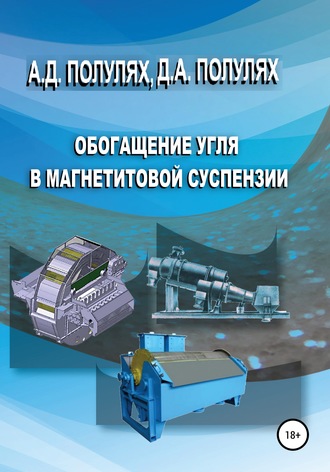
Полная версия
Тяжелосредное обогащение углей
В магнетитовых рудах контактово-метасоматического и гидротермального происхождений (горно-обогатительные комбинаты Соколовско-Сарбайский, Азербайджанский, обогатительные фабрики «Абагурская», «Мундыбашская», «Высокогорная», «Лебяжинская», «Гороблагодатская», «Магнитогорская», «Северо-Песчанская») собственно магнетита присутствует от 29,6 до 59,1 %, гематита (мартита) – от 0,5 до 3,6 %. Содержание железа колеблется от 29,9 до 46,9 %.
Магнетитовые руды того же происхождения, добываемые и обогащаемые Ковдорским ГОКом, относятся к магномагнетитам [(Fe, Mg)O · Fe2O3]. В них содержание собственно магнетита составляет 44 %, железа 28,2 %.
Руды Коршуновского ГОКа квалифицируются как титаномагнетитовые (FeO · F2O3 + FeO · TiO2) и содержат изоморфные примеси титана, магния, алюминия, кальция. Содержание магнетита составляет 34,0 %, гематита (мартита) – 4 %, железа – 28,7 % Понижение содержания железа объясняется также дисперсной вкрапленностью нерудных минералов (от 5 до 15 %), которые практически невозможно отделить от магнетита.
Гематито-магнетитовые руды добываются и обогащаются на Оленегорском (Мурманская обл.) и Михайловском (КМА) ГОКах, а также на Магнитогорском комбинате. Эти руды содержат от 12 (Магнитогорская фабрика) до 32,6 % (Михайловский ГОК) магнетита и соответственно от 8,7 до 16,5 % гематита и мартита. Содержание железа изменяется от 32,1 (Оленегорский ГОК) до 38,5 % (Михайловский ГОК).
Значительное содержание в гематито-магнетитовых рудах самостоятельно вкрапленных зерен гематита либо сростков гематита с магнетитом является препятствием для использования концентратов, полученных из этих руд, в качестве утяжелителей при тяжелосредном обогащении угля.
По химическому составу (%) магнетитовые кварциты осадочно-метаморфического происхождения, поступающие на горно-обогатительные комбинаты Криворожского бассейна и Курской магнитной аномалии (табл.1.4), отличаются сравнительно высоким содержанием железа и окиси кремния, по минералогическому (%) (табл. 1.5) характеризуются большим количеством магнетита и кварца. На ряде ГОКов обогащается магнетитовая руда, в которой содержится 5–7% гематита (Южный, Лебединский и Северный горно-обогатительный комбинаты). Из нерудных компонентов в необогащенной руде присутствует значительное количество слюды, что характерно для всех ГОКов, обрабатывающих магнетитовые кварциты. Иногда в магнетитовых кварцитах отмечается существенное содержание сидерита (ЮГОК – 5,7 %, Криворожский центральный ГОК – 11,2 %, Новокриворожский ГОК – 11,0 %). Низкое содержание серы и фосфора (кроме руд некоторых месторождений, в которых серы бывает от 0,16 %, а фосфора – до 0,1 %) является ценным свойством магнетитовых кварцитов.
