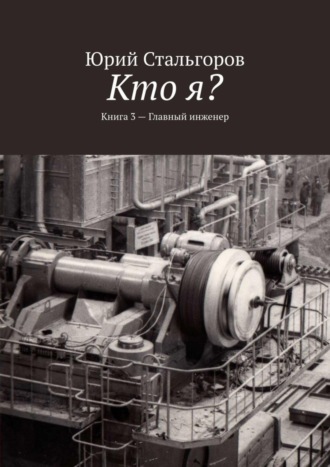
Полная версия
Кто я? Книга 3. Главный инженер
Для противопожарной защиты я применил стандартные противопожарные мероприятия и оборудования для всех производственных цехов любого завода, этот проект по моей просьбе по-быстрому разработал ГТСХМ, чтобы его можно было финансировать. Согласно проекту через определенное расстояние во всех цехах кузнечного комплекса были расположены стационарные пенотушители большой емкости, а также была смонтирована противопожарная система водоснабжения.
Участником госкомиссии по приемке производственных мощностей должен быть пожарный инспектор. Почему-то камышинский пожарный инспектор в ходе приемки термического и молотового цехов заартачился и потребовал выполнить противопожарную защиту, предусмотренную проектом для масла как закалочной среды. Как я писал выше, сделать это было невозможно. Тогда член госкомиссии, заместитель министра по капитальному строительству (не помню его фамилию) сказал: «Обойдемся и без участия в госкомиссии пожарного инспектора – по закону его участие совсем необязательно». Так пожарного инспектора не включили в акт госкомиссии, и в конце 1983 года термический цех вместе с молотовой кузницей был принят в эксплуатацию.
К концу года все оставшиеся проектные мощности кузнечного производства были приняты, необходимо было только улучшать организацию и повышать производительность труда на каждом рабочем месте. Необходимо было сформировать кадры командного состава кузнечного производства. В организационном плане у нас сформировался кузнечный корпус, в его состав входили следующие цеха: кузнечно-заготовительный, молотовой, прессовый и термический. К этому производству примыкал также цех кузнечных штампов, который находился, правда, в корпусе вспомогательных цехов. В самом здании кузнечного корпуса была сформирована ремонтно-механическая база с различными станками для механической обработки деталей оборудования. В кузнечном корпусе были механик и энергетик с обслуживающим, соответственно, персоналом. Фактически это был отдельный кузнечный завод.
Кузнечные проектные мощности были сформированы, однако рабочие изготавливали горячих штамповок намного меньше, чем позволяли эти мощности, по самым различным причинам.
Во-первых, у нас не было загрузки. Мы строились для потребностей Чебоксарского завода промышленных тракторов, однако заказов на всю введенную мощность от него мы не получили. Я сейчас не могу сказать, по каким причинам это произошло. По одной детали могу сказать – две наши линии горячей штамповки (это около 10 тысяч тонн в год) должны были штамповать звено гусениц чебоксарского трактора. Но нам эту штамповку тракторный завод не отдал, для них эту деталь изготавливал Чебоксарский завод запасных частей. Я был на этом заводе и видел, как изготавливалась эта деталь. На 10-тонном молоте они отштамповывали всю потребность Чебоксарского тракторного завода, и никто не хотел передавать эту деталь нам – она у нас обходилась немного дороже.
