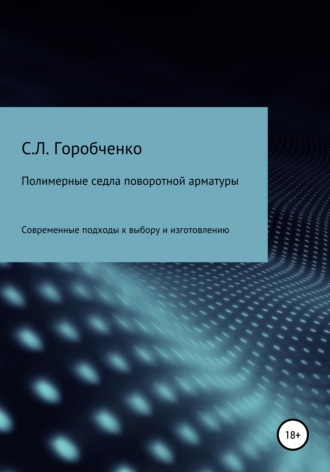
Полная версия
Полимерные седла поворотной арматуры. Современные подходы к выбору и изготовлению
Старение полимеров – это самопроизвольное необратимое уменьшение технических характеристик со временем. Причиной являются воздействие света, теплоты, кислорода, озона, многократные деформации и влага. Для определения способности противостоять старению проводят испытания: естественное в атмосфере, тепловое при Т<Тпл на 500С до 50% снижения характеристик.
Причиной старения является образование сложных радикалов с деструкцией полимера из-за окисления кислородом или структурирование. Деструкция приводит к размягчению, выделению летучих веществ (каучук). Структурирование, напротив, приводит к увеличению твердости, хрупкости, потери эластичности (полистирол). Тепловое старение наблюдается при температурах 200-5000С и выше с образованием газовой фазы из-за разложения компонентов во всем объеме.
Термостабильны полиэтилен, полифенолы. Они обладают высокой теплотой полимеризации или высокой степенью полярности, как фторполимеры. Устранение склонности к старению достигается добавкой органических стабилизаторов и антиоксидантов (амины, фенолы). Это приводит к значительному увеличению срока службы. Так, для полиэтилена, стабилизированного сажей, можно увеличить срок службы более 5 лет, поливинилхлорида до 10-25 лет.
Радиационная стойкость – способность противостоять ионизации и возбуждению, из-за которых происходит разрыв связей и образование свободных радикалов. Основными вредными проявлениями являются сшивание цепей или деструкция. При сшивании увеличивается молекулярная масса, повышается теплостойкость и механические свойства.
При деструкции происходит снижение молекулярной массы и уменьшение прочности. Деструкция характерна для полипропилена, полиэтилена и полиамида. Наиболее устойчивы к радиации бензолы (полистирол). Устранение вредного влияния радиации достигается введением антирадов – ароматических аминов, устраняющих энергию возбуждения и обеспечивающих ее рассеяние.
Вакуумстойкость полимеров. При вакуумировании возможно ухудшение свойств из-за выделения добавок из материала (пластификаторов, стабилизаторов) и деструкция. К примеру, это может быть деполимеризация. К потере вакуумстойкости склонны полиэтилен, полипропилен, полиамиды. Оценка вакуумстойкости проводится по газопроницаемости, газовыделению и вакуумплотности.
Газопроницаемость – это способность пропускать газ через уплотнитель. На газопроницаемость влияют состав, структура, природа газа, температура. Газопроницаемость меньше у полярных и линейных полимеров, выше у гибких макромолекул, при введении пластификаторов, и в меньшей степени при введении минеральных наполнителей.
Абляция – разрушение материала, сопровождаемое уносом его массы газовым потоком.
Ее характеризуют через абляционную стойкость. Она определяется устойчивостью к механической, тепловой и термоокислительной деструкции. Для линейных полимеров характерна низкая стойкость к деструкции и деполимеризации, для лестничных и сетчатых характерно структурирование и обезуглероживание. Для повышения абляционной стойкости материала, его армируют более теплопроводящими материалами, например, железом.
Адгезия – это слипание разнородных тел из-за межмолекулярного взаимодействия. Это явление используется при нанесении пленок и покрытий. Для полимеров может встречаться и аутогезия – самослипаемость. Ее причинами являются адсорбция, электростатическое притяжение, диффузия макромолекул.
ПЛАСТИЧЕСКИЕ МАССЫ
Пластмассы – массы, получаемые на основе органических полимерных связующих. Они способны при нагреве быть пластическими, а отверждаются при дальнейшем нагреве или охлаждении.
Состав, классификация и свойства пластмасс.
В состав пластических масс входят:
1. Связующие (синтетические смолы, эфиры, целлюлозы) и наполнители – порошкообразные или волокнисты. При пропитке наполнителя связующими и их опрессовывании получается монолитная масса.
