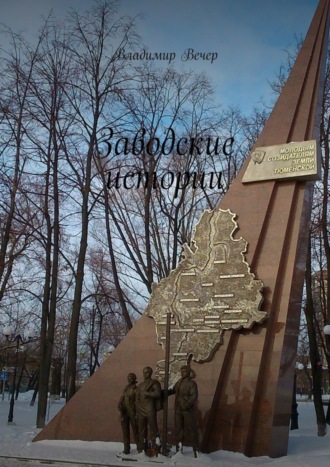
Полная версия
Заводские истории
Для выработки кислорода на Тобольском НХК был создан Азотно-кислородный цех (АКЦ). Закупили смонтированную на шасси двух автомобилей установку СКДС -70М для получения кислорода из воздуха. Такие установки выпускались для Советской Армии и предназначались для получения кислорода в условиях полевых мастерских.
Кислородоазотодобывающие станции типа АКДС-70, СКДС-70, МКДС-100К состоят из 2-х отделений:
– Компрессорное отделение, предназначено для получения сжатого воздуха.
– В технологическом отделении происходит осушка, очистка, ожижение и разделение воздуха на азот и кислород.
Оба отделения оснащены отопительной и вентиляционной системами, имеют естественное и искусственное освещение, а также систему охлаждения компрессоров.
Станция поставляется в комплекте с наполнительной рампой, что позволяет осуществлять заправку газовых баллонов до давления 150 атм.
Для получения максимального количества столь необходимого для стройки продукта оборудование сняли с автомобилей и установили на фундамент во временное здание цеха АКЦ. Подключили электродвигатель привода поршневого компрессорного детандера по постоянной схеме электропитания (т.е. не от дизель-генератора).
Детандер -это устройство в котором газ сжатый компрессором расширяется, при этом охлаждаясь до низких температур.
СКДС -70 М Производительность
Газообразный (м3/час) Азот (100),Кислород (70)
Жидкий (кг/час) Азот (70),Кислород (70)
Чистота получаемого газа (%)
Газообразный Азот (98—99),Кислород (99,2)
Жидкий Азот (98—99), Кислород (99,2)
На оборудовании круглосуточно в три смены выдавали «на гора» кислород (О2) уже работники комбината.
В помещении рядом с оборудованием стояли 2 обычные в квартирах, но странные здесь в цеху белые эмалированные ванны. Ванны всегда до краёв наполнены были чистой водопроводной водой. Было это предусмотрено для безопасности персонала, а не для обычных гигиенических процедур.
По инструкции оператор кислородной установки в случае воспламеннения на нём одежды должен прыгнуть и погрузиться в эту ванну с головой и этим прекратить возгорание.
Огнетушители в такой ситуации бесполезны.
Т.о. цех АКЦ начал полностью обеспечивать потребности строительно-монтажных организаций кислородом, а также первые вводимые в эксплуатацию объекты ТНХК сжатым воздухом для КИПиА (контрольно-измерительных приборов и автоматики).
Вскоре за этим возникла потребность в азоте (N2).
На схеме упрощённо показано, как получают кислород О2 в баллонах 150 атм. и газообразный азот N2
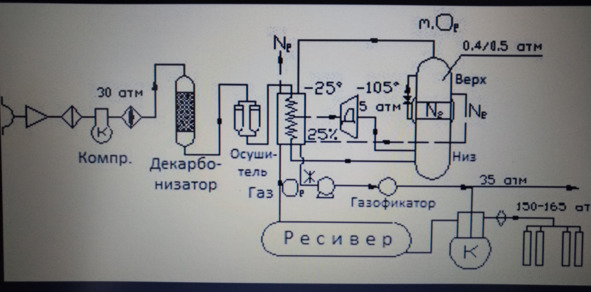
Схема 1. Получение кислород О2 и азот N2
К,к -поршневые компрессоры
Д -турбодетандер
Колонна ректификационная для разделения на жидкий кислород О2 и азот N2
Этот инертный газ (азот) требуется для опрессовки вновь вводимых в строй аппаратов и трубопроводов, для освобождения оборудования от продуктов в процессе производства, для ревизии и капитального ремонта.
