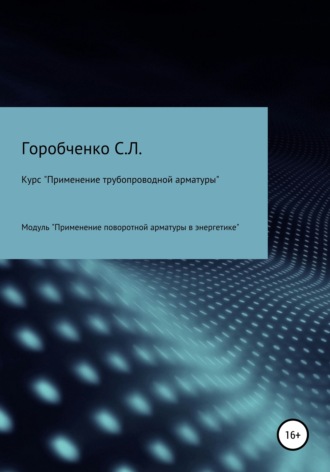
Полная версия
Курс «Применение трубопроводной арматуры». Модуль «Применение поворотной арматуры в энергетике»
Учитывая частые изменения нагрузки, использование программы NELPROF в режиме «он-лайн» поможет производству и технологам вовремя увидеть проблемы нарастания погрешности в связи с выходом за нижнюю или верхнюю границу пропускной характеристики. Так, по данным аудита одного из энергетических хозяйств ЦБК, свыше 50% регулирующих клапанов работало при угле открытия ниже 40%, что было главной проблемой накопления ошибок при регулировании. В случае если бы в системе автоматизации была бы установлена программа NELPROF, технологи и специалисты по автоматизации смогли бы выявить проблему значительно раньше и задать ограничения по процессу или снижению производительности.
Таким образом, уравнения погрешностей или их совокупностей, если затрагиваются несколько выходных характеристик, могут служить расчетным аппаратом при решении задач отстройки системы от нежелательных уровней выходных характеристик, либо задачи доводки последних до необходимой величины.
При моделировании точности необходимо учесть, что особенное влияние на поле рассеяния параметров имеет динамика протекания технологического процесса. Чем выше скорость, производительность, чем меньше устройств сглаживания, резервирования или транспортных звеньев, также способных сглаживать процессы, тем выше неустойчивость регулирования и колебательность процесса. При этом следует принять во внимание, что смещается как математическое ожидание характеристики под действием систематических факторов (износ, разбалтывание соединений, люфты в клапане, другие возмущающие факторы), так и случайные факторы при поднастройке контура регулирования и самого клапана. Растет дисперсия вследствие действия систематических факторов, например, динамических отклонений и, соответственно, динамической расстройки контура, так и случайных факторов.
Это также означает, что необходим определенный запас точности настройки, как минимум между двумя ППР и должна рассчитываться зона безопасного смещения математического ожидания вырабатываемой совокупности и роста ее дисперсии. В этом случае в «алмазной диаграмме» программы FIELDCARE можно предусмотреть 2 основные части поля рассеяния – большую часть, равную вероятностной сумме случайных погрешностей и меньшую, зону безопасного смещения математического ожидания и роста ее дисперсии, или зона запаса точности. Они, как понятно, должны быть меньше поля допуска. В анализе, приводимом специалистами по точности (ИПМАШ, Санкт-Петербург), показывается, что при применении, например, унифицированного метода, чем точнее выполняется обработка (точнее работает контур регулирования), тем создается большая возможность увеличения допусков. Этот принцип реализуется только при автоматическом непрерывном регулировании точности. Как уже показывалось выше, автоматический перерасчет клапанов он-лайн и встройка тревожных сигналов в системы автоматизации, может стать первым приемом повышения эффективности качества регулирования.
Если при моделировании используются различные гидравлические или электрофизические аналогии, то появляется возможность определить влияние дополнительных малых параметров на динамику системы. При разработке алгоритмов, они также могут быть включены в систему автоматизации процесса. Такие модели могут быть наиболее полезны при анализе точности сложных технологических схем, состоящих из большого числа узлов, соединенных последовательно или содержащих несколько разветвленных схем из таких последовательных цепочек. Требуется расчет точности контура регулирования каждого элемента и точности взаимного влияния этих контуров, для того, чтобы гарантировать функциональную точность процесса. Кроме того, модели должны учитывать изменение погрешностей во время эксплуатации. Ряд таких работ проводится в ВШТЭ СПБГУПТиД (бывшее ГТУРП), Санкт-Петербург. В результате моделирования одним из первых результатов может быть предсказание того, достигнет ли контур требуемой точности, будут ли сбои в определенный период, необходимо ли перепроектировать сам контур и т.п.