Таблица 1.4
Химический состав магнетитовых руд
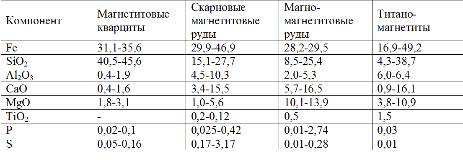
Таблица 1.5
Минералогический состав магнетитовых руд
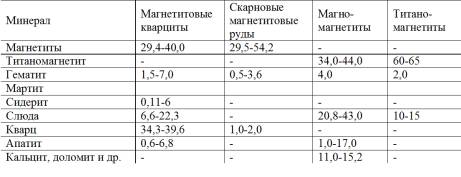
Физические свойства магнетитовых кварцитов – плотность, объемная масса, пористость – зависят от содержания железа. При увеличении содержания железа от 20 до 40 % плотность возрастает с 3190 до 3820 кг/м3, объемная масса – с 3060 до 3480 кг/м3, пористость – с 4,0 до 9,1 %.
При обогащении измельченных кварцитов содержание железа в концентрате зависит от его крупности. Так, например, при измельчении до <74 мкм содержание железа составляет 61,2-67,7 %, а при измельчении <50 мкм – 64,1-69,8 %.
Основным железорудным минералом скарновых руд является магнетит, в небольших количествах присутствуют гематит и мартит. Эти руды отличаются значительным количеством сульфидов в виде пирита и пирротина, в которых содержатся титан, ванадий, кобальт, иногда цинк, свинец, медь. Плотность скарновых магнетитовых руд составляет 3100–3400 кг/м3, они менее абразивных, чем магнетитовые кварциты. При обогащении этих руд, измельченных до крупности <74 мкм, содержание железа в концентрате в зависимости от вкрапленности колеблется от 62 % (весьма тонковкрапленные руды – размер вкраплений магнетита 1-10 мкм) до 67 % и более (крупновкрапленные руды – размер вкраплений магнетита 50 мкм – 10 мм).
Магномагнетитовые руды характеризуются высоким содержанием окиси магния и практическим отсутствием кварца. Содержание железа в них ниже, чем в магнетитовых кварцитах и скарновых рудах. Сернистые соединения либо отсутствуют, либо находятся в небольших количествах, отмечается существенное содержание фосфора, связанного с апатитом. Плотность руды зависит от содержания железа и колеблется от 3250 до 4600 кг/м3.
Важнейшей технологической характеристикой железных руд, от которой зависит глубина их измельчения на ГОКах, является размер вкраплений рудных и нерудных минералов. Отмечается постепенное увеличение размеров вкраплений (от пылевидных до сплошных) по мере роста содержания в руде железа.
Для магнетитовых (гематитовых) руд характерна тонкая слоистость, связанная с чередованием рудных, нерудных и смешанных слоев. При этом мощность слоев изменяется в широких пределах – от 0,1–2 мм до десятков миллиметров. Слой представлен вкраплениями рудных, нерудных и смешанных частиц, находящихся в нем в виде зерен, сростков и агрегатов. В магнетитовых рудах средние размеры зерен – 0,1 мм, агрегатов – 0,32 мм, нерудных зерен – 0,02 мм, агрегатов – 0,07 мм, смешанных зерен – 0,03 мм, агрегатов – 0,08 мм.
Для отдельных бассейнов размер включений колеблется в значительных пределах.
По крепости магнетитовые руды относятся по большей части к плотным и обладают коэффициентом твердости по шкале проф. М.М. Протодьяконова от 6 до 16 единиц, однако имеются и преимущественно рыхлые руды (например, частично руды Коршуновского месторождения), для которых коэффициент твердости составляет 2–6 единиц.
Магнетитовые руды относятся к сильно магнитным (ферромагнетикам), тогда как гематитовые и мартитовые руды – к слабомагнитным. Вмещающие породы, например, такие как кварц – немагнитные.
1.2.2. Требования к магнетитовым концентратам – утяжелителям суспензии
Гранулометрический состав
В качестве критериев крупности магнетитовых концентратов служит обычно содержание одного или двух классов, определяющих их характерный гранулометрический состав.
В СССР и в странах СНГ до настоящего времени в угольной промышленности существует классификация магнетитовых утяжелителей по трем классам крупности с разделением на три сорта (табл. 1.6) [13].