2. Наполнители служат для повышения механических свойств, снижения усадки и придания специфических свойств.
3. Пластификаторы повышают эластичность и облегчают обработку.
4. Отвердители – амины
5. Катализаторы – перекисные соединения для ускорения отвержения термореактивных полимеров
6. Ингибиторы предохраняют массы от самопроизвольного отвержения
7. Красители.
Свойства пластмасс определяются составом компонентов, сочетанием компонентов и их количественным соотношением.
Классификация пластмасс.
Пластмассы классифицируют
1. по типу связующего
1.1. термопласты – удобны, усадка менее 1-3%, упруги, нехрупки, способны ориентироваться и иметь ориентационное упрочнение.
1.2. реактопласты – хрупки, усадка до 10-15%, для повышения их свойств вводят усиливающие или пластифицирующие наполнители.
2. По виду наполнителя
2.1. порошковые (карболиты) – наполнителем является древесная мука, графит, тальк
2.2. волокнистые – в качестве волокна используют очесы хлопка или льна, стекловолокно, асбест.
2.3. слоистые – используют листовые наполнители
2.4. газонаполненные – пено-поропласты, где наполнителем является воздух или нейтральные газы.
3. По применению
3.1. силовые – конструкционные, фрикционные и антифрикционные, электроизоляционные
3.2. несиловые – прозрачные, химически стойкие, электроизоляционные, декоративные, уплотнительные.
Особенности пластмасс
Их достоинствами являются:
1. малая плотность 1-2 т/м3
2. низкая теплопроводность 0.1 – 0,3Вт/мК
3. Электроизоляционные свойства
4. химическая стойкость
5. антифрикционность
6. прочность
7. технологичность.
Недостатками являются:
1. низкая теплостойкость
2. высокое тепловое расширение (в 10-30 раз больше, чем у стали)
3. низкая упругость и вязкость
4. склонность к старению
ТЕРМОПЛАСТИЧЕСКИЕ МАССЫ
Термопласты – полимеры линейной или разветвленной структуры, иногда с пластификатором. Свойства – Траб – обычно не выше 60-700С, теплостойкие до 150-2500С, термостойкость с жесткими цепям и циклическими структурами – до 400 – 6000С.
Особенности эксплуатации – при эксплуатации происходит снижение прочности и вынужденная эластичность при длительном статическом нагружении. – повышение хрупкости с ростом скорости деформации. Прочность – 10-100МПа, модуль упругости 1,8-3,5х103 МПа. Хорошо сопротивляются усталости сигма 0,2-0,3 от предела прочности.
Виды термопластов – полярные и неполярные. Неполярные – полиэтилен, полипропилен, полистирол, фторопласт 4. Полярные термопласты – фторопласт 3, ПВХ, полиамиды, полиуретаны, полиэтилентерефталаты, поликарбонаты, полиакрилат, пентапласты, полиформальдегиды.
Термостойкие пластики
Термостойкость обеспечивается за счет введения фениленовых звеньев, что обеспечивает работоспособность при 4000С и при замене гибких звеньев на жесткие гетероциклические, что повышает Траб до 6000С. Виды термостойких пластиков: ароматические полиамиды, полифениленоксид, полисульфоны, гетероциклические полиимиды.
Термопласты с наполнителями
Связующим является полимерная основа. Наполнители – стекловолокно, асбест, органические волокно, углеродные волокна и пр. Волокнистые наполнители образуют каркас и упрочняют материал. Промышленное использование имеют полиамиды и поликарбонаты, наполненные рубленным стекловолокном. Это повышает прочность до 90-149 МПа, обеспечивает повышенное сопротивление усталости и износу при Тисп 60-1800С.
Перспективны термопласты с синтетическим наполнителем – пропиленом, капроном, лавсаном, винолом. При близкой химической природе и типе связей обеспечивается совместная работа на упрочнение и рост длительной прочности в десятки раз.
Слоистые термопласты – в них используются ткани из различных волокон. Пример: полиамид, армированный стеклотканью, имеет предел прочности 430 МПа, предел текучести 280 МПа, ударную вязкость а = 250 КДж/м2, Тисп = 2200С.