Для получения N2 смонтировали и запустили турбодетандер из того же армейского комплекта. В отличии от поршневого детандера описанной выше установки получения О2, сжатый воздух от компрессора подавался на турбину детандера. Сжатый воздух в полостях вращающейся турбины эффективно расширялся при этом охлаждаясь переходил в жидкое состояние. Скорость вращения турбины измерялась с помощью датчика оборотов у торца оси турбины. По показаниям стрелочного индикатора, работавшего в паре с датчиком оператор вручную регулировал (устанавливал) нужное количество оборотов турбины в секунду. Турбинка была небольшая 15 см. в диаметре, но при потере контроля могла превысить обороты и «пойти в разнос». Температура перехода сжатого воздуха в жидкое состояние была порядка минус105—200градусов цельсия.
Вот с этим маленьким датчиком у меня была следующая история.
Ночной звонок диспетчера ТНХК. Полчаса поездки на диспетчерском автобусе из города в цех АКЦ. Вызов связан с отсутствием показаний оборотов турбины – толи она крутится, толи стоит. Короче не работает турбодетандер по получению азота.
Подобраться к датчику непросто из-за плотной теплоизоляции всей установки. Операторы вскрыли теплоизоляцию. Мы вместе с дежурным слесарем КИПиА сняли датчик оборотов. Проверка прибором показала обрыв катушки датчика. Катушка до того маленькая, а провод до того тонкий, что тоньше волоса человеческого. Если кто пробовал разбирать неисправные проводные наушники для смартфона – улитку в составе которой тоже катушка проводов миниатюрного звукового динамика, или если просто держал в руках те наушники, тот мог бы представить стоявшую перед нами задачу.
Что делать? Это теперь выбросил, купил новый наушник. А тогда, где было взять новый датчик?
В пору впасть в отчаяние: цех стоит, вопрос на контроле у Генерального директора. Разбираться не будут – кто виноват. Всем достанется.
Рядом со мной и слесарем КИП уже прибывший по вызову диспетчера начальник цеха КИПиА, Николай Иванович Савельев, говорит: _Кто-то этот датчик изготовил, кто-то сломал, кто-то же должен его починить!
И он сам взялся перематывать эту «художественную миниатюру». Вняли словам и примеру начальника и мы.
Без лупы и при слабом освещении, почти на коленке нашли оборванный волосок. Зачистили изоляцию проводка, обжали пассатижами присоединив к выводным клеммам датчика (паять нельзя – припой крошится при таких низких температурах), установили датчик на место, подключили провода к стрелочному индикатору показывающему обороты, восстановили теплоизоляцию, пустили воздух на турбину – работает.
И таких поломок датчика было ещё пару раз, пока технологи не научились аккуратно снимать и восстанавливать теплоизоляцию турбодетандера при профилактических работах.
Вот ещё была история
Декабрь месяц. Заканчиваются пусконаладочные работы (ПНР) на крупнейшей в СССР и в Мире ЦГФУ (центральной газофракционирующей установке). Вот вот предстоит приём сырья ШФЛУ (широкая фракция лёгких углеводородов).
И в это время случается отказ прибора «Флюорит» в цехе АКЦ.
Газоанализатор потоковый «Флюорит» предназначен для контроля (обнаружения) появления кислорода О2 в азоте N2, что недопустимо даже в микроскопических концентрациях.
Как гарантировать чистоту N2, когда газоанализатор сдох?
Прибор на заводе в единственном экземпляре и гарантийный срок у него ещё не истёк. Пришлось вскрыть корпус прибора, сорвав гарантийные пломбы. Осмотр внутренностей прибора ничего не даёт. Явных повреждений не обнаружено. А принципиальную электрическую схему завод изготовитель не выдаёт. Держит в секрете.
Принято решение – отправить прибор на ремонт на завод изготовитель в г. Ангарск.
Для ускорения направляют в командировку за 3000км в Сибирь инженера ответственного за работу КИПиА этого цеха т.е.меня.