Во-вторых, работа на молотах чрезвычайно тяжелая для кузнеца и его подручного. Работа оператора по обслуживанию прессовых линий горячей штамповки соответствовала мнению рабочего о современных условиях труда, так как физически была нетяжелой. А работа кузнецов на молотах – тяжелый физический труд при той механизации работы на молотах, которая была заложена в проекте. По проекту труд кузнеца, казалось бы, был полностью механизирован. Для этого применялись механические манипуляторы, представляющие собой тележку, на которой сидел оператор и управлял работой манипулятора. Захватом манипулятора брались из печи нагретые заготовки, переносились к молоту и укладывались на неподвижную часть штампа. После того как кузнец, управляя молотом, отштамповывал в одном ручье заготовку, манипулятор перекладывал эту заготовку в другой ручей штампа. Потом манипулятором убирались готовая заготовка и облой. Однако манипулятор работал крайне медленно, и эта система себя не оправдывала, поэтому кузнецы вынуждены были часть операций производить вручную. Всё дело в том, что этот манипулятор был сконструирован и изготовлен конструкторским бюро кузлита. На мой взгляд, все сотрудники этого бюро были исключительно некомпетентными и безграмотными конструкторами, потому и получилось у них такое неработоспособное изделие. Они даже не искали аналогов и не интересовались, какие манипуляторы используются в других странах, потому они с самого начала и не могли разработать годную конструкцию.
Рассмотрим штамповку одной детали, которая производилась на 10-тонном молоте – коленчатой оси ведомого колеса (ленивца) трактора. Заказ на эту деталь у нас был большой, изготовление этой штамповки нам заказал Саратовский завод тракторных запасных частей «Серп и молот». Эта штамповка изготавливалась также в цехе Волгоградского тракторного завода для комплектации своих тракторов и в запасные части. Я знал, что эту штамповку изготавливал на 10-тонном молоте в Волгограде кузнец по фамилии Аркатов, Герой социалистического труда. В Волгограде я иногда встречал его на различных мероприятиях. Я знал, что он за семь с половиной часов отштамповывает 400 коленчатых осей, тогда как наши камышинские кузнецы не могли отштамповать за это же время даже установленную для них норму выработки в 40 штук. Я попросил директора Волгоградского тракторного завода Хватова, очень хорошо мне знакомого, чтобы он прислал к нам Аркатова на день или два для штамповки этой оси.
Приехал Аркатов. Он посмотрел на молотовой участок штамповки и сказал: «Все здесь надо переделать. Молот нормальный, но подача заготовок к нему не годится. Ваши манипуляторы – дерьмо, их надо просто выбросить. Давайте, сделайте, пожалуйста, так, как сделано в кузнечном цехе Волгограда! Сделайте такую же нагревательную печь, как у меня Волгограде, и поставьте ее буквально рядом с молотом. Повесьте монорельс для подачи заготовок к молоту, и на него повесьте электротельфер, потому что в данных условиях штамповки 400 осей и быть не может. Как только сделаете, приглашайте меня».
Я распорядился выполнить все его просьбы. Печное бюро отдела главного металлурга быстро выдало чертежи на нагревательную печь, а конструкторское бюро механизации выдало чертежи на монорельс. В течение месяца вся работа была сделана: выброшены манипуляторы, изготовлена газовая нагревательная печь, механизирован процесс подачи заготовок в печь и подачи нагретых заготовок к молоту, удаления готовой штамповки и облоя. Приехал Аркатов, посмотрел и сказал, что все хорошо сделано, и он станет штамповать. Он попросил дать ему подручного, которым мы поставили кузнеца, работавшего на этом 10-тонном молоте. Следующим утром Аркатов пришел и стал штамповать коленчатую ось вместе с подручным. За 7,5 часов при 30-минутном перерыве на обед они отштамповали 400 «с хвостиком» коленчатых осей.
Вместе с начальником цеха я собрал три смены кузнецов, работающих на этом молоте, и их подручных, и спросил: «Убедились, что можно штамповать 400 штук коленчатых осей за смену?». Кузнец, который штамповал вместе с Аркатовым как подручный, сказал: «Юрий Михайлович, так работать, как работает Герой социалистического труда Аркатов, мы не сможем и не будем. Так интенсивно работать обыкновенному человеку невозможно». Я сказал: «Но ведь Аркатов со своим подручным уже много лет работает в таком темпе». На это кузнец ответил: «Ну и пусть работают, а мы не будем. Такая работа выматывает человека полностью. Это хуже, чем работают какой-либо ишак или лошадь. Нам это не под силу».