ТЕРМОРЕАКТИВНЫЕ ПЛАСТМАССЫ
Связующими являются термореактивные смолы с пластификаторами, отвердителями, катализаторами, замедлителями и пр. Смола склеивает слои наполнителя, что необходимо для прочности при расслаивании. Адгезивность обеспечивается полярностью.
Виды связующих – фенолформальдегидные, кремнийорганические, эпоксидные смолы, имеющие наибольшею адгезию. Это дает возможность использовать армированные пластики. Они обладают высокой прочностью.
Теплостойкость кремнийорганических смол 260-3700С, фенолформальдегидных до 2600С, эпоксидных до 2000С.
Для крупногабаритных деталей используют непредельные полиэфиры и эпоксидные смолы. Они твердеют не только при повышенной, но и нормальной температуре без усадки и выделения вредных веществ.
Используются наполнители – порошковые, волокнистые, слоистые. В качестве порошковых используют органические (древесная мука), минеральные (молотый кварц, асбест, слюда, графит). Порошковые пластмассы отличают изотропность, низкая прочность и вязкость. Их применяют в несиловых конструкциях. Пластмассы с минеральными наполнителями имеют хорошую водостойкость, химическую стойкость, электроизоляционность.
ГАЗОНАПОЛНЕННЫЕ ПЛАСТМАССЫ
Газонаполненные пластмассы – это гетерогенные системы, состоящие из твердой и газообразной фаз. Структура состоит из связующих, образующих стенки пор или ячеек с распределенной в них газовой фазой. Основными свойствами являются малая масса и высокие тепло и звукоизолирующие свойства.
Основные виды газонаполненных пластмасс – пенопласты, поропласты, сотопласты.
Пенопласты. В них ячеистая структура представлена газообразным наполнителем и изолирована друг от друга тонкими слоями полимерного связующего. Свойства: плавучесть, термоизоляционность, невысокая прочность. Используются пенополистирол ПС с Тисп до +-600С, фенолкаучуковые ФК Е120-1600С, пенополиэпоксиды и др.
Поропласты – губчатые материалы с открытопористой структурой, где включения газа свободно сообщаются между собой и атмосферой. Применяются для водопоглощения и пр.
Сотопласты – тонколистовые материалы в виде гофра, склеиваются в виде пчелиных сот. В качестве материала в настоящее время используются ткани.
ЭКОНОМИЧЕСКАЯ ЭФФЕКТИВНОСТЬ ПРИМЕНЕНИЯ ПЛАСТМАСС
1. снижение материалоемкости за счет малой массы в 4-5 раз
2. снижение трудоемкости вместо литья, ковки и резания только формообразование – в 4-5 раз, например, вместо 30-50 операций производится только одна – литье.
3. снижение капиталовложений на оборудование и инвентарь – в 4-6 раз.
4. себестоимость продукции уменьшается в 2-3 раза, дешевле цветных металлов в 4-9 раз, дешевле черных металлов в 2-6 раз.
2.2. Методические основы выбора пластмасс
Применение пластмасс в изделиях эффективно только в том случае, если материал выбирается с учетом условий эксплуатации и режима формования изделий. Поэтому сначала выбирают вид пластмассы исходя из требований к ее эксплуатационным свойствам, а затем базовую марку и марку с улучшенными эксплуатационными и технологическими свойствами, которая эффективно перерабатывается заданным методом.
Методы выбора вида пластмассы по заданным требованиям эксплуатации различны. Если трудно задать точные значения параметров эксплуатационных свойств пластмассы, обеспечивающие работоспособность изделия в заданных условиях эксплуатации, а можно указать только требования к эксплуатационным свойствам и ориентировочные значения параметров этих свойств, можно воспользоваться методом аналогий.
Подобрать пластмассу по методу аналогий можно используя классификацию пластмасс по эксплуатационному назначению и анализируя сведения о различных полимерах и марках с улучшенными эксплуатационными свойствами, характере эксплуатационных свойств, назначении, достоинствах, ограничениях и рекомендаций по применению и способам переработки.
При выборе пластмасс по методу аналогий можно использовать рекомендации по применению пластмасс для различных типов изделий, работающих в условиях аналогичных заданным. Например, определяют к какому типу изделий относится данное и выбирают пластмассу из рекомендованных для этого типа изделий.
