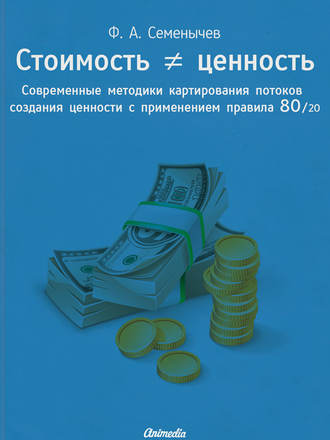
Полная версия
Стоимость ≠ ценность. Современные методики картирования потоков создания ценности с применением правила 80/20
С одной стороны, простота этого инструмента обусловлена наглядностью и коротким алгоритмом реализации, отсутствием потребности в специальной квалификации и не требует относительно длинного промежутка времени для реализации. После первых просмотренных презентаций или прочитанных книг и учебных пособий становится понятно, что надо делать. Не нужно никаких сложных технических средств для применения инструмента: достаточно большого листа бумаги, карандаша, стикеров или разноцветных маркеров. Впрочем, набор средств для построения КПСЦ может быть совершенно различный. Сложность же заключается по большей части в небольших, но значимых с точки зрения применения инструмента ошибках-ловушках, в которые часто попадают те, кто применяет этот инструмент (см. раздел 4 и Приложение 2).
В современных организационных структурах на Российских предприятиях и организациях, как правило, несколько менеджеров отвечают за различные части потока создания ценности, а ответственность за весь поток в целом лежит на директоре (топ-менеджере). К примеру, один руководитель отвечает за изготовление заготовки, другой – за её обработку, третий – за её сборку и т. п. При вопросе «кто отвечает за этот поток?» на лицах руководителей, как правило, возникает недоумение. Как в таком случае может улучшаться поток, имеющий несколько неполноправных владельцев? В такой ситуации очень хорошо подходит поговорка «тянуть одеяло на себя». Однако, как уже было сказано, картирование позволяет увидеть весть поток целиком, от начала до конца, вместе со всеми видимыми потерями. Такое визуальное представление создания продукта позволяет каждому из менеджеров по-новому взглянуть на процесс его изготовления. Уверен, что при первом применении КПСЦ менеджеры различных его частей откроют для себя достаточно много новой и интересной информации, на которую ранее они просто не обращали внимание, информацию не только о чужих сферах ответственности, но и о своей. Это нормальное явление, этого не надо стесняться и противиться. Некоторые руководители могут принципиально отказываться от применения такого рода визуализации за ненадобностью, ссылаясь на огромный опыт и безграничную компетенцию, позволяющую им в памяти полностью воспроизвести предполагаемую картину. Такие частые ответы, как «зачем мне это», «я лучше всех знаю, как это происходит», «все проблемы в…, зачем нам что-то строить» и подобные являются нормальным явлением и должны восприниматься как издержка нашего ремесла – процесса совершенствования. Восприятие командной работы и визуализации при работе с КПСЦ в данном случае трактуется как некие сомнения в их компетенции. Разумеется, мы понимаем, что это не так, но этого мало. Для того чтобы это объяснить, нужны аргументы. Ни в коем случае не стоит подвергать сомнению компетенцию таких руководителей: вряд ли кто-то сознательно пытается скрыть потери. В конце концов, любой адекватный человек приходит на работу, чтобы получить удовлетворение, увидев результаты своего труда, но никак не навредить организации. В данном случае срабатывает, как я его называю, механизм «замыливания глаз», когда человек, на протяжении долгого времени совершая одни и те же действия, перестаёт обращать внимания на мелочи, выпадающие из постоянного фокуса его внимания, и не замечает их изменений. Механизм «замыливания глаз» можно наблюдать у любого человека, в том числе и у нас с вами. Вспомните, когда последний раз посторонний человек делал вам какое-либо элементарное замечание, на которое вы просто не обращали внимание, а потом удивлялись – как вы этого не заметили сами? Знакомо? Визуализация, применимая в большинстве инструментов lean, отчасти направлена на борьбу с эффектом «замыливания глаз». Отображённая визуально, к примеру, карта потока содержит в себе информацию, знания, которыми владела разрабатывающая её группа. Это некий визуальный накопитель знаний, которым может воспользоваться (что-либо добавить или почерпнуть) любой имеющий удовлетворительное зрение человек.