ПРИМЕНЕНИЕ ТЕОРИИ ВКЛАДОВ ДЛЯ АНАЛИЗА И СИНТЕЗА ТОЧНОСТИ
Вклад – эта мера влияния данного фактора на тот или иной показатель точности выходной характеристики. По-видимому, этот метод наиболее характерен для расчета погрешностей процессов технологических схем, как уже было продемонстрировано. При этом вклады могут быть следующими
1. абсолютный вклад фактора, включая и возмущающие, в математическое ожидание или среднее значение,
2. относительный вклад того же фактора,
3. относительный вклад свободного члена исходной модели (погрешности линеаризации, моделирования, полноты учета входных параметров),
4. относительный вклад дисперсии фактора в дисперсию выходной характеристики,
5. относительный вклад поля рассеяния фактора в поле рассеяния выходной характеристики,
6. относительный вклад совместного влияния 2-х дисперсий в дисперсию выходной характеристики, поля рассеяния,
7. относительный вклад отклонения от среднего значения факторов в отклонение от среднего значения выходной характеристики.
Методология рассмотрения точности по методу вкладов позволяет решать следующие задачи:
– ранжирование факторов по степени их влияния на выходные характеристики,
– оценка вклада в линеаризованную область, что позволяет анализировать роль неопознанных, неучтенных факторов и возмущений, а также погрешностей моделирования,
– оценка технических требований к конструкции и процессам, а также их уточнение,
– совершенствование управления технологическим процессом.
Следует отметить, что вклад в среднее значение может быть мал, но в дисперсию может быть доминирующим. Это означает, что при проектировании технологических схем необходимо учитывать все вклады контуров регулирования и в алгоритмах управления производством предусматривать то же самое. Включение в технические требования на клапан только основных показателей, которые оказывают доминирующее влияние на номинальное значение выходной характеристики, как это, к сожалению, наблюдается в практике проектных организаций, может привести к утрате контроля за полем рассеяния факторов, оказывающих на него существенное влияние. Это напрямую ведет к непредсказуемому колебанию уровня доли качественного выполнения процесса, что часто и наблюдается.
АНАЛИЗ КОНТУРА РЕГУЛИРОВАНИЯ С УЧЕТОМ ФАКТОРА ВРЕМЕНИ И ЭКСПЛУАТАЦИОННЫХ ИЗМЕНЕНИЙ
При проектировании должны учитываться как период эксплуатации, так и изменение ремонтных размеров, для чего необходимо устанавливать связь качества изготовления и сборки клапана с последующим качеством работы его при эксплуатации. Для этих целей задаются функциональные параметры, эксплуатационные показатели и связь между ними. Пределы изменения эксплуатационного показателя, например, гистерезиса, определяется допусками изготовления деталей. При эксплуатации параметры клапана изменяются из-за износа или возмущений и величину параметра через время эксплуатации можно записать уравнениями, где должна быть добавлена скорость изменения параметра. Методологически это делается при помощи использования данных трендов с «Алмазной диаграммы» программы FIELD CARE.
Расчет или аппроксимация данных и расчет уравнений регрессии процесса падения точности позволяет задавать категории допусков и принимать определенные показатели дисперсий, назначать допуска на входные и функциональные параметры, определять средний срок службы.
Проведенный обзор показывает, как внимательное отношение к контурам регулирования с точки зрения не только автоматизации процесса, но и повышения их точности и связи с технологией позволят добиваться более существенного роста качества технологического процесса.
Шагами к этому является знание технологии, анализ технологических схем на предмет точности регулирования и знание особенностей поведения клапана с целью устранения колебательности процесса.
НАДЕЖНОСТЬ КЛАПАНОВ
Как известно, надежность закладывается при проектировании, обеспечивается при изготовлении и поддерживается при эксплуатации. Однако, в приложении к регулирующим клапанам, подразумевающим надежность регулирования, и в приложении к отсечным клапанам, подразумевающим надежность отсечки, эти понятия часто бывают спорными. Тем более трудно научиться считать надежность клапанов. Для того чтобы разрешить проблему, необходимо разобраться с терминами, требованиями по надежности со стороны потребителей, выявить связь надежности работы клапанов с надежностью оборудования и узлов, в которые входит арматура, с системой АСУ ТП, измерительными комплексами. Рассмотрение будет неполным без разбиения анализа отказов на внезапные и постепенные, а также скрытые или невыявленные.