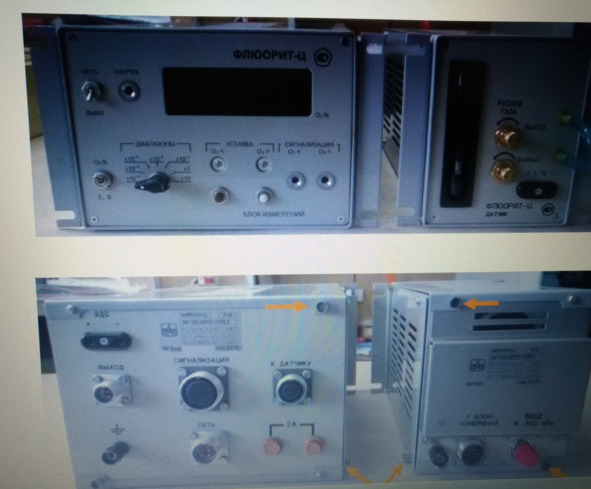
Газоанализатор Флюорит, лицевая и обратная стороны прибора.
Мой багаж это два места: блок датчика (160 х 145 х 340мм.) и измерительный блок (250 х 145 х 350мм.) газоанализатора «Флюорит» (килограмм десять будет). Правда я вынул эти блоки из общего корпуса газоанализатора, сократив вес на три килограмма. Сопроводительные документы: паспорт прибора, командировочное удостоверение и официальное письмо от руководства о важности и срочном восстановлении работоспособности газоанализатора.
Предпологаемая продолжительность командировки по маршруту: Тобольск-Тюмень поездом -12 часов, Тюмень-Иркутск самолётом 3 часа.
Но вот тут-то, как говорится, и была «собака зарыта».
Конец декабря 1985 года, морозы на всём огромном пространстве за Уралом. Вот приземлились мы (наш рейс) вместо Иркутска в Новосибирске и застряли надолго.
И не мы одни – скопилось в аэропорту много транзитных бортов. Как в воронку сваливались в а/п Толмачёво всё новые и новые самолёты.
Сидим, ждём у моря погоды. Никого не выпускают ни на Восток, ни на Запад.
Когда пошли вторые сутки сидения, сделал я отметку у нач. смены аэропорта о причине отказа от дальнейшего полёта (о возврате денег не шло и речи, но деньги-то казённые). Поехал на ж.д.Вокзал, купил билет на первый скорый поезд на Восток и через 12 часов сошёл в г. Ангарске.
Была первая половина дня субботы. ОКБА (опытно-конструкторское бюро автоматики) на пятидневке. Кого просить, кроме охраны на проходной?
Нашёл гостинницу, устроился, пообедал, взял в магазине колбаски на вечер. И тут у меня появилась идея: завтра воскресенье – надо съездить на о. Байкал. Иркутск от Ангарска недалеко, а там и до п. Листвянка на Байкале всего 70 км. Когда ещё появится такая возможность?
В те мои молодые годы я стремился везде побывать, всё повидать. Возможность появлялась только в каникулы, а затем на работе в короткие отпуска. Ещё командировки случались и были на расхват среди моих сверстников. Отслужившие в Армии, потом пол жизни вспоминали те годы и места, где им пришлось служить.
Вот один мой брат старший двоюродный, Валера, служил подводником в Приморье г. Находка, Дальний Восток.. Два других, Лёня и Саша, в Приамурье в Благовещенске, в разные годы и в разных видах войск: в пехоте и в ПВО.
В воскресенье я поехал на о. Байкал. Автобус привёз меня в пос. Листвянка где-то в час дня. Прямо на конечной остановке у берега озера вышел я на лёд. Прозрачный лёд через который видно дно на небольшой глубине. День морозный, над озером туман. Видимость 1- 2 километра. Подошёл к проруби, зачерпнул ладонью и попробовал на вкус Байкальской воды.
В посёлке ни автовокзала, ни гостиницы тогда ещё не было.
Я купил обратный билет и на том же автобусе через час поехал обратно в Иркутск. Посёлок Листвянка расположился у устья реки Ангары. Ангара единственная река вытекающая из Байкала, а впадает 336 рек и речек. Устье Ангары не замерзает даже в лютую стужу – километр в ширину и столько же в длину полынья. Над открытой водой испарения и промозглая сырость. Замёрз даже в «Икарусе» – самый комфортабельный в то время автобус, выпускали его в ВНР (Венгерской народной республике).
