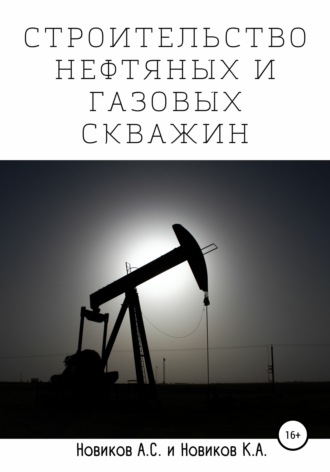
Полная версия
Строительство нефтяных и газовых скважин
Долота типа К – применяются для разбуривания самых твердых и крепких абразивных пород (хрупких) окременелых и кремнистых, мелкокристаллических известняков, доломитов, кварцитов, нитритов и др. Оснащен полусферическими зубками.
Долота типа ОК – предназначены для разбуривания очень крепких пород, сильно абразивных (горнорудная промышленность). Вылет зубка малый.
Шарошечными долотами бурили 90 % скважин на нефть и газ, в настоящее время долота PDC вытесняют повсеместно шарошечные долота. Несмотря на более высокую стоимость долот PDC, они эффективней шарошечных долот, но полностью заменить шарошечные не смогут. [48]
По конструкции корпуса шарошечных долот делятся на две группы: А – секционные долота от 46 до 346 мм, корпус сварной; Б – корпус целый, литой. Шарошки на долоте вращаются на шариковых и роликовых подшипниках. Шариковый также служит замком, удерживающим шарошку на цапфе. В зависимости от комбинации подшипников долота могут быть: низкооборотные, преобладают ролики, в шифре долота имеется буква Н; высокооборотные, преобладают шарики, в шифре имеется буква А; долота с герметизированной опорой, где подшипники герметизированы специальным сальниковым уплотнением, а смазка подается по каналам в лапах из специальной полости, в шифре присутствует ГНУ и ГАУ. У серии ГНУ – опора качения (ролики), ГАУ – опора скольжения. Характерная особенность долот этих серий: вращение долот невозможно без приложения начальной нагрузки. [9]
Компоновка узлов и деталей шарошечного долота приведена на Рис. 5.5.
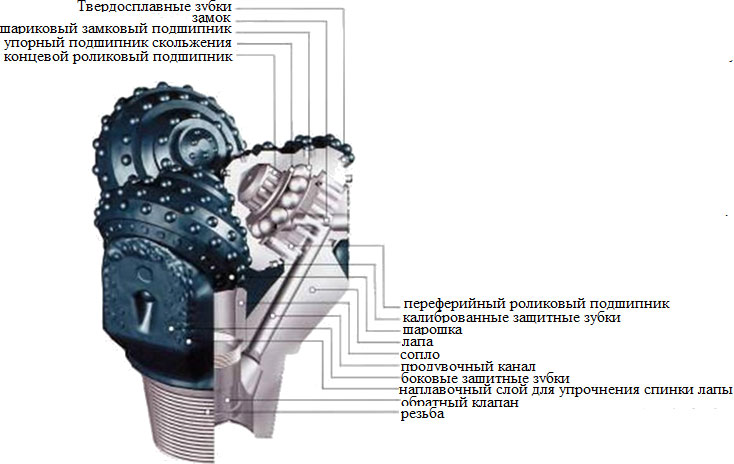
Рис. 5.5. Компановка шарошечного долота
Существуют различные виды узлов промывки: центральная, гидромониторная, асимметричная, с горизонтальным направлением одного сопла, с вертикальным направлением. Для гидромониторной промывки применяются насадки, изготовляются за рубежом из вольфрама кобальтового твердого сплава, устойчивого к абразивному износу, в России из металлокерамики. Диаметр и количество насадок рассчитываются для конкретных условий бурения, для создания гидромониторного эффекта и эффективной очистке забоя. Насадки могут быть мини удлиненные и макси удлиненные. Также изготавливаются щелевые насадки из высокопрочного чугуна. [9]
Ассортимент шарошечных долот достаточно велик. По диаметрам, диапазон долот составляет от 93 мм до 914,4 мм. Компанией Huges Christensen разработано гибридное долото на базе шарошечного и долота PDC рис. 5.6. По сравнению с обычными типами алмазных долот PDC, уровень крутильных колебаний в системе буровых долот Kymera на 50 процентов меньше, поэтому его называют динамически устойчивым. Предназначены для бурения в перемежающихся твердых абразивных породах, состоящая из сланцевой глины, песка, эрозионного гранита, плотного песчаного пропластка, известняка и ангидритов, перемежающихся породах. Прерывистое скольжение возникает только при низких оборотах вращения долота. Так же снижены вихреобразные возмущения при высоких оборотах вращения долота. [21]
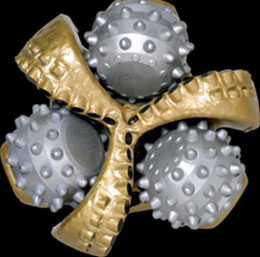
Рис. 5.6. Гибридное долото
§ 16. Кинематика шарошечного долота при бурении скважин
