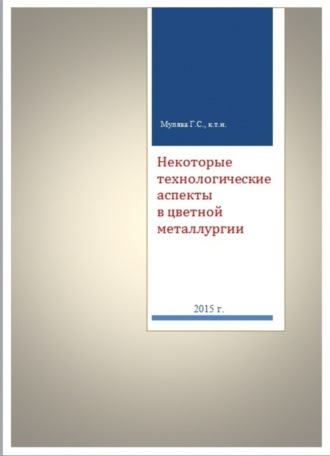
Полная версия
Некоторые технологические аспекты в цветной металлургии
Результаты расчётов экспериментальной степени перехода молибдена из огарка ППМ в водно-аммиачный раствор ŋэ Мо раств. по плану приведены в таблице 1.19.
По этим данным составлена таблица 1.20, где рассчитаны экспериментальные значения частных функций Y1, … Y6 от, соответственно, факторов Х1, … Х6. Результаты таблицы обработаны методом наименьших квадратов, определены частные функциональные зависимости и установлены их значимости вычислением коэффициентов корреляций. Получено, что для Y1, Y2, Y3 и Y4 коэффициенты корреляции меньше 0,3, что говорит о незначимости этих функций. Для Y5 иY6 они равны, соответственно, 0,912 и 0,821.
Частные уравнения:
Y5 = 0,856 – 0,00338*Х5,
Y6 = 0,513 + 0,0475 Х6.
Обобщённое уравнение:
У = (Y5* Y6)/0,654 = 0,672 – 0,00304 Х5 + 0,0622 Х6 – 0,000282 Х5 Х6. ( 11 )
или ŋэ Мо раств.= 0,672 – 0,00304СО2 + 0,0622ТНКО2 – 0,000282 СО2ТНКО2.
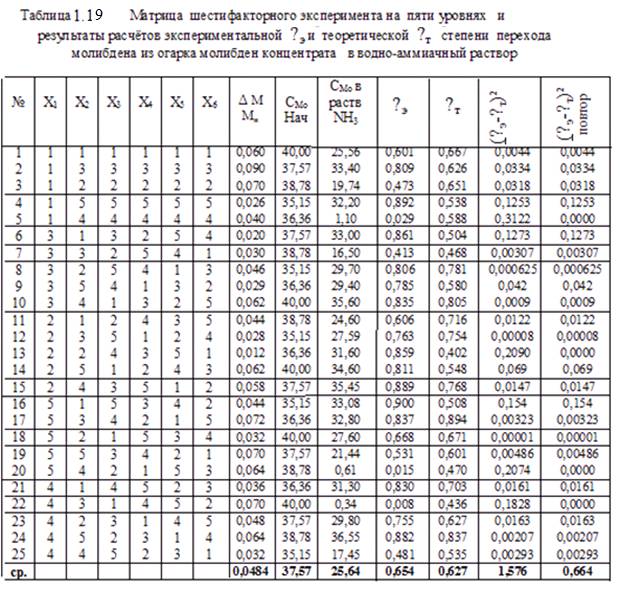
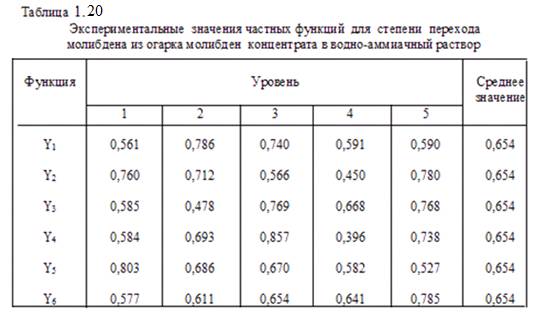
Ошибка уравнения ( 11 ) с поправками на грубые промахи – 18,7 %.
Получены экспериментальные данные и уравнение, из которых следует, что основными факторами, влияющими на степень перехода молибдена из огарка молибденитового концентрата в водно-аммиачный раствор являются концентрация кислорода в воздушно – кислородной смеси СО2 и количество кислорода в единицах ТНК для окисления MoS2 в концентрате – ТНКО2.
Температура обжига в выбранных пределах при проведении эксперимента по плану (500 – 700) 0С, время обжига (2 – 6) час, массовая доля каолина (1 – 13) % и диаметр гранул (2 – 10) мм практически не влияют на степень перехода молибдена в окисленные формы, растворимые в водном аммиаке.
