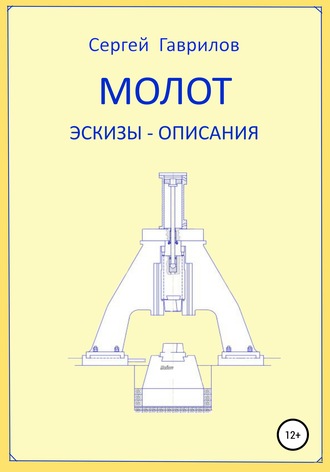
Полная версия
Молот. Эскизы-описания

Введение
Инженер конструктор отдела гл.механика Гаврилов Сергей Фёдорович написал эту книгу для конструкторов, студентов механиков и механиков цехов. Данная книга содержит эскизы узлов и деталей молота близкие к рабочим чертежам, некоторые расчеты и подробное описание двух стоечного арочного паровоздушного молота двойного действия. Приведены инструкции по работе на молоте, по ремонту и обслуживанию молота.
Описанный молот интересен тем, что выпущен в 1884 году английской фирмой, в настоящее время не существующей, установлен 1896 г. и успешно работает по сей день. Все основные детали молота остались фирменными, что подтверждает правильность выбранной схемы молота, выбранных материалов и расчетных коэффициентов.
Молот
История.
Молот был установлен еще в царское время. Работал молот от паропровода с давлением пара 12 кгс/кв.см. Где то в 2010 году экономисты решили, что работа на пару обходится дорого и перевели питание молота на сжатый воздух давлением на входе в молот равное 6 кгс/кв.см. . Перевод произвели упрощенно – магистральный паропровод к цеху отрезали от общезаводского паропровода и подсоединили к общезаводской магистрали сжатого воздуха. Внутри цеха ничего не менялось. В литературе было указано, что при резком расширении сжатого воздуха, его температура сильно понижается и вода, содержащая в воздухе, замерзает. Подвод сжатого воздуха производится трубопроводом Ду = 80 мм. Перед молотом установлен влаго отделитель в виде двух последовательно соединенных баков емкостью примерно по 100 литров, оборудованных вентилями сброса конденсата. Влаго отделители выполняли, так же функции пневмо аккумуляторов. Возможно наличие влаго отделителей убрало эффект образования льда в цилиндре молота – льда в деталях молота при работе не наблюдалось. Конечно, сила удара уменьшилась, но всю номенклатуру заготовок, необходимую для заводских ремонтов, на молоте ковать получалось. Возможно, молот по заводу перемещали, так как я, работая на заводе двадцать шесть лет, дважды обеспечивал конструкторской документацией капитальный ремонт этого молота с полной разборкой, с частичным разрушением и восстановлением фундамента молота. Все это время также обеспечивал чертежами текущие ремонты молота.
# ........
Причины появления этой книги: В настоящее время в технической литературе очень мало конкретных данных по устройству, конструкции узлов и деталей. Редко приводятся реальные цифры. Автор постарался подробно раскрыть устройство узлов и деталей молота. Молот фирмы английской фирмы получился удачным и заслуживающим изучения. Редко какой молот, может работать более ста лет, сохраняя в целости все основные фирменные детали. Автор подробно описывает устройство молота, иллюстрирует эскизами узлов и деталей, приводит некоторые расчеты, описывает технологию ремонта фундамента молота и ремонта самого молота, приводит справочные данные. Приводит выдержки из технологической инструкции и инструкции по эксплуатации молота. Приведены необходимые справочные таблицы и формулы, часто используемые в расчетах.
Основные узлы молота
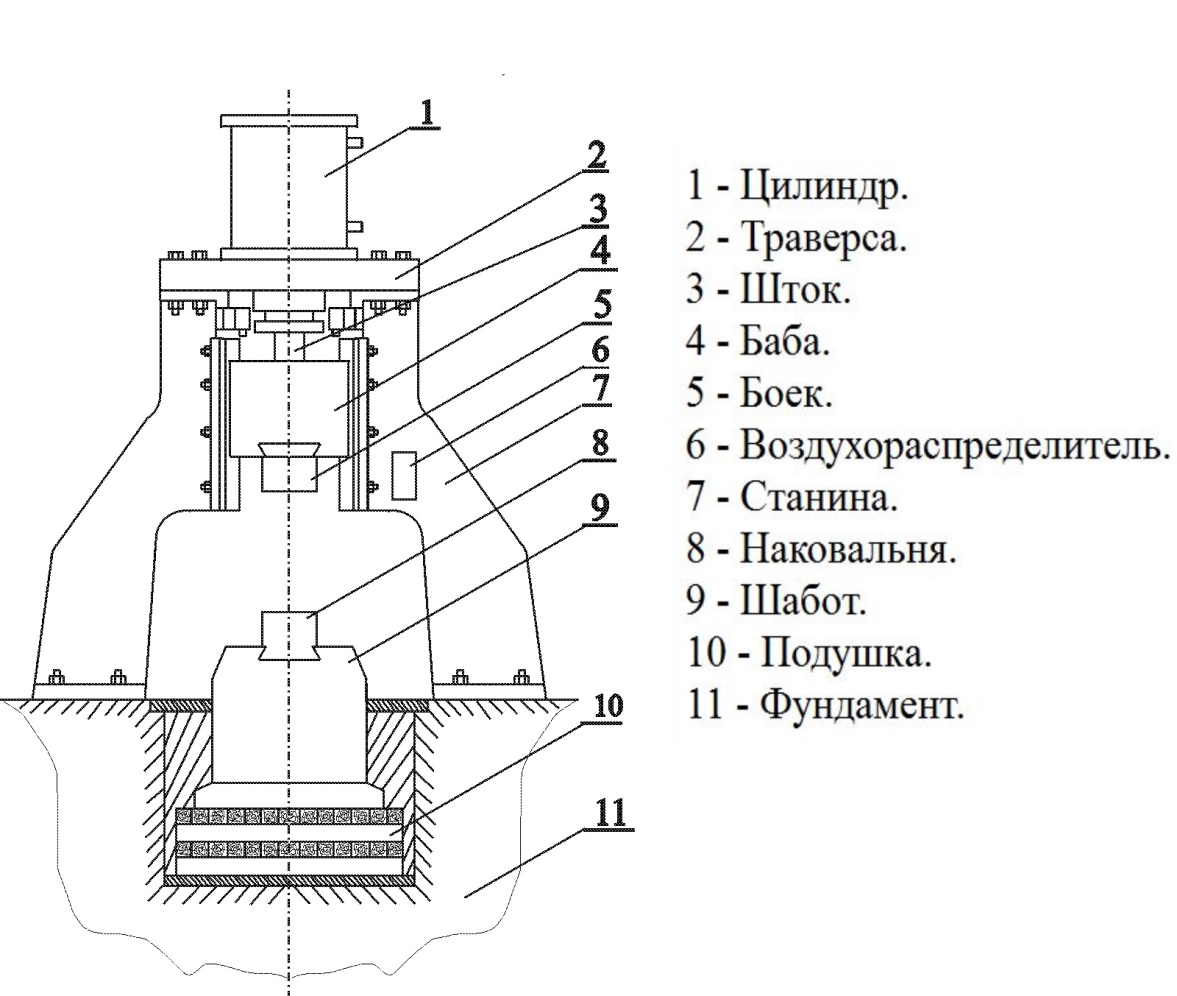
Преимущества и недостатки
Преимущества молота: Молот, при одинаковых размерах обрабатываемой поковки, значительно легче и меньше по размерам, чем ковочный пресс. За счет искусного умения кузнеца, на молоте можно выполнять сложные по конфигурации поковки используя простые и дешевые приспособления. Для исполнения подобных поковок на ковочном прессе нужны сложные и дорогие штампы и матрицы. Для привода молота достаточно иметь доступ к общезаводскому паропроводу или воздухопроводу. Пар и сжатый воздух все равно нужен заводу – поэтому стоимость привода молота, это малый процент от общезаводского паро или пневмо снабжения. Сложных систем управления молоту не требуется. Простой молота или включение молота мало влияют на загруженность общезаводского ресурса. Для пресса же необходим специализированный индивидуальный или групповой гидропривод, электропривод, достаточно сложные системы управления и, как правило, системы охлаждения.