Шарошечное долото является своеобразным механизмом, преобразующим в процессе взаимодействия с забоем вращения бурильной колонны или вала забойного двигателя в продольные, крутильные, а в определенных условиях, поперечные колебания.
Сильные вибрации могут привести:
1. Разрушению бурильных труб;
2. Разрушению элементов вышки;
3. Повреждению забойных двигателей и забойной аппаратуры;
4. Увеличению диаметра скважины;
5. Преждевременному износу долота;
6. Снижению Vмex.;
При усилении вибраций и при отсутствии контроля за их уровнем, может возникнуть явление «резонанса», которое может привести к катастрофическим разрушениям элементов бурильных труб и долота. [54]
Продольные и крутильные колебания органически связаны со спецификой конструкции шарошечных долот и принципом их работы.
Колебания имеет волновую природу. [6] Они классифицируются на:
• Продольные;
• Поперечные;
• Крутильные;
Они возникают одновременно и зависят от волновой характеристики бурильной колонны и включенных в ее компоновку устройств (калибраторов, центраторов, демпферов, амортизаторов), типоразмера долота, свойств разбуриваемых пород, параметров режима бурения.
Основные причины возникновения колебаний:
• Скачкообразный характер разрушения горных пород;
Ухабистость забоя скважины, которая в свою очередь зависит от:
а) воздействия бурильной колонны на забой при ее продольных и крутильных колебаниях;
б) резких и частых изменениях параметров режима бурения;
в) неоднородности, трещиноватости, и резкой перемежаемости по твердости разбуриваемых пород;
г) различия давления под разными опорными зубцами долота, вызываемого:
1. Неравномерным износом цапф и деталей подшипников долота, приводящим к нарушению соосности геометрической оси шарошки с осью вращения, а как следствие, к неодинаковому динамическому нагружению разных опорных зубцов;
2. Неравномерным износом зубцов, приводящим к образованию разной площади контакта с породой;
3. Зубчатая рабочая поверхность долота; пульсация давления в нагнетательной системе;
4. Дискретную подачу инструмента и др.
Форма поверхности ухабообразного забоя может быть различной, но наиболее вероятной является волнообразная
Экспериментально установлены характеристики колебаний:
Частота продольных колебаний:
• Высокочастотные колебания – 110–170 Гц;
• Низкочастотные колебания – 3–20 Гц;
Частота крутильных колебаний:
• Низкочастотные – 6–16 Гц;
• Высокочастотные – 120–220 Гц;
• Промежуточные – 20–110 Гц;
Амплитуда продольных колебаний составляет 0,1–1 мм. Хотя абсолютные значения частоты для различных видов колебаний различный, однако, порядок числовых значений примерно одинаков. Поэтому колебания, в которых работает долото, можно разделить на две гармоники: – высокочастотную и низкочастотную. [54]
§ 17. Практические приемы и устройства для снижения воздействий вибраций при бурении
Практика показывает, что высокочастотные колебания бурильного инструмента, возникающие при перекатывании зубцов шарошки по забою скважины и недостаточные по амплитуде для объемного разрушения породы, могут быть без ущерба погашены. [54]
В этом случае опоры шарошек будут испытывать вибрации меньшей интенсивности и ресурс долота возрастет.
