
Полная версия
Технический углерод. Процессы и аппараты. Дополнительные материалы
Циркониевые огнеупоры на основе окиси циркония (ZrO₂) имеют высокую огнеупорность– 2300-2400⁰С. В применении таких огнеупоров были заинтересованы многие отрасли промышленности, использующие высокотемпературные процессы, однако низкая термостойкость не позволяла применять их в чистом виде, так как при перепадах температур, которые неизбежны в промышленных аппаратах, они быстро разрушались. Термостойкость циркониевых огнеупоров удалось повысить за счёт стабилизирующих добавок: MgO, CaO, Y₂O₃ и др. Добавка к стабилизированному диоксиду циркония 10-12% моноклинной составляющей повышает термостойкость до 25 теплосмен. Это подробно изложено в источниках /1.7.5./ и /1.7.7/. Из изложенного ясно, что такие огнеупоры могут применяться в промышленности технического углерода, однако выяснилось, что в России такие огнеупоры не производились, не смотря на наличие крупного месторождения в Мурманской области. Обращение специалистов ОЗТУ к известным зарубежным изготовителям огнеупоров тоже не дали результатов. Положение изменилось только после обращения в «Украинский научно-исследовательский институт им. А.С. Бережного» Этот институт ещё в Советское время занимался разработкой огнеупоров для промышленности технического углерода.
В соответствии с заключённым в январе 2003 года договором с ОАО «Техуглерод» (Омским ЗТУ) ОАО «УкрНИИО им Бережного» разработал набивную массу и мертель из диоксида циркония на фосфатной связке, стабилизированной окисью иттрия (Y2O3) для температуры применения до 2400⁰С. Изготовление огнеупорных циркониевых блоков производилось на заводском участке по изготовлению огнеупоров.
Первый реактор с камерой горения из циркониевых блоков был запущен в начале ноября 2003 года и эксплуатировался 2 года и 7 месяцев без ремонта при средней температуре в камере горения 1940⁰С. Это был первый промышленный реактор, камера горения которого была футерована циркониевыми огнеупорами, причём, не только в отечественной промышленности, но и мировой промышленности техуглерода. В последующие годы на мировых конференциях по техуглероду (Carbon Black World) появились материалы по реакторам с футеровкой камеры горения из циркониевых огнеупоров, но это были только предложения изготовителей огнеупоров, и нигде не было ссылок на наличие таких реакторов в фирмах по производству техуглерода / 1.7.3. /.
О применении циркониевых огнеупоров на Омском заводе технического углерода было сообщено специалистами ОАО «УкрНИИО» им. А.С.Бережного на международной научно-технической конференции «Технология и применение огнеупоров и технической керамики в промышленности» ( 26-27 апреля 2005 года ) / 1.7.5./. Тезисы доклада даны в приложении 8.5. Внедрение циркониевых огнеупоров позволило увеличить температуру в камерах горения реакторов с 1830-1850⁰С. до 1960-1990⁰С и, как следствие, повысить выход техуглерода из сырья на 3-4% абсолютных, а также увеличить выход техуглерода на сумму сырья и топлива, уменьшить расход газа на 1т. вырабатываемого техуглерода и снизить объём газов, образующихся из 1т. сырья, что позволяет дополнительно увеличить нагрузку реактора по сырью. Увеличение количества сырья, подаваемого в реактор, ведёт к увеличению производительности всей установки по производству техуглерода, а, следовательно, и получению дополнительной прибыли.
Следует отметить, что одновременно с внедрением новых огнеупоров (корундовых, а затем циркониевых) внедрялись новые реакторы заводской конструкции, обеспечивающие увеличение производительности реакторов, а также новые воздухоподогреватели заводской разработки, обеспечившие повышение температуры воздуха, подаваемого в реактор с 500-550⁰С. до 750-820⁰С..
Кроме того, в связи с увеличением выпуска техуглерода возник дефицит сырья, в результате в сырьевые смеси начали вовлекаться низкосортные компоненты, вплоть до мазута. Поэтому определить повышение выхода непосредственно за счёт применения новых огнеупоров можно было только при проведении балансовых испытаний.
Для проведения сравнительных балансовых испытаний был запущен реактор, футерованный огнеупорными блоками из муллитокорундовой массы КС-90 и оборудованный воздухоподогревателем ВНИИТУ с температурой подогрева воздуха 550⁰С., при этом температура в камере горения была выше норм ВНИИТУ на 50-60⁰С. и составляла 1590-1600⁰С., то-есть это была та температура, которая поддерживалась в реакторах омского ЗТУ перед внедрением корундовых огнеупоров. Для сравнения использовался реактор, футерованный корундовыми блоками с содержанием окиси алюминия 99% и той же температурой подогрева воздуха.
Для определения изменения выхода техуглерода от применения циркониевых огнеупоров сравнивались режимы получения техуглерода N347 в реакторах с циркониевой и корундовой камерами горения