Пресс в сумме с приводами и системой управления занимает значительно больше места.
В итоге: При организации ремонтной службы молот предпочтителен.
Недостатки молота: Работа на молоте более опасна, чем на прессе. Молот – динамическая система. При ударе, молот стремится порвать фундаментные болты, пробить шаботом дно фундамента, оторвать траверсу от станины, цилиндр от траверсы.
При ошибке кузнеца – инструмент выбивает из рук, в кузнеца может попасть кусок горячей окалины или кусок металла. Кузнец подвергается тепловому облучению.
При ударе молота возникают сильные колебания почвы вокруг кузницы. В конторе в двухстах метрах от молота, в отдельном здании, компьютеры содрогались от ударов молота. Понятно, что точные станки, сложную электронику поблизости от молота располагать нельзя. Пресс, в отличии от молота, замкнутая система. Пресс работает почти бесшумно, сотрясений почвы не вызывает, фундамент динамическими нагрузками не разрушает. Пресс предпочтительней при организации массового производства.
Фундамент молота
Фундамент молота должен превосходить вес падающих частей молота в 80…100 раз. Крымский стр. 120. Рассматриваемый молот имеет вес падающих частей равный 3000 кгс. Значит вес фундамента должен быть не менее 270 тонн. Размеры фундамента в плане 5200 * 3600 при глубине 3980 мм по весу получается меньше рекомендованного примерно в два раза. Полного комплекта чертежей фундамента в цехе нет – утеряны. При ремонтах используются ремонтные чертежи ремонтируемых фрагментов фундамента.
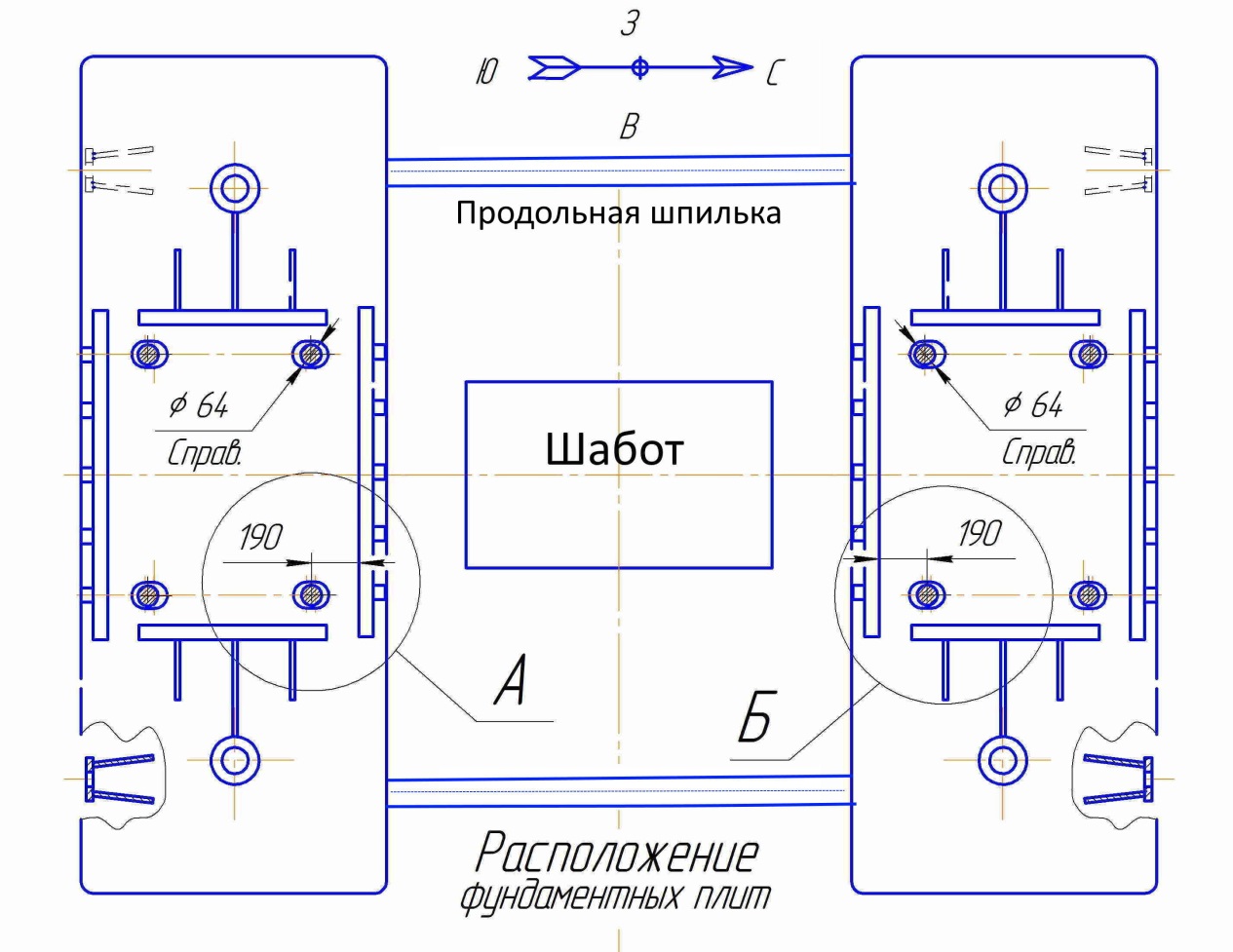
Основания северной и южной станин молота опираются на фундаментные плиты.