На основе этого анализа мы предлагаем рассмотреть методики определения надежности, применимые к арматуре. В частности, ими могут быть методики предварительного статистического и полевого аудита.
Надежность регулирующих клапанов в большей степени определяется их способностью обеспечивать наибольшую точность регулирования. Критериями надежности в этом случае будут надежность их работы в измерительном контуре, способность противостоять отказам и диагностироваться на внезапные и постепенные отказы. Учитывая значительный вклад регулирующих клапанов в поддержание точности контура, важно будет определить, как происходит постепенный метрологический отказ и сбои, и какие виды диагностики могут определять подобные отказы.
Для работы контуров отсечки важно рассмотреть влияние режимов работы на работоспособность клапанов. При этом существенное влияние оказывает уже коррозия, эрозия и кавитация. Клапаны постоянно подвергаются пульсациям и вибрации, вносящим значительный вклад в снижение надежности работы клапанов.
Рассмотренные факторы позволяют предложить ряд конструктивных и эксплуатационных методов для повышения надежности, включая метрологическую надежность. Оценка их на основе расчета технико-экономических параметров позволяет выбрать наиболее оптимальную. Но в большей степени такая оценка позволяет наметить долгосрочные пути повышения надежности. Производители арматуры способны в этом случае предложить программы расширения сроков гарантий на основе повышения надежности арматуры.
УМЕЕМ ЛИ МЫ СЧИТАТЬ НАДЕЖНОСТЬ РЕГУЛИРОВАНИЯ?
Хотя клапаны используются повсеместно, однако, для арматуры энергохозяйств, подобные расчеты надежности в проектные решения практически не закладываются. Иногда производители регулирующей арматуры приводят данные по потокам отказов или наработке на отказ в своих каталогах. В то же время клапан, установленный на сложном участке тепловой схемы и работающий в условиях агрессивной среды, может иметь в 6 раз большую вероятность отказа по сравнению с нормальными условиями, при которых приведены данные по отказам в каталогах арматуры. Наверное, именно поэтому, только длительная эксплуатация и статистика может служить надежным критерием оценки применяемых клапанов.
В предлагаемых материалах мы хотели бы обсудить, что такое надежность регулирующих клапанов и запорной арматуры, как повысить надежность и расширить сроки гарантий по применяемым клапанам, а также предложить оригинальную методику предварительной оценки надежности и диагностики.
НЕМНОГО О ТЕРМИНАХ
Основным показателем качества клапанов является надежность их работы, т.е. свойство выполнять заданные функции, сохраняя свои эксплуатационные показатели в заданных пределах в течение требуемого промежутка времени или требуемой наработки (определение по ГОСТ 53672 -2009 Арматура трубопроводная. Общие требования безопасности).
Надежность клапана обусловливается его безотказностью, ремонтопригодностью, сохраняемостью и долговечностью его частей.
Безотказность – это способность сохранять работоспособность в течение срока наработки без вынужденных перерывов.
Вероятность отказа – это вероятность того, что в течение времени T произойдет хотя бы один отказ.
Интенсивность отказов – отношение числа клапанов, вышедших из строя в какой-то интервал времени к среднему числу клапанов, находящихся в этом интервале в работоспособном состоянии, деленное на этот интервал времени. Этот критерий является удобной характеристикой надежности и определяется из опыта эксплуатации и специальных испытаний для оценки надежности.
Работоспособность – это состояние клапана, при котором он способен выполнять заданные функции с параметрами, установленными требованиями технической документации.
Долговечность – свойство сохранять работоспособность до предельного состояния с необходимыми перерывами для технического обслуживания и ремонтов.
Отказ – событие, заключающееся в нарушении работоспособности.
Неисправность – состояние узла, при котором он не соответствует хотя бы одному из требований технической документации.
Ремонтопригодность – свойство, заключающееся в его приспособленности к предупреждению, обнаружению и устранению отказов и неисправностей путем проведения технического обслуживания и ремонтов.
Дополнительно используются термины вероятности безотказной работы, вероятности отказа, интенсивности отказов, равнонадежности, потока отказов, среднего времени безотказной работы, эффективности восстановления и др.
