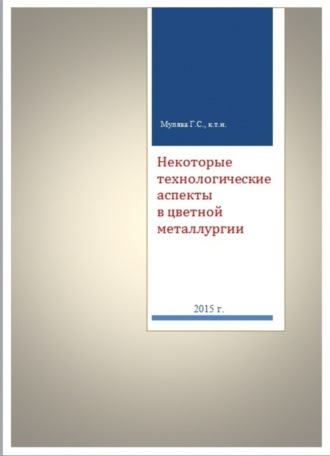
Полная версия
Некоторые технологические аспекты в цветной металлургии
3 Обсуждение результатов работы
Как видно из уравнений для извлечения меди в раствор, после температуры обжига 600 0С извлечение резко падает, что говорит о другом механизме окисления сульфидов в концентрате.
Из результатов исследований по плану следует, что обжиг шлакового концентрата в неподвижном слое при избытке воздуха при условиях: температура – 5600 С, время – 1,62 часа позволяет практически полностью перевести медьсодержащие сульфиды концентрата частично в оксиды меди и остальное – в сульфат меди. Об этом свидетельствует как высокая степень извлечения меди в раствор (таблица 2.2) так и тот факт, что экстраполяция зависимости извлечения Cu от концентрации серной кислоты приводит при СН2SO4 = 0 к переводу меди в раствор, по уравнению ( 1 ), в размере 68,06 % . При этом уравнение для извлечения в раствор железа даёт отрицательное значение, что можно интерпретировать, как отсутствие железа в растворе.
Действительно, известно, что при температурах (480 – 520) 0 С сульфаты железа разлагаются или, если процесс разложения не завершился полностью – значительно хуже растворяются в воде, чем сульфат меди. Причиной же высокой концентрации железа в сульфатном растворе при кислотном выщелачивании является, очевидно, воздействие серной кислоты на вновь образовавшиеся при сульфатизации ШК «свежие» оксиды железа.
Таким образом, выполненные исследования по плану показали, что при определённых условиях окислительной термообработки шлакового концентрата (560 +– 40 0С) можно последующим кислотным выщелачиванием добиться глубокого извлечения меди в раствор – 95,6 % (таблица 2.2). Однако при этом остаётся высокое содержание кислоты в растворе (следует из балансовых расчётов) и, главное, в раствор переходит большое количество железа, до 14 г/л.
В то же время, после обжига шлакового концентрата вблизи 560 0С, по крайней мере, половина меди находится в форме сульфата и её можно затем извлечь из огарка водой, практически не затронув в кеке железо. Это и было использовано при дальнейшем проведении работы.
2.1.2 Извлечения из огарка шлакового концентрата меди водой.
Получение кристаллического пяти водного сульфата меди.
Извлечение меди из огарка шлакового концентрата проводили водой с навесками массой (100 – 150) г. Чтобы получить достаточно большое количество огарка (более 2 кг), шлаковый концентрат обжигали в муфельной лабораторной печи в периодически перемешиваемом слое массой проб по 500 г при (520 – 600) 0С в течение (2,5 – 3) час и при контролируемом (избыточном) доступе воздуха к слою.
Накопленный огарок перемешивали, отбирали пробу на анализ и герметизировали. В огарке определяли содержание меди, железа и цинка.
Выщелачивали огарок при Ж : Т = 2 : 1 в интенсивно перемешиваемом слое при температуре (55 – 60) 0С. По окончании выщелачивания пульпу охлаждали, фильтровали на нутч – фильтре, кек промывали водой до появления прозрачного фильтрата, определяли суммарный объём фильтрата и анализировали его на содержание контролируемых элементов.
Кек после сушки взвешивали, смешивали и анализировали на содержание меди, железа и цинка.
Исследовали влияние времени на степень извлечения в раствор меди и железа при водном выщелачивании огарка шлакового концентрата после сульфатизации. Кроме этого контролировали поведение цинка. В растворах опытов №2 и 4 анализировали массовую долю золота. Результаты извлечения в раствор меди, железа и цинка из огарка приведены в таблице 2.3.
Хотя нами было выбрано достаточно малое время выщелачивания водой огарка – 0,5 час, не удалось установить время «разгона» процесса растворения CuSO4 . Уже при этом времени в раствор перешло наибольшее количество, более 40 % исходной меди. Это говорит о практическом отсутствии диффузионных сопротивлений и доступности жидкой фазы к сульфату меди. Следовательно, при протекании реакций окисления сульфидов в шлаковом концентрате в период сульфатизации сульфат меди формировался на поверхности оксидов меди (железа).