Подбор пластмасс осложняется тем, что параметры эксплуатации оказывают очень сильное влияние на их эксплуатационные свойства. Для правильного выбора пластмасс нужно знать изменение их эксплуатационных свойств в зависимости от параметров эксплуатации.
Другим подходом к выбору пластмасс является выбор по комплексу заданных значений параметров эксплуатационных и технологически свойств. Этот метод применяют, когда можно задать весь комплекс требуемых значений параметров эксплуатационных свойств пластмассы, обеспечивающий работоспособность изделия в заданных условиях эксплуатации. Он основан на сопоставлении заданных параметров эксплуатационных свойств с параметрами эксплуатационных свойств различных пластмасс. Отбирают пластмассы, параметры эксплуатационных свойств которых наиболее точно соответствуют заданным. Для выбора пластмасс разрабатывают банк справочных данных по параметрам свойств различных полимеров и марок на их основе с улучшенными эксплуатационными свойствами.
Первоначально подбирают базовую марку полимера в зависимости от метода переработки. Наиболее существенным показателем перерабатываемости полимера является его вязкость. В каталогах на полимеры указывают назначение каждой базовой марки полимера по вязкости – литьевые, экструзионные, для прессования и т.д. Далее подбирают базовую марку полимера по вязкости в зависимости от конфигурации и размеров изделия. Сравнительно просто подобрать базовую марку для получения экструзионных изделий. В каталогах на пластмассы обычно приводятся конкретные рекомендации по применению экструзионных марок. Порядок выбора литьевых марок для изготовления литьевых изделий более сложен.
Выбор марки с улучшенными технологическими свойствами выбирают на основе базовых с использованием справочной информации о выпускаемых типах марок с улучшенными технологическими свойствами, назначения, экономических эффектах, которые дает применение марок, рекомендациях по применению марок для различных изделий. Основная линия пластмасс для данного применения по вязкости может быть найдена по рис.2.4.
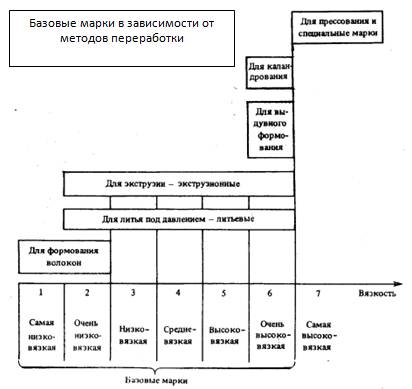
Рис. 2.4. Распределение базовых марок полимеров по методам переработки в зависимости от вязкости.
Распределение базовых марок полимеров по методам переработки и характерным группам изделий приведены в табл.2.1.
Табл. 2.1. Распределение базовых марок полимеров по методам переработки и характерным группам изделий [2]
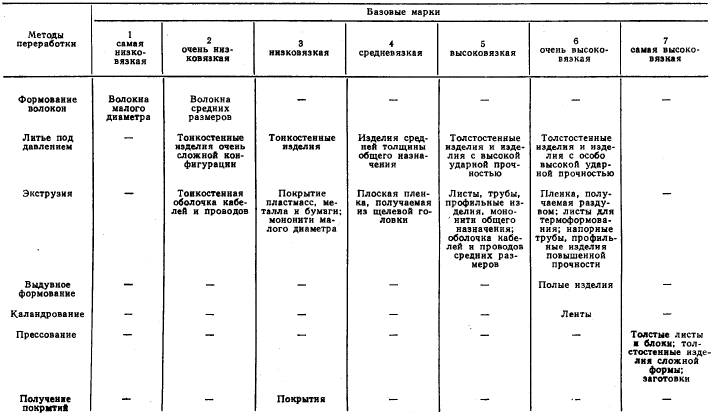
2.3. Материалы для изготовления уплотнений арматуры
Пластмассы широко используются для седел арматуры. Благодаря им появился целый класс арматуры, называемый арматурой с мягкими уплотнениями. С качественным ростом их свойств и упрощения их переработки, количество используемых пластмасс, например, взамен резиновых и, особенно металлических седел и уплотнений будет возрастать.
В настоящее время пластмассы наиболее широко используются для изготовления деталей или для облицовки внутренних поверхностей, непосредственно соприкасающихся с коррозионными средами.