С ростом концентрации кислорода в воздушно – кислородной смеси СО2 эта степень падает, а при повышении количества кислорода в смеси в единицах ТНКО2 – возрастает. Оптимальными в выбранных интервалах изменения при проведении эксперимента по плану являются СО2 = 20 % и ТНКО2 = 5. При этих значениях параметров степень перехода молибдена в окисленные формы. растворимые в аммиачном растворе, будет наибольшей и составит Уопт = 89,40%.
1.7.4 Относительные потери молибдена в возгоны (газы и пыль)
Относительные потери молибдена в возгоны рассчитывали по формуле:
ŋэ Мо в возг. = 1 – (1 – ΔМ/ М0) * (Мообщ к / Мообщ н), дол. един.,
где: ΔМ/ М0 – убыль массы навески гранул шихты при обжиге, дол. един.
Мо общ н – начальное содержание молибдена в шихте (до обжига), определяется с учётом степени «разубоживания» ППМ каолином, %,
Мо общ к – конечное содержание молибдена в огарке, %.
Результаты расчётов экспериментальных значений относительных потерь молибдена в возгоны при обжиге по плану приведены в таблице 1.21.
По данным ŋэ Мо в возг. составлена таблица 1.22, где приведены экспериментальные значения частных функций Y1, Y2 и т. д. от факторов Х1, Х2
определены частные функциональные зависимости и установлены их значимости.
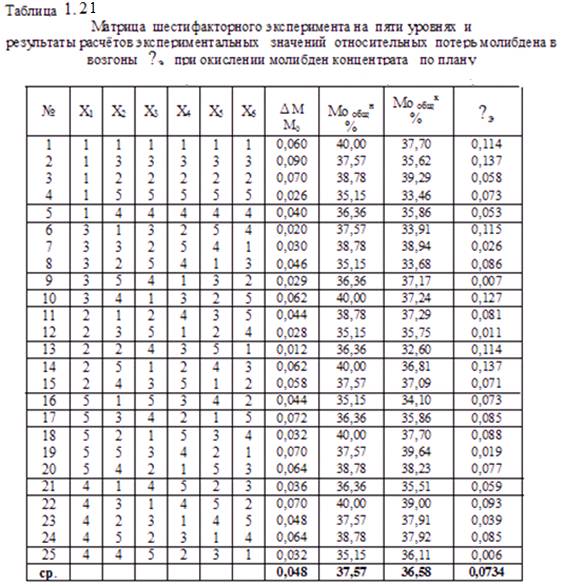
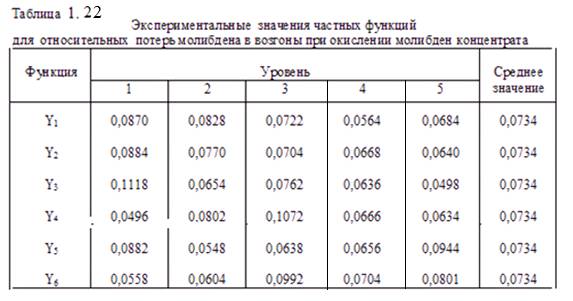
Результаты таблицы обработаны методом наименьших квадратов, определены частные функциональные зависимости и установлены их значимости вычислением коэффициентов корреляций. Получено, что для всех частных функций Yi коэффициенты корреляции меньше 0,3, что говорит о незначимости этих функций.
Следовательно, относительные потери молибдена в возгоны в выбранных интервалах изменения факторов: температуры (500 – 700) 0С, времени обжига в неподвижном слое (2 – 6) час, крупности гранул (2 – 10) мм, содержания в гранулах каолина (1 – 13) %, концентрации О2 в воздушно – кислородной смеси (20 – 100)% и количества кислорода в единицах ТНК (1 – 5) остаются практически близкими среднему значению – 0,0734 (или 7,34 %):
ŋэ Мо в возг. = 7,34 %. ( 12 )
1.7.5 Степень перехода рения в возгоны
Степень перехода рения в возгоны рассчитывали по формуле:
ŋэ Re в возг. = 1 – (1 – ΔМ/ М0) * (Re к / Re н), дол. един.,
где: ΔМ/ М0 – убыль массы навески гранул шихты при обжиге, дол. един.