Обращает на себя внимание снижение распределения железа в раствор с ростом времени выщелачивания, что, по-видимому, свидетельствует о протекании «обратной» реакции после прохождения определённого времени
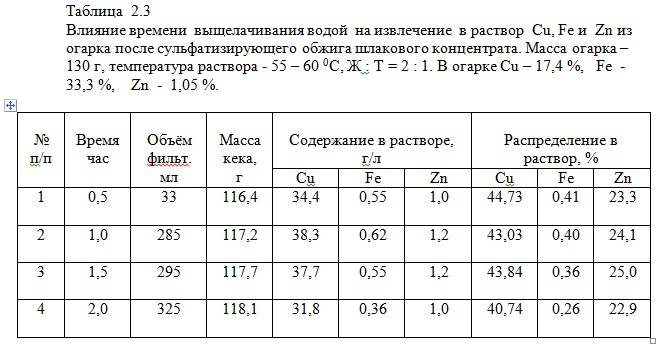
«очистки» поверхности оксидов меди от сульфата меди:
Fe2(SO4)3 + 3CuO + 3H2O = 3CuSO4 + 2Fe(OH)3.
Интересно, что одновременно падает и распределение цинка в раствор. Возможно, протекает реакция:
ZnSO4 + CuO + H2O = CuSO4 + Zn(OH)2.
Из таблицы 2.3 видно, что однократное выщелачивание водой огарка при Ж : Т = 2 : 1 при 60 0С не позволяет получить раствор с концентрацией меди более 40 г/л. Для повышения концентрации меди в растворе провели двукратное выщелачивание, т.е. в раствор от первого выщелачивания вновь добавили свежий огарок и операцию повторили. В итоге получили раствор сульфата меди с содержанием Cu – 65,4 г/л. Такой раствор в процессе горячей очистки от железа можно затем выпарить до половины и получить концентрированный горячий раствор с содержанием меди 120 -140 г/л, пригодный для производства медного купороса.
В растворе после его двукратной обработки огарком получили массовую долю железа – 2,0 г/л.
Полученные затем при полупромышленных испытаниях растворы сульфата меди применили для изготовления медного купороса, рисунок 2.1. Результаты испытаний легли затем в основу создания нового способа переработки сульфидных медных концентратов.
Основной объём работ по получению высококачественного купороса был связан с очисткой «полупромышленного» раствора от двухвалентного железа, содержание которого колебалось в растворах (по партиям) – от 5,8 до 6,9 г/л.
Для глубокой очистки раствора от железа (до 100 – 150 мг/л) потребовалось применение свежеобразованного оксида меди, который получали из собственного очищенного раствора сульфата меди добавкой в горячий раствор 20 % раствора гидроксида натрия. В укрупнено – лабораторных условиях, при продувке воздухом горячего раствора сульфата меди, загрязнённого железом, необходимой степени очистки удалось достигнуть при повышении ТНК меди на осаждение железа до 2,6 – 2,8 раз.
После фильтрации раствора и выведения медно-мышьякового (железистого) кека, раствор подкислили, упарили до 200 г/л и осадили кристаллы со степенью перевода меди из раствора в твёрдое – (60 – 62) %. Через сутки от кристаллов отсасывали маточник, промывали водой и сушили при (100 – 105) 0С.
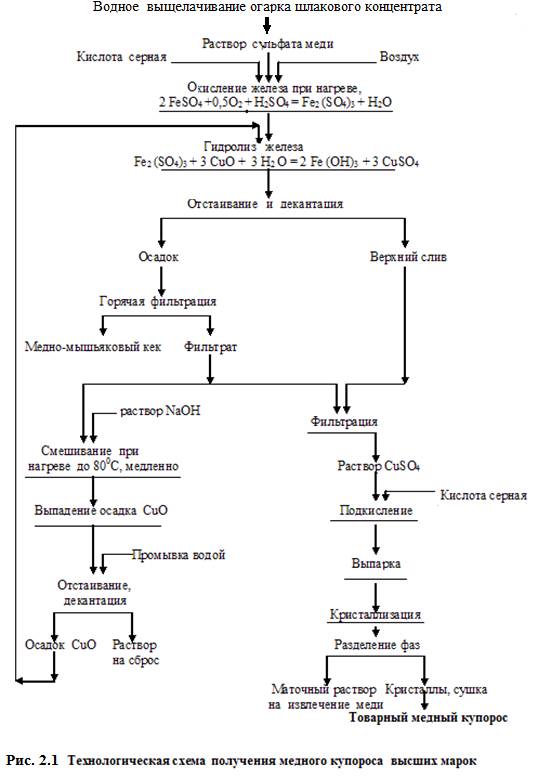
Анализы опытной партии полученного продукта, показали следующие данные, % : (в скобках – нормы по ГОСТ 19347-99 для марки А, высший сорт): массовая доля меди – 27,31 (не менее 25,20), массовая доля мышьяка – не обнаружено (не более 0,002), массовая доля железа – 0,017 (не более 0,020), массовая доля свободной серной кислоты – 0,025 (не более 0,20), массовая доля нерастворимого в воде остатка – 0,022 (не более 0,03).
Обращает на себя внимание низкое содержание в пробах мышьяка – не более 0,001%. Это объясняется тем, что в шлаковом концентрате по данным анализов его массовая доля не превышает 30 г/т или 0,003%, что вызвано большим давлением паров оксидов мышьяка при высокотемпературной плавке медных концентратов. Также, при избытке соединений железа в шлаках, форма нахождения мышьяка в них – нерастворимый ферро арсенид FeAs2.
