, так как наружные стенки барабанов омывались светящимися факелами с более высокой температурой, чем температура продуктов сгорания природного газа. Это в конечном итоге привело к сокращению сроков службы сушильных барабанов. Кроме того, имелись случаи разрушения камер обогрева при «хлопках» газовоздушных смесей в камерах обогрева при утечках сжиженного газа.
С 1991 года на Омском заводе техуглерода началась газификация завода, заключающаяся в замене всех видов топлива на природный газ, который был подведён к заводу. Эта замена коснулась, прежде всего, реакторов и камер обогрева сушильных барабанов. На всех камерах обогрева горелки для сжиженного газа были заменены горелками для сжигания природного газа, было также увеличено количество горелок на каждую сушильную камеру. Одновременно с этим проводилась реконструкция цеха сухой грануляции по переводу потоков цеха на мокрую грануляцию, что потребовало установки дополнительных сушильных барабанов. Реконструкция 1-го потока была завершена в 1992-м году, 4-го потока – в 1994, 2-го в 2003 году и 3-го только в 2012 году. Необходимо отметить, что на третьем потоке было заменено всё оборудование полностью. Проектирование нового потока осуществлялось заводскими службами. Из-за ограниченных сроков, отпущенных на реконструкцию этого потока, на нём не удалось осуществить сушку техуглерода с использованием отходящих газов. Сушку техуглерода отходящими газами удалось восстановить в том же году на потоке №4 Цеха № 1. По сравнению с первоначальным проектом был увеличен диаметр выхлопной трубы камеры обогрева сушильного барабана, ликвидирован подвод воды в боров топки, заменена шамотная футеровка топки, борова, распределительного коллектора и окон в камере обогрева на корундовую для обеспечения возможности сушки техуглерода природным газом при временном отсутствии отходящих газов. Были исключены из схемы и горелки, установленные в камере обогрева сушильного барабана. Объёмы топки и борова были оставлены без изменения для обеспечения полного сгорания отходящих газов.