В понедельник в 8 часов был уже на проходной ОКБА. После оформления пропуска и документа на пронос моего прибора, сдал его на ремонт. По поводу отсутствия пломбы пришлось мне написать расписку о том, что поломка прибора в гарантийный срок эксплуатации. В общем к заводу претензий не имеется. Получил после обеда, но без новой гарантии ввиду отсутствия корпуса прибора. С исполнителями ремонта мне поговорить не довелось, а при беглом осмотре видна была свежая пайка микросхемы.
Билет на самолёт из Иркутска в Тюмень купил на вторник утром.
Взлетели, я спал себе не глядя на часы. А когда приземлились, гляжу – аэропорт-то не Тюменский. Стюардесса объявила, что по метеоусловиям теперь уже Тюмени нам предстоит подождать в Новосибирске.
Снова сидел в зале ожидания. Снова не отойди далеко от своего «бесценного» багажа. Народу в предновогоднюю неделю скопилось в а/п Толмачёво не мало. Свободных мест на скамьях нет. Только встанешь чтобы размять ноги, тут же займут твоё место.
Во второй половине дня объявляют: _Желающие вылететь в Омск пройдите к секции регистрации. Мгновенно образовалась очередь и Ту-134 заполнился до отказа. Мне и ещё многим не повезло.
Вскоре объявили дополнительный рейс на Омск на Ан-24. Вот на него я и сел. Ставить отметку в авиабилете об изменении маршрута у нач. смены аэропорта уже не было времени.
Взлетели, летели и сели почти что в сполшном тумане.
Омский аэропорт мне знаком, но тут что-то другое!
Стюардесса молчит. Потом объявила, что сели на аэродром Омского военного авиазавода, что у пилота здесь знакомый диспетчер. А тот самолёт Ту-134 вернулся назад в Новосибирск.
Значит теперь нам повезло!
На поле лётное подали автобус и предложили пассажирам продолжить путешествие в а/п г. Омска или на ж.д. вокзал. Кому как удобно. Отметку в билете о вынужденной остановке можно сделать в аэропорту или в городском агентстве Аэрофлота.
Я вышел на Вокзале чтобы не терять время на отметку в авиабилете об отказе от дальнейшего полёта по маршруту Иркутск-Тюмень.
Поездом доехал до Тюмени за 12 часов. Ещё 12 часов на поезд до Тобольска. не считая временных промежутков на ожидание своего рейса.
Поезд пришёл в Тобольск в 6 утра, и вызвав по телефону диспетчерский дежурный автобус, я поехал сразу на работу в цех АКЦ.
Включить прибор в работу вместе с дежурным слесарем КИП и убедиться в достоверности показаний газоанализатора было делом техники и нескольких минут. И на этом же автобусе отправился домой отсыпаться, доложив начальнику об окончании командировки.
На следующий день был обстоятельный письменный отчёт для бухгалтерии о моих «похождениях» с приложением всех проездных документов. Мои объяснения в необходимости всех моих пересадок и отсутствие отметок в билетах были приняты и я не остался в накладе, в смысле финансов конечно.
А от полученных впечатлений меня до сих пор прёт и плющит!
Циркониевая керамика
Фарфор, фаянс, хрусталь – это о посуде, а вот в химических лабораториях в большой цене стеклянные изделия. И в штате такой лаборатории стеклодув не менее ценен, чем опытный лаборант.
В производственных цехах есть приборы стационарные и переносные в конструкции которых присутствуют датчики из стекла и керамики.
Так вот в блок датчика (блок подготовки газа) описанного выше газоанализатора «Флюорит» входил, скорее всего и поныне входит циркониевый датчик – гальваническая ячейка из твёрдоэлектролитной трубки, точнее пробирки, на наружной и внутренней поверхности которой есть покрытие – электроды. Эта гальваническая ячейка похожа на одну банку автомобильного аккумулятора, тоже с двумя электродами, только вместо жидкого электролита твёрдый материал диоксид циркония ZrO2. Т.о. циркониевый датчик – это гальванический элемент из циркониевой керамики.