В и н и п л а с т представляет собой твердую негорючую пластмассу, получаемую путем термической пластификации поливинилхлоридных смол. Обладает высокой химической стойкостью против действия многих агрессивных сред – кислот, щелочей и их растворов. Из винипласта изготовляются детали кранов и пр. Он используется также в качестве материала для защитного покрытия. Применяется для рабочей среды с температурой до 40…60°С.
Среди неметаллических коррозионно стойких материалов особое место занимает ф т о р о п л а с т (политетрафторэтилен C2F4), так как является наиболее коррозионностойким пластмассовым материалом. Молекулу фторопласта можно представить в виде молекулы полиэтилена, в которой атомы водорода замещены атомами фтора. В разных странах он получил разное название: в США – тефлон, галон; в Англии – флюон; в Японии – полифлон; во Франции – сорефлон; в Италии – альгофлон; в ФРГ – хостафлон.
Наибольшее применение получил фторопласт 4, выпуск которого составляет 80 – 90% от всех фторполимеров. Он представляет собой порошок белого цвета плотностью 2,2 г/см3. Фторопласт при нагревании до 327°С плавится, но расплав имеет высокую вязкость и остается в высокоэластичном состоянии до температуры 415°С, выше которой он разлагается с выделением ядовитого газа.
Фторопластовые детали изготавливают механической обработкой из заготовок в виде труб или листов, которые получаются прессованием порошка при давлении 35…100 МПа и последующим спеканием при температуре 365…385°С. Таблетки из фторопласта, полученного эмульсионным методом полимеризации, можно перерабатывать способом экструзии при давлении 10…120 МПа, получая, таким образом, трубы, ленты, профили. После экструзии изделия подвергают спеканию при температуре 370°С.
По химической стойкости фторопласт 4 превосходит платину, графит, кварц и все известные синтетические материалы. Его коррозионная стойкость сохраняется в широком интервале температур (от –269 до +250°С). Для того чтобы обеспечить нормальную герметичность затвора, в рабочей среде не должно быть твердых частиц размером более 70 мкм по наибольшему измерению.
Элементарный фтор и его галогениды медленно взаимодействуют с фторопластом, а расплавленные и нерастворенные щелочные металлы разрушают поверхность фторопласта, но вглубь материала не проникают. Высокая химическая стойкость фторопласта обусловлена прочным взаимодействием фтора с углеродом, а также тем, что атомы фтора экранируют атомы углерода. Фторопласт – изолятор с высокими значениями электрической прочности при температурах от –269 до +260°С. Электротехнические детали из фторопласта имеют высокие диэлектрические свойства.
Фторопласт 4 не смачивается водой и не набухает, по внешнему виду напоминает парафин, имеет низкий коэффициент трения. Ползучесть материала зависит от контактного давления и температуры. Фторопласт 4 используется для изготовления деталей кранов, клапанов, труб, сильфонов, прокладок, мембран, сальниковых набивок и различных деталей электроаппаратуры. Фторопласт 3 применяется для температуры до 70°С, выпускается в виде плит толщиной 1…8 мм, трубок, шнура, используется также для покрытия шероховатых металлических поверхностей, предварительно нагретых до температуры 275°С. При изготовлении седел лист фторопласта обычно обрезается по размеру будущего уплотнения и механически обрабатывается.
На основе фторопласта 4 изготавливаются всевозможные модификации для удовлетворения потребностей различных отраслей промышленности. Например, фторопласт 42, несколько теряя в свойствах, обладает литейными качествами. Для уплотнений используется фторопласт, наполненный графитом. Такая модификация фторопласта, как флубон хорошо зарекомендовала себя в качестве уплотнительных колец шаровых кранов на давление 32 МПа.
Существенно улучшены потребительские свойства пористого уплотнительного материала на основе фторопласта 4Д. Заготовка – жгут круглого или прямоугольного сечения подвергается многократной вытяжке и термообработке, в результате которой приобретает
особую структуру, которая придает материалу высокую прочность при пористости свыше 50% и необычную гибкость и подвижность.