2.2 Получение глёта для пробирного анализа из свинца и воды
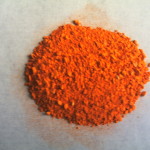
Глёт свинцовый для пробирного анализа; получен из свинца,
воздуха и воды.
2.3 Получение дицианоаурата калия (I) из отходов гальванического производства.
Вторичные драгоценные металлы, как правило, формируются больше в промышленной сфере, чем в бытовой. Так, вторичное золото (и серебро) мы фиксировали в электронных приборах (списанные ЭВМ старых поколений и ПК, множительная техника), в жидких отходах гальванических производств, в фотобумаге и киноплёнке (последние содержат только серебро).
Утилизация вторичных драгметаллов может быть организована на предприятии, имеющем, кроме разрешительных документов и соответствующих инструкций, обученный персонал, необходимые реагенты и условия, обеспечивающие безопасность работ.
Технологическая схема переработки вторсырья на таком предприятии не обязательно должна заканчиваться получением марочного металла. Это может быть либо товарная соль, имеющая спрос, либо концентрат, направляемый по договору на переработку на специализированное металлургическое предприятие.
В качестве примера приведём принципиальную технологическую схему получения из отработанных электролитов золочения соли – калия дицианоаурата (I), KAu(CN)2 , ч.д.а., рисунок 2.2.
Как видно из схемы, раствор (после входного контроля на содержание золота и определения рН) обрабатывают с целью доведения рН до 8. При этом образуется желеобразный осадок, в котором, как показал анализ, имеется
повышенное содержание фосфатов. Этот осадок отделяют от раствора на объёмном фильтре, сушат и затем обжигают в печи с получением твёрдого рассыпчатого продукта – золы.
Далее, например химическим способом, высаживают из раствора золото, которое диспергируют и затем направляют на растворение в растворе цианида калия. Полученный золотосодержащий раствор каскадно (в несколько этапов) выпаривают (медленно – иначе повысятся потери золота с паром), соль промывают ледяной водой, отделяют на фильтре и сушат. Партии соли объединяют, тщательно (защитив органы дыхания противопылевым респиратором) перемешивают и определяют золото и примеси в соответствии с требованиями ГОСТ на дицианоаурат калия ( I ).
Сборы маточных растворов объединяют, выпаривают, сушат, добавляют к золе и направляют на извлечение золота. Последнее также используют в цикле производства соли.
Опыт освоения такой технологии отражён в нижерасположенном балансе золота, таблица 2.4. Видно, что его прямое извлечение из отработанных растворов золочения достигает 96,29 %, а потери золота не превышают 2,0 % от исходного в растворе (потери должны соответствовать разработанному, утверждённому на предприятии и согласованному с Пробирной палатой «Нормативу потерь»).
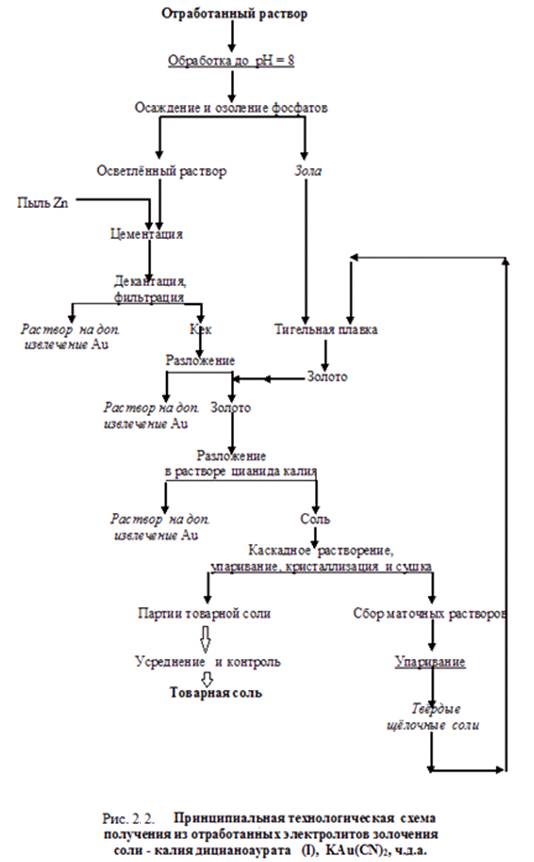
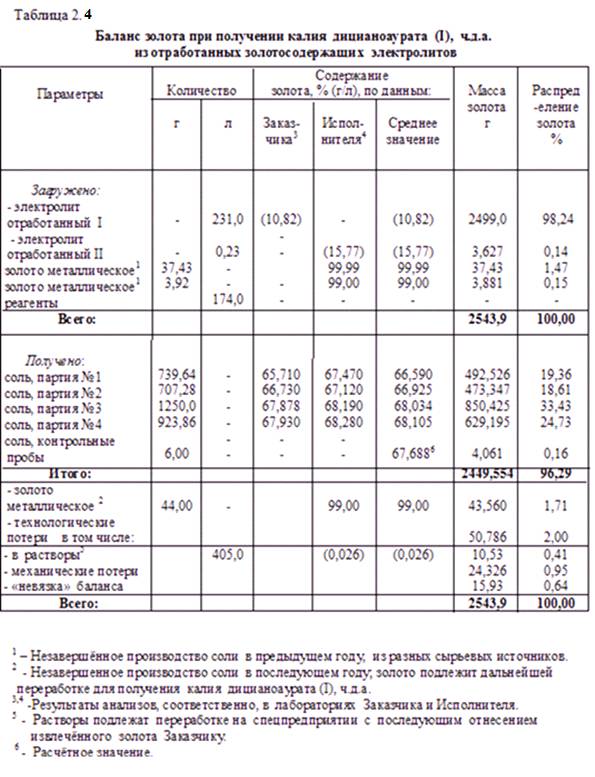
2.4 Формула красной ртути?