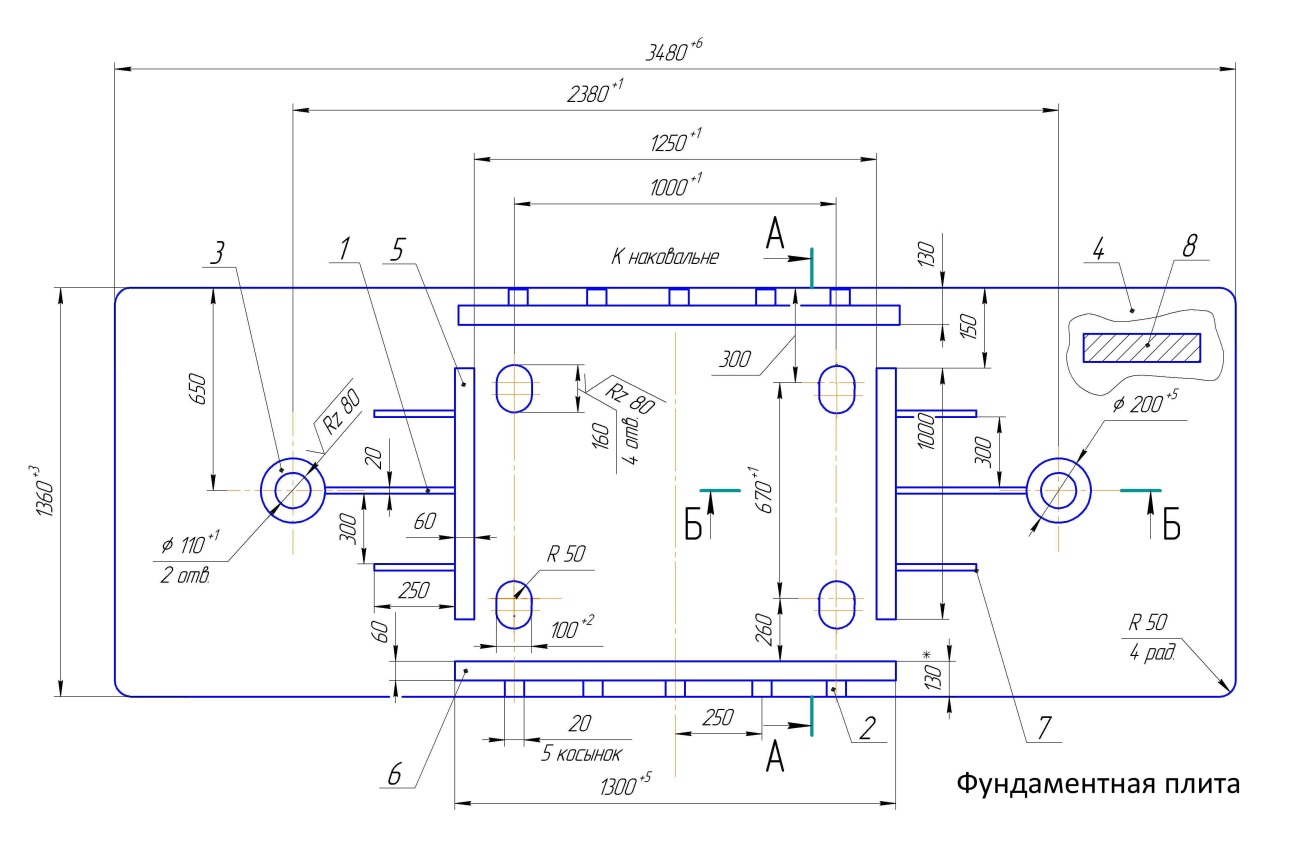
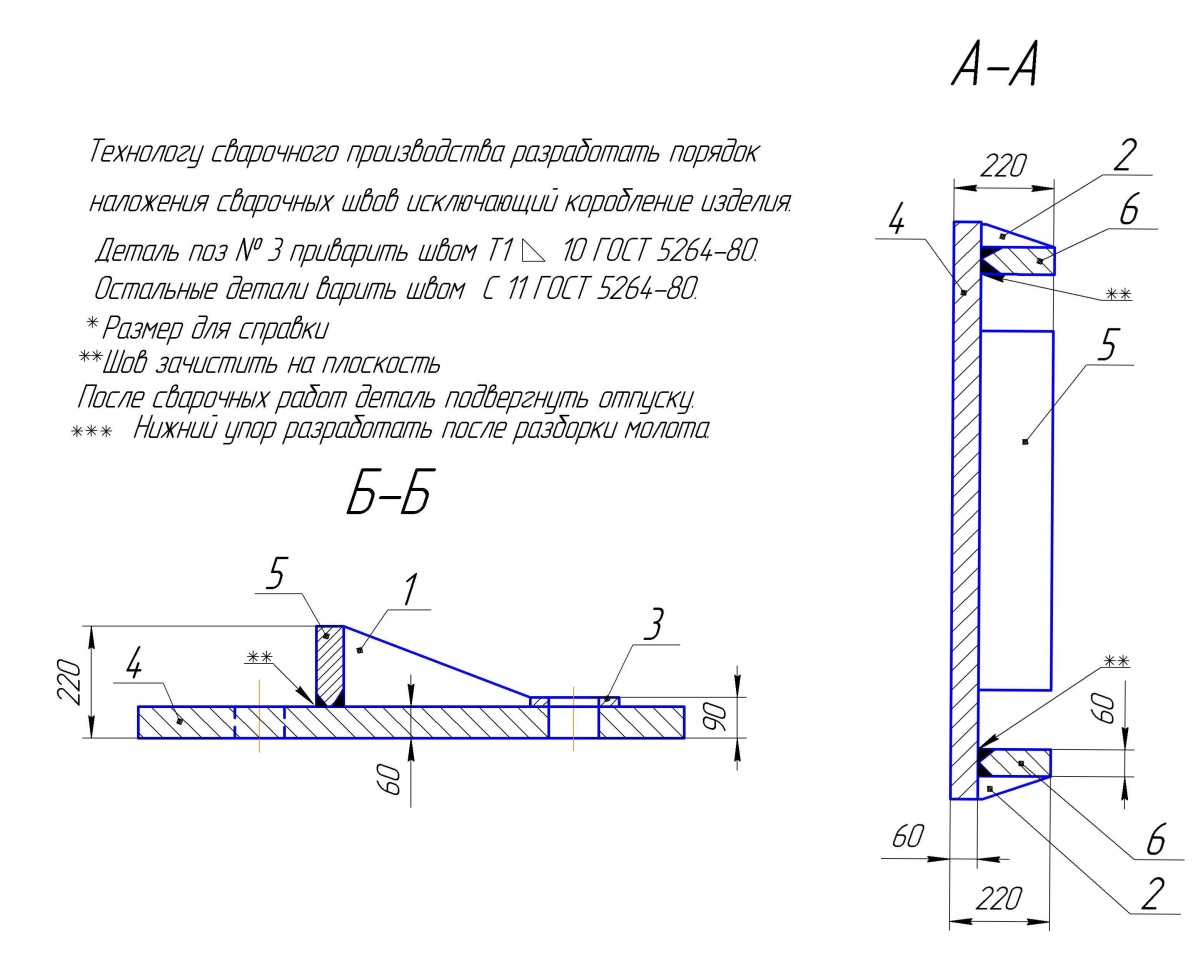
Фундаментные плиты забетонированы в фундамент и притянуты к фундаменту анкерными шпильками и стянуты между собой продольными шпильками.
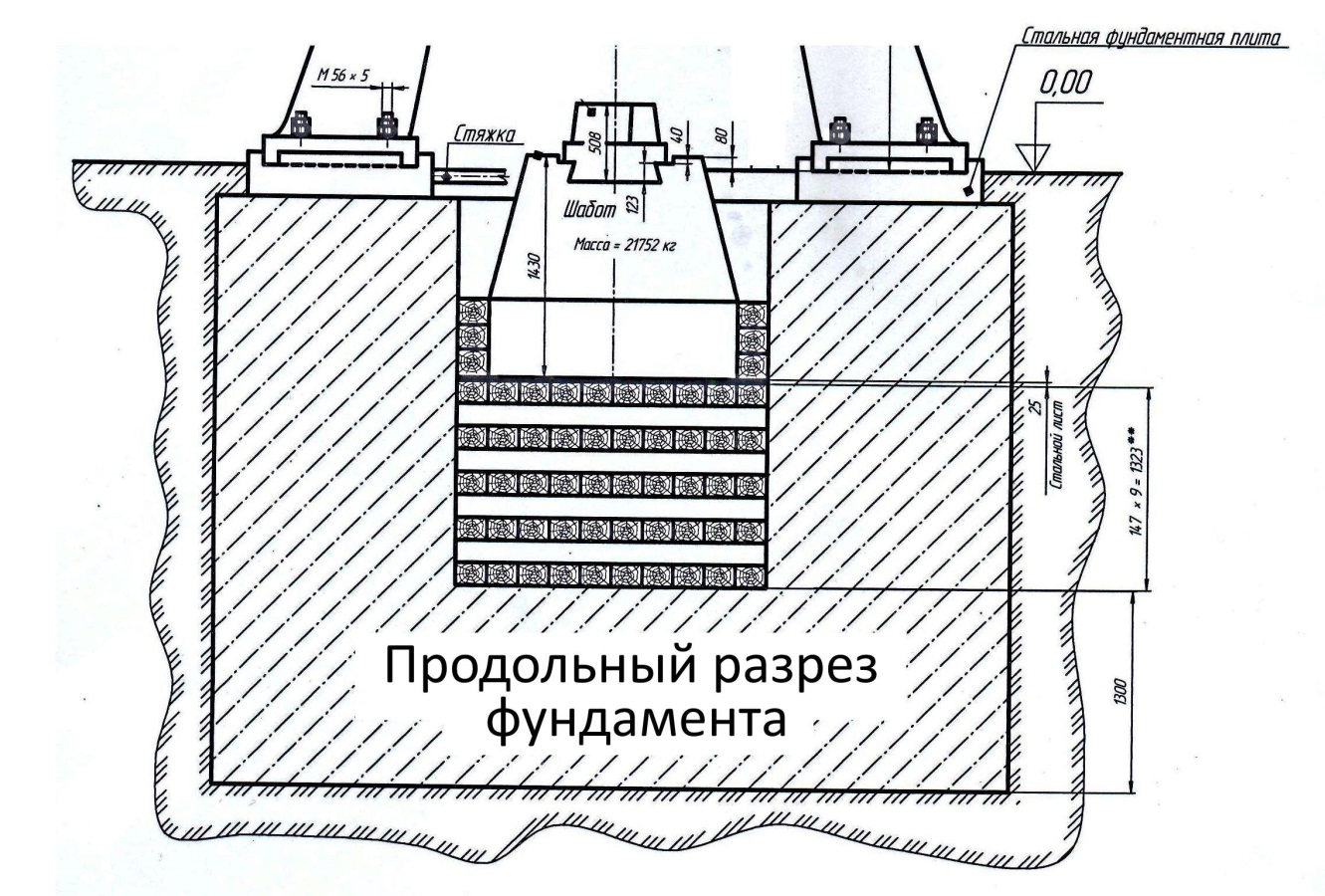
Перед ремонтом фундамента на полу кузницы определяют реперные точки, относительно которых замеряют текущее положение анкерных болтов молота в плане относительно реперных точек и высоту положения основных элементов фундамента относительно высотной реперной точки принятой за условный « ноль » высоты .