Благодаря таким свойствам, антифрикционность сохраняется в широком диапазоне температур (от –240 до +270°С). Мягкость и гибкость материала позволяют легко прирабатываться, обеспечивать надежное уплотнение узла, в том числе и в случае длительно эксплуатирующееся арматуры, при небольших усилиях обжатия. Материал не замерзает и не дает усадки в щелях. Американская фирма GORE создала уникальные уплотняющие материалы на основе пористого фторопласта. Лента GORE ТЕХ эффективна для фланцевых уплотнений, листы GORE ТЕХ GR с толщиной от 0,5 до 6,5 мм применяются при небольших усилиях сжатия и значительных неровностях уплотнительных поверхностей, например, для эмалированной арматуры.
Германская фирма PROPACK изготавливает сальниковые набивки высокого качества, сплетенные из фторопластовой пряжи фирмы GORE.
П о л и э т и л е н используется как коррозионностойкий материал для изготовления уплотнительных колец, прокладок.
П е н т а п л а с т БГ 1 и сополимер формальдегида (СФД) для рабочей среды температурой до 100°С, сополимер формальдегида (литьевой) марки АК 80/20 – до 60°С, пластмасса МХФ (масса холодного формования) – до 50°С используются для изготовления деталей клапанов малых диаметров прохода, предназначенных для коррозионных сред.
К а п р о н, п о л и п р о п и л е н, н е й л о н и другие пластмассы имеют в арматуре ограниченное применение, но могут применяться в качестве добавок для повышения тех или иных свойств.
Механические характеристики некоторых неметаллических материалов и пластмасс приведены в табл. 2.2. Табл. 2.3. иллюстрирует стойкость защитных покрытий и мембран в агрессивных средах.
В табл. 2.4. и 2.5. указаны области применения арматуры из полипропилена и пентапласта БГ 1, используемых при различных коррозионных рабочих средах.
Табл. 2.2. Механические свойства некоторых неметаллических материалов и пластмасс, применяемых при изготовлении арматуры
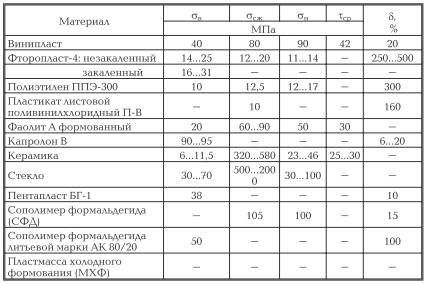
Табл. 2.3. Материалы защитных покрытий и мембран запорных и регулирующих мембранных клапанов, применяемых при различных агрессивных средах
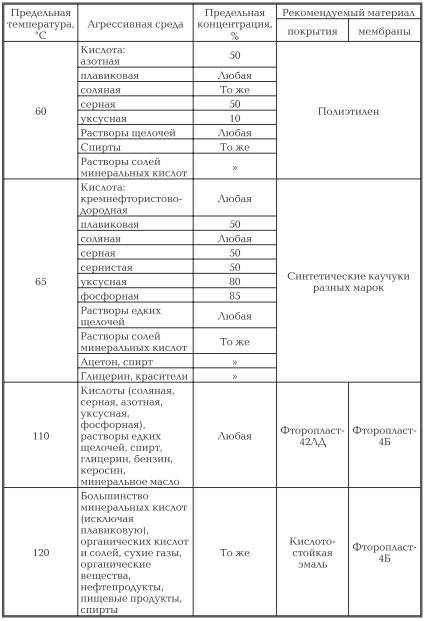
Табл. 2.4. Рабочие среды, при которых применима арматура из полипропилена
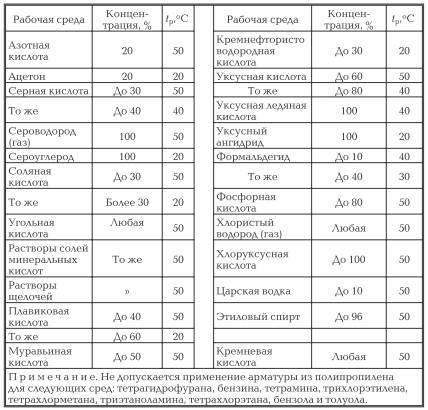
Табл. 2.5. Рабочие среды, при которых применима арматура из пентапласта БГ1
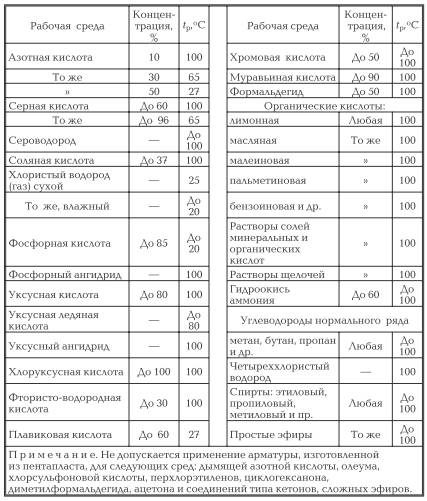
С и н т е т и ч е с к и е к а у ч у к и, называемые эластомерами или резинами, широко используются для изготовления уплотнительных деталей. Например, в золотниках предохранительных клапанов для природного газа после нескольких конструктивных доработок, вызванных негерметичностью на рабочей среде, содержащей песок и другие включения, были установлены уплотнительные кольца из высокомолекулярного уретанового синтетического каучука – полипропилена. Уплотнения успешно выдержали испытания. Из синтетических каучуков изготавливают уплотнительные кольца, вкладыши дисковых поворотных затворов, диафрагмы запорных и регулирующих клапанов.