ТРЕБОВАНИЯ НАДЕЖНОСТИ
По опросу, проведенному журналом CONTROL ENGINEERING в 2007 году, рис.2.5., около 80% респондентов – пользователей регулирующих клапанов – сообщили, что надежность является наиболее важным качеством клапанов. На лучших предприятиях работают или внедряются программы повышения надежности наиболее критичных регулирующих контуров, т.е. тех, которые определяют качество всего процесса, конечного продукта или существенно влияют на себестоимость. Требование надежности возрастает в случае повышения скорости процессов, повышения качества, необходимости стабильности технологических процессов и всегда помогает осуществить высокий уровень автоматизации.

Рис. 2.5.. Критерии выбора регулирующих клапанов
Уже достигнуты несомненные успехи по повышению надежности работы клапанов. До 40 % пользователей клапанов сообщили, что они заменяют или ремонтируют клапаны раз в 3 года, 30 % – раз в 2 года и 30 % – раз в год. При этом компании, которые осуществляют ремонт раз в 3 года, используют интеллектуальные системы диагностики клапанов, позволяющие предвидеть аварию, а не разбираться с ней по свершившемуся факту.
Основными причинами невысокого уровня надежности арматуры назывались: недостаточный учет реальных условий эксплуатации, недостатки в методологическом подходе к решению проблемы обеспечения надежности, скрытые технологические дефекты. Рассмотрим их подробнее.
Недостаточный учет условий эксплуатации. Имеется как минимум три этапа, и точнее это стыки между этими этапами, когда объективно «теряются» и не учитываются факторы, являющиеся потенциальными причинами будущих отказов: это недостаточное определение технических требований и неправильное заполнение опросных листов, неучет возмущающих факторов при эксплуатации. Ими могут быть: реальные режимы нагружения на элементы арматуры, зависящие от постоянных, аварийных и незапланированных пульсаций давления; монтажные перекосы и вибрация трубопроводов; усилия, возникающие при функционировании арматуры; внутренние концентраторы напряжений; технологическое термоциклирование и др. Это и специфичность совместного действия механических и термических факторов – коррозии и механических напряжений. Всегда существует возможность появления критических режимов протекания рабочих сред вследствие изменения технологических режимов системы, приводящих к повышенной турбулизации, кавитации, эрозии в местных гидравлических сопротивлениях проточной части арматуры.
Как показывает опыт, основной причиной выхода из строя арматуры является ее неправильное применение, неучет особенностей эксплуатации и параметров трубопроводных систем. При анализе и аудите причин выхода из строя арматуры зафиксировано большое число отказов, возникающих вследствие использования арматуры в условиях, не предусмотренных технической документацией.
Чтобы избежать этого, многие фирмы разрабатывают программы по повышению качества и надежности арматуры. В таких программах выделяются следующие основные задачи: создание паспортов арматуры и компьютерной базы данных по истории эксплуатации (обслуживание, аварии, ремонт каждой единицы арматуры) и снятие с тендеров закупок арматуры без надлежащего анализа ее пригодности для конкретных условий эксплуатации, предоставление поставщиком расчетных данных и обеспечения гарантий по работоспособности арматуры во время ее эксплуатации, гарантии сервисного обслуживания, поставок запчастей и др. Это устраняет возможность эксплуатации некондиционной арматуры и аварийных внеплановых остановов по причине ее выхода из строя.
К факторам, нарушающим требования документации при монтаже и эксплуатации, относятся следующие:
– перед установкой арматуры в систему не проводятся приемочные испытания, регламентируемые технической документацией;
– не контролируется гарантийный срок службы, что приводит к эксплуатации некондиционной арматуры, вероятность аварийного выхода из строя которой особенно велика;
– нарушается регламент освидетельствования и ремонта арматуры, ведение паспорта
– применяются «крючки» – рычаги-удлинители при закрывании арматуры вместо применения динамометрических ключей;
– при эксплуатации экстремальные условия возникают при незапланированных остановах и пусках технологических линий;
– запорная арматура может использоваться при регулировании и дросселировании, что приводит к выходу ее из строя.