Рис 3.4. Сушка техуглерода с применением отходящих газов производства техуглерода.
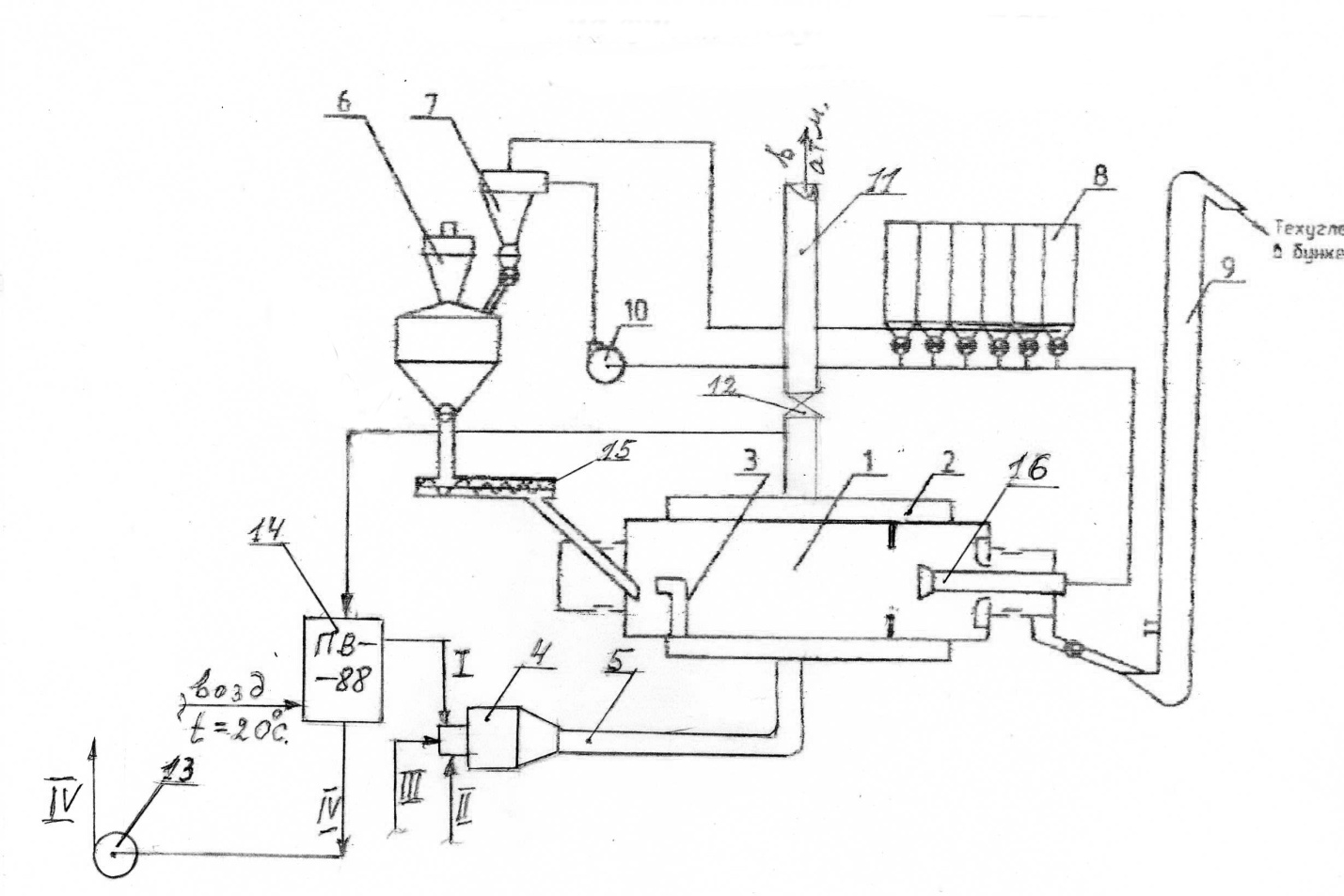
1—сушильный барабан БСК–40; 2—камера обогрева барабана; 3—заборный патрубок; 4—топка сушильного барабана; 5—боров топки; 6—Циклон-уплотнитель; 7—циклон доулавливания; 8—фильтр доулавливания; 9—элеватор; 10—турбовоздуходувка отсоса газов из сушильного барабана; 11—выхлопная труба камеры обогрева; 12—дроссель; 13—турбовоздуходувка эвакуации газов из дымовой трубы; 14—воздухоподогреватель; 15—гранулятор; 16—патрубок отсоса газов из сушильного барабана; I—трубопровод подачи воздуха в горелку топки; II—трубопровод подвода отходящих газов; III—подвод природного газа; IV—продукты сгорания отходящих газов.
На Рис.3.4. показана схема сушки техуглерода продуктами сгорания отходящих газов, образующихся при производстве техуглерода. Отходящие газы с температурой 190–220⁰С. по трубопроводу II подаются в горелку топки сушильного барабана 4, туда же по трубопроводу I подаётся воздух, нагретый в воздухоподогревателе 14 до 350–400⁰С. По трубопроводу III к горелке подводится природный газ. При обычном режиме сжигания отходящих газов природный газ может подаваться в небольших количествах для стабилизации процесса их горения, а также для повышения температуры газов, поступающих в камеру обогрева сушильного барабана. Используется природный газ также при розжиге горелки и при разогреве топки. В топке происходит полное сгорание отходящих газов, и продукты их сгорания с температурой 1100–1300⁰С. по борову 5 поступают в камеру обогрева сушильного барабана. Газы в сушильной камере равномерно распределяются по длине сушильного барабана как это показано на Рис.3.5
Рис. 3.5. Распределение газов в камере обогрева сушильного барабана.