Следует отметить недостаточную четкость отечественной и зарубежной классификаций из-за наличия нескольких критериев крупности (выход определенных классов), а также несоответствие фактического гранулометрического состава, применяемых на практике утяжелителей, диапазонам крупности, принятым в классификациях.
Таблица 1.6
Классификация магнетита по сортам
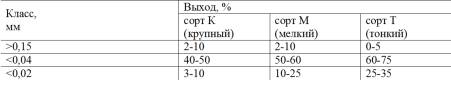
Магнитные свойства. Наряду с крупностью, важнейшей физической константой, определяющей выбор магнетитового концентрата в качестве утяжелителя, является его магнитная характеристика.
Наличие в магнетитовых рудах примесей слабомагнитных компонентов (в первую очередь, гематита и мартита, в также сопутствующих пород) ухудшает их магнитные свойства. Магнетитовые концентраты, получаемые после многостадийного измельчения и магнитного обогащения, обладают ярко выраженными магнитными свойствами, зависящими от химического состава руды, строения кристаллической решетки, крупности, насыпной массы и др. Однако их магнитные константы менее контрастны, чем у чистого магнетита.
Наиболее часто для характеристики магнитных свойств магнетитовых утяжелителей пользуются величиной магнитной проницаемости. Абсолютная магнитная проницаемость μ – физическая величина, характеризующая магнитную индукцию, т. е. результирующее магнитное поле при воздействии внешнего магнитного поля. Это отношение магнитной индукции В к магнитному потоку Н. Магнитная проницаемость связана с магнитной восприимчивостью, т. е. способностью вещества менять магнитный момент (намагничиваться) под действием внешнего магнитного поля

т. е. магнитная индукция, связана с напряженностью внешнего магнитного поля и намагниченностью вещества.
Предложено магнитные свойства магнетитовых утяжелителей характеризовать величиной условной магнитной проницаемости μус, измеряемой в долях единицы от значения магнитной проницаемости эталонной пробы чистого магнетита, для которого μус =1.
Измерение условной магнитной проницаемости осуществляется с помощью специального прибора-компаратора, состоящего из моста переменного тока с катушками индуктивности и показывающего гальванометра.
Магнетитовый концентрат считается пригодным к использованию в качестве утяжелителя, если для него μус >0,7. Отечественные магнетитовые концентраты обладают высоким содержанием магнитных фракций (как правило, выше 94 %), однако в числе требований к магнетитовому утяжелителю указывается также и нижний предел содержания магнитных фракций – 90 %.
Содержание магнитных фракций в утяжелителе определяется с помощью магнитного анализатора.
При измерении условной магнитной проницаемости берется магнитная фракция утяжелителя, выделенная с помощью магнитного анализатора.
Магнитные свойства исследованных магнетитовых концентратов и содержание в них магнитной фракции приведены в табл. 1.7.
Все концентраты по магнитным свойствам и содержанию магнитной фракции отвечают требованиям, предъявляемым к утяжелителям.
Таблица 1.7
Магнитные свойства магнетитового концентрата
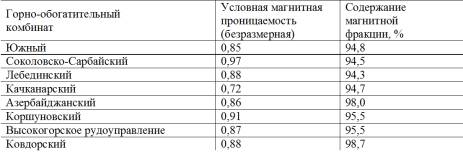
Плотность. В качестве утяжелителей рекомендуется применять магнетитовые концентраты плотностью 4300–4600 кг/м3 и более (примерно до 5000 кг/м3).
Плотность магнетитового концентрата является одной из важных физико-механических характеристик его как утяжелителя суспензии, так как определяет количество дисперсной фазы в суспензии заданной плотности и ее вязкость. Допустимое содержание в разделительной среде для тяжелосредных обогатительных процессов дисперсной фазы, т. е. утяжелителя, и засоряющих его угольных зерен должно быть не выше 32 %. Магнетитовые концентраты плотностью 4300–5000 кг/м3 обеспечивают получение разделительной среды плотностью до 2100 кг/м3, что удовлетворяет практически всем требованиям обогащения угля, антрацитов и сланцев.