Недостатки в методологическом подходе к оценке надежности. К ним относятся: Применение только статистических моделей, на основе информации «работоспособность – отказ» и только формального модельного подхода к распределению вероятностей отказа, тогда как на самом деле необходимо полноценно использовать данные эксплуатации.
Для расчетов надежности только арматуры по критерию постепенного или внезапного отказа применяется методика анализа и критерий непревышения критических значений «нагрузка – прочность», для анализа метрологической надежности – критерий «параметр-поле допуска».
Силовые воздействия, формирующие поля напряжений, например, в корпусных деталях вызываются, как правило, гидростатическим давлением рабочей среды, усилием уплотнения в затворе от привода, изгибающим моментом в местах соединения трубопроводов (монтажные погрешности, деформации трубопроводов в режиме эксплуатации). Возможные последствия силовых воздействий – это недопустимые деформации и разрушение деталей арматуры, разгерметизация в затворе и относительно окружающей среды.
Из всех элементов арматуры наиболее катастрофические аварии случаются при разрушении корпусов арматуры. Однако, доля таких разрушений достаточно мала, связаны они, в основном с гидравлическими ударами, технологическими скрытыми дефектами и составляют 3-5% всех видов отказов.
Наибольшее число отказов вызвано поверхностными процессами – изнашиванием, коррозией, эрозией, кавитацией и их совместным действием. Например, анализ отказов различных видов арматуры (более 150.000 случаев, данные ЦКБА) показал, что их основной причиной явились различные виды изнашивания – 65%, коррозии – 25%, эрозии и кавитации – 5%.
Особенно потенциально опасны агрессивные и коррозионно-активные среды. Кроме коррозионного поражения эти среды в условиях действия полей напряжений приводят к усилению механохимических реакций – резкому возрастанию скорости растворения деформированных участков поверхности, коррозионному растрескиванию, значительной интенсификации изнашивания, эрозии и кавитации.
Термическое воздействие среды приводит к заклиниванию деталей в сопряжениях вследствие различного коэффициента термического расширения, возрастанию коррозионной активности рабочей среды, возникновению в деталях дополнительных полей термонапряжений, изменению механических свойств материала и др.
СВЯЗЬ НАДЕЖНОСТИ КЛАПАНОВ С НАДЕЖНОСТЬЮ УЗЛОВ ОБОРУДОВАНИЯ
Важность учета специфики надежности клапанов, как с непрерывностью процесса, необходимостью точного регулирования, так и с огромным количеством установленных клапанов, очевидна. Их количество на одном крупном энергоблоке может доходить до 40.000 ед. При этом на долю отказов установки в целом по причине выхода из строя клапанов может приходиться до 60-70%.
Среди общих простоев до 15% приходится на долю клапанов и арматуры. В структуре ремонтного цикла на долю арматуры приходится также значительная часть. Каждое ТО связано так же, как минимум, с осмотром арматуры и ведением ее паспорта. Сам отказ клапанов может приводить как к полному отказу установки, так и к постепенной потере эффективности. По классификации отказов клапаны попадают во все категории, см. табл. 2.7.
Табл. 2.7. Категории отказов клапанов
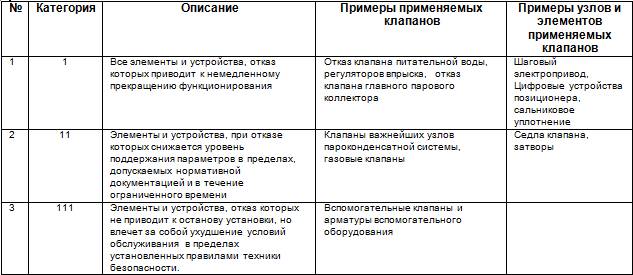
Уже достаточно давно установлено, что максимальные простои приходятся на первые годы эксплуатации. И далее, приближаясь к 8 годам эксплуатации, когда большая часть узлов исчерпывает свой ресурс, эксплуатационные затраты растут, а эксплуатационная эффективность падает. Заметное снижение уровня надежности в целом начинается через 4-5 лет после выхода на нормальный режим эксплуатации. Эти данные могут использоваться для повышения и расчета надежности клапанов, в частности, для того чтобы кратность их замены приходилась на этапы замены и других изношенных узлов. При этом уровень капитального ремонта всей установки может быть повышен. Таким образом, формируя ремонтный цикл арматуры до уровня 4-5 лет после выхода на нормальный режим установки в целом, можно добиться повышения надежности и эффективности, как капитального ремонта, так и эксплуатационной эффективности установки в целом.