Как же привести разумные аргументы о необходимости визуализации КПСЦ? Самый действенный способ, не затрагивая вышеизложенные аргументы, это попросить скептически настроенного руководителя выступить в роли эксперта, воспользоваться его «безграничным опытом и знанием процесса». Ему не надо что-либо строить или рисовать, пусть он проверит знания группы, изложенные в виде КПСЦ, возможно, и произойдёт обратное. Ни в коем случае не стоит пропускать ни один шаг алгоритма построения КПСЦ ни под каким предлогом. Помните, правильное применение инструмента многократно увеличивает эффективность его работы, а это возможно лишь при безусловном выполнении всех шагов и этапов алгоритма. Правильное применение инструмента позволяет достичь желаемого результата, что, в свою очередь, прибавляет уверенности в работоспособности и эффективности lean инструментов и мотивирует на дальнейшие улучшения, формируя у человека желание успешно применить инструмент повторно. Со временем появляются соответствующие навыки, формируется новое мышление и культура, направленная на дальнейшие улучшения. Такая культура будет требовать всё более сложные инструменты и глубокие знания для дальнейших улучшений (см. рисунок 3.1). Любая организация, внедряющая методы lean и исповедующая принципы lean, стремится к такой культуре. Чего искренне желаю и вам.
Так всё-таки, зачем необходимо КПСЦ?
Какой большой ни была бы организация, сколько бы сотрудников в ней ни работало, кормит её основной, создающий ценность процесс, а прибыль поступает от реализации продукта (услуги). Вспоминая универсальное правило Парето: «80 процентов причин обусловлено 20-ю процентами следствий» (и наоборот) и применяя его в настоящей ситуации, выводы будут следующие.
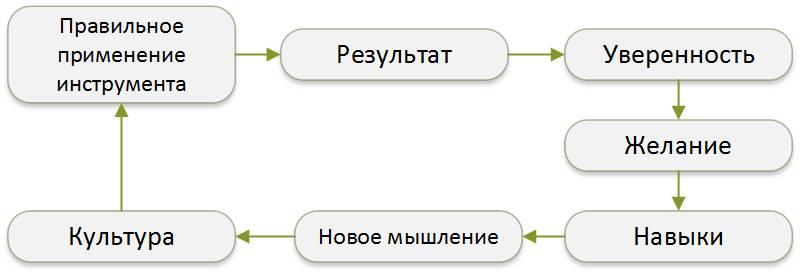
Рис. 3.1
Воздействовав на создающий ценность процесс, мы улучшаем «кормушку» организации максимально эффективным способом, т. е. именно в том месте, где это принесёт максимальную пользу. Выравнивая поток, оптимизируя запасы и избавляясь от прочих проблем, мы не только высвобождаем финансовые средства и деньги, но и формируем необходимый в организации корпоративный дух.
Как уже говорилось, применение КПСЦ в основном ориентировано на выравнивание потока и оптимизацию запасов для своевременного удовлетворения потребности Заказчика с минимальными издержками. В данном случае межоперационные запасы или незавершённое производство (НЗП) является индикатором разбалансированности потока. Если последующая стадия процесса (например, операция) не успевает перерабатывать то, что получает от предыдущей стадии, то, как следствие, между ними скапливаются запасы. Или наоборот, если последующая стадия процесса перерабатывает быстрее, чем успевает производить предыдущая стадия, соответственно будут иметь место её периодические простои. Таким образом, применение КПСЦ позволяет выявить и сократить такие потери, как перепроизводство, излишние запасы, время ожидания, излишнюю транспортировку, дефекты и переделки в привязке к соответствующим операциям процесса. Это, в свою очередь, может помочь улучшить такие показатели, как «эффективность потока» или доля времени создания ценности (см. раздел 9), «время прохождения продукта», уровень дефектности и другие (см. приложение 4).
Может показаться, что выше изложено описание некого универсального инструмента на все случаи жизни, позволяющего решить большинство проблем организации и устремиться к «светлому будущему». Возможно, так оно и есть. Не буду ни приукрашивать, ни отрицать: выше изложены далеко не все возможности и не так красочно и ярко, как можно было бы это сделать. Разумеется, всё зависит от желания и правильного применения инструмента.
Конец ознакомительного фрагмента.
Текст предоставлен ООО «ЛитРес».
Прочитайте эту книгу целиком, купив полную легальную версию на ЛитРес.
Безопасно оплатить книгу можно банковской картой Visa, MasterCard, Maestro, со счета мобильного телефона, с платежного терминала, в салоне МТС или Связной, через PayPal, WebMoney, Яндекс.Деньги, QIWI Кошелек, бонусными картами или другим удобным Вам способом.
Примечания
1
Эффективность – это достижение каких-либо определённых результатов с минимально возможными издержками или получение максимально возможного объёма продукта из данного количества ресурсов.
2
Канбан – метод управления производством по вытягивающей системе. Заключается в подаче сигнала о начале производства или доставке изделий с одного процесса на другой при помощи бирок, карточек, тары, электронных сообщений.
3
Шивера – относительно мелководный (глубина до 1,5–2 м) участок реки с беспорядочно расположенными в русле подводными и выступающими из воды камнями и быстрым течением.
4
Андон – сигнальная система, либо устройство визуального оповещения о состоянии процесса или оборудования.
5
6 сигм – концепция управления производством, суть которой сводится к необходимости улучшения качества выходов каждого из процессов, минимизации дефектов и статистических отклонений в операционной деятельности.