Re н – начальное содержание рения в шихте (до обжига),
определяется с учётом степени «разубоживания» ППМ каолином, %,
Re к – конечное содержание рения в огарке, %.
Результаты расчётов экспериментальной степени перехода рения в возгоны ŋэ Re в возг по плану приведены в таблице 1.23.
По данным ŋэ составлена таблица 1.24, где приведены эксперимен-тальные значения частных функций Y1, Y2 и т. д. от, соответственно, факторов Х1, Х2 и т. д. Результаты таблицы обработаны методом наименьших квадратов, определены частные функциональные зависимости и установлены их значимости вычислением коэффициентов корреляций. Получено, что для Y2 – Y6 коэффициенты корреляции меньше 0,3, что говорит о незначимости этих функций. Для Y1 с коэффициентом корреляции 0,722 получено частное значимое уравнение
У1 = 0,627 – 0,0000264 * (Х1 – 575)2.
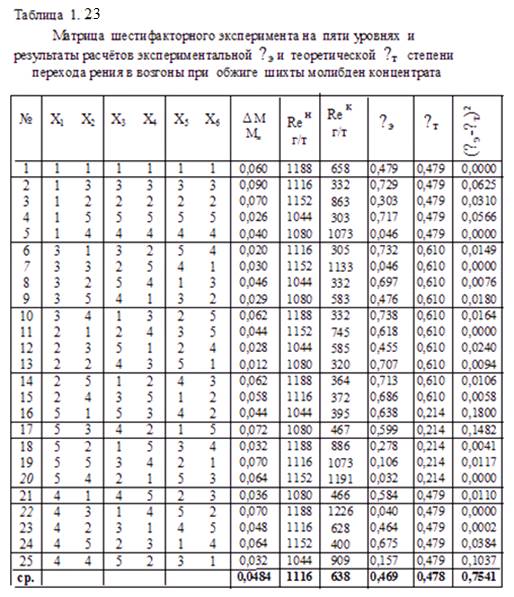
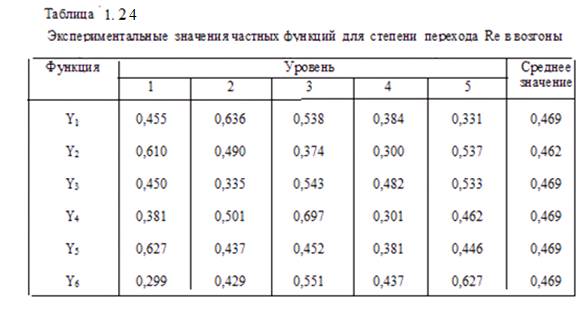
Обобщённое уравнение:
У = 0,627 – 0,0000264 * (Х1 – 575)2, дол. ед.,
или ŋэ Re в возг. = 0,627 – 0,0000264 * (Тобж – 575)2.
ŋэ Re в возг. max при Тобж = 575 0 С равно 0,627, дол. ед.
Ошибка У с поправками на грубые промахи – 19,9 %.
Получены экспериментальные данные и уравнение, из которых следует, что основным фактором, влияющими на степень перехода рения в возгоны при обжиге ППМ является температура обжига. В выбранных пределах при проведении эксперимента по плану: время обжига (2 – 6 ) час, массовая доля каолина (1-13) %, диаметр гранул (2 – 10 ) мм, концентрация кислорода в воздушно-кислородной смеси (20 – 100) % и количество кислорода в смеси в единицах ТНК (1 – 5) практически не влияют на степень перехода рения в возгоны.
Наоборот, при температуре Тобж = 575 0С извлечение рения в возгоны при обжиге шихты из ППМ и каолина в неподвижном гранулированном слое максимально и составляет, как было определено выше, 0,627 (или 62,7 %).
1.7.6 Обсуждение результатов
Выполненные исследования позволили установить новые закономерности. Так, нами получено, что со снижением концентрации кислорода в воздушно – кислородной смеси степень десульфуризации возрастает. Такой рост степени десульфуризации концентрата при прочих равных условиях можно объяснить появлением в воздушно – кислородной смеси в заданном интервале изменения концентраций О2 (20 – 100 %) возрастающего количества инертного газа – азота.