О важности показаний газоанализатора «Флюорит» сказано было ранее. Отказы в работе прибора продолжались и после выше описанного случая.
Приходилось устранять неисправности самостоятельно, на ходу и не оглядываясь на гарантии завода изготовителя. Гарантии отсутствовали, поскольку пломбы сорваны. Да и что бы дали эти гарантии – если сломался снова вези в Ангарск.
Вот, к примеру, была такая ситуация:
В первый раз этот отказ газоанализатора «Флюорит», как по «закону подлости», случился ночью. Осмотр показал, что неисправность связана с работой циркониевого датчика прибора. Возможно сам датчик исправен, но термостат в котором циркониевый датчик разогревается до температуры (634+/_ 1) град. С не работает. К слову сказать, именно при этой температуре, ни больше ни меньше даже на один градус, при попадании кислорода О2 в продукт производства – инертный газ азот N2 циркониевый датчик срабатывает, как гальванический элемент, выдавая ЭДС в милливольтах.
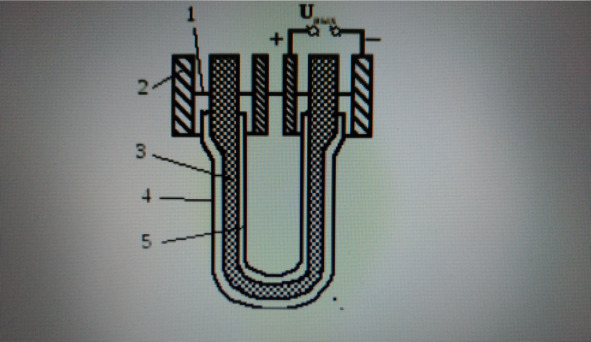
Рис.1 Датчик кислорода газа анализатора «Флюорит».
Описание Рис. 1. Устройство циркониевого датчика кислорода:
1. Электропроводное уплотнение.
2. Корпус.
3. Твердый электролит-циркониевая керамика. 4. Внешний электрод. 5. Внутренний электрод
Циркониевый датчик (рис. 1) имеет два электрода – внешний 4 и внутренний 5. Оба электрода выполнены из пористой платины или ее сплава и разделены слоем твердого электролита, которым является диоксид циркония ZrO2 с добавлением оксида иттрия Y2O3 для повышения ионной проводимости.
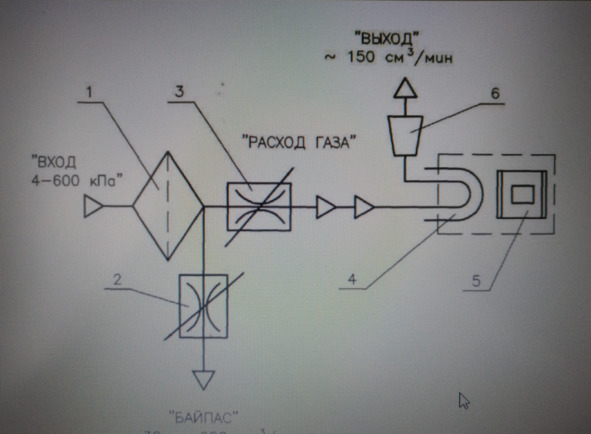
Сх.2 Блок подготовки газа анализатора «Флюорит».
Описание сх.2: 1. Фильтр, 2. Регулятор байпасного сброса, 3. Регулятор расхода газа, 4. Циркониевый датчик, 5. Термостат, 6. Ротаметр, индикатор расхода газа.
Подключаем вместо датчика температуры регулирующего работу термостата переносной потенциометр, задаём по градуировочной шкале термометра соответствующее этой температуре напряжение 1,99—2,00мВ (милливольта) – термостат разогревается и разогревает циркониевый датчик до малинового свечения «циркона» (рабочее название датчика из циркониевой керамики).
Вывод очевиден и прост – неисправен датчик температуры. В нашем случае это платина-платинородиевая термопара. Длина этого нестандартного бескорпусного датчика температуры 15 см. Чувствительный элемент термопары – горячий спай помещается в 1—2 мм от раскалённого датчика, а с холодных концов термопары снимаются показания в виде ЭДС (электродвижущая сила) в милливольтах, опираясь на которые электроника управляет работой термостата.