Если принять за основу гипотезу о существовании т.н. «красной» ртути, то можно предложить к рассмотрению следующую схему формирования макро-молекул пироантимоната ртути или полипироантимоната ртути (под действием инициирующего излучения в среде кислорода, см. патент РФ № 2077159).
Применим способ изложение материала в виде структурных формул, где одна чёрточка между атомами в молекуле означает электронную связь (например, между ионами металла и кислорода в оксиде).
Схема образования сложного оксида – пироантимоната ртути – из оксидов ртути и сурьмы приведена на рисунке 2.3.
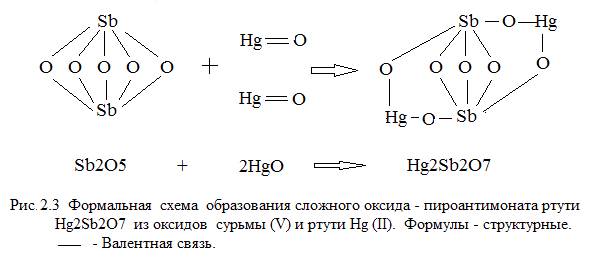
При энергетическом воздействии на соль возможна перестройка связей между ионами металлов и кислорода и «сшивание» молекул Hg2Sb2O7 в линейную макромолекулу (Hg2Sb2O7)n, как это показано на рисунке 2.4.
Наконец, возможна схема двумерной макромолекулы [(Hg2Sb2O7)n]m , что видно на рисунке 2.5:
Молекулу М на рисунке 2.5 точнее будет представить в форме такой же молекулы, но со связями– 7 отрицательных и 7 положительных, см. рисунок 2.5.1.
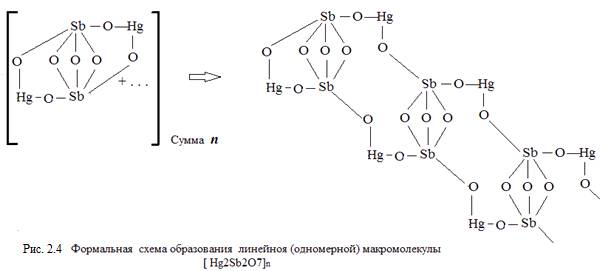
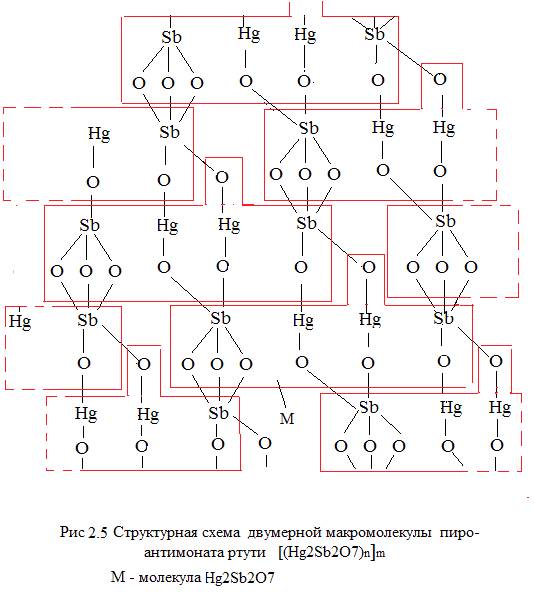
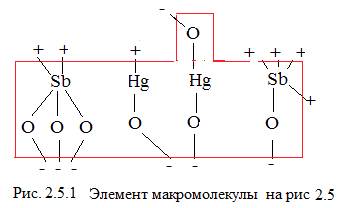
Можно построить молекулу Hg2Sb2O7 (из ионов в форме шаров), в определённом масштабе с учётом величин действительных радиусов ионов сурьмы, ртути и кислорода, рисунок 2.6.
«Удачное» сочетание размеров этих ионов делает молекулу пироантимоната в значительной степени компактной, как и двумерную макромолекулу полипироантимоната, см. рисунок 2.7. Можно предположить, что именно это может явиться причиной высокой плотности продукта (до 20 г/см3), который называют «красной» ртутью.