Результаты измерения плотности исследованных магнетитовых концентратов следующие: Южный ГОК 4330, Соколовско-Сарбайский 4680, Лебединский 4930, Качканарский 4620, Азербайджанский 4560, Коршуновский 4355, Высокогорское рудоуправление 4440, Ковдорский 4570 кг/м3.
Таким образом, все эти магнетиты укладываются в нормативные показатели.
Определение качества магнетита осуществляется в соответствии с ДСТУ ISO 8833:2003 Магнетит для збагачення вугілля. Методи випробування [14].
1.2.3. Магнетит для обогащения угля
В настоящее время магнетит для процессов углеобогащения специально не выпускается.
Качество магнетитовых концентратов, поставляемых угольной промышленности, значительно изменилось из-за усовершенствования технологических схем измельчения и обогащения руды на ГОКах. Существенно возросло в магнетитовом концентрате содержание тонких классов и соответственно уменьшился средний размер зерна. В связи с этим увеличились потери магнетита при магнитной регенерации суспензий и с продуктами обогащения. Особенно это сказывается при обогащении углей с легкоразмокаемой породой.
В табл. 1.8 приведены потери магнетита на углеобогатительных фабриках Украины. Данные табл. 1.8 демонстрируют, что потери магнетита составляют от 1,2 до 4,9 кг/т перерабатываемого угля, что в 1,3–4,3 раза больше, чем предусмотрено нормами для обогащения крупного машинного класса в колесных сепараторах. Возросшие потери магнетита на углеобогатительных фабриках Украины, по нашему мнению, связаны в первую очередь с его гранулометрическим составом и относительной магнитной проницаемостью.
Таблица 1.8
Потери магнетита при обогащении крупного машинного класса на углеобогатительных фабриках Украины
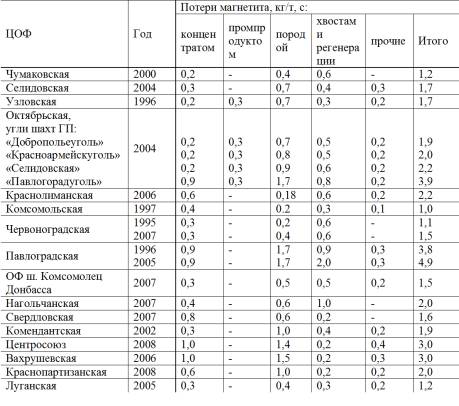
В табл. 1.9 приведены данные качества магнетитовых концентратов, выпускаемых горно-обогатительными комбинатами Криворожского железорудного бассейна: ЦГОКа, ЮГОКа, СевГОКа, ИнГОКа, НКГОК Арселоор Миталл Стилл, а также общие требования к магнетитовому утяжелителю суспензий, применяемых для обогащения углей. При этом для сравнения взяты сорта с лучшими показателями качества магнетитовых концентратов.
Таблица 1.9
Исходные данные для сравнительного анализа
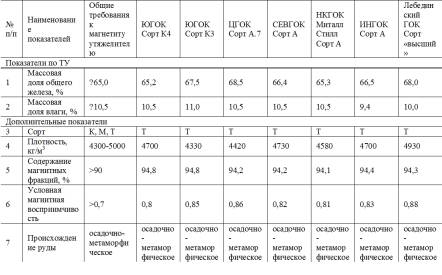
Из табл. 1.9 следует, что рассматриваемые сорта соответствуют общим требованиям к магнетиту-утяжелителю по всем показателям, кроме крупности. В современных магнетитовых утяжелителях отсутствуют сорта К и М.
Применение магнетита сорта Т вместо сортов К и М для обогащения соответственно крупного и мелкого машинных классов угля и привело к росту потерь магнетита на углеобогатительных фабриках.