Вывод сделан, а где взять исправный датчик температуры?
В той ситуации мы поступили так:
1.Откусили пассатижами самый кончик термопары горячий спай – диаметром 2 мм.
2. Выполнили скрутку проводов на конце термопары длиной 2,5 мм.
3. Установили термопару в термостат, как указано выше и включили в работу прибор.
Термостат автоматически нагрел датчик до нужной температуры (634+/_1) град С, что визуально было видно по малиновому свечению «циркона».
У «Флюорита» несколько диапозонов измерения объёмной доли кислорода О2 в инертных газах и азоте N2.
В нашем случае использовалась шкала прибора в диапозоне: от 1х10 -3 до 0,01 об. доли О2, %.
Даже такая мизерная доля О2 в N2 не допускается.
Для периодического контроля работоспособности газоанализатора предусмотрен переход на следующий диапозон: от 1 до 100 об. доли О2,%.
При этом прибор показывал содержание кислорода О2 в атмосферном воздухе, а ОНО в атмосфере у поверхности ЗЕМЛИ (20,7 +/– 0,8) %.
О последствиях отравления парами азота думать не приходилось. Просто задерживал дыхание, когда подгонял расстояние термопары от корпуса «циркона» и настраивал его малиновое свечение при заданной температуре. Не в противогазе же работать, когда готов чуть-ли не влезть в корпус блока подготовки газа. А симптомы отравления следующие: Снижение работоспособности и сообразительности, избыточная болтливость и эйфория, головокружение, боли в груди и голове, слёзоточение, кашель, иногда отёк лёгких.
На пуске ЦГФУ
Пуск первого крупного объекта Тобольского нефтехимкомбината (ТНХК)
Центральной газофракционирующей установки (ЦГФУ) состоялся накануне и в Новогоднюю ночь 1985 года.
Автоматизированных систем управления ещё не было. Применялись пневматические приборы и средства автоматизации. Всё оборудование КИПиА было отечественного изготовления. Требовало больше людей и ресурсов при эксплуатации.
Взять в расчёт только КИПовцев: два сменных слесаря и мастер (две смены – 6 человек). Пять дневных и ст. мастер плюс нач. участка – 7 чел. Итого 13 человек непосредственно на пуске средств КИПиА установки ЦГФУ. Наладчики в день – 3 чел. Да с других участков присылали в помощь одного, двух. В общем вавилонское столпотворение!
Но и объект стоил того.
Десять лет прошло с тех пор, как в 1974 году было объявлено о начале строительства Тобольского нефтехимкомбината.
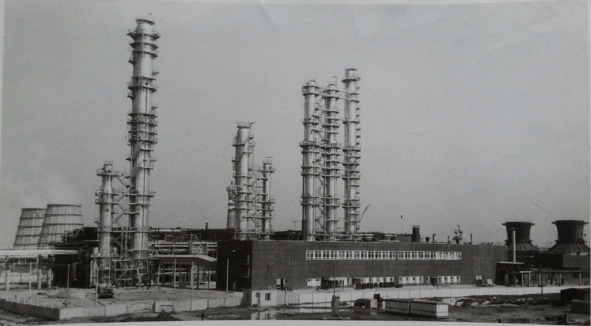
Пусконаладочные работы на ЦГФУ 1984 г.
Теперь предстоял пуск самой крупной в стране и в мире установки по разделению попутного нефтяного газа северных нефтяных месторождений на фракции пригодные для применения в народном хозяйстве.
Короче большое дело делалось и зачастую молодыми людьми.