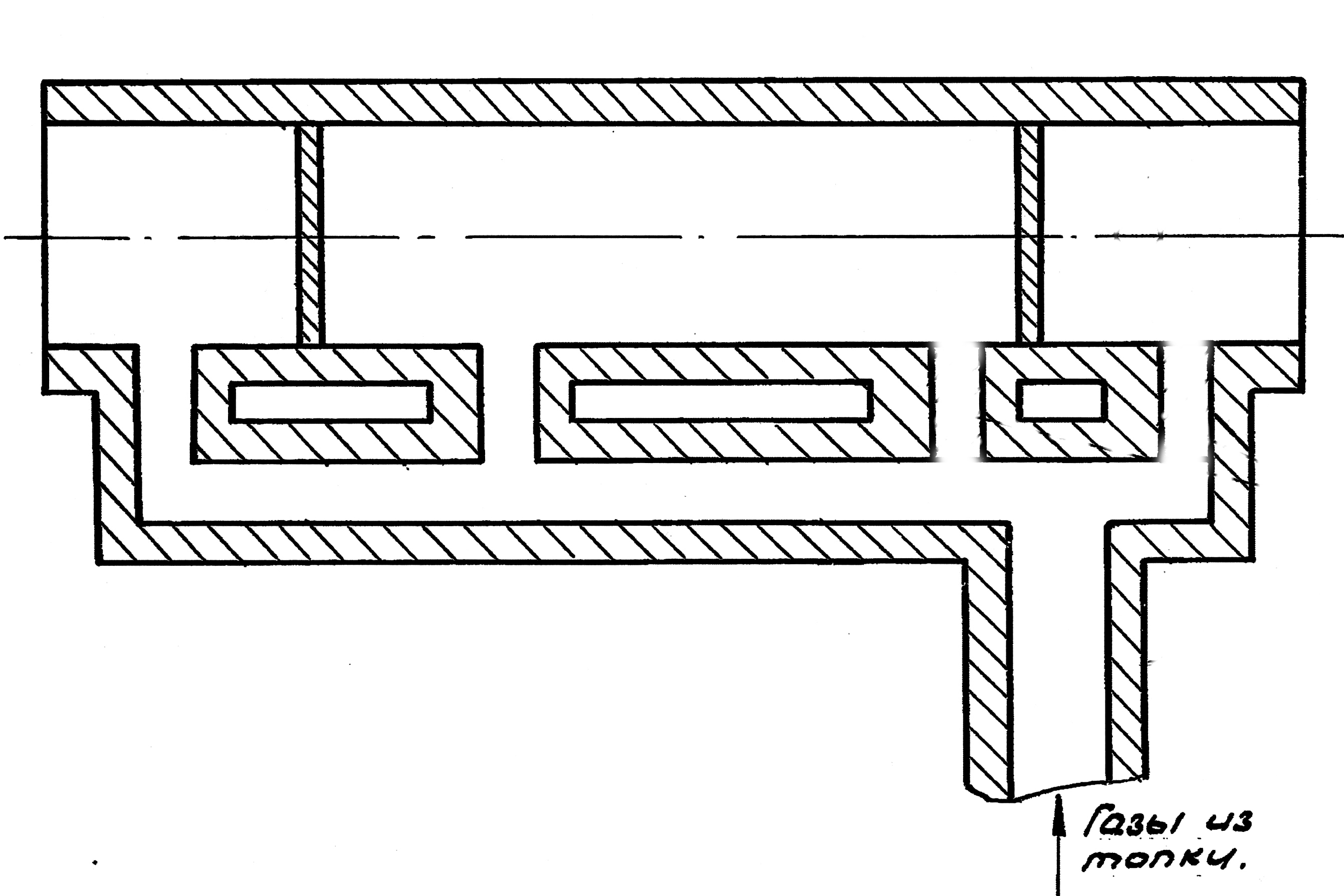
Часть газов из камеры обогрева по заборному патрубку 3 поступает в сушильный барабан ( Рис.3.4.) для удаления водяных паров, образующихся при сушке техуглерода, другая часть газов используется для наружного обогрева барабана (передачи тепла от горячих газов влажному техуглероду через стенку барабана). Газы с водяными парами удаляются из полости барабана через патрубок 16 и турбовоздуходувкой 10 направляются в систему доулавливания. Отработанные газы из камеры обогрева с температурой 500–550⁰С. поступают в дымовую трубу 11 и далее, пройдя воздухоподогреватель 14, поступают во всасывающий трубопровод турбовоздуходувки 13. В межтрубное пространство воздухоподогревателя 14 подаётся воздух, который за счёт тепла газов, проходящих по трубам воздухоподогревателя, нагревается до 330–450⁰С. и по трубопроводу I поступает в горелку топки 4. Отработанные газы из воздухоподогревателя 14 с температурой 300⁰С. поступают во всасывающий трубопровод турбовоздуходувки 13 и далее по трубопроводу IV направляются в рубашки обогрева гранулятора, бункеров уплотнителя и циклонов, шлюзовых питателей, течек и.т.д. Обогрев поверхностей технологического оборудования производится для предотвращения налипания техуглерода на внутренних поверхностях аппаратов. Избыточная часть газов из дымовой трубы через дроссель 12 сбрасывается в атмосферу.
В связи с тем, что температура газов, омывающих сушильный барабан, значительно ниже, чем при использовании для сушки природного газа и, тем более, сжиженных газов, возрастает срок службы корпусов сушильных барабанов. В этой связи необходимо отметить также и одну из самых распространённых причин уменьшения сроков службы сушильных барабанов, не связанной непосредственно с видом применяемого для сушки топлива. Такой причиной является остановка барабана без своевременного отключения подачи топлива, что приводит к перегреву металла, из которого изготовлены барабаны, и последующему их разрушению. Это происходило по той причине, что автоматическое отключение подачи топлива в камеру обогрева