Присутствие движущегося над обжигаемым слоем гранул азота в незамкнутой реакционной системе (мы изучали обжиг при движении воздушно – кислородного и затем газового – кислородного – потоков) способствует ускорению отвода продуктов реакции (SO2) и, таким образом, смещению равновесия реакции окисления дисульфида молибдена вправо (известный эффект «газа – носителя»).
Конечно, если в такой воздушно – кислородной системе увеличивать количество кислорода (и пропорционально – азота), то процесс окисления пойдёт с ещё большей интенсивностью, что и получено нами, когда исследовали влияние роста количества кислорода в единицах ТНКО2 на степень окисления МоS2, см. уравнения выше.
При расчёте материального и теплового балансов печи для обжига молибден концентрата (см. далее), нами принято, что на обжиг шихты подаётся воздух, но в количестве, обеспечивающем массу кислорода в единицах ТНК для окисления МоS2 равным 5. Результаты расчёта показали несколько неожиданное значение скорости газов на выходе из печи – 5,8 см/сек.
Как раз такая скорость названа характерной в [2] при организации обжига молибденитовых концентратов в печи КС. Следовательно, выполненный нами эксперимент по плану в неподвижном слое показал такие оптимальные условия обжига (СО2 = 20, ТНКО2 = 5), которые приводят при их практической реализации к необходимости создания аппаратуры для окисления концентрата в «кипящем слое».
При этих значениях параметров степень десульфуризации будет наибольшей и составит Уопт = 87,90 %. ( наоборот, при СО2 = 100 и ТНКО2 = 5 , т.е. в чисто кислородной среде с избытком кислорода над ТНК в 5 раз, десульфуризация меньше и равна У = 59,3 %).
Аналогичные результаты, как и следовало ожидать, получены нами при изучении влияния параметров воздушно – кислородной смеси на степень перехода молибдена из огарка ППМ в водно – аммиачный раствор. Именно при обжиге в воздухе (концентрация кислорода СО2 = 20 %) и при превышении количества кислорода над необходимым над ТНК для окисления МоS2 в пять раз получены наилучшие результаты. Степень необходимого окисления дисульфида молибдена преимущественно в МоО3 (хорошо растворим в водном растворе аммиака; МоО2, например, практически нерастворим, [2]) достигла при этом 89,4 %.
Задачей окислительного обжига молибденитовых концентратов является не только десульфуризация и перевод MoS2 в МоО3, но и достижение максимально возможной степени возгонки рения в газовую фазу печи.
Нами в результате выполнения эксперимента по плану выявлено, что для возгонки рения оптимальной температурой является 5750С. При превышении этой температуры, как и при более низких температурах, степень возгонки рения существенно падает. Рост степени возгонки рения при подъёме температуры до 575 0С можно объяснить образованием вторичного семи оксида рения (за счёт окисления кислородом сформированных при 210 – 280 0С первичных ReO3 и ReO2) и разложением при 400 и 460 0С сформированных при более низких температурах перренатов железа и меди.
При превышении 575 0С в гранулах начинают преобладать процессы спекания, что способствует протеканию вновь реакций взаимодействия соединений рения (ReS2 и Re2O7) c МоО3 и МоS2 и образованию вторичных мало летучих оксидов ReO2 и ReO3 [3]. Не исключена также возможность образования перрената алюминия, связывающего часть рения в огарке.
Список источников, использованных в п.1.7
1. Малышев В.П. Математическое планирование металлургического и химического эксперимента // Изд-во «Наука» / Алма-Ата: 1973, С. 37.
2. Зеликман А.Н. Молибден // Изд-во «Металлургия» / М.: 1970. С. 440.
3. Лебедев К.Б. Рений // Изд. 2-е, перераб. и доп., «Металлургиздат»/М.:1963.С.206.
1.8 Окислительный обжиг арсенопиритного концентрата.
Что получим, добавив в медную шихту отражательной печи (ОП) арсенопиритный золотосодержащий концентрат? С очевидной целью – перевести золото концентрата в штейн, затем в черновую медь и, окончательно, сконцентрировать это золото в анодном шламе.
Рассмотрим поведение мышьяка при переработке в ОП шихты, если добавить в неё арсенопиритный концентрат.