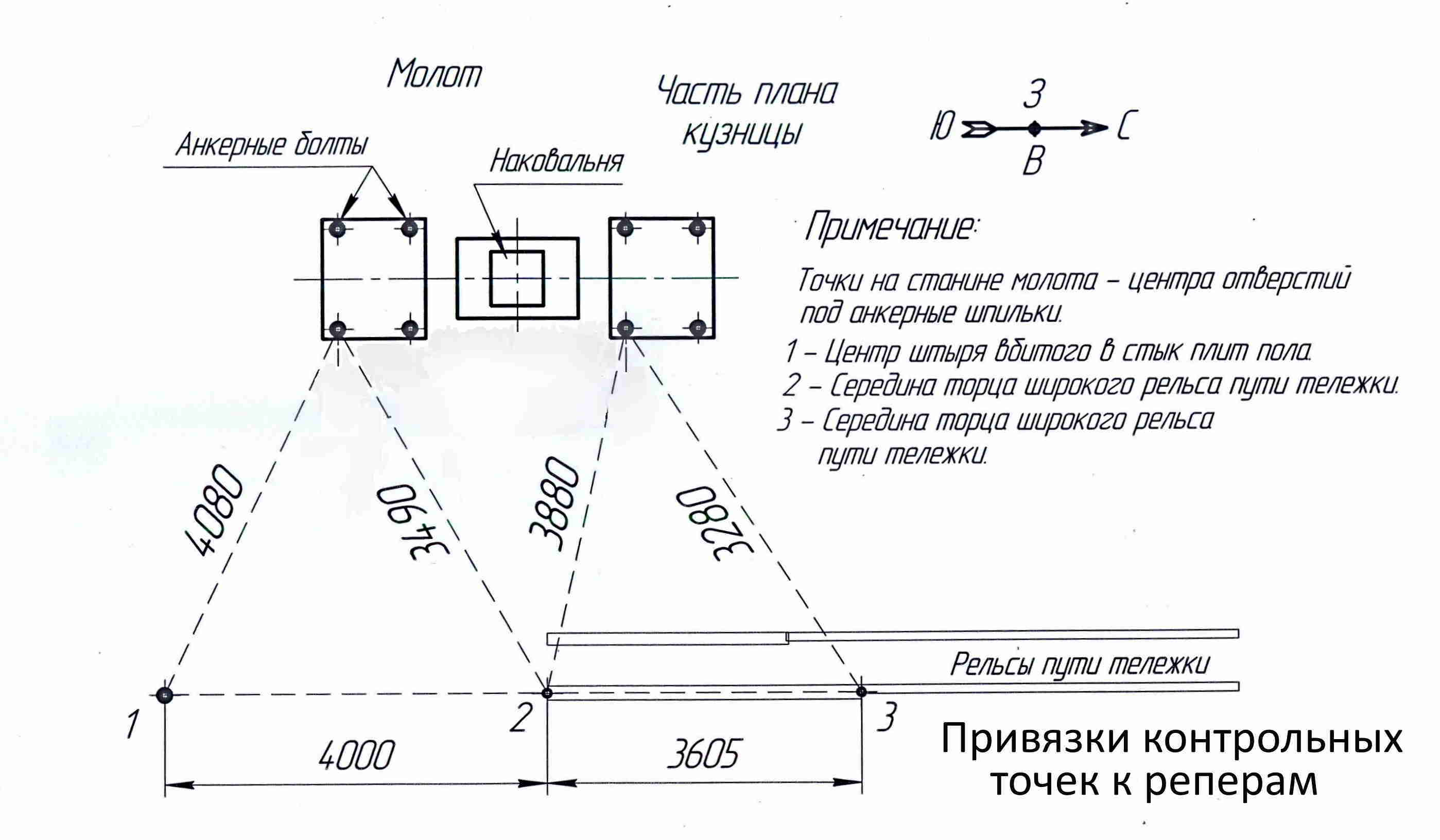
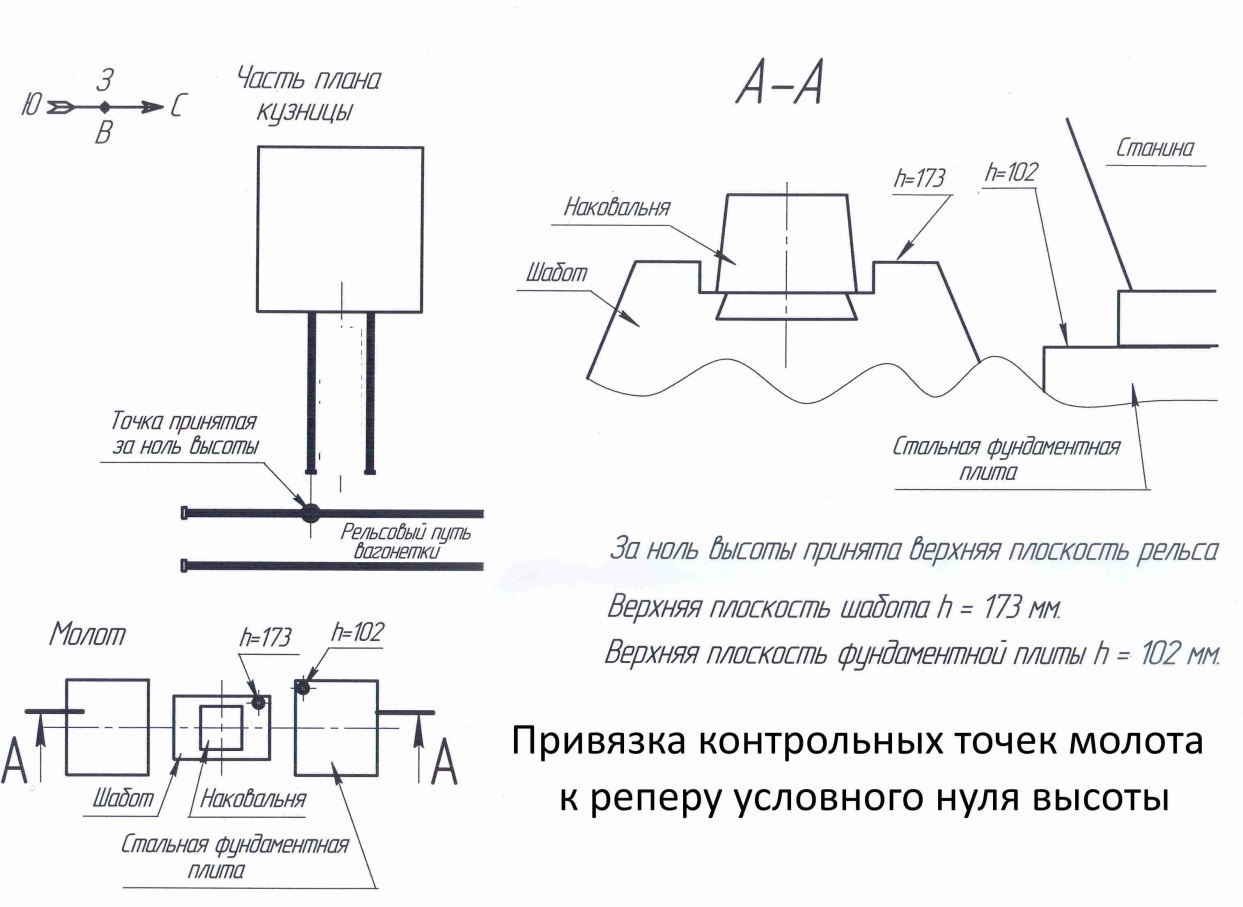
После разборки молота – станины молота монтируются на приспособление
« Фальшбаба ». Две одинаковых Фальшбабы устанавливают на станины, одну сверху, другую снизу, вместо направляющих, для установки станин молота строго в проектное положение. Станины, через фальшбабы, жестко стягиваются болтами в единое целое. Станины выкладываются в сборе в положение удобное для замеров. В отверстия станин, предназначенные под анкерные шпильки, вставляем стальные, слегка конические, пробки с четко обозначенными центрами в виде неглубоких отверстий Ф 2 мм. затем
замеряется фактическое межцентровое расстояние отверстий анкерных шпилек.