На очереди – построение структурной формулы и эскиза трёхмерной макромолекулы полипироантимоната ртути {[( Hg2Sb2O7)m]n}p.
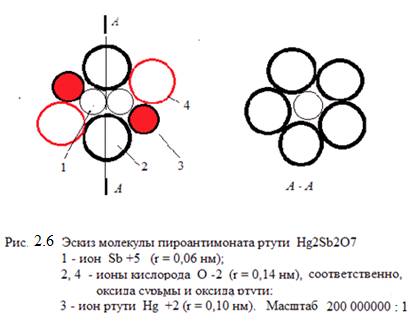
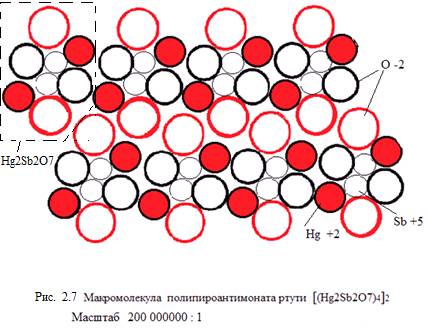
3. НЕКОТОРЫЕ ПРИЁМЫ ЗАЩИТЫ ПРИРОДЫ
3.1 Технологические схемы и балансы металлургической переработки
лома и отходов цветных металлов.
Из вторичного металлургического сырья, имеющего наибольший сбор (в виде лома и отходов), интерес представляют вторичный алюминий, медь и свинец. Эти виды сырья позволяют получить цветные металлы в сплавах алюминия, меди и свинца, а также соли свинца (последние – после разделки использованных свинцовых аккумуляторов).
Технологические схемы производства вторичных сплавов из лома и отходов основываются в первую очередь на выполнении требований ГОСТ 1639-93 «Лом и отходы цветных металлов и сплавов. Общие технические условия» и определяют выбор аппаратурного оформления процесса.