Мышьяк арсенопирита в условиях обжига при плавлении шихты вначале окисляется до летучего три оксида по известной суммарной реакции [1] :
2 FeAsS + 5 O2 = Fe2 O3 + As2 O3 + 2 SO2 .
Часть три оксида мышьяка при повышенной температуре и избытке кислорода переводится в нелетучий пента оксид мышьяка:
As2 O3 + O2 = As2 O5.
Пента оксид мышьяка образует с окислами металлов, уже имеющимися в шихте, при (450 – 650) 0С соли мышьяковой кислоты – арсенаты:
3 CuO + As2 O5 = Cu3 (As O4 )2,
3 FeO + As2 O5 = Fe3 (As O4 )2.
Арсенаты – стойкие соединения, разлагающееся только при высокой температуре [2].
С ростом температуры пента оксид мышьяка разлагается с образованием летучего три оксида As2 O3 .
При (900 – 950) 0С в шихте как сульфид свинца PbS медных концентратов, так и сульфат PbSO4 , например, промпродуктов цинкового производства, добавляемых в медную шихту, в процессе реакций окисления и разложения преобразуются в жидкий оксид свинца PbO, который вступает во взаимодействие с арсенатами меди и железа:
Cu3 (As O4 )2 + PbOж = Pb3 (As O4 )2 + 3 CuО,
Fe3 (As O4 )2 + PbOж = Pb3 (As O4 )2 + 3 Fe О.
Таким образом, мышьяк в условиях окислительных процессов подготовки шихты к плавке в отражательной печи, является коллектором свинца.
При формировании в отражательной печи штейно-шлаковой фазы арсенаты свинца и непрореагировавшие арсенаты меди и железа частично растворяются в шлаке, частично – в штейне. При этом в штейне арсенаты восстанавливаются по реакции, аналогичной реакции в [3], например:
Pb3 (As O4 )2 + 4Cu2 S = 3Pb + 8Cu + 2As + 4SO2 .
При выпуске штейна, следовательно, в атмосферу цеха должны выделяться (по причине высокого давления) пары свинца и мышьяка. В черновой меди и затем анодном шламе повысится содержание свинца и мышьяка (в сравнении с плавлением шихты без арсенопиритного концентрата).
При выпуске шлака в атмосферу цеха будут выделяться летучие оксиды свинца и мышьяка от термического разложения арсенида свинца:
Pb3 (As O4 )2 = 3РbO + As2 O3 + О2.
(При 1200 0С давление пара РbO составляет 13 атм. [4]). В отвальных шлаках
при плавлении шихты с добавкой арсенопиритного концентрата должно быть повышенное содержание свинца и мышьяка.
Степень выделения мышьяка и свинца в атмосферу цеха и прирост массовых долей As и Pb в продуктах плавки, очевидно, будут повышаться при росте содержания арсенопирита и соединений свинца в шихте ОП.
Таким образом, добавка в медную шихту ОП арсенопиритного концентрата приведёт к резкому ухудшению санитарной обстановки в цехе, как, впрочем и вокруг завода (газовые выбросы в атмосферу). Кроме этого, ухудшится качество получаемой продукции.
Список источников, использованных в п. 1.8
1. Рцхиладзе В.Г. Мышьяк // Металлургия / М.: 1969. Стр. 37.
2. Лоскутов Ф.М. Металлургия свинца // Металлургия /М.: 1965. Стр. 101.
3. Металлургия меди. / Худяков И.Ф., Тихонов А.И. и др. Т.1.// Металлургия. – М.:
1977.Стр.165.
4. Физико-химические свойства окислов. / Справочник под. ред. Самсонова Г.В.//
Металлургия / М.: 1978. Стр. 167.
1.9 Окислительный обжиг больших количеств отработанной фотоплёнки
Одним из наиболее распространённых способов извлечения серебра из отходов фотоплёнки, в том числе использованной, является огневой способ. В промышленных установках, кроме непосредственно печи для сжигания плёнки и приёмника золы, должно быть пыле очистное устройство.
Это чаще всего жидкостный скруббер, снабжённый циркуляционным насосом, отстойником и форсунками для распыления жидкости. Используют раствор соды, что позволяет нейтрализовать кислые продукты огневой переработки. Ниже, рисунок 1.37, приведена схема цепи аппаратов установки, на которой было переработано 25 т фотоплёнки.