Низкочастотные колебания связаны с усилием прижатия бурильной колонны к стенкам скважины, носят релаксационный характер и полностью связаны по частоте и амплитуде с крутильными колебаниями.
По данным исследований, низкочастотные колебания по амплитуде в 1,3–2,6 раза превышают статические усилия нагружения долота бурильным инструментом. Эта нагрузка способна создавать усилия для объемного разрушения забоя скважины. Следовательно, эффективность работы долота при условии сохранения динамических импульсов, возникающих при воздействии низкочастотных колебаний бурильного инструмента, повышается. При возникновении вибраций необходимо:
• Заново приработать долото;
• Отбурить 1–1.5 м нового ствола;
• Остановить вращение на 15–30 сек. и промыть забой;
• Продолжить бурение на пониженных режимах;
• При продолжении вибраций изменить режим бурения – снизить об/мин и/или повысить нагрузку на забой;
Если принятые меры неэффективны, необходимо применять в КНБК над долотный амортизатор. Рекомендуется над долотный амортизатор устанавливать на некотором расстоянии от долота, для использования низкочастотных колебаний при разрушения породы.
Для гашения продольных и крутильных колебаний разработаны различные конструкции амортизаторов, демпферов. В качестве амортизирующего элемента используются эластомеры и пружины.
Увеличение количества промывочной жидкости, подаваемой на забой скважины, снижает амплитуду продольных колебаний;
Неравномерность нагрузки на долото увеличивает амплитуду крутильных колебаний;
Поперечные колебания можно снять установкой полноразмерного над долотного калибратора, если это не спровоцирует рост зенитного угла скважины.
Если, самые высокие значения механической скорости проходки (ROP) достигаются при использовании нескольких комбинаций, нагрузка на долото (и обороты долота), то всегда нужно использовать наименьшую по величине комбинацию, что позволит снизить вероятность возникновения вибраций.
В крепких породах вероятность возникновения вибраций достаточно велика, поэтому необходимо при переходе из мягких пород в твердые, снижать скорость вращения долота, и проводить тест по подбору режима бурения. Максимальная скорость проходки должна быть при минимальных вибрациях. Из практики известно, что при возникновении осевых вибраций, уход в сторону снижения осевой нагрузки и оборотов ротора до 40–60 об/мин, устраняет вибрации, но снижает механическую скорость проходки. Увеличение скорости вращения ротора до 200 об/мин, так же устраняет вибрации, при увеличении мех, скорости проходки, но риск слома бурильных труб и УБТ возрастает. [54]
§ 18. Долота истирающего типа
Алмазные долота – применяются для нижних интервалов бурения, в малоабразивных и абразивных породах твердых и средней твердости (известняки, аргиллиты, плотные глины, ангидриты, доломиты, песчаники и др., где проходка на шарошечные долота 5–10 м). Изготовляются диаметрами: 140; 159; 188; 214,3; 241; 267 мм:
a. Однослойные:
b. Радиальные;
c. Ступенчатые;
d. Ступенчатые с шаровыми выступами;
e. Импрегнированные с примерно равномерным распределением в матрице (слой 5–6 мм) зерен алмазов.
К конструктивным элементам относятся: сорт, размер, форма и выступление из матрицы зерен алмазов, конструкция центральной и торцевой части, высота калибрующей поверхности, твердость и абразивная стойкость матрицы, а также конструкция промывочных узлов. В долотах обычно используют наименее ценную разновидность природного алмаза (самого твердого минерала), именуемую карбонатом, карбонадо (бразильские технические алмазы) или черным алмазом. Но цвет алмазов этой разновидности может изменяться от черного до темно-коричневого, серого и серовато-зеленого в зависимости от присутствия тех или иных примесей. Перед использованием в буровых долотах природные алмазы обычно окатывают (овализуют) путем трения алмаза об алмаз. В результате такой обработки получают более прочные овализованные алмазы, подверженные раскалыванию в меньшей степени, чем остроугольные.