Ниже на рисунках 3.8 – 3.11 приведены технологические схемы подготовки к переработке и получения вторичных алюминиевых сплавов, получения медных сплавов, а также технологическая схема утилизации свинцовых аккумуляторных батарей.
В соответствии со схемами и на основании практических и расчётных данных составлены балансы алюминия, меди, свинца и сурьмы при переработке их (алюминия и меди) ломов и отходов, а также отработанных (и бракованных) свинцовых аккумуляторных батарей. Балансы даны в таблицах
3.1 – 3.3.
Приведенные данные явились основой для составления технологических инструкций с учётом современных требований к производству – рисунки 3.12 и 3.13.
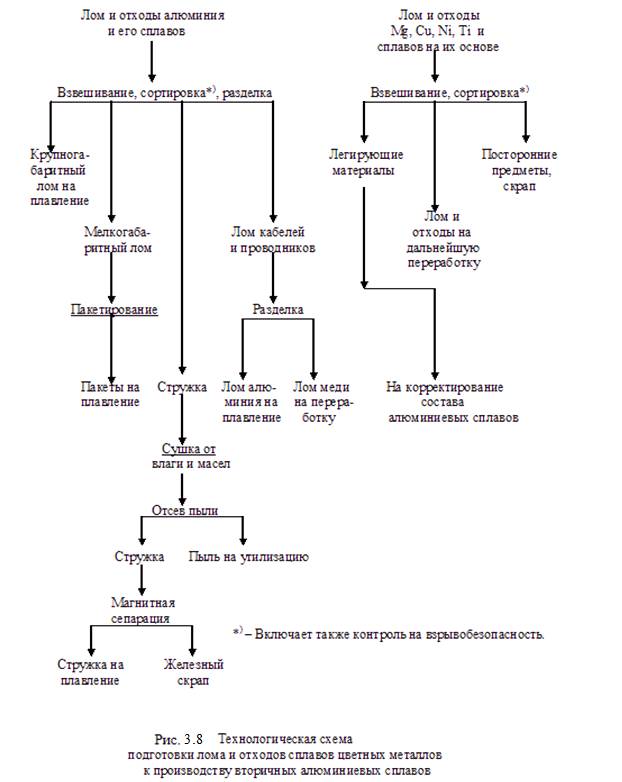
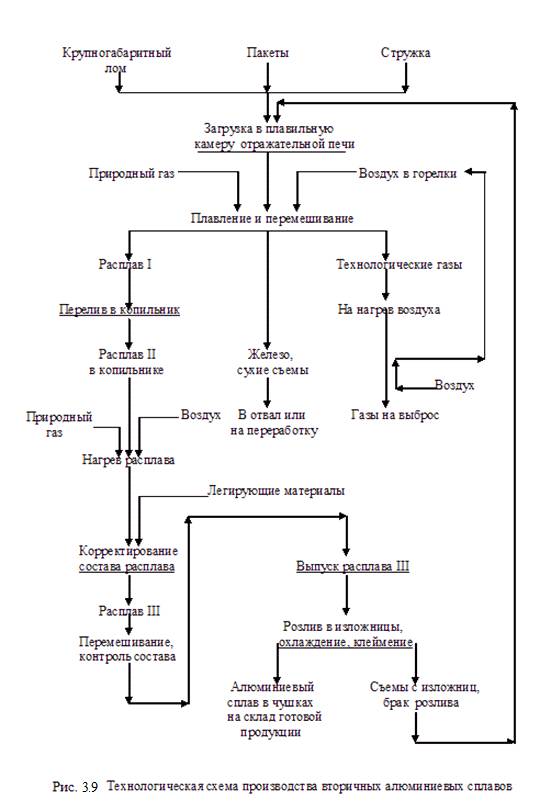
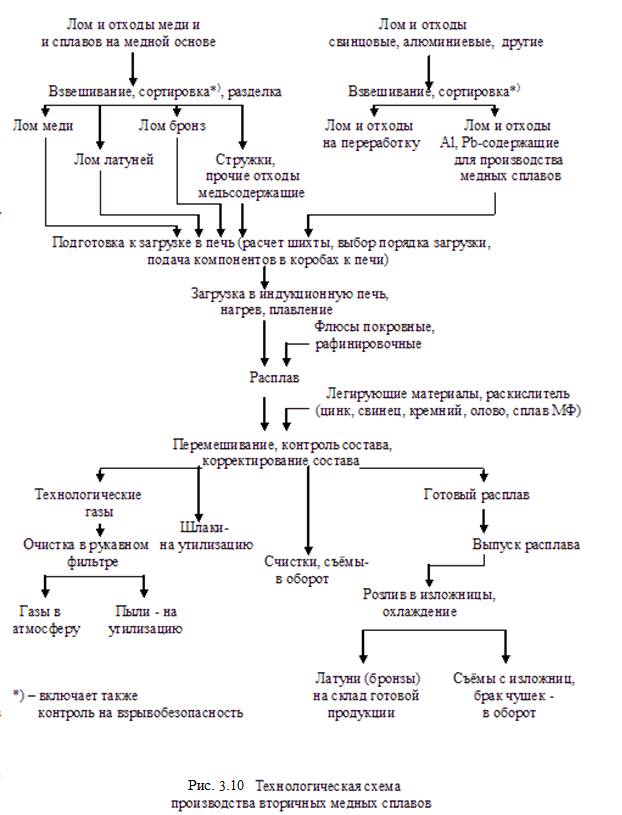