Продукты сжигания отходов – золу и обезвоженные кеки скруббера по партиям
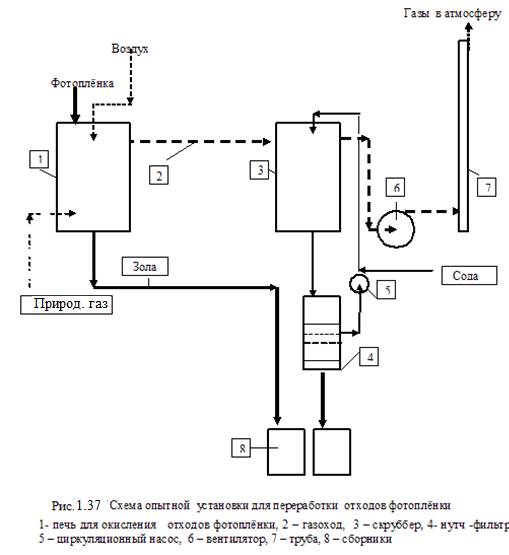
отдельно взвешивали, усредняли, разравнивали в тонкий слой и опробовали.
Провели работу по уточнению методик определения содержания серебра в плёнке общеизвестными приёмами: смывом с плёнки серебросодержащего желатинового слоя горячей водой (6 час) с добавкой затем для коагуляции соды или обработкой плёнки раствором азотной кислоты (разбавленной 1 : 1).
Растворы в обоих случаях получили мутные, плохо фильтруемые и практически непригодные для определения серебра на спектрофотометре. Из-за плохой фильтруемости в дальнейшем от применения щелочных растворов для обработки плёнки отказались. Азотнокислые растворы после отделения осадка анализировали на приборе АА-200 и получили рабочую концентрацию растворов по серебру – 180 – 190 мг/л.
Осадки после сушки и взвешивания подвергали шерберной плавке (метод
пробирного анализа) и затем купеляции веркблеев. Получили серебряные
корольки. Распределение серебра после промывки плёнки в кислый раствор составило 76 – 83 %, в осадки – 24 -17 % соответственно.
Партии отработанной фотоплёнки опробовали: случайно отбирали из мешка с отходами 2 – 3 листа фотоплёнки, их ножницами измельчали до крупности 7 – 10 мм, перемешивали и отбирали две параллельные навески массой 20 – 30 г. Навески подвергали тигельной плавке в шихте, включающей, кроме измельчённой фотоплёнки, глёт, соду и буру.
Кроме пробирных плавок, провели определение серебра в серебросодержащем шламе объёмно-аналитическим методом Фольгарда (сущность – в 4-часовом кипячении навески в смеси серной и азотной кислот). Хотя в литературе утверждается высокая точность метода, применяя его к золе от сжигания плёнки также в итоге получили серебросодержащие осадки, распределение серебра в которых составило только лишь 37,3 – 47,6 %. При таких данных приняли решение отказаться от метода Фольгарда и проводить прямую шерберную плавку золы. Продукты плавок – шлаки повторно проверили на содержание серебра и установили, что в них может оставаться до 13 % металла от исходного. Окончательно выбрали для анализов золы двойную шерберную плавку, купеляцию веркблеев и суммирование масс серебряных корольков.
Результаты измерений и анализов позволили составить баланс серебра при огневой переработке фотоплёнки, который приведен в таблице 1.25.
Работу по обжигу 25 т фотоплёнки проводили в две смены по 8 час. При производительности 132 кг/час обжиг занял по времени 1 квартал.