Я понял, что такая механизация работы кузнеца на молоте не годится. Та механизация, которая была в проекте и предполагала использование самодельных манипуляторов, не позволяла выходить на возможности самого молота, а схема, предложенная Аркатовым – это лишь частичная механизация работы кузнецов на молотах на уровне американской механизации кузнечного производства 20-х годов. Она всё равно была несовершенной, поскольку не исключала полностью тяжелый физический труд. И, конечно, современные кузнецы не хотели работать с использованием такой допотопной технологии. Таким образом, мой эксперимент с Аркатовым мало что дал. Конечно, 40 штамповок за смену мои кузнецы теперь будут делать, но вряд ли доберутся хотя бы до 200.
Забегая в современность, хочу добавить, что к 2020 году новые владельцы молотовой кузницы в Камышине купили в Германии полный комплекс механизации всех работ по обслуживанию кузнецом молота без ущерба его производительности. Они купили у немцев кольцевую нагревательную печь, обслуживающую не один, а группу молотов; купили, можно сказать, роботы-манипуляторы, которые полностью механизируют работу кузнеца. По сути кузнец на молоте стал оператором, обслуживающим линию молотовой горячей штамповки. А я в те годы на кузлите этого сделать не мог и смирился с низкой производительностью молотовой кузницы.
Глава 9
Как я уже говорил ранее, в 1984 году практически все мощности кузнечного производства были приняты и начали работать, пришла очередь литейного производства.
Что такое литейное производство? Слово «литейное» означает, что какую-то жидкость нужно лить. Действительно, литейное дело зиждется на том, что различные жидкости льются в необходимую форму, чтобы получить нужное изделие. В нашем случае жидкостями являлись различные расплавленные металлы: сталь, чугун различных марок, алюминиевые и медные сплавы. Литейными сплавами также являются жидкоподвижные неметаллические смеси, в том числе стекло. Все жидкости разливаются либо в песчано-глинистые, либо в гипсовые, либо в металлические формы. Изделия, получаемые только литейным способом – унитаз, его бачок и крышка бачка – отливаются в гипсовую форму. Всю стеклотару: банки, бутылки, колбы, мензурки и прочее – получают путем заливки жидкого расплавленного стекла в металлические формы. Металлические сплавы в свою очередь отливаются в металлические или песчано-глинистые формы.
Примеры стальных отливок – звенья гусениц различных машин (танки, экскаваторы, бульдозеры, гусеничные тракторы), башня танка и некоторые другие детали тракторов, танков и других самоходных машин, шары и броня цементных мельниц, крестовины железнодорожных путей.
Примеры чугунных отливок – детали двигателей внутреннего сгорания: блок цилиндров, головка блока, поддон картера (я плохо помню конструкцию автомобилей, поэтому перечислить все чугунные отливки для них я не могу). Также из чугуна и только методом литья получают изделия для жилищно-коммунального хозяйства: секции отопительных батарей, решетки и оголовки решеток для колодцев ливневой канализации, оголовки и крышки люков различных канализационных колодцев, стояки канализационных систем, ливневые воронки на крышах зданий, канализационные трубы.
Из цветных сплавов отливают секции отопительных батарей, различные краны и клапаны для систем водоснабжения. Отдельно нужно отметить, что колеса турбокомпрессоров, применяемых в двигателях, можно получить только способом литья в соответствующую форму. Только таким способом можно получить корпуса электродвигателей, станины металлорежущих станков. Я назвал далеко не все изделия, которые можно получить только способом литья.
Литейное производство сложное, намного сложнее кузнечного производства, а мы должны были построить и принять в эксплуатацию чугунолитейный цех массового производства отливок. Рассмотрим технологию литейного производства на кузлите. В ЧЛЦ-2 была запроектирована технология изготовления чугунных отливок в песчано-глинистых формах. Эти формы изготавливались из песчано-глинистой смеси в виде полуформ (верха и низа) на формовочных автоматах и собирались на конвейере. Для изготовления форм необходимо приготовить по определенной рецептуре песчано-глинистую смесь и подать ее к формовочным автоматам. Необходимо также расплавить металл и залить его в изготовленные формы.