проектом предусматривалось только при остановке электродвигателя привода барабана. Однако при разрушении муфтовых соединений блокировка не срабатывает, так как в этом случае двигатель продолжает работать и при остановленном барабане, что является одной из основных причин разрушения сушильных барабанов. Такие аварии были устранены после установки на все барабаны датчиков движения, разработанных специалистами Омского
Технического Университета. В этом случае блокировка срабатывает сразу же при прекращении вращения корпуса барабана. Большое значение при эксплуатации барабана имеет контроль температуры стенки барабана, измеряемой специальным пирометром. В период пуска и освоения процесса сушки техуглерода в барабанах с наружным обогревом не удалось обеспечить достоверные показания пирометров для измерения температуры стенки барабана. Обеспечить надёжную работу этих пирометров удалось только в 90-х годах. Выяснилось, что температура стенки барабана при соблюдении регламентных режимов сушки не превышала 550⁰С. и подача воды в боров топки не требовалась. Однако к тому времени для сушки техуглерода уже использовался природный газ. Следует отметить, что температура стенки барабана является важным параметром и позволяет своевременно определить уменьшение или прекращение поступления техуглерода в сушильный барабан и принять необходимые меры. Эта температура должна измеряться в нескольких точках по длине барабана.
3.3. Основные характеристики отходящих газов производства техуглерода.
При сжигании отходящих газов, образующихся при получении техуглерода, необходимо знать и учитывать физические и химические свойства этих газов.
Усреднённый состав сухой части газов:
СО—14—16%; СО2—3—4.5%; Н2—9—13%; О2– 1—2%; СН4—0,1—0,5%; Н2S—0,05—0,2%; N2—72,85—63,35%.
Здесь указан состав сухой части газов, так как газовым анализом определяется состав только сухой части газов и все расчёты процессов горения проводятся, как правило, на сухую составляющую газов. Количество водяных паров определяется расчётным путём и в расчётах обычно относится на сухую часть газов.