По эскизу фактических межцентровых будут располагать новые анкерные шпильки.
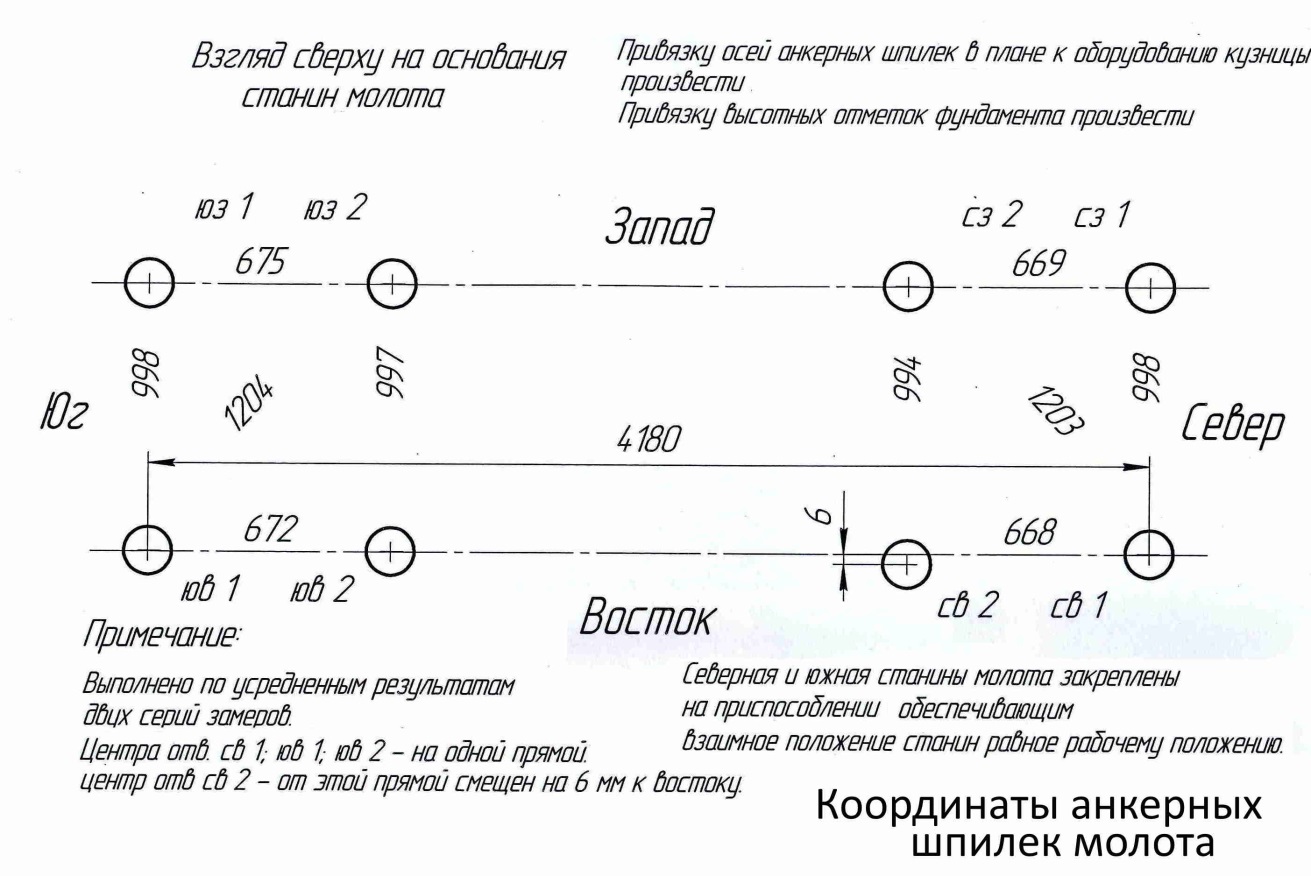
После фактического определения координат анкерных шпилек – делаются установочные шаблоны в которые устанавливают анкерные шпильки, индивидуально для северной и южной станин.
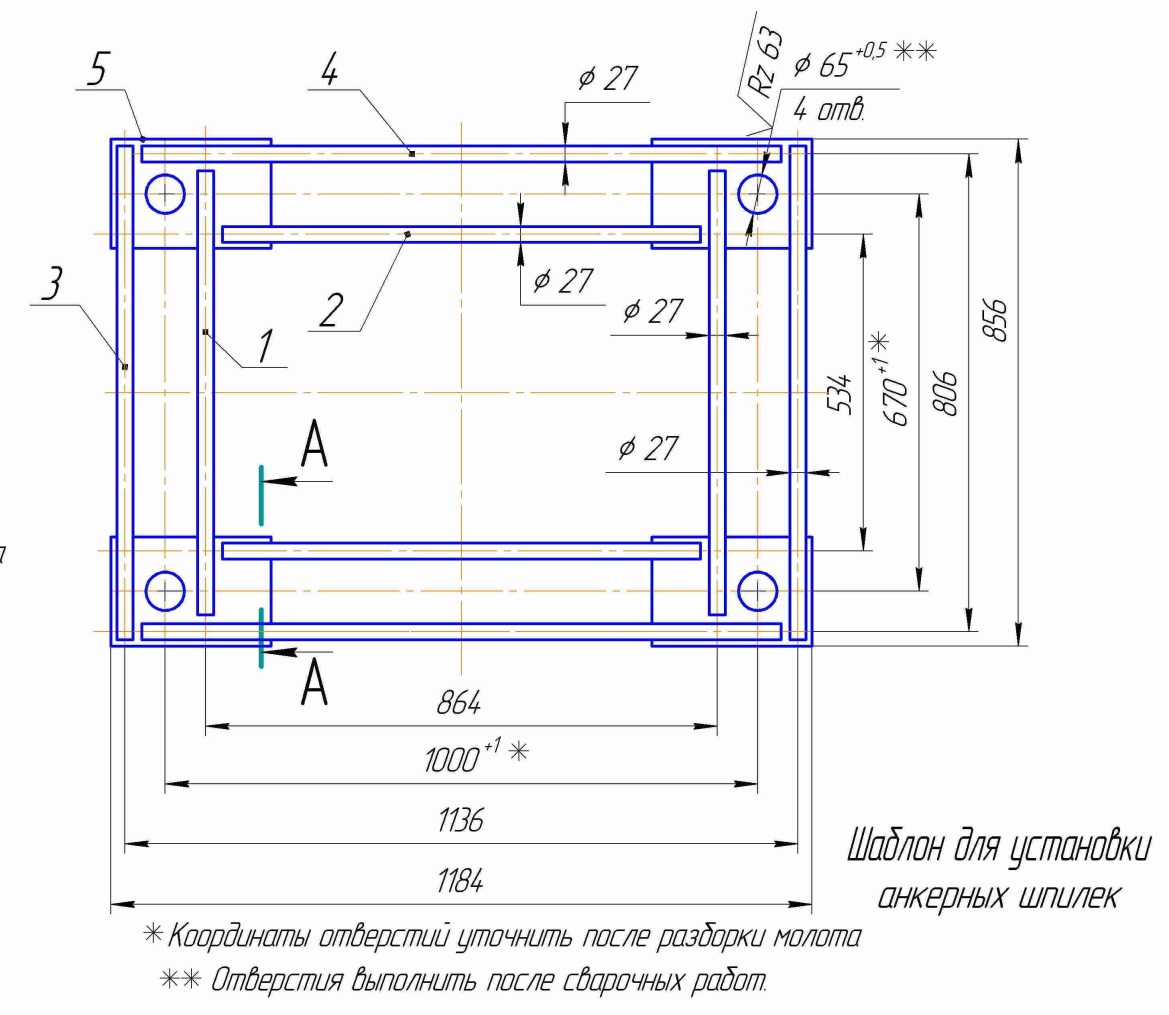
После выборки необходимого объема старого бетона, в оставшемся бетонном массиве старого фундамента сверлят отверстия в шахматном порядке с шагом 400 мм.