Для выплавки чугуна применялись вагранки – это плавильный агрегат непрерывного действия. Расплавленный в вагранке металл должен был заливаться на конвейере в собранные песчано-глинистые формы. Когда я изучал проект чугунолитейного цеха, я обнаружил, что эта технология устаревшая и что она имеет ряд серьезных недостатков. Прежде всего, из вагранки непрерывно выливается расплавленный чугун в количестве 20 тонн в час, а разлить его иногда невозможно – по каким-то причинам на автоматической линии (а это были немецкие линии фирмы «Гизаг») не было достаточного количества форм. Под заливку всегда должны были поступать 150 собранных форм в час. При освоении производства в общем плане, когда абсолютное большинство рабочих еще не обучены, такой производительности конвейер не может дать, а сливать жидкий чугун некуда – тупик.
Кстати говоря, примерно в 1975 году Правительство Советского Союза запретило использовать вагранки как плавильные агрегаты во вновь строящихся литейных цехах. А я приехал в Камышин в 1980 году, и к тому времени там уже было смонтировано три блока по две вагранки в каждом, то есть 6 вагранок. Таким образом, мощности плавильных агрегатов были очень высоки и притом излишни, так как кроме того, что нужно было под заливку подавать каждый час 150 форм, нужно было, чтобы в каждую форму можно было залить 90 кг металла. А номенклатура, которую передал нам главк, не обеспечивала такой металлоёмкости в форме. То есть проект чугунолитейного цеха №2 устарел еще до запуска производства. Как я упоминал, это был проект Купянского центролита нашего же Министерства, но купянский завод приняли в эксплуатацию целых 17 лет назад.
Получалось, что в Камышине мне необходимо было воплотить в жизнь уже давно устаревший проект. Слава богу, кончились деньги для строительства. В связи с изменением номенклатуры кузнечного производства и строительством кузнечного корпуса для удовлетворения нужд Чебоксарского завода промтаркторов условия для пересмотра проекта были благоприятные.
Я не мог отменить вагранки, хотя мне очень хотелось это сделать. Мне хотелось вместо вагранок поставить в цех электроплавильные печи, но, поскольку вагранки уже были куплены и частично смонтированы на кузлите, Министерство не разрешило мне это сделать (кстати, мотивируя это не деньгами, а задержками в строительстве). Более того, мне пришлось вместе с работниками Министерства добиваться специального решения Совета министров СССР в виде исключения разрешить нам принять в эксплуатацию уже имеющиеся фактически вагранки.
Я думаю, что это была моя ошибка – следовало настоять на том, чтобы вагранки не применялись, а внести в проект плавильные электропечи любой конструкции. Это давало бы цеху исключительную мобильность в приготовлении литейных сплавов. Увы, такое изменение сдерживало бы приемку мощностей, а это не входило в планы Министерства. Правда, я сумел внести в проект после вагранки 20-тонные электрические миксеры, что позволяло в какой-то степени иметь резервные емкости для слива туда жидкого чугуна, а также корректировать его химический состав. Еще я вставил в проект электрические индукционные заливочные машины емкостью 500 килограммов жидкого металла. Эти изменения давали все же какую-то возможность работать в цехе.
Глава 10
Итак, мы добились в Министерстве разрешения изменить проект завода в связи с изменением номенклатуры кузнечного производства и отсутствием цеха по производству товаров народного потребления. Если раньше стоимость строительства завода была около 400 миллионов рублей, то теперь мы набрали 650 миллионов. Таким образом, для строительства завода нам оставалось 250 млн. рублей. Началось согласование проекта опять же с городскими властями. В первоначальном проекте городские власти при размещении кузлита в Камышине выставили технические условия, при которых они согласны, что в Камышине будет строиться новый завод на 10 000 работающих.