Молярная масса М, кг/кмоль– это отношение массы вещества к его количеству. В расчётах её величина может использоваться для определения плотности газов.
Плотность ρо, кг/м³– это масса газа, приходящаяся на 1м³ занимаемого им объёма. Плотность газовой смеси определяется по формуле:
ρсм = 0,01(ρ1V1 + ρ2V2 + . . . .+ ρnVn),
Где ρ1, ρ2, ……,ρn – плотность компонентов газового топлива; V1, V2, ….., Vn – содержание компонентов, % по объёму.
Плотность сухой части отходящих газов производства техуглерода в нормальных условиях определяется по формуле:
ρ0 = 0,01(1,25СО + 0,09 Н2 + 1,54 Н2S + 0,717 СН4 + 1,98 СО2 + 1,25 N2 + 1,43 О2 + 1,98 СО2), где СО, Н2…………..,СО2 – компоненты отходящих газов, % по объёму. /3.1./.
Здесь и в дальнейшем объёмы воздуха и других газов берутся при нормальных физических условиях ( Р= 101,3кПа и Т= 273К).
Горючие составляющие газов: СО; Н2; СН4; Н2S. ( Остальные газы – О2, СО2, N2– это балластные газы).
Влажностью называется содержание в газе водяного пара.
Абсолютной влажностью (влагосодержанием) газа называется количество или масса водяных паров, содержащихся в единице объёма газа. Единица измерения абсолютной влажности– г/м³.
Объём влажных газов связан с объёмом сухих газов фрмулой: Vв.г.= Vс.г. (1+d/0.805), где d– влагосодержание газа, г/м³., 0,805 плотность паров воды, г/нм³. Так, например, при влагосодержании газов 302г/м³ объём влажного газа составит: Vв.г. = Vс.г. (1+302/0,805) = 1,375Vс.г.
Главной характеристикой отходящих газов, как и любых горючих газов, является их
Теплота сгорания Это количество теплоты, которое выделяется при полном сгорании единицы количества топлива, в нашем случае 1м³ отходящих газов. Различают высшую и низшую теплоту сгорания. Высшей теплотой сгорания топлива Qв называется количество теплоты, выделяющейся при полном сгорании единицы количества топлива при полной конденсации водяных паров в продуктах сгорания. Низшей теплотой сгорания топлива Qн называется количество теплоты, выделяющееся при полном сгорании единицы количества топлива при отсутствии конденсации водяных паров в продуктах сгорания, образующихся при горении.
Температура уходящих газов, отводимых из теплоиспользующих установок, превышает 100⁰С.,следовательно, конденсация водяного пара, содержавшегося в продуктах сгорания, не происходит, поэтому теплотехнические расчёты выполняют на основе низшей теплоты сгорания топлива. Отходящие газы производства техуглерода подаются на сжигание при температурах 170—210⁰С. Низшая теплота сгорания этих газов Qн составляет 1,9– 2,6 МДж/м³.
Теплоту сгорания сухих отходящих газов производства техуглерода, МДж/м³, с достаточной степенью точности определяют по элементному составу, выраженному в процентах по объёму:
Qн=0,126СО + 0,108Н2 + 0,238Н2S + 0,358CH4.
Теплота сгорания (теплотворная способность по прежней терминологии) является основной технологической характеристикой топлив, которая используется для их оценки как энергоносителей.
Теплоёмкость газа представляет собой количество теплоты, необходимое для нагрева газа на 1К. Если теплоёмкость отнести к количеству газа, то это будет удельная теплоёмкость. В зависимости от того, что принимается за единицу количества газа, удельная теплоёмкость называется массовой, малярной, объёмной. Для расчётов процессов горения газов используется средняя объёмная теплоёмкость при постоянном давлении, (кДж/м³·К). или (кДж/м³·⁰С.) Зависимость средней объёмной теплоёмкости продуктов сгорания газов от температуры дана в Табл.3.1.( Приложенние 8.1.).