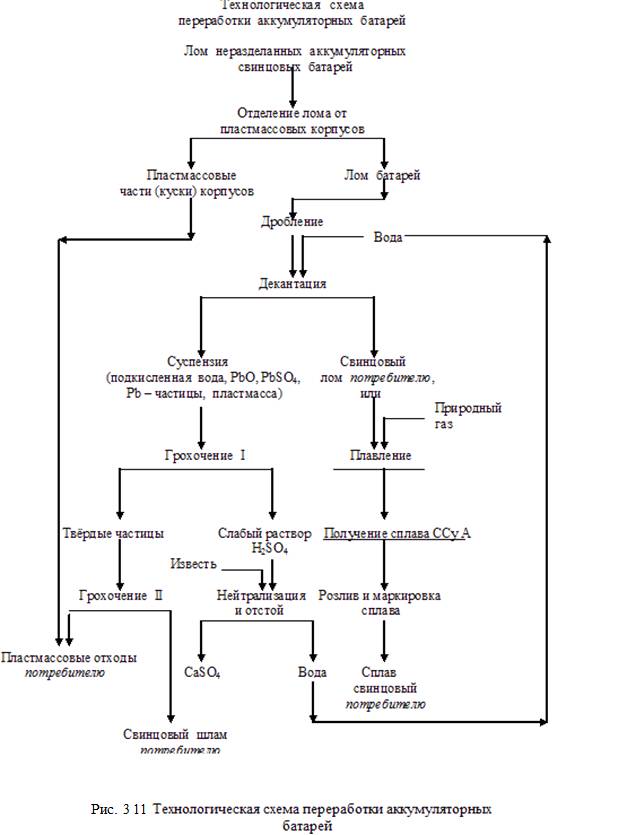
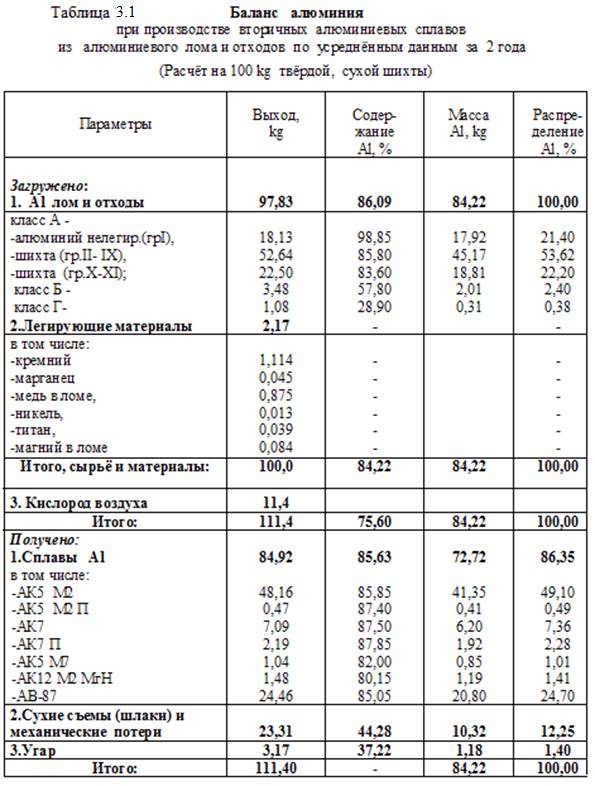
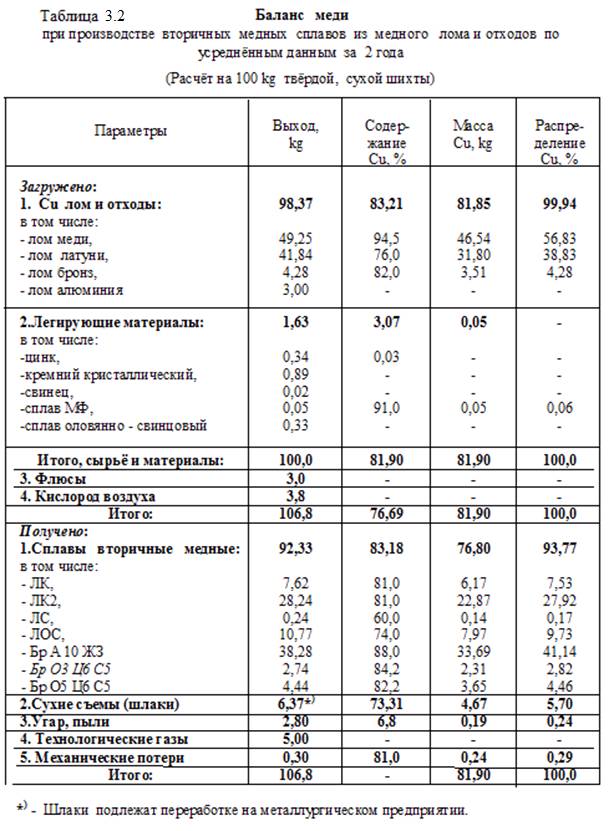
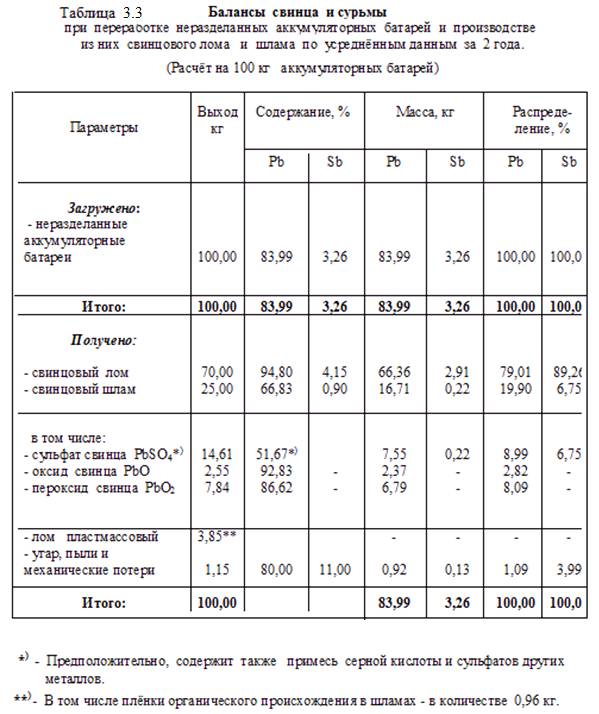
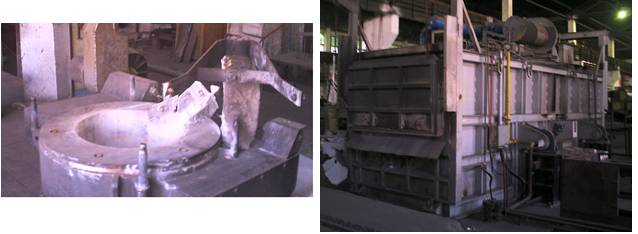
Рис. 3.12 Тигельная индукционная печь для выплавки медных сплавов
Рис. 3.13 Отражательная печь для выплавки алюминиевых сплавов
3.2 Экологически чистый способ утилизации ртутных люминесцентных ламп.
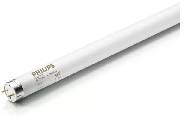
Линейная люминесцентная ртутная лампа
Демеркуризация ламп, как известно – это «обезртучивание» двух видов ламп: бракованных и отработанных. Бракованные лампы формируются при их производстве. Технология демеркуризации таких ламп заключается в механическом отделении стекло боя и колпачков (лампы предварительно дробят) от порошкового люминофора, куда переходит мелкокапельная ртуть.