При составлении баланса недоставало данных по уносу серебра с выбросными газами. Их получили расчётным путём. Объём газов приравняли к объёму прокачиваемого через установку вентиляторного воздуха. Массу серебра с пылевыми выбросами определили по разнице массы серебра на входе (с плёнкой) и масс серебра с золой и кеком. Отнеся эту массу к объёму прокачиваемого воздуха (газов) получили 2,36 mg/m3 Порядок этого значения концентрации серебра в уносных газах соответствует, на наш взгляд, действительности. Интересно, что определение КПД скруббера с учётом расчётной массы выбросов дает значение 74 %. Это также близко действительному КПД. Конечно, для более точного баланса серебра требуется
разработка (несуществующей пока) методики контроля концентрации серебра
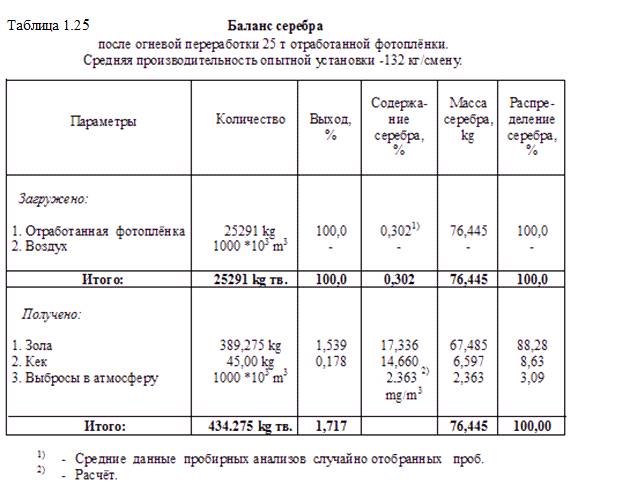
в пылегазовых выбросах.
Таким образом, балансовые испытания огневой переработки отработанной фотоплёнки показали, что в серебряный концентрат (золу и кеки) можно перевести до 97% металла. С учётом относительно небольших потерь серебра на специальном предприятии (при получении на нём слитков) видно, что коэффициент возврата серебра при огневой переработке плёнки может быть близок 95 %. Это значение существенно отличается от приведенных для РФ нормативов сдачи серебра после утилизации отработанной фотоплёнки – 66 %.
2. НЕОБЫЧНЫЕ СПОСОБЫ В ЦВЕТНОЙ МЕТАЛЛУРГИИ
2.1 Получение чистого медного купороса из шлаков плавки
сульфидных медных концентратов.
2.1.1 Исследование поведения меди и железа при кислотном
выщелачивании огарка от сульфатизирующего обжига шлакового
концентрата.
1. Методика исследований по плану.
Исследования проводили для шлакового концентрата (ШК), рациональный состав которого приведен в таблице 1.7. Там же для сравнения показан рациональный состав рудного концентрата.
Выше, п. 1.6, выполнены термодинамические расчёты и определены изобарно-изотермические потенциалы ZT для реакций окисления кислородом сульфидов меди и железа, характерных для шлакового концентрата, в интервале температур (673 – 1073) К.
Из расчётов следует, что при обжиге до 600 0С и достаточном количестве кислорода протекают реакции сульфатизации, а присутствие сульфида меди в форме борнита добавляет к сульфату меди также и оксид меди. При более высоких температурах обжига в продуктах реакций сульфат меди частично может быть замещен её ферритом.
Данные термодинамических расчётов позволили разработать методику экспериментов по извлечению меди из шлакового концентрата. Методика включает термообработку пробы концентрата в присутствии кислорода воздуха в течение заданного времени и агитационное выщелачивание огарков растворами серной кислоты при разных температурах и при добавлении окислителя. Последний применили для случаев, которые не могли быть полностью учтены в модели процесса (неполное окисление металлической меди, присутствующей в концентрате, появление металлической меди при растворении Cu2О, образование которой не исключено при окислении сульфидов меди).
Обжиг концентрата и выщелачивание огарка проводили в неподвижном тонком слое в лабораторной установке стандартного типа при подаче избытка воздуха.
Извлечение в раствор меди и железа исследовали методом математического планирования эксперимента. Изучали влияние шести факторов на пяти уровнях, см. таблицу 2.1.
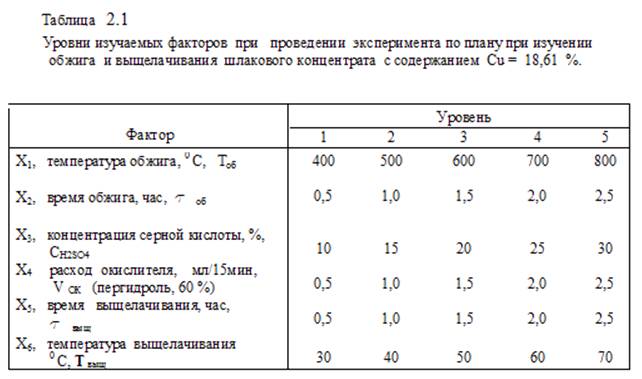
При обжиге ШК определяли влияние температуры и времени; при выщелачивании огарка исследовали влияние концентрации серной кислоты, расхода окислителя (концентрированная перекись водорода Н2О2, которую дозированно подавали в перемешиваемую пульпу каждые 15 мин), времени выщелачивания и температуры пульпы. Число оборотов мешалки лабораторного реактора – 180 мин-1.