По размещению алмазов в матрице различают две разновидности долот: однослойное и многослойное, т. е. с импрегнированными алмазами (Рис. 5.7). Однослойные долота получают при однослойной укладке относительно крупных алмазов в графитовую пресс-форму, что приводит к их распределению в определенном порядке на поверхности матрицы, а импрегнированные – при равномерном перемешивании алмазов (как правило, мелких и невысокого качества) с частицами карбида вольфрама и другими компонентами матрицы перед спеканием долота. В импрегнированных долотах алмазы перемешаны с матрицей. Долото так спроектировано, что изношенные алмазы будут постепенно выпадать из долота по мере износа матрицы. Следовательно, стойкость таких долот существенно выше чем традиционных, а МСП не должна уменьшаться. [9]
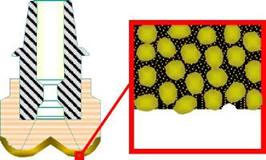
Рис. 5.7. Импрегнированные алмазные долота
Для различной твердости пород существуют различные профили. Кроме того, используется азное число и размер лопастей. Для более твердых и перереслаивающихся пород используется средний более плоский и круглый профиль. Количество лопастей увеличено.
Технические показатели алмазных долот во многом зависят от качества и размеров алмазов. Качество определяют группой и категорией, а размер – числом камней на 1 кар (0,2 г). Работоспособность алмазного долота в наибольшей степени, чем инструмента любого другого вида, зависит от чистоты ствола и забоя и качества промывки. При наличии металла или твердого сплава (даже в малом количестве), или крупных обломков крепких пород на забое происходит образование выбоин, выкрашивание или раскалывание алмазов и быстрое разрушение долота. При недостатке бурового раствора наблюдается перегревание и растрескивание (прижог) алмазов.
Долота ИСМ – отличие от алмазных: сверхтвердый материал, которым оснащены вставки (породоразрушающие элементы). Этот материал называется славутичем. Характерное отличие – высокая износостойкость. Выпускаются три разновидности: режущие, торцевые (зарезные), истирающие. В настоящее время ведется работа по изготовлению долот ИСМ для твердых абразивных пород. В отличие от алмазных долот, ИСМ более дешевые, меньше эффект поршневания, устойчивы от разрушения при работе по металлу. Существует метод повышения стойкости долот ИСМ за счет охлаждения в жидком азоте. [62] При опытной отработке 12 долот на Усинском нефтяном месторождении, стойкость увеличилась в среднем в четыре раза. При отработке серийных долот изнашивалась матрица долота – образовывалась кольцевая выработка, происходил рост давления на насосе, рейс прекращался. В Оренбургской области было отработано долото PDC, при износе резцов корпус долота не износился, долото было обработано жидким азотом. На опытных образцах это явления происходило тоже. Исследованиями, установлены причины улучшения показателей работы долот, не только ИСМ, но и шарошечных долот за счет фазовых превращений металла.
Испытания показали, криогенная обработка – цементированной стали, несколько повышает ее износостойкость при ударно-усталостном изнашивании. Повышает твердость и прочность цементированного слоя и снижает содержание остаточного аустенита его структуре, в результате криогенной обработки не приводит повышению хрупкости. Кроме того, как следует из анализа фрактограмм, у обработанных холодом образцов наблюдается более вязкое разрушение поверхности при ударе, что приводит к повышению износостойкости. Криогенная обработка не ухудшила свойства герметизирующих материалов и смазочных материалов опор долота.