Теплосодержанием газа называется количество теплоты, которым он обладает при данной температуре. QT=Cm·m·T, где Сm – удельная массовая теплоёмкость, Дж/(кг·К); m – масса газа, кг; Т – температура газа, К.
Теплосодержание продуктов сгорания Qпс= Vпс·Cp· Tг, где Vпс – объём продуктов сгорания; Сp – средневзвешенная объёмная теплоёмкость продуктов сгорания в диапазоне от 0 доТг; Тг – температура горения.
По теплосодержанию компонентов смеси можно определить её температуру (это будет показано на примере).
Теплосодержание единицы массы или объёма при данной температуре называется энтальпией.
Пределы воспламенения ( взрываемости ) в смеси с воздухом в % объёмных находятся в пределах 47 – 81%.
Это означает, что если содержание газов в воздухе составляет менее 47%, то такая смесь не горит и не взрывается из-за недостатка горючих веществ, при содержании газов в воздухе более 81%, такая смесь тоже не горит и не взрывается но уже из-за недостатка окислителя. На практике верхний и нижний пределы взрываемости отходящих газов определяют по содержанию в них кислорода, так как он легко определяется как лабораторным путём, так и с помощью автоматических газоанализаторов. Отходящие газы могут взрываться при содержании в них кислорода от 4 до 11%. Если кислорода в отходящих газах будет содержаться больше 4%, то при наличии источника огня (например, искры горящего техуглерода) в аппарате может произойти взрыв. Поэтому содержание кислорода в отходящих газах постоянно контролируется. Подача отходящих газов на сжигание допускается только при содержании в них кислорода менее 2%. Перед подачей газов в аппараты для сжигания трубопроводы продуваются отходящими газами для вытеснения из них воздуха. Производится также и продувка трубопроводов природного газа перед подачей их для сжигания
Температура воспламенения. В разделе 3.2.3. дано объяснение процесса воспламенения газов и указаны температурные пределы воспламенения отходящих газов производства техуглерода (600—750⁰С.) В Таб.3.2. приведены основные характеристики газов, используемых в промышленности техуглерода, и основных газов, входящих в состав отходящих газов производства техуглерода.
Табл.3.2. приведена в приложении 8.2.
3.4. Температура горения отходящих газов.
Температурой горения называется температура раскалённых продуктов сгорания. Она является одной из основных характеристик газа, а также любого другого топлива.
Источником энергии, идущей на нагрев продуктов сгорания, является теплота сгорания газа и физическая теплота, вносимая газом и окислителем (на 1м³газа).
В зависимости от условий сжигания газа в настоящее время различают максимальную (адиабатическую) температуру горения, называемую ещё жаропроизводительностью, а также калориметрическую и теоретическую температуры горения.
Жаропроизводительность Тж– максимальная температура продуктов полного сгорания газа в адиабатических условиях с коэффициентом избытка воздуха 1,0 и при температуре газа и воздуха, равной 0⁰С.:
Тж= Qн /(Vпс·cp). (3.3.),
где QН – теплота сгорания газа; Vпс– объём продуктов сгорания газа; ср – средневзвешенная объёмная теплоёмкость продуктов сгорания газа.
Тж– величина, определяемая расчётным методом при условии отсутствия теплообмена с окружающей средой (т.е. в адиабатных условиях). Эта температура является важной характеристикой топлива. Сравнение различных видов топлива по их способности создавать высокие температуры при горении становится возможным при сравнении величин жаропроизводительности (Тж ) этих топлив.
Таким образом, жаропроизводительность является второй по значению энергетической характеристикой (после теплоты сгорания), от которой зависит оценка эффективности топлива как энергоносителя.
Жаропроизводительность ⁰С, в сухом воздухе некоторых простых газов: водород—2235, оксид углерода– 2370, метан– 2043, пентан– 2119, ацетилен– 2620.