При согласовании нового проекта строительства кузлита городские власти к ранее выставленным добавили дополнительные технические условия. Таким образом, их полный список выглядел так:
– Выстроить городской «Водоканал», включая новый водозабор и новые канализационно-очистные сооружения.
– Построить больницу на 500 коек с поликлиникой на 1000 посещений в сутки.
– Построить городской троллейбусный транспорт от заводской площадки до автостанции плюс два или три маршрута по городу.
– Построить котельную на 450 гигакалорий.
Очистные канализационные сооружения строились приличными темпами. Это за городом, ниже по течению Волги. Канализационно-очистные сооружения производительностью 120 000 кубометров стоков в сутки – очень приличное сооружение с механической, химической и биологической очисткой. Также мы приступили к строительству водозабора выше Камышина по течению Волги на 97 000 кубометров воды в сутки (на этот объем строились водоочистные сооружения). Строилось также административное здание «Водоканала». Завод строил камышинский «Водоканал» как собственное производственное подразделение, нанял туда рабочих, предоставил всем им жилье, как положено по проекту и по штатному расписанию. Руководил этим Когаев Павел Иванович.
Что касается строительства больницы, то я не понимал, зачем городу такая огромная больница. С 1980 года она все еще не строилась, поскольку город выделил под ее строительство земельный участок на месте оврага. Овраг был засыпан, и строители выжидали 10-летний срок, после которого здесь можно будет строить больницу.
Что касается котельной и троллейбусов, то мы вынуждены были согласиться, хотя я лично не видел никакой потребности ни в троллейбусном транспорте, ни в котельной. Хотя троллейбус – это муниципальный транспорт, и, может быть, городские власти были правы, однако дальнейшая жизнь показала, что это оказалось не так.
Заканчивая с городскими потребностями, я скажу, что был построен только городской «Водоканал», и он до сих пор функционирует и приносит пользу городским жителям. По имеющимся у меня данным, камышинский «Водоканал» является самым лучшим из всех водоканалов на Волге, самым современным и полностью обеспечивающим все нужды городского населения. Вода, выходящая в Волгу из канализационных очистных сооружений города, по всем показателям чище волжской воды, и ее можно пить. Наладчик оборудования «Водоканала», женщина из какого-то института Волгограда, по окончании наладочных работ принесла воду, и мы с ней распили по стакану этой воды из канализационно-очистных сооружений.
С начала 1984 года мы приступили к строительству и сдаче в эксплуатацию первой очереди ЧЛЦ-2. Был составлен так называемый пусковой комплекс, в который входило окончание строительства механизированного склада формовочных материалов. Там же принимался и хранился кокс и известняк, один блок (2 шт.) вагранок, один миксер, три автоматических линии формовки, участок изготовления формовочной смеси, участок изготовления стержней, участок обрубки и очистки отливок, отдельно стоящее 6-этажное бытовое помещение. В этом здании размещались отдел главного металлурга, ремонтные службы ЧЛЦ-2 на первом этаже, гардеробные и душевые на 3—4 этажах, некоторые бытовые помещения оказались свободными, так как были рассчитаны на два цеха – ЧЛЦ-1 и ЧЛЦ-2.
В пусковой комплекс должен был входить участок грунтовки. По проекту этот участок размещался в другом здании, которое располагалось между кузнечными и литейными цехами. Это здание было построено в 1975 году, но использовалось как складское помещение. Бытовые помещения этого корпуса использовались как здание заводоуправления кузлита. Это было 3-этажное здание, где размещались офисы руководителей завода: кабинет директора, кабинет главного инженера, кабинет секретаря партийной организации, кабинет председателя профкома завода и зал заседаний размещались на третьем этаже; на втором и первом этажах размещались кабинет заместителя директора по общим вопросам, кабинет заместителя директора по быту, отдел снабжения, отдел сбыта, первый отдел и офис второго отдела, бухгалтерия, финансовый и производственный отделы.