Следует отметить, что в технических условиях на магнетитовые концентраты ГОКов отсутствуют показатели, характеризующие их гранулометрический состав.
Приведем данные фактического гранулометрического состава магнетитовых концентратов, выпускаемых ГОКами Криворожского железорудного бассейна. Данные диаграммы великолепно демонстрируют тот факт, что выпускаемые сегодня магнетитовые концентраты по гранулометрическому составу не соответствуют требованиям, предъявляемым к магнетиту-утяжелителю.
Увеличение крупности концентрата, то есть снижение содержания класса минус 0,04 и минус 0,02 мм обязательно приведет к снижению качества концентрата. Этот вывод подтверждают результаты, представленные на диаграммах, демонстрирующих содержания железа и кварца в классах крупности готового концентрата по всем ГОКах Кривбасса (рис. 1.4–1.9).
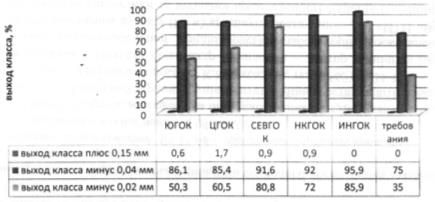
Рис. 1.4. Сравнительная характеристика гранулометрического состава магнетитовых концентратов с требованиями к утяжелителям марки Т
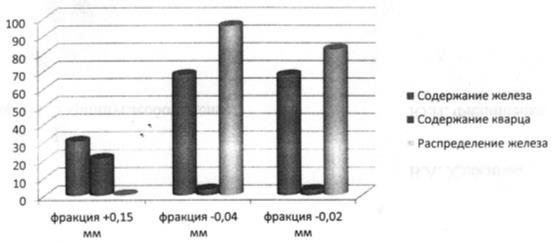
Рис. 1.5. Качественные показатели концентрата СЕВГОКа
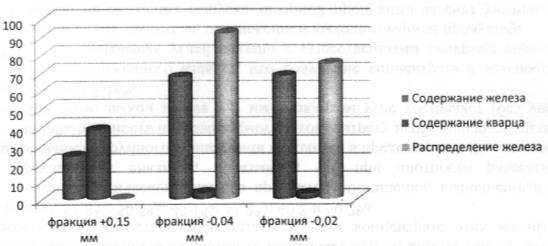
Рис. 1.6. Качественные показатели концентрата НКГОКа
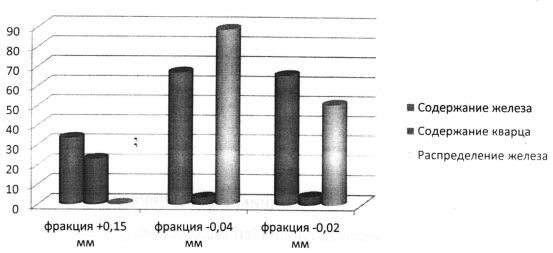
Рис. 1.7. Качественные показатели концентрата ЮГОКа
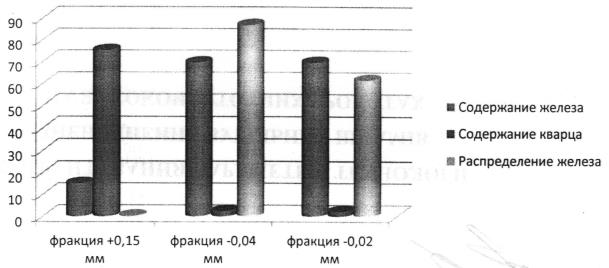
Рис. 1.8. качественные показатели концентрата ЦГОКа
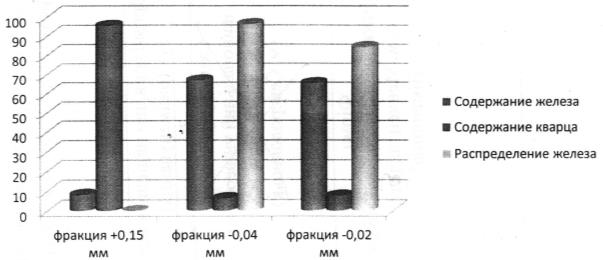
Рис. 1.9. Качественные показатели концентрата ИНГОКа
Поэтому концентраты ГОКов Кривбасса и предназначены только для переработки на металлургических предприятиях, а не для использования в качестве утяжелителя на углеобогатительных фабриках.