Учитывая, что затраты на криогенную обработку долот невелики, такой вид обработки был бы целесообразен
§ 19. Особенности эксплуатации алмазных долот
Область применения алмазных долот – крепкие абразивные породы. Особенностью отработки алмазных долот является износ по диаметру, что в песчаниках является проблемой. Расширку при этом, можно производить только шарошечным долотом, имеющими ограниченный ресурс, поэтому нужно заранее знать ресурс алмазного долота по диаметру, инженеру необходимо лично присутствовать при навороте, спуске и замере диаметра долота. При расширке шарошечным долотом велика вероятность оставления шарошек (если ресурс определен неправильно) и заклинке долота, поэтому инженер должен лично присутствовать при этой операции. Перед спуском алмазного долота в скважину, ствол скважины проверяется на наличие сужений, особенно в крепких породах (места сужений прорабатываются шарошечными долотами), забой скважины очищается от металла, при помощи забойных шламометаллоуловителей и магнитных фрезов. Структурно-механические свойства бурового раствора доводятся до минимально допустимых значений. Спуск алмазного долота производится на ограниченной скорости. Нагрузка на алмазное долото, по сравнению с шарошечными значительно ниже и составляют 5–8 т.с. Требуют высоких скоростей вращения инструмента, при ограниченных нагрузках. Недостаки-очень низкая механическая скорость проходки. [62]
Ассортимент алмазных долотДолота типа М – для бурения мягких пород, однослойные. Матрица тороидально-ступенчатая, выпускается пять размеров: ДК-188М6, ДК241М6, ДК267М6, ДК292М6. Д – алмазное долото, К – ступенчатый профиль, 188 – диаметр долота, М – тип долота, 6 – порядковый номер модификации.
Долота типа С – для бурения средних пород, изготавливаются как однослойные, так и импрегнированные. Выпускают три размера: 138, 149, 188;
Импрегнированные долота типа С – 7–8 мм рабочий слой, форма ступенчатая, выпускают два размера: ДИ188С6, ДИ212С6.
Долота типа СТ – для бурения среднетвердых пород; однослойные, радиальные, изготавливают четыре размера: ДР159СТ1.[9]
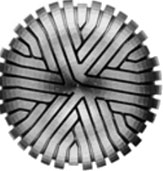
Рис. 5.8. Алмазное долото
§ 20. Долота типа PDC
Новым типом породоразрушающего инструмента являются долота оснащенными резцами PDC. Рис. 52 Изначально область их применения – бурение в мягких породах, разработчики долот успешно проектируют и начинают опробовать долота PDC в средних и твердых породах и даже абразивных. Преимущества долот PDC перед шарошечными долотами:
1. Отсутствие опоры долота;
2. Более высокая механическая скорость проходки;
3. Более высокая стойкость и соответственно проходка на долото по сравнению с шарошечными долотами;
4. При правильном выборе интервала применения долот PDC, значительная их экономическая эффективность по сравнению с шарошечными долотами и долотами истирающего типа.
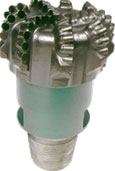
Рис. 5.10. Долото PDC
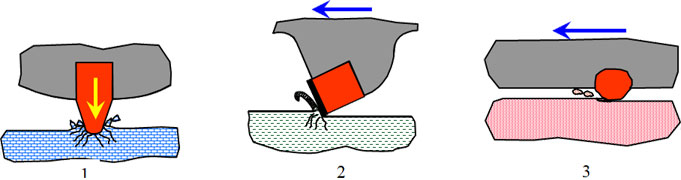
Рис. 5.11. Механизм разрушения горной породы различными типами долот.
1 – разрушение зубком шарошки;
Раздавливание и отрыв частиц породы, зубок требует высоких удельных нагрузок для дробления породы сжатием.
2 – разрушение резцом PDC;
PDC резец срезает слой породы. Породы легче разрушаются при боковой нагрузке в связи с анизотропными свойствами горных пород;
3 – разрушение истиранием (алмазосодержащим зубком алмазные долота, ИСМ).
Долота PDC имеют наиболее энергетически эффективную режущую структуру.
Современные резцы PDC используются при бурении от мягких до средне-крепких, абразивных пород. Долота PDC конструируются и изготавливаются индивидуально, в строгом соответствии с требованиями заказчика. [48]
Основные конструктивные параметры долот PDC:
1. Профиль долота;
2. Размер и тип резцов;
3. Плотность установки резцов;
4. Распределение резцов;
5. Распределение режущих усилий;
6. Стабилизирующие устройства;
7. Гидравлика;
8. Система калибрующих резцов.