Отверстия сверлить Ф 60 мм, глубиной 400 мм. В отверстия установить прутки арматурной стали L = 800 мм. Пруток 2ф – МД1-15 А 400 ГОСТ 34028-2016. Котлован зачистить от мусора. Промышленным пылесосом удалить пыль и мелкие крошки, смочить поверхность котлована водой. В котлован устанавливают кессон для колодца Шабота. Кессон загружают металлом по расчету отрицательной плавучести кессона в жидком бетоне ( удельный вес жидкого бетона принимаем примерно 2,5 тонны на кубометр ).
В котлован устанавливают шаблоны, в шаблоны устанавливают анкерные шпильки. Все тщательно выверяется по координатам в плане и по высоте верхних торцов шпилек и по вертикальности шпилек. Шаблоны и шпильки привязывают эл.сваркой к арматуре фундамента, к кессону и окончательно выверяется. Бетонирование вести бетоном класса В-30 на цементе марки 400 с вибро уплотнением. Все заливают бетоном до отметки немного ниже нижних точек фундаментных плит. Одновременно с заливкой основного массива бетона – в формы заливают контрольные образцы бетона, которые затем проверяют в лаборатории на прочность. Когда бетон немного затвердеет – устанавливают фундаментные плиты. Стягивают фундаментные плиты продольными шпильками в проектное положение. Выставляют фундаментные плиты на проектную высоту и плоскости для опоры станин выставляют в единую плоскость. После выверки и геодезического контроля, производится подливка фундаментных плит бетонным раствором повышенной текучести с вибро уплотнением. Примечание: Ориентировочно для заливки фундамента необходимо четырнадцать куб.м. бетона.
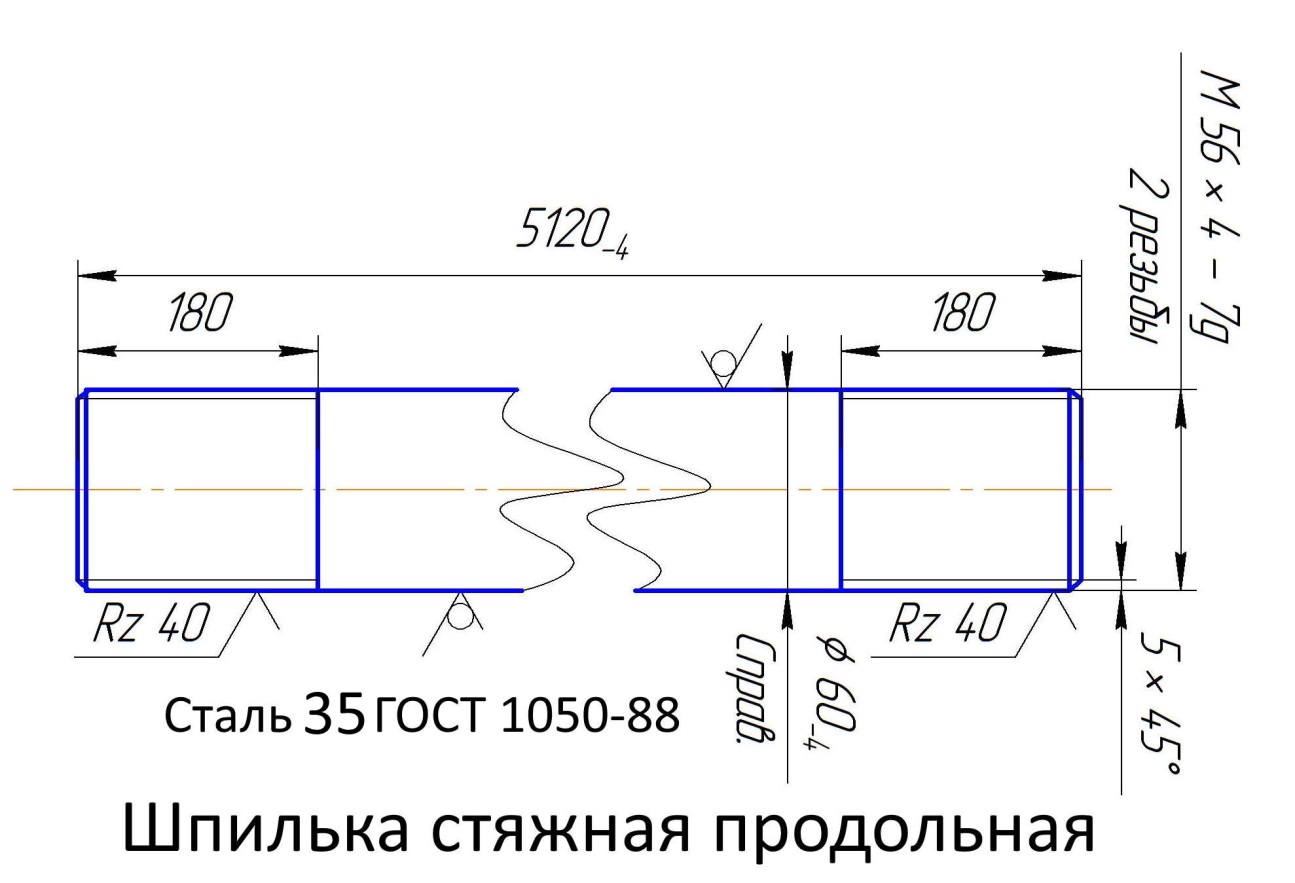
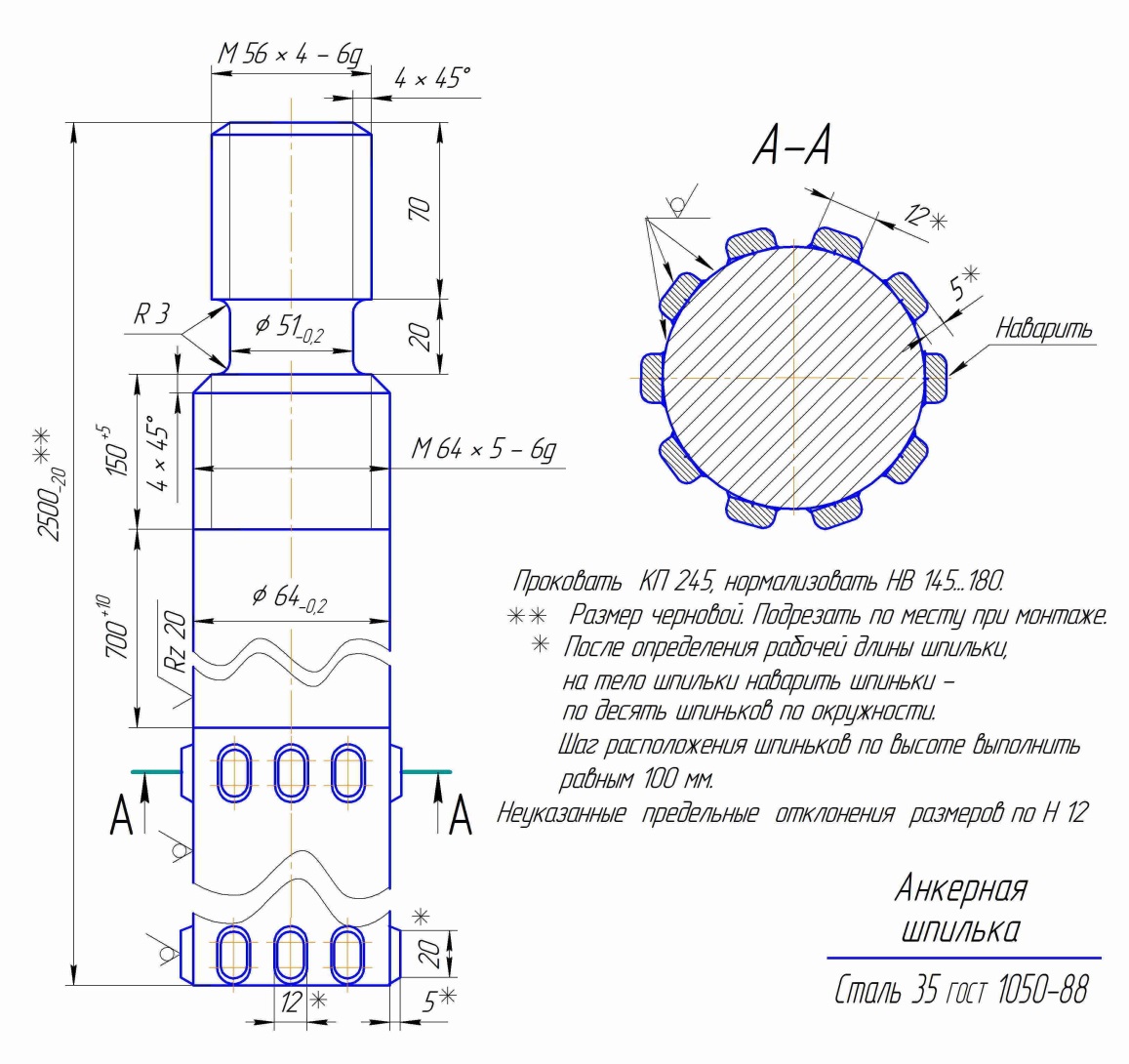
Хронометраж ремонта молота:
Разборка молота = два дня. Разборка фундамента, фундамент долбим гидрокопьем установленным на экскаватор с гидроприводом. Обломки бетона убираем вручную.
Сверлим отверстия алмазным сверлом пневмосверлильной машинкой. = двадцать один день. Окончательная очистка котлована, обеспыливание промышленным пылесосом = один день. Армирование котлована, установка шаблонов, установка анкерных шпилек, установка кессона и временных опор, выверка всех элементов и контроль геодезистами = десять дней. Заливка котлована бетоном. Установка и окончательная выверка фундаментных плит, подливка под плиты, выдержка для набора прочность бетоном = шесть дней. Монтаж молота на фундамент, выверка, регулировка, запуск в работу = восемнадцать дней. В среднем бригада монтажников состояла из шести человек. Бригада строителей тоже состояла из шести человек.