Одной из важных проблем пластмасс является ограниченный температурный диапазон применения, рис. 2.5. В настоящее время он ограничивается примерно 2000С с учетом запаса до температуры размягчения.
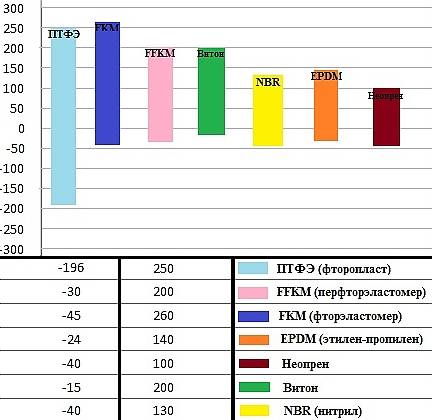
Рис. 2.5. Температурный диапазон применения основных типов пластмасс в уплотнениях и седлах.
Некоторые свойства полимеров, применяемых для шаровых кранов приведены в табл.2.6.
Табл. 2.6. Свойства некоторых полимеров для седел шаровых кранов [3]
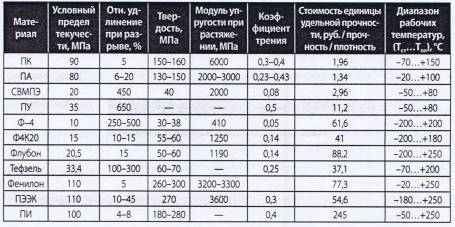
Здесь же приведены и корреляции между основными свойствами материалов и свойствами уплотнений, требуемыми в эксплуатации
Табл. 2.7. Корреляции между свойствами полимерных материалов и эксплуатационными параметрами уплотнений
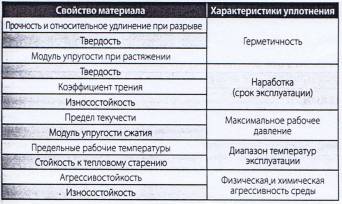
Выбор материалов из пластика для деталей арматуры представляет собой определенные трудности. Так, например, для уплотнений шаровых затворов могут быть предложены материалы из термопластика или термореактивы.
Сравнение термореактивных и термопластичных полимерных композиционных материалов относительно изготовления изделия «Уплотнение шарового затвора» показывает, что по сравнению с термопластами термореактивы обладают следующими основными недостатками:
1. Большая усадка и, как следствие, невозможность изготовления изделий высокой точности. В отличие от термопластов эта усадка не может быть скомпенсирована при переработке на этапе выдержки под давлением;
2. Меньшая средняя рабочая температура до 2500С, обусловленная отсутствием кристаллической фазы;
3. Большая себестоимость изготовления и меньшая производительность, обусловленная более длительным циклом полимеризации;
4. Большая вероятность появления в процессе изготовления различных дефектов (пор, микротрещин вследствие выделения летучих соединений при полимеризации), что приводит к значительному разбросу получаемых характеристик;
5. Как правило, большая токсичность;