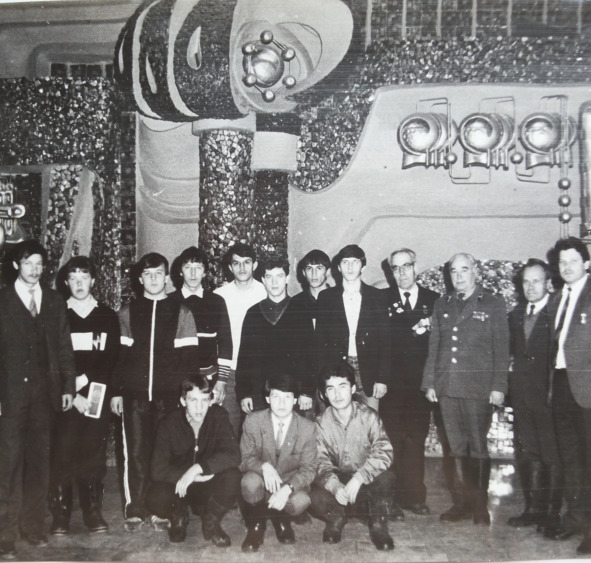
В фойе д/к«Комсомолец”молодёжь на встрече с ветеранами П. М. Вевчеренковым, С. С. Шабельяновым, А. Д. Сакериным.
Галиев Равиль Махмутович работал тогда старшим мастером КИПиА и оказался в этот момент скажем прямо на своём месте. Возникнут-ли вопросы у нач. смены ЦГФУ – к нему.
Утренний разбор произошедшего в ночную смену, доклад наверх и расстановка на работу дневного персонала – всё успевал.
Но особенно запомнился его подход к организации рабочих мест и ведению технической документации.
Кроме верстаков с тисами и столов для ремонта-настройки приборов, да стеллажей с резервными приборами, в мастерской участка никаких особенных стендов и приспособлений не было. Но расстановка даже этого имеющегося хозяйства характеризовала рациональный склад ума у парня. И участок КИПиА по праву называли -” Хозяйство Галиева».
К монтажным и принципиальным схемам, которые имели свои места в шкафу с документацией, непрерывно шёл поток людей разбирающихся и не сильно в них. И всегда главным арбитром в спорах был Равиль Галиев.
По своей инициативе, плюс ко всем чертежам, Равиль начертил альбом схем основных контуров управления технологическими аппаратами, насосными агрегатами и другими важными механизмами цеха.
Этот, затёртый от частого употребления, альбом схем многим помог разобраться в работе оборудования и средств автоматизации. Даже всезнающие пусконаладчики пользовались этим альбомом. Такой альбом схем был предвестником мнемосхем техпроцессов на экранах мониторов современных производств.
А на тот момент технологическим процессом ЦГФУ, цеха по разделению широкой фракции лёгких углеводородов (ШФЛУ) на этан, пропан, бутан, пентан персонал в ручном режиме управлял из центральной операторной посредством системы управления СУ ЦЕНТР. Причём эта СУ была полностью пневматическая и такие системы применялись на взрыво-пожароопасных производствах. В проект была заложена автоматизированная система управления технологическим процессом АСУ ТП на базе управляющих ЭВМ, но она так и не была реализована.
И не мудрено: наше научное и промышленное отставание в области АСУ ТП было заметным.
Хотя моя специальность и не была связана с электронно-вычислительными машинами, но ещё в институте у нас были занятия и решение курсовых заданий на ЭВМ. Самые передовые советские машины БЭСМ и ЕС ЭВМ занимали несколько комнат. Ввод расчётных данных своей курсовой я выполнял с помощью перфолент и перфокарт, которые набивал на специальном перфораторе.
ЭВМ тогда использовались в основном для расчётов фонда заработной платы персонала крупных промышленных предприятий, в работе Министерств и Генплана СССР.
Безопасность эксплуатации взрывопожароопасных объектов обеспечивалась массовым применением пневматических средств КИПиА. В контрольно-измерительных приборах и автоматике использовалась энергия сжатого воздуха – пневматическая энергия.
Конец ознакомительного фрагмента.
Текст предоставлен ООО «ЛитРес».
Прочитайте эту книгу целиком, купив полную легальную версию на ЛитРес.
Безопасно оплатить книгу можно банковской картой Visa, MasterCard, Maestro, со счета мобильного телефона, с платежного терминала, в салоне МТС или Связной, через PayPal, WebMoney, Яндекс.Деньги, QIWI Кошелек, бонусными картами или другим удобным Вам способом.