Причины ремонтов фундамента: Ремонт в начале 2000 г. пришлось произвести потому, что дно колодца, в котором находился шабот, не выдержало и провалилось – шабот осел. Кроме того было частично оборваны анкерные шпильки. При ремонте укрепили дно колодца под шабот, заменили шпалы подушки, старые шпильки частично срезали и сваркой в стык, с разделкой кромок приварили новые верхние части шпилек. Выполнили текущий ремонт износившихся деталей. Через четырнадцать лет – три анкерные шпильки на южной станине оборвались без возможности их восстановления. Осталась целой только одна фундаментная шпилька из четырех. Шпильки жесткие, свободная длина шпильки мала, станина тоже жесткая. Нагрузка от удара между фундаментными шпильками практически не распределяется, нагружена только одна, наиболее затянутая шпилька. Ударная нагрузка приводит к образованию усталостной трещины и шпилька рвется. Все фундаментные шпильки обрывает по нижнему торцу гайки, перпендикулярно оси шпильки. Далее рвется следующая наиболее затянутая шпилька. После обрыва на южной станине трех фундаментных шпилек из четырех– молот проработал на одной оставшейся шпильке с резьбой М 52 шаг 5 мм. еще двадцать два месяца.
Этот случай позволил достоверно, экспериментально, определить усилие отдачи станины молота от фундамента. Параметры шпильки: Резьба шпильки М 52 шаг 5 мм. Внутренний диаметр Ф 46,587 мм. Площадь сечения S = 1705 кв.мм. Сталь 30 ГОСТ 1050-88
Предел прочности 50 кгс/кв.мм. Предел текучести 30 кгс/кв.мм. При коэф. запаса К=1,35. Допустимая нагрузка на шпильку F = 30*1705/1,35 = 37889 кгс. Значит ударная сила отдачи на одну станину не превышает 37889 кгс. Шпилек четыре, на одну шпильку нагрузка равна 9472 кгс. Qот = 9472 кгс. Сила отдачи станины при ковке на одну шпильку.
При ремонте, резьбу шпилек увеличили и сталь 30 заменили на сталь 35 ГОСТ 1050-88.
Допустимая нагрузка: Для анкерной шпильке с резьбой М 64 шаг 5 мм.
Внутренний диаметр резьбы 58,587 мм. Площадь поперечного сечения S = 2696 кв.мм.
По ГОСТу предел текучести шпильки из стали 35 Вт = 3150 кгс / кв.см.
Допускаемое напряжение при пульсирующей нагрузке Вп = 1250 кгс/кв.см.
В.И. Анурьев Т1 справочная таблица стр 86.
Допустимое усилие затяжки шпильки Fз = S * Вп / 1,35. Fз = 26,96*1250 / 1,35.
Fз = 24963 кгс. Шпильки прочны.
Для выравнивания нагрузки между шпильками и для гашения удара была предложена:
Кольцевая пружина
Кольцевая пружина для предохранения анкерных шпилек от перегрузок.
Материал пружины Сталь 60С2Н2А ГОСТ 14959-79.
Первый класс – циклическая нагрузка на Пять миллионов циклов
по Анурьеву выпуска 2001 г. – Десять миллионов циклов
из сталей 60С2А и 65С2ВА ГОСТ 14963-69 HRC 46 … 52..
и из стали 50ХФА ГОСТ 14963-69 HRC 44 … 50..
допускаемое касательное для этих сталей не более 56 кгс/кв.мм.
Применим сталь 60С2А ГОСТ 14959-79. Предел текучести 143 кгс/кв.мм.
Предел прочности 163 кгс/кв.мм. Ресурс принимаем = 5000000 циклов.
Допускаемое напряжение на растяжение Вд = 9600 кгс / кв.см.
Закалка с 870 градусов в масло затем отпуск с 420 градусов..
Рассчитываем наружное кольцо пружины при работе испытывающей напряжения
растяжения. Внутренняя пружина испытывает напряжения сжатия – что менее опасно.
Величины напряжений и деформация при равенстве поперечных сечений одинаковы.
Поэтому внутреннее кольцо считать не будем.