В табл. 1.10 для сравнения приведен гранулометрический состав магнетитовых концентратов за 1983 г. по данным [13].
Ранее выполненными исследованиями установлена взаимосвязь относительной магнитной проницаемости от гранулометрического состава магнетита, зависимость которой приведена на рис. 1.10 [15]. Как видно из рисунка, по мере снижения дисперсности магнетита относительная магнитная проницаемость возрастает, достигая максимума при d ≈ 0,059 мм, а затем плавно снижается.
Таблица 1.10
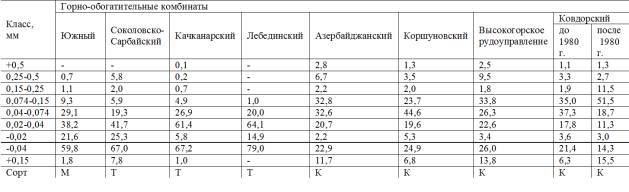
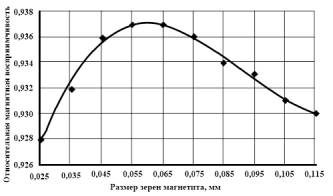
Рис. 1.10. График зависимости относительной магнитной проницаемости от степени дисперсности магнетита (по данным [15])
В результате многочисленных опытов установлено, что относительная магнитная проницаемость утяжелителя, ранее поставляемого ЮГОКом обогатительным фабрикам Украины, не превышала 0,932.
Нами были проведены специальные исследования по снижению степени дисперсности утяжелителя. Степень дисперсности утяжелителя должна соответствовать такой его крупности, при которой магнитная проницаемость будет не ниже 0,936. Этому требованию удовлетворяет магнетитовый концентрат со средневзвешенным диаметром частиц не более 0,0875 мм.
Установлено, что суспензия, приготовленная из магнетитового утяжелителя повышенной крупности d = 0,0875 мм с содержанием шлама 130–140 г/л, обладает идентичной гравитационной устойчивостью, что и суспензия с содержанием шлама 70–80 г/л, полученная из магнетита обыкновенной крупности.
Это дает основание считать целесообразным использованием магнетитового утяжелителя повышенной крупности на обогатительных фабриках и установках с повышенным содержанием шлама в суспензии (не менее 140 г/л).
Сравнительные испытания магнетитовых утяжелителей обыкновенной и повышенной крупности были проведены на ЦОФ «Украина» [15]. Характеристика испытуемых магнетитовых концентратов приведена в табл. 1.11.
Содержание шлама в магнетитовой суспензии составляло при испытаниях 180–190 г/л.
Как видно из приведенных данных, несмотря на более высокую нагрузку по углю на сепаратор СК и соответственно несколько повышенное содержание в нем класса 0–6 мм, потери утяжелителя повышенной крупности ниже по сравнению с потерями утяжелителя обыкновенной крупности.
Таблица 1.11
Характеристика магнитных концентратов
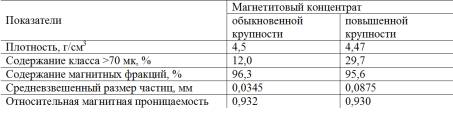
Результаты сменных опробований приведены в табл. 1.12.