После обжига огарки охлаждали в эксикаторе и затем определяли их массу. Взвешенные огарки хранили в герметичных условиях (в бюксах). После выщелачивания определяли массу сухих кеков, объём фильтрата, содержание в нём Cu и Fe. Контролировали в растворе также массовую долю Zn и Pb. Для повышения точности определения извлечения меди в раствор измеряли массовую долю меди в кеках.
2 Результаты исследований и их обработка
Матрица эксперимента по плану и результаты обжига шлакового концентрата и выщелачивания огарка приведены в таблице 2.2.
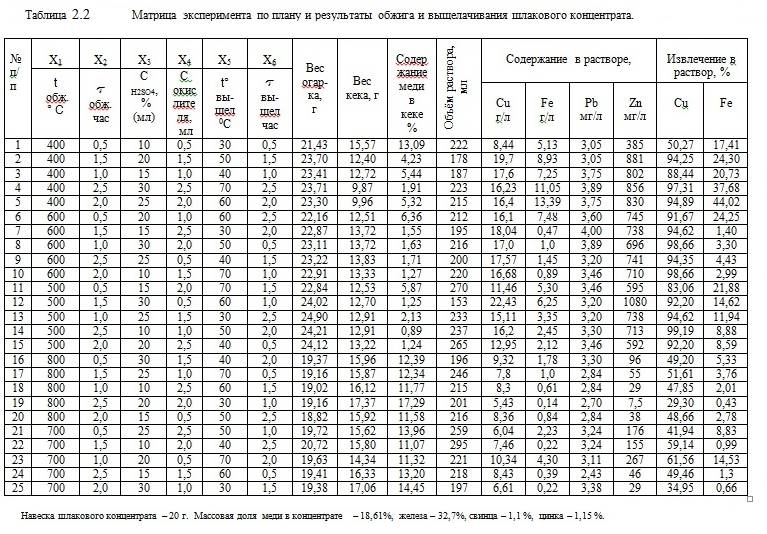
Результаты обработки данных эксперимента по плану показали следующее:
– обобщённое уравнение для определения извлечения меди из огарка шлакового концентрата в раствор при обжиге концентрата в интервале (400 – 600) 0 С имеет вид:
Y т = ( П Yi т ) / Y n – 1cр =
= 2,52 * 10-6 *[97,5 – 0,00093* (Х1 – 562)2] [78,62 – 11,545* (Х2 – 1,62)2]*
*[ 68,06 +0,266*Х3] [ 60,0 + 8,28*Х6], %, ( 1 )
и при обжиге в интервале (600 – 800) 0 С:
Y т = ( П Yi т ) / Y n – 1cр=
= 2,52 * 10-6 *[ 45,0 +0,00125* (Х1 – 800)2] [78,62– 11,545* (Х2 – 1,62)2]*
*[ 68,06 +0,266*Х3] [ 60,0 + 8,28*Х6], % . ( 2 )
Ошибка уравнений ( 1 ) и ( 2 ) +– 12,45 абс. %.
– Обобщённое уравнение для определения извлечения железа из огарка шлакового концентрата в раствор при обжиге концентрата в интервале
(400 – 800) 0 С:
Y т = П Yi т =
= 6,6*10-4 * [2,23 + 0,000146* (Х1 – 800)2] [15,0 – 0,041* (Х3 – 25)2 ]*
* [ -4,4 + 0,313 Х5 ] [ 3,87 + 4,85 Х6 ], %. ( 3 )
При оптимальных: температура обжига Х1 = 560 0С, время обжига Х2 = 1,62 час, концентрация серной кислоты Х3 = 30 %, температура выщелачивания Х5 = 300С и время выщелачивания Х6 = 2,5 час, когда расчётное извлечение меди в раствор достигает 100 %, расчётное извлечение железа в раствор равно:
Y т = 6,6 *10-4 * 11,35 * 13,98 * 4,99 * 16,00 = 8,37 %,
что, например, при Ж : Т = 2 даёт концентрацию железа в сульфатном медном растворе 13,73 г/л.