Профиль долотаПрофиль режущей структуры долота выбирается исходя из физико-механических свойств проходимых пород, а также в соответствии с технологическими особенностями бурения (направленное и т. п.).
Размер резцов.
Из большого разнообразия диаметров резцов PDC, имеющихся на рынке, используются 6мм, 9мм, 13мм, 16мм, 19мм и 22мм резцы;
6 мм – резцы – примененяются только в долотах малого диаметра;
9 мм – резцы-применяются в долотах для бурения твёрдых пород там, где ранее использовались долота, армированные натуральными алмазами;
13 мм – резцы-наиболее широко используемый размер, оптимален для бурения средних и средне-твёрдых пород;
16 мм – резцы-используются в тех случаях, когда 13мм резцы, слишком твёрдые породы, а 19мм, – слишком мягкие породы;
19 мм – 22 мм резцы-предназначены для бурения в мягких и средне мягких породах с высокой скоростью проходки. [48]
Профиль долота.
Влияет непосредственно на:
• Стабильность работы долота;
• Управление направлением бурения;
• Плотность посадки резцов;
• Надёжность долота;
• V мex;
• Очистку и охлаждение долота.
Компоненты профиля долота.
• Центр;
• Конус;
• Нос;
• Плечо или наружный конус;
• Наружный диаметр (ODR);
• Калибрующие.
Центр – (геометрический центр долота).
Различается по углу открытия Cone
• Глубокий конус (~90°);
• Мелкий конус (~150°).
Глубокий конус.
Преимущества:
• Высокая стабильность долота;
• Повышенное содержание алмазов.
Недостатки:
• Сложность управления направлением бурения;
• Хуже очистка;
• Снижение агрессивности
Мелкий конус
Преимущества:
• Управляемость направлением бурения;
• улучшение очистки;
• Повышение агрессивности.
Недостатки:
• Снижение стабильности;
• Уменьшение объёма алмазов.
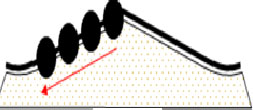
Рис. 5.12. Профили долот PDC
Профиль долот
4 основных типа:
• Плоские;
• Короткая парабола;
• Средняя парабола;
• Длинная парабола.
• Долота с плоским профилем используются для бурения крепких, мало абразивных пород;
• Долота с длинным параболическим профилем предназначены для бурения мягких пород;
Обратный угол резания:
• Угол атаки породы;
• Увеличение его даёт повышение ударной прочности и износостойкости резца;
• Снижение обратного угла повышает Vmex;
• Выбирается в соответствии с условиями бурения с учётом получения максимальной производительности долота.
Больший обратный угол резания соответствует более мягким породам и наоборот.
Величины обратных углов
• 5° – 10° Очень мягкие – глины, сланцы, высокие скорости бурения;
• 15° Универсален, мягкие поды – сланцы;
• 20° Универсален, дольше жизнь резца, абразивные породы;
• 30° Крепкие породы, типично для калибрующих резцов. [94]
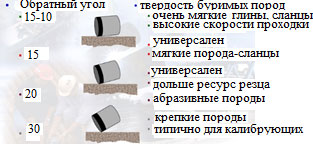
Рис. 5.13. Типовые обратные углы резания
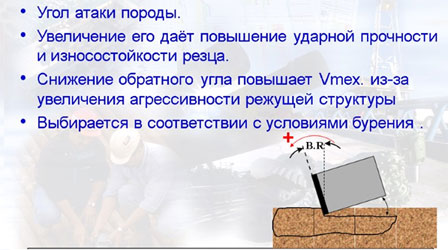
Рис. 5.14. Обратный угол резания
Классификация долот PDC
• С твердосплавным вооружением;
• С комбинированным вооружением:
• Твердосплавное вооружение + PDC;
• Для бурения с отбором керна;
• Для зарезки боковых стволов;
• Для наклонно-направленного бурения;
• Для бурения с одновременным расширением ствола скважины (бицентричные долота)
• Ступенчатые.