Из процессов, действующих на клапаны и арматуру в составе энергоустановки, можно выделить 3 основных:
– обратимые – временно изменяющие параметры и поддающиеся регулированию, например, процессы регулирования,
– необратимые – износ штока, седла клапана, "разлохмачивание" сальникового уплотнения и др.,
– медленно развивающиеся процессы – зарастание масляной шубой пневмопровода, карамелизация клапана, прикипание, забивание слизью, уплотнение сгустков и др.,
– монотонные процессы средней скорости – линейное расширение клапанов пароконденсатной группы при температурах эксплуатации.
– быстроизменяющиеся процессы – работа клапана в условиях высокой вибрации трубопровода, наличие кавитации.
Учитывая, что в большей степени в настоящее время применяют поузловое обслуживание и ремонт, то обслуживание клапанов также должно сочетаться с кратностью обслуживания этих узлов. Надежность клапанов и арматуры должна быть больше нормируемых показателей надежности для этих узлов.
Общая эксплуатационная надежность одного и того же клапана или его элемента может отличаться в десятки раз. Так, по данным, приведенным в исследованиях по надежности в ряде отраслей, показаны следующие цифры, см. табл. 2.8. Из этих же данных можно увидеть и место вероятности отказа клапана среди других элементов контуров регулирования и сопряженных узлов.
Табл. 2.8. Вероятность отказа клапанов и элементов контуров регулирования
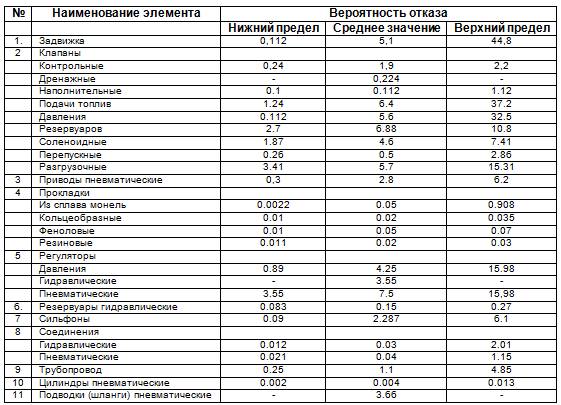
Внезапные и постепенные отказы
В зависимости от характера изменения параметров отказы делятся на внезапные и постепенные. Внезапные отказы возникают в результате скачкообразного изменения значений одного или нескольких основных параметров. Постепенные отказы возникают в результате постепенного изменения значений одного или нескольких параметров вследствие старения, например, прокладки, мембраны или износа, например, затвора или штока и т.п. В интеллектуальных клапанах, в которых применяются цифровые регуляторы, встречаются т.н. сбои.
Для иллюстрации постепенных и внезапных отказов рассмотрим схему, как контура регулирования, так и внутренней передаточной функции самого клапана.
Контур регулирования выглядит следующим образом: «датчик – коммуникатор – преобразователь – логическое устройство – коммуникатор – преобразователь – клапан». Из проблем, связанных с этими элементами, к внезапным отказам, означающим полную потерю работоспособности клапана или потерю работоспособности за короткое время, можно отнести заклинивание клапана и катастрофические утечки. К постепенным – износ, заедание клапана, постепенное накопление люфтов в механических соединениях, карамелизация и др.
Внутренняя передаточная функция и внутренняя схема передачи сигнала клапана строится следующим образом: задание значения управления «позиционер-привод-клапан» и обратная связь с отслеживанием положения клапана. В этой схеме к внезапным отказам можно отнести заклинивание клапана, разработку отверстий, разбалтывание болтов между штоком и клапаном с последующим заклиниванием, забивание инородными предметами, грязью и т.п. К постепенным отказам – постепенный износ затвора с постепенным увеличением протечек, постепенное «разлохмачивание» уплотнений и сальников, постепенное увеличение мертвого хода в связи с разбалтыванием механических соединений, постепенное увеличение пропуска воздуха в приводах и энергопотребления в связи с износом поршня и др.