Чтобы пустить в работу окрасочный комплекс, требовалось освободить складское помещение и смонтировать там окрасочное оборудование и печи для сушки окрашенных отливок и поковок. Этот комплекс обслуживал как литейное, так и кузнечное производство. Необходимо было построить галерею, соединяющую ЧЛЦ-2 с окрасочным участком, и смонтировать достаточно длинный подвесной конвейер для транспортировки отливок из ЧЛЦ-2 в окрасочный участок.
Построить окрасочный комплекс вместе с первой очередью ЧЛЦ-2 строителям было не под силу. Я уже писал, что генеральным подрядчиком строительства Камышинского кузнечно-литейного завода был трест «Камышинпромжилстрой». Управляющим трестом в то время был Старцев, главный инженер Пыжьянов. Эти руководители заняли свои должности в марте 1980 года, до этого руководителем треста был Суворов, а Старцев был главным инженером. Суворов в чем-то провинился, и по рекомендации Камышинского горкома партии его отправили на пенсию. И Старцев, и Пыжьянов категорически отказались строить окрасочный комплекс.
На одном из оперативных совещаний в присутствии заведующего строительным отделом Волгоградского обкома КПСС Ф. И. Данилова было принято решение, обязывающее меня найти временное решение по грунтовке отливок. Я принял решение включить в пусковой комплекс участок грунтовки отливок ЧЛЦ-2, разместив его на первом этаже этого цеха. При этом я принял обязательство, что новое отделение грунтовки не будет ни взрыво-, ни пожароопасным – будем использовать грунтовку на водной основе. Такой участок грунтовки отливок мне довелось увидеть на Харьковском тракторном заводе в 1969 году. У них была построенная линия грунтовки отливок с использованием итальянского грунта на водной основе. Правда, когда я позвонил в Харьков и спросил, работает ли у них эта линия грунтовки и какой маркой грунтовки они пользуются, мне ответили, что итальянской грунтовки у них больше нет, и участок не работает. А грунтуют отливки они как обычно – оранжевой грунтовкой на обычном растворителе, и их участок грунтовки взрыво- и пожароопасен. Тем не менее, по моему техническому заданию Харьковский проектный институт выдал документацию на строительство участка грунтовки отливок ЧЛЦ-2 на первом этаже этого здания без всяких противопожарных устройств.
Это дополнение к проекту строители приняли к исполнению. Я лихорадочно стал искать водорастворимую грунтовку в СССР. Законодателем в области различных красок и грунтовок, применяемых в машиностроении, в то время был Институт лакокрасочной промышленности, который находился в Ярославле. Я связался с этим институтом и выяснил, что грунтовок на водной основе в СССР нет. За рубежом такие имеются, но стоят они достаточно дорого, и вряд ли я смогу добиться поставки нашему заводу таких грунтовок. Дальше мне пояснили, что у них разработана грунтовка – модификатор ржавчины, но она черного цвета. Впрочем, она вполне пригодна под окраску любым растворителем любого цвета.
Заручившись согласием ярославцев на поставку кузлиту нескольких тонн такой грунтовки, я все внимание обратил на стройку и подготовку рабочих для работы на автоматических линиях. Подготовкой и набором рабочих занимались Врублевский и его заместитель по кадрам. Рабочие были набраны и отправлены на учебу в Купянск, где такие линии работали с 1967 года.
Конец ознакомительного фрагмента.
Текст предоставлен ООО «Литрес».
Прочитайте эту книгу целиком, купив полную легальную версию на Литрес.
Безопасно оплатить книгу можно банковской картой Visa, MasterCard, Maestro, со счета мобильного телефона, с платежного терминала, в салоне МТС или Связной, через PayPal, WebMoney, Яндекс.Деньги, QIWI Кошелек, бонусными картами или другим удобным Вам способом.