Жаропроизводительность ⁰С, в сухом воздухе некоторых сложных газов усреднённого состава: природный газовых месторождений – 2040, сжиженный(50% С3Н8 + 50% С4Н10) – 2115, коксовый – 2120, генераторный из тощих углей – 1670, доменный – 1470. Жаропроизводительность отходящих газов производства техуглерода усреднённого состава достигает только величины 1076⁰С.
Калориметрическая температура горения Ткал—температура, определяемая без учёта диссоциации водяных паров и диоксида углерода, но с учётом фактической начальной температуры газов и воздуха. Она отличается от жаропроизводительности Тж тем, что температура газа и воздуха, а также коэффициент избытка воздуха( α )принимаются по их действительным значениям. Определить Тк для газа можно по формуле:
Ткал.= (Qн +qфиз)/(ΣV·ср) (3.4.)
Где qфиз– теплосодержание( физическая теплота газа и воздуха, кДж/м³). Или
Ткал= (Qн + 1,0·cсг·tг +α·Vв·св·tв)/(ΣVп.сг.·Спр.сг.+Vв.изб.·св), где
Vв.изб.= (α -1)·Vв·Св. Объём сухих газов в формуле указан равным единице, так как расчёт проводится на 1м³ сухого газа.
Ткал отходящих газов производства техуглерода будет отличаться от величины жаропризводительности в связи с учётом тепла отходящих газов производства, поступающих в топку с температурой 170– 210⁰С., тепла нагретого до 300– 450⁰С. воздуха и учётом коэффициента избытка воздуха.
Теоретическая температура горения определяется также в условиях адиабатического сжигания газов, т.е. при отсутствии теплообмена с окружающей средой, но с учётом теплосодержания свежей горючей смеси , реакций диссоциации молекул СО2 и Н2О и потерь тепла от физической и химической неполноты сгорания.
Следует сразу же отметить, что отходящие газы производства техуглерода сжигаются при температурах гораздо ниже 1600⁰С.,поэтому диссоциация молекул СО2 и Н2О не происходит, а потери тепла от физической и химической неполноты сгорания не значительны и в расчётах обычно не учитываются. Поэтому при расчёте действительной температуы продуктов сгорания за основу принимается калориметрическая температура.
. Действительная температура продуктов сгорания Тд – температура, которая достигается в реальных условиях сжигания газов. Она всегда ниже теоретической, так как зависит от потерь тепла в окружающую среду. Потери тепла в окружающую среду для топки и борова сушильной камеры определяют исходя из поверхности и температуры корпусов борова и топки. Обычно эти потери тепла не превышают 5%. В металлургии действительная температура продуктов сгорания определяется исходя из величины калориметрической температуры и значения пирометрического коэффициента n по формуле:
ТДЕЙСТВ = nпир · Ткал (3.5.) , где nпир – пирометрический коэффициент. Этот коэффициент по данным/3.7.1./ стр. 78. составляет, например, для топочной камеры – 0,95, для топки экранированного котла– 0,65 – 0,7.
Примечание. В последние годы в теплотехнике проведены изменения в терминологии температур горения топлива. Если ранее максимальная температура продуктов полного сгорания топлива в адиабатических условиях с коэффициентом избытка воздуха α =1,0 и при температуре газа и воздуха равной 0⁰С. обозначалась как калориметрическая температура (термин Д. И. Менделеева термин жаропроизводительность рассматривался как синоним калориметрической температуры), то сейчас эта температура обозначается термином жаропроизводительность, а калориметрическая температура определяется с учётом тепла газов и воздуха и учётом избытка воздуха, как это указано выше.
Из этого следует, что в таблице 2.2. источника /3.7.2./. стр. 30 значения калориметрической температуры полностью соответствуют значениям определяемой в настоящее время по формуле 3.3. жаропроизводительности.