Таблица 1.12
Результаты сменных опробований
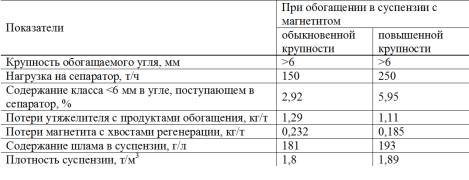
Было также установлено, что в результате применения магнетитового утяжелителя повышенной крупности расход его на фабрике сократился на 200–400 г/т обогащаемого угля, а потери в породе угольных и промпродуктовых фракций снизились на 0,1–0,2 %.
Таким образом, в результате проведенных исследований магнетитовых концентратов ГОКов Кривбасса, как утяжелителя для тяжелосредного обогащения каменных углей и антрацитов, установлено:
– применяемые к качестве утяжелителей магнетитовые концентраты не отвечают предъявляемым к ним требованиям по гранулометрическому составу, что приводит к большим потерям магнетита особенно при обогащении углей с легкоразмокаемой породой;
– диапазон крупности магнетитового концентрата должен находиться в пределах значений средневзвешенного диаметра частиц от 0,045 мм до 0,075 мм. В этом случае относительная магнитная проницаемость будет более 0,936;
– суспензия, приготовленная из магнетитового утяжелителя повышенной крупности d = 0,0875 мм с содержанием шлама 130–140 г/л, обладает идентичной гравитационной устойчивостью, что и суспензия с содержанием шлама 70–80 г/л, полученная из магнетита обычной крупности;
– применение более зернистого магнетита на фабриках с содержанием шлама в магнетитовой суспензии более 100 г/л приводит к снижению потерь магнетита и возможности увеличения нагрузок на сепаратор, обезвоживающее и регенерирующее оборудование.
Следует также помнить, что на первых этапах развития тяжелосредного обогащения для каждого из типов тяжелосредных сепараторов подбирался индивидуальный утяжелитель суспензии (табл. 1.13). В основных угледобываемых странах была произведена классификация магнетитовых утяжелителей по сортам крупности, а сортов крупности – по видам применения.
Следует иметь в виду, что увеличение глубины тяжелосредного обогащения до 0,1 мм и менее предопределяет необходимость наличия всего диапазона крупности магнитного концентрата, особенно в случае высокой плотности разделения. С этой точки зрения, чем мельче исходный материал, тем тоньше должен быть магнетит: от 30 % – 0,044 мм для класса +13 мм, до 90 % – 0,044 мм для класса 0,1–1,0 мм.
В случае необходимости, на углеобогатительных фабриках можно производить доизмельчение магнетита в шаровой мельнице небольшой производительности, так как расход магнетита не большой и не должен превышать 1 кг на тонну обогащаемого угля. При наличии классификатора измельчение в шаровой мельнице можно производить в замкнутом цикле.
Кроме того, при необходимости, можно осуществлять классификацию магнетита в гидроциклонах с выделением двух (и более) классов крупности (рис. 1.11).
В общем случае, применение магнетита на углеобогатительной фабрике в качестве утяжелителя необходимо рассматривать с четырех точек зрения:
– непосредственно обогащение данного класса крупности угля;
– необходимости создания разности плотностей разделения в секциях трехпродуктовых гидроциклонов не менее 500–700 кг/м3;
– отмывки магнетита от продуктов разделения минимальным количеством воды на грохотах с достижением нормативной влажности надситных продуктов;
– полноты улавливания магнетита на магнитных сепараторах.
Правильный выбор гранулометрического состава магнетита влияет не только на показатели обогащения угля, но и определяет схему регенерации, тип применяемого оборудования, режим его работы и эффективность обогащения. С увеличением содержания тонких частиц в магнетите ухудшается отмывка утяжелителя от продуктов обогащения, снижается эффективность регенерации суспензии, возрастают ее вязкость и предельное напряжение сдвига.