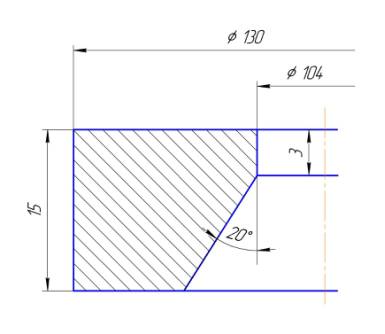
Кольцевая пружина – внешнее кольцо.
Pii = 3,1415926 … Число Пи…
Е = 2000000 кгс / кв.см. Модуль упругости стали..
Максимальное осевое усилие вдвигающее конус в коническую расточку кольца принимаем равной: Q = 20000 кгс. При силе отдачи станины на одну шпильку равной
Qот = 9472 кгс.
Предполагаемый коэф. трения на конусе: Ктр = 0,1.. ( вибрация уменьшает трение)..
Угол трения: Gt = arctan ( 0,1 )… Gt = 5,6666666º…
Наружный диаметр кольца: Ф = 130 мм.
Внутренний цилиндрический участок: Фв = 104 мм. Длина Lв = 3 мм.
Полная высота кольца пружины L = 15 мм.
Коническая расточка внутреннего диаметра:
Угол: Образующая – Ось кольца: G = 20º.. Высота расточки Lк = 12 мм.
Наибольший диаметр расточки: Фк = ( Lк × 2 × ( tan 20º )) + Фв.. Фк = 112,7353 мм.
Площадь поперечного сечения кольца пружины: S = 1,68794 кв.см.
Объем кольца пружины: V = 62,8739 куб.см.. Масса = 0,49356 кг…
Средний диаметр кольца пружины: Фср = V / ( S × Pii )…
Фср = 62,8736 / ( 1,68794 × 3,1415926 ) .. Фср = 11,85662 см… Фср = 118,5662 мм.
Gsf = 461030/2725231222…
Так как угол трения значительно меньше угла конуса – при снятии нагрузки пружина
вернется в исходное положение.. При этом часть энергии израсходуется на трение на
конусе – поэтому колебания при снятии нагрузки быстро затухнут..
Удельное давление на кольцо при внедрении конуса:
.g = Q / ( Pii* Ктр*L* Фср*((0,34202/ Ктр)+0,9397)).. В.С. Поляков стр, 156..
Где: 0,3420201 – синус 20 градусов. 0,9397 – косинус 20 градусов..
20 градусов – угол осевая – образующая конуса.
.g = 20000 / ( Pii* 0,1*1,5*11,85662 *4,36).. .g = 821 кгс/кв.см.
Расчет ведем по формулам для цилиндра под давлением. По Даркову стр 674…
Радиальное напряжение:
X=g*Rv*Rv/((Rn*Rn)-(Rv*Rv))
Y=Rn*Rn/(Rv*Rv)
Br=X*(1-Y).... # Радиальное напряжение
Где: Rn = 6,5 см – Наружный радиус цилиндра.
Rv = 5,92831 см. – Внутренний радиус цилиндра.
# …
X=821*5,92831 *5,92831 /((6,5*6,5)-( 5,92831 *5,92831))…
X=4061…
Y=6,5*6,5/(5,92831 *5,92831)… Y=1,20217…
Br=4061*(1-1,20217).... Br= -821 кгс / кв.см… # Радиальное напряжение
# ....
Тангенцальное ( растягивающее ) напряжение в кольце.
Bt=X*(1+Y) # Тангенциальное напряжение
Bt=4061*(1+1,20217 ) … Bt= 8943 кгс / кв.см… # Кольцо прочно…
# …
Развернутая длина кольца Ср = Фср * Pii.. Ср = 11,85662 * Pii.. Ср = 37,24867 см.
Удлинение средней линии при напряжении Вt = 8943 кгс/кв.см. по закону Гука
.dL = Cр* Вt/Е.. dL = 37,24867 * 8943/2000000.. dL = 0,1666 см.. или увеличение диаметра dФ = 0,053017 см.. dФ = 0,53017 мм.. Так как внутреннее кольцо сжимается на ту же величину, то общее изменение диаметра dФ = 1,0603 мм.. Изменение радиуса
dR = 0,53017 мм. Осадка конуса под нагрузкой dH = dR/(tan 20).. dH = 0,53017 /0,36397..
dH = 1,457 мм.. ( осадка пары конус – кольцо, без учета трения на конусе ).
Расчет производим по И.А. Биргеру. Стр. 173..
Тангенциальное ( растягивающее ) напряжение в кольце Вt = 8943 кгс / кв.см.
Что меньше допускаемого. Пружина будет более долговечна..
# ,,,,,,,
Проверим расчет исходя из заданной осадки конуса dH = 0,7285 мм..
( без учета сжатия конуса и без учета трения на конусе ).
Изменение радиуса при осадке dR = dH * tg 20.. dR = 0,7285 * 0,36397..
dR = 0,2652 мм. Изменение диаметра dd= 0,5303 мм.
Изменившийся средний диаметр Фсри = 118,5662+0,5303 = 119,0965 мм.
Изменившаяся длина окружности Ссри =118,90389 * Pii = 374,152704 мм.
Относительное изменение длины окружности Сотн = (Ссри–Ср) / Ср..
Сотн = (374,152704 –372,486703) / 372,486703.. Сотн = 1,666 / 372,486703..
Сотн = 0,00447265… Далее по закону Гука..
При таком относительном удлинении напряжение растяжения будет:
Врас = Е * Сотн… Врас = 2000000 * 0,00447265… Врас =8945,3 кгс/кв.см.
Для пружинной стали напряжение нормальное..
С учетом того, что коническая часть входящая в кольцо имеет равное кольцу
поперечное сечение т сожмется на ту же величину, то в целом осадка удвоится
и будет равной 1,457 мм.
# ,,,,,,
Тот же самый расчет по И.А. Биргеру. Но при коэф.трения = 0,01.. Gt = 0,57º…
Площадь поперечного сечения кольца пружины: S = 1,68794 кв.см.
Напряжение растяжения: Вр = Q / ( Pii*S*tan ( G + Gt ))…
Вр = 20000 / ( Pii*1,68794*tan ( 20 + 0,57 ))… Вр = 10048 кгс / кв.см.
Осадка конуса в кольцо пружины при приложении назрузки:
dH = Q*Фср / ( 2*Pii*E*tan ( G )*tan ( G + Gt )*S )…
dH = 20000*11,85662 / ( 2*Pii*E*tan ( 20 )*tan ( 20,57 )*1,68794 )…
dH = 0,08 см.. dH = 0,8 мм. С учетом того, что наружное кольцо и внутреннее
кольцо работают в паре и жесткость внутреннего примерно = наружного, то суммарная
осадка пары колец: dH = 1,6 мм..
Реальный результат будет между результатами этих двух расчетов..
# ,,,,,,,,,,,,
Расcчитаем кольцевую пружину по формулам книги Р. С. Курендаш стр 98…103..
По расчетам приведенным выше:
Расчетное усилие принимаем Q = 20000 кгс.
Угол: Образующая – Ось кольца: G = 20º.. Высота расточки Lк = 12 мм.
Предполагаемый коэф. трения на конусе: Ктр = 0,1.. ( вибрация )..
Угол трения: Gt = arctan ( 0,1 )… Gt = 5,6666666º…
Наибольший диаметр расточки: Фк = ( Lк × 2 × ( tan 20º )) + Фв.. Фк = 112,7353 мм.
Площадь поперечного сечения кольца пружины: S = 1,68794 кв.см.
Объем кольца пружины: V = 62,8739 куб.см.. Масса = 0,49356 кг…
Средний диаметр кольца пружины: Фср = V / ( S × Pii )…
Конец ознакомительного фрагмента.
Текст предоставлен ООО «ЛитРес».
Прочитайте эту книгу целиком, купив полную легальную версию на ЛитРес.
Безопасно оплатить книгу можно банковской картой Visa, MasterCard, Maestro, со счета мобильного телефона, с платежного терминала, в салоне МТС или Связной, через PayPal, WebMoney, Яндекс.Деньги, QIWI Кошелек, бонусными картами или другим удобным Вам способом.