Отделение проводят на мелкоячеистом вибросите. Ртутно-люминофорный шлам для обеззараживания смешивают, например, с серой, и, после его накопления в герметичных контейнерах, вывозят на специализированное предприятие для переработки. Стекло бой бракованных ламп, как и колпачки, могут быть использованы в обороте, [1].
Внешне достаточно простую и в чём-то привлекательную (на малой
площади можно поместить установку высокой производительности), не
требующую сложного оборудования, эту технологию, как нам представляется – необоснованно, применяют в некоторых регионах также для демеркуризации отработанных ламп. Почему этого делать не нужно и к чему может привести ?
При производстве ламп на заводе в них дозируют от 30 до 120 мг металлической жидко капельной ртути (другие технические решения здесь не рассматриваем). Лампы в среднем эксплуатируют в течение 10 тыс. часов. За это время:
– люминофор насыщается ртутью,
– ртуть диффундирует через его слой к внутренней поверхности колбы,
– ртуть сорбируется стеклом в приповерхностном слое стенок колбы.
Измерения содержания ртути в отмытом крепким раствором азотной кислоты от люминофора стекло бое отработанных люминесцентных ламп
показали, что концентрация ртути в нём изменяется от 10 до 50 мг/кг. В среднем она составляет 30 мг/кг и почти в 15 раз превышает ПДК ртути для почв.
Из баланса ртути при механическом способе демеркуризации
отработанных ламп (см. ниже) следует, что в стекло бой переходит более 11,5 % ртути от исходной (75 мг/лампу). Это снижает извлечение ртути в шлам до 88 %. Расчёт показывает, что при таком способе демеркуризации, например, одного млн. ламп (тип – ЛБ-40) в год, со стекло боем при сбросе в отвал перейдёт до 9 кг ртути.
Далее, распределённая в стекле на молекулярном уровне ртуть постепенно будет вымываться подкисленными водными стоками и при взаимодействии с почвой перейдёт в новые формы – ещё более ядовитые ртутно – органические соединения. Следовательно, такой стекло бой не является сбросным, и по существующим нормам, подлежит дальнейшей демеркуризации.
Альтернативным механическому является разработанный нами термо – химический способ демеркуризации отработанных ламп, [2,3]. Здесь вакуум колб и их нагрев до 350 0С используют для десорбции ртути из стекла, а обработка горячих колб химически активным по отношению к ртути раствором способствует и разрушению (дроблению) колб, и связыванию ртути в нетоксичное соединение.
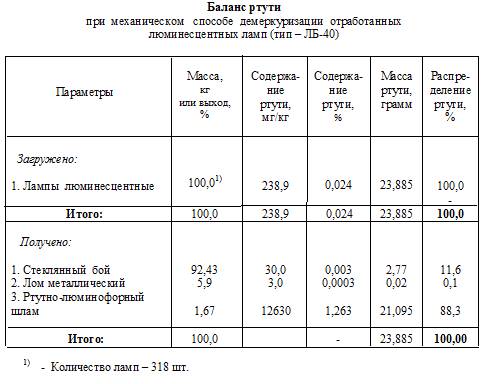
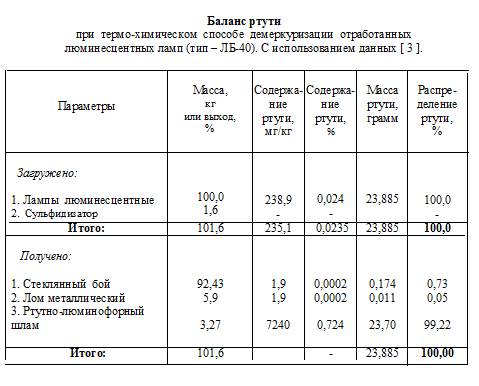
.
Из приведенного выше баланса ртути следует, что при термо – химическом способе в шлам удаётся извлечь более 99 % ртути и получить практически чистый по ртути стекло бой. Его можно не только без последствий для окружающей среды сбрасывать в отвал, но использовать в различных областях строительства, а также плавить в пламенных печах.
Термо-химический способ демеркуризации линейных ламп дневного света был успешно реализован на практике в Узбекистане: в г. Ташкенте (АСП СЭЛТА), [ 2 ] и в г. Зарафшане, ЦРУ НГМК, в 1997г.
Список источников, использованных в п. 3.2.
1. Фёдоров В.В. Производство люминесцентных ламп. М.: Энергия, 1981 г., 232 с.
2. Демеркуризация линейных люминесцентных ламп на опытно-промышленных установках "СЭЛТА" / Зайцев Н.Г., Хоменко С.Н., Раджабов Ю.Ш., Данилевская Е.В. и Мулява Г.С. // Сб. материалов III-й научно-технической конференции. "РТУТЬ, комплексная система безопасности". // С-Петербург:: РМА ГП "ВНИИ метрологии им. Д.И. Менделеева", НПО "Мониторинг", 1999 г.. 156 с.
3. К вопросу о выборе способа демеркуризации отработанных люминесцентных
низкого давления / Мулява Г.С., Зайцев Н.Г., Данилевская Е.В. // Там же.