Таблица 1.13
Диапазон крупности магнетита, применяемого для тяжелосредных сепараторов (по данным [13])
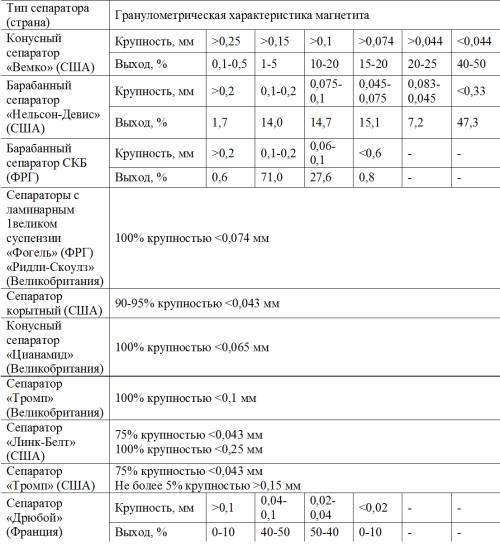
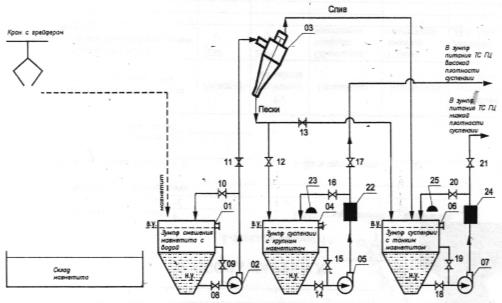
Рис. 1.11. Схема подготовки и дозирования магнетита
Увеличение крупности магнетита выше определенного предела также нецелесообразно. В этом случае значительно снижаются гравитационная устойчивость суспензии и магнитная восприимчивость утяжелителя при регенерации суспензии на магнитных сепараторах. Кроме того, увеличение крупности частиц магнетитового утяжелителя требует повышения скорости восходящего потока в обогатительном аппарате, что приводит к снижению эффективности разделения исходного угля вследствие выноса мелких породных частиц во всплывший продукт.
Форма частиц и механическая прочность утяжелителя влияют на вязкость суспензии, определяют степень износа оборудования и разрушение утяжелителя в процессе его циркуляции при обогащении угля. Суспензии, приготовленные из чистого магнетита даже при высокой их плотности (1800–2100 кг/м3), имеют невысокие вязкость и предельное напряжение сдвига. При добавлении к магнетиту угольных и глинистых шламов эти показатели значительно возрастают. Вязкость и предельное напряжение сдвига становятся тем больше, чем мельче утяжелитель и чем больше в нем шламов. При обогащении углей и антрацитов в суспензиях высокой плотности (2100–2200 кг/м3) с целью полного извлечения горючей массы возможно применение магнетитовых суспензий с добавкой ферросилиция, частицы которого имеют шарообразную форму, гладкую, зеркальную поверхность и повышенную твердость. Плотность гранулированного ферросилиция 6800–7200 кг/м3, он практически не подвержен коррозии. Максимальная плотность суспензии, приготовленной из гранулированного ферросилиция, равна 3300–3500 кг/м3. Такая суспензия в настоящее время применяется только при обогащении руд.
1.2.4. Источники потерь магнетита на углеобогатительных фабриках
В качестве утяжелителя для приготовления рабочей суспензии на углеобогатительных фабриках применяется магнетитовый концентрат, плотность которого должна соответствовать 4300–4600 кг/м3 с содержанием магнитной фракции более 93 %.
На обогатительных фабриках разгрузка, складирование и доставка магнетита, а также приготовление суспензии механизированы. Неудовлетворительная организация этих операций приводит к большим затратам ручного труда, чрезмерным потерям магнетита.
Повышенный расход магнетита при ведении технологического процесса на тяжелосредных установках обусловлен:
– нарушением технологии отмывки магнетита от продуктов обогащения и его улавливания из-за несовершенства применяемых ополаскивающих устройств, узкого фронта регенерации разбавленной суспензии, недостаточного количества слива электромагнитных сепараторов, подаваемого на ополаскивание;
– отсутствием систем сбора и возврата на регенерацию всех случайных сбросов, переливов, разбрызгиваний суспензий, выпусков из стояков и течей через сальниковые уплотнения суспензионных насосов;