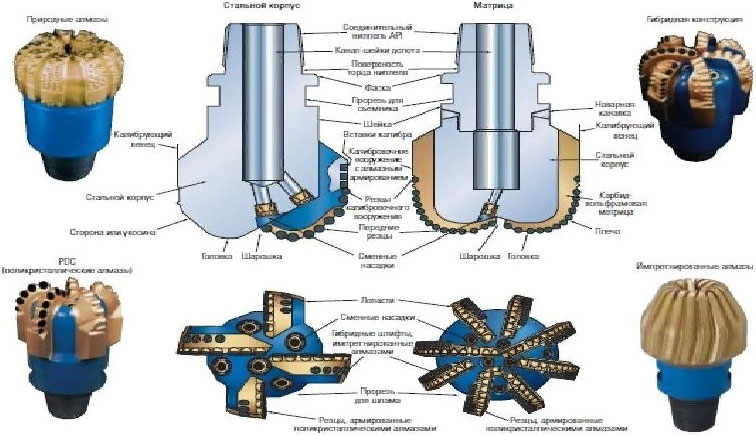
Рис. 5.15. Типы долот PDC

Рис. 5.16. Характеристика износа сегментов долот PDC
Таблица 11. Классификация долот PDC по коду IADC
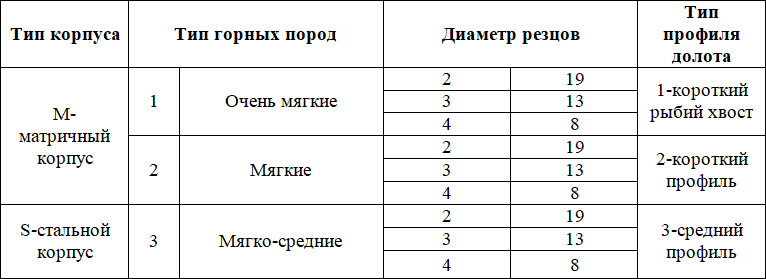
Перспективным направлением совершенствования долот PDC, являются долота с матричным корпусом. Матрица изготавливается из композиционных материалов. Металлическая матрица композиционных материалов (спеченный твердый сплав, обладающий высокими противо абразивными, упруго пластичными свойствами и микро твёрдостью) выбирается из условий получения максимальной удельной прочности материала, обеспечения связи между упрочняющими элементами и получения необходимых технологических и эксплуатационных свойств. Она обеспечивает передачу нагрузки на волокна, вносит существенный вклад в модуль упругости и снижает чувствительность к концентраторам напряжений. В качестве матриц используются магний, алюминий, титан, кобальт, никель и их сплавы, стали. [48]
В отличие от долот с одноразовым стальным корпусом, матричные долот подлежат ремонту. Восстановление PDC долота позволяет значительно увеличить его ресурс. Износ PDC долота в основном заключается в абразивном истирании PDC резцов, скалывании их алмазных пластин, а также утрате PDC долотом номинального диаметра и возникновении кольцевых проточек на его корпусе.
§ 21. Бицентричные долота
Бицентричные долота рис 5.17. предназначены для бурения с одновременным расширением ствола скважины, разработаны как альтернатива раздвижным шарошечным расширителям. Область применения – бурение ниже башмака спущенной колонны, диаметром более диаметра колонны. Пилот центрует долото по оси скважины, расширитель расширяет и формирует увеличенный ствол скважины. [48] Разработаны в СССР в г. Киеве. Впервые успешно применены и доработаны с участием автора в Арчединском УБР П/О Прикаспийбурнефть, при бурении скважин под хвостовик на Тенгизском нефтяном месторождении. Были оснащены твердосплавным вооружением, получен диаметр 240 мм. В дальнейшем компании Smith bits, Bakker, Reed и др. западные компании значительно улучшили показатели бицентричных долот, за счет использования резцов PDC.