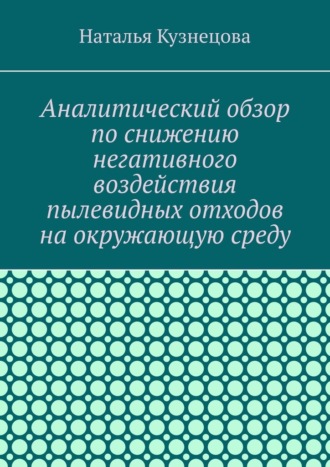
Полная версия
Аналитический обзор по снижению негативного воздействия пылевидных отходов на окружающую среду

Аналитический обзор по снижению негативного воздействия пылевидных отходов на окружающую среду
Наталья Кузнецова
© Наталья Кузнецова, 2024
ISBN 978-5-0064-8466-5
Создано в интеллектуальной издательской системе Ridero
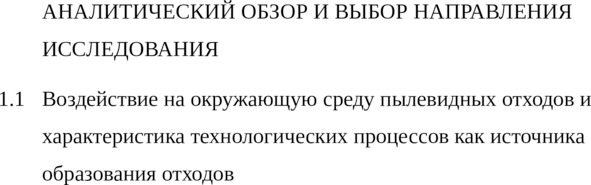
Значительная часть современных технологических процессов связана с изготовлением, переработкой, транспортированием и применением порошкообразных материалов, и сопровождается образованием большого количества пылевидных отходов. Недостаточное внимание к воздействию на окружающую среду пылевидных отходов, которые к тому же содержат ценные компоненты, несовершенство или высокая стоимость существующих систем разделения пылевидных отходов приводит к тому, что количество последних увеличивается. Неиспользуемые отходы производства в значительных количествах накапливаются в отвалах, что приводит к негативному воздействию на окружающую среду.
На территории России в отвалах накоплено около 80 млрд. т. различных твердых отходов [55, 103, 104, 106, 107, 114]. В связи с недостаточным количеством полигонов для складирования и захоронения промышленных отходов, широкое распространение получила практика размещения отходов в местах неорганизованного складирования (несанкционированные свалки), которые не отвечают действующим нормативам, представляя особую опасность для окружающей среды [30, 91, 108, 109]. Объемы размещения отходов на несанкционированных свалках, площади занятых под них земель постоянно растут, а, следовательно, растет и негативное воздействие на окружающую среду. Например, в Волгоградской области общая площадь только стихийных свалок превышает 400 тыс. кв. метров и складируется там более 100 тыс. т отходов [61]. А площадь санкционированных девяти полигонов промышленных отходов – около 210 га. Хранится на них приблизительно 50 млн. т. отходов и каждый год эта масса увеличивается еще на 2 млн. т. [61].
Положение с отходами производства выросло в огромную экологическую проблему, и необходимость ее решения обусловлена загрязнением окружающей среды и истощением природных ресурсов.
Технологические процессы производства строительных материалов сопровождаются образованием значительного количества пылевидных отходов, содержащих наряду с посторонними включениями, исходное сырье, которое может быть возвращено в производство. Извлечения посторонних включений позволяет, с одной стороны, снизить негативное воздействие отходов на окружающую среду, а с другой стороны обеспечить экономию минеральных природных ресурсов [68].

В Волгоградской области накоплено 1,657 млн. т. и ежегодно образуется 159 тыс. т. отходов производства щебня, содержащих щебень и глинистые частицы [114].
Сырьем для производства щебня (фракционного камня) служит горная масса. Добытый в карьере материал представляет собой смесь кусков различных размеров и формы. В горной массе находятся обычно различные примеси (ил, глина), содержание которых в товарном продукте недопустимо. Для того чтобы горную массу превратить в качественный материал, необходимо выполнить целый ряд технологических операций, основными из которых являются дробление и сортировка. [50].
По химическому составу породы состоят в основном из окиси кальция и окиси магния. Физико-механические свойства карбонатных пород характеризуются значительной неоднородностью. Плотность изменяется от 2,60 до 2,96 г/см3, объемная масса от 1,79 до 2,81 г/см3, пористость – от 35,5 до 1,1%, водопоглощение от 0,44 до 21,18%, прочность -от 31 до 1503 кгс/см2 в насыщенном водой состоянии. Коэффициент морозостойкости изменяется от 0,45 до 0,97. Эти данные [68] приведены для горной массы, добытой в карьере «Перекопский» Клетского района Волгоградской области
Технологический процесс производства щебня состоит в последовательном дроблении и сортировки. Дробильно-сортировочная установка состоит из следующих элементов: – питателя пластинчатого ТК-15А-01; агрегата крупного дробления СМ-16Д; грохота сортировки; агрегата передвижного среднего дробления СМД-131А; агрегата сортировки передвижного СМД —174 [50].
Установка оснащена металлоискателем, семью конвейерами ленточными ТК. Из карьера сырье доставляется автосамосвалами КРАЗ, КАМАЗ и ссыпается в приемный бункер установки, оттуда питателем подается на дробление. Продукт дробления подается на грохот сортировки, где происходит рассев на фракции 0¸10мм, 10¸20 мм; 20¸70мм. Фракции 0¸10мм, 10¸20 транспортируются на склад. Фракция 20¸70 мм поступает на агрегат среднего дробления СМД -131 А. На этом агрегате происходит дробление на фракции 20¸40 мм, 40¸70мм. Раздробленная порода подается на агрегат сортировки СМД-174. После сортировки фракции 20¸40 мм, 40¸70мм подаются на склад [35—37]. Схема производства щебня представлена на рис. 1.1. [35].
Отсевы карбонатной породы, образующиеся после грохочения, отбираются и отдаются в лабораторию на анализ на содержание пылеватых и глинистых частиц. Как правило, содержание пылеватых и глинистых частиц превышает 3% по массе, следовательно, такое сырье не пригодно для производства щебня [119—120] и направляется в отвал. Отсевы щебня складируются в карьерах, засоряя огромные территории, в то время, как отделение щебня от глинистых позволило сократить воздействие пылевидных отходов на окружающую среду, вернув их в производство.
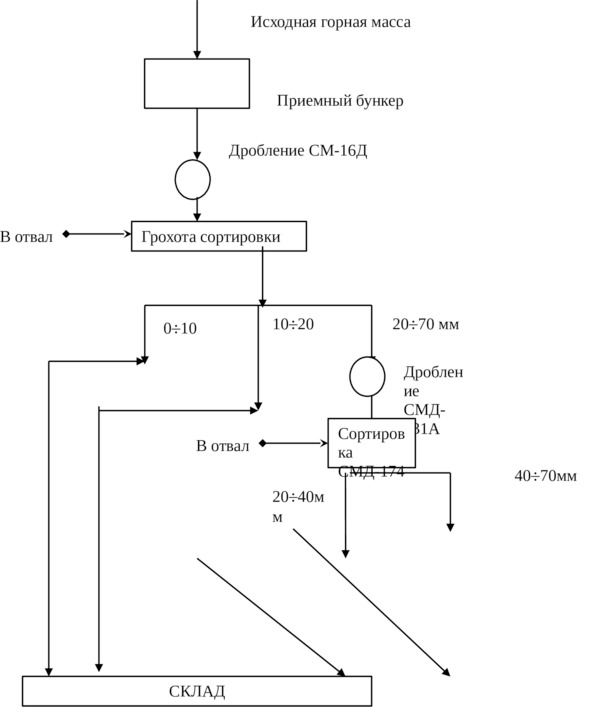
Рис. 1.1. Схема технологического процесса производства щебня [35].

В алюминиевом производстве на участке просева глиноземных сметок ежегодно образуется порядка 3750 т пылевидных отходов, содержащих ценное сырье —глинозем, наряду с посторонними включениями [45, 46]. Наличие посторонних включений препятствует их использованию в производстве, поэтому отходы направляются на полигон, что оказывает негативное воздействие на окружающую среду. Отделение глинозема от посторонних включений позволит сократить количество образующихся отходов за счет их частичного использования и снизить воздействие на окружающую среду, сохранив при этом ценные минеральные ресурсы.
В основе производства алюминия лежит электролиз криолито-глиноземных расплавов [9, 125]. Основным и самым дорогостоящим компонентом сырья является глинозем (Al2O3), который в России не производится и доставляется с Украины железнодорожным транспортом. Поэтому вопросы его рационального использования и возвращения в производство являются первоочередными.
Загрузка глинозема в электролизёр производится с помощью самоходных машин МРГ, МРС. Этот процесс сопровождается естественными потерями сырья [125]. Полы электролизного цеха снабжены решетками, для того чтобы просыпаемый глинозем собирался в специальном помещении нижнего уровня. Получаемый таким образом продукт, содержащий глинозем и 15% кремнезем с примесями, называют глиноземными сметками. Эта пылеглиноземная смесь собирается в мульды и транспортируется на участок просева глиноземных сметок, засыпается в бункер, оборудованный колосниковой решеткой [9, 1252]. Отделенная более мелкая фракция транспортером направляется на грохот. Просеянный продукт собирается в бункер. Глиноземные сметки, отделенные от крупных примесей, в настоящее время используют только в качестве насыпных подушек электролизеров. Однако, большая их часть сейчас направляется в отвал. Экономически целесообразно было бы часть данного продукта возвращать в электролитическое производство алюминия, однако это не допускается по ГОСТ 6912.1—93 из-за высокого содержания примесей [11]. Таким образом, ежегодно теряется значительное количество основного сырья производства первичного алюминия и возрастает техногенная нагрузка на окружающую среду. В связи с этим очень актуальной является проблема отделения глинозема от примесей.

Анализ технологических процессов позволил определить, что в производстве щебня и при просеве глиноземных сметок образуются пылевидные отходы, содержащие, наряду с исходным продуктом и посторонние включения, которые не позволяют их повторно использовать в производстве. Для снижения антропогенного воздействия на окружающую среду и сохранения минеральных ресурсов необходимо снизить количество образующихся пылевидных отходов посредством совершенствования системы их разделения.
В настоящее время для отделения твердых частиц применяются различные методы сепарации, в том числе магнитная, акустическая, электростатическая сепарация, разделение под действием гравитационных сил, центробежных сил, а также разделение по аэродинамическим свойствам пыли. В данной работе рассматриваются только сухие методы, поскольку применение мокрых методов сепарации делает невозможным или слишком сложным и дорогостоящим использование отделенных компонентов в производстве и промышленности строительных материалов.
Магнитная сепарация сыпучих материалов. Магнитные сепараторы – это многоцелевые системы, предназначенные для отделения магнитных примесей от немагнитных [59]. Различают магнитные сепараторы, использующие в своей работе постоянные магниты и электромагниты.
Магнитные сепараторы для сыпучих веществ обычно устанавливаются в трубопровод, по которому транспортируется сыпучий продукт. Сепараторы такого типа предназначены для удаления из сыпучих материалов случайно попавших железосодержащих примесей, при их небольших количествах. Магнитные системы генерируют неоднородное магнитное поле, которое отделяет и удерживает магнитные примеси на поверхности магнитных труб. Магнитный сепаратор необходимо периодически очищать от накопленных магнитных примесей. Это может производиться вручную, полуавтоматически и автоматически в зависимости от типа сепаратора.
В настоящее время используются следующие основные типы сепараторов на постоянных магнитах: барабанные сепараторы, плоские магнитные сепараторы, магнитные сепараторы из системы выдвижных решеток [59].
Существует большое разнообразие конструкций магнитных сепараторов [59]. Магнитный способ сепарации достигает большой эффективности в основном за счет интенсивной магнитной коагуляции, образуя агрегаты ферромагнитных частиц. Однако, во-первых, магнитная сепарация не позволяет разделять пылевидные отходы на фракции, а во-вторых, она применима только для отделения частиц, обладающих магнитными свойствами.
Сепарация в акустическом поле. В последние годы разделение пылегазовых потоков проводят с помощью акустических полей. Акустическая коагуляция осуществляется при воздействии на запыленный газ упругих колебаний звуковой и ультразвуковой частоты. Эти колебания вызывают вибрацию пыли, в результате чего растет число их столкновений. Процесс коагуляции происходит при силе звука не менее145—150 децибел и частоте 2—50кГц [53]. Скорость пылегазового потока не должна превышать при этом величины критической скорости, определяемой силами сцепления в данной неоднородной системе. Кроме того, концентрация дисперсной фазы должна быть в пределах 0,2—230 г/м3 [53]. Акустическая коагуляция находит промышленное применение для предварительной очистки горячих газовых потоков, а также при обработке газов в условиях повышенной опасности. Акустическая коагуляция также не позволяет классифицировать частицы по фракциям. Кроме того, этот метод применим для мелкодисперсной фракции.
Сепарация в электрическом поле. Сепарация в электрическом поле основана на том, что при поступлении пылевоздушной смеси в неоднородное электрическое поле в местах с большим напряжением образуются ионы, которые движутся в направлении осадительного электрода под воздействием сил поля [53, 126]. При движении эти ионы поглощаются частицами пыли, увеличивая их заряд. Заряженные частицы будут продолжать двигаться к осадительному электроду и оседать на нем. Учитывая, что частицы могут получать большие заряды, несмотря на малую массу, то и силы электрического поля намного больше инерционных и гравитационных. Но электрическая сепарация эффективна для частиц менее 10 мкм [53].
Конструкции и методы аэродинамического разделения сыпучих материалов на фракции. По способу перевода частиц в подвижное состояние различают механические (сита, грохоты, вибросепараторы) и аэродинамические классификаторы [15,20,21,36,44,47,50,58,64—67,76,83, 84,90,95.].
Разделение порошкообразных материалов на фракции просеиванием через сита является самым простым. Применяя сита с различными отверстиями можно разделить сыпучий материал на определенное количество фракций. Устройства, в которых идет процесс просеивания называют ситами или грохотами. Сита применяют в случае разделения мелкозернистых сыпучих материалов, а грохот при разделении крупнозернистых и кусковых материалов [26,42—44,50,83].
Выделяют колосниковые, валковые, качающиеся грохоты, гирационные грохоты, вибрационные грохоты, барабанные грохоты [64, 65, 83,].
Валковые грохоты имеют высокую производительность, устойчивы в работе и не дают динамических нагрузок, что позволяет их устанавливать в верхних этажах. Эти достоинства валковых грохотов, несмотря на некоторую сложность в изготовлении, способствуют их широкому распространению [83].
Из всех известных грохотов наиболее распространенными являются ситовые. Ситовые грохоты по конструктивным особенностям и устройству привода делятся на качающиеся, гирационные и вибрационные.
Барабанные грохоты являются динамически уравновешенными аппаратами. У них нет качающихся масс, таких как у плоских грохотов. Эта отличительная особенность позволяет устанавливать барабанные грохоты на верхних этажах, не опасаясь возникновения динамических нагрузок. Серьезным недостатком барабанных грохотов является низкий коэффициент использования поверхности сит. При заполнении барабана на 15—18% его объема поверхность сит используется всего на 20—30% [26,83].
Особенность вибрационных грохотов заключается в приводном механизме и обязательной установке короба на пружинящих опорах или пружинящих подвесках.
Вибгрохоты, использующие явление резонансного усиления амплитуды колебаний отдельных струн, обладают следующими недостатками: различная амплитуда колебаний струн по длине; необходимость поддержания одинаковости напряжения каждой струны в процессе всего времени эксплуатации; сильная зависимость амплитуды колебаний каждой струны от величины местной рабочей нагрузки [26,64,65,83]. При использовании прямого возбуждения просеивающей поверхности вибратором имеется другой недостаток-амплитуда уменьшается до нуля в направлении к месту крепления просеивающей поверхности к неподвижному коробу.
С целью ликвидации указанных недостатков предлагается [64] использовать дополнительные грузы, особым образом расположенные на струнной просеивающей поверхности. Особенность примененного магнитного вибратора состоит в том, что он выполнен как составная часть всего виброгрохота, что упрощает общую конструкцию и повышает надежность эксплуатации. Кроме того, отпадает необходимость поиска производителей надежных вибраторов подходящих типоразмеров.
С целью совершенствования технологии обогащения щебня создана конструкция спирального виброгрохота [65], который состоит из поверхности просеивания, представляющую собой упругую спираль, которая приводится в равномерное вращение вокруг собственной оси к колебательному движению приводными кулачками. Простота конструкции спирального виброгрохота позволяет его изготавливать, не применяя сложных технологических процессов.
Вибрационное грохочение гораздо выгоднее, чем другие виды грохочения, поскольку в процессе вибрационного перемещения по ситу грохота смесь сыпучего материала получает наилучшие условия для сепарации, так как вибрация способствует хорошему сортированию, самоочищению отверстий от застрявших в них частиц, разрыхлению слоя материала [26].
Конец ознакомительного фрагмента.
Текст предоставлен ООО «Литрес».
Прочитайте эту книгу целиком, купив полную легальную версию на Литрес.
Безопасно оплатить книгу можно банковской картой Visa, MasterCard, Maestro, со счета мобильного телефона, с платежного терминала, в салоне МТС или Связной, через PayPal, WebMoney, Яндекс.Деньги, QIWI Кошелек, бонусными картами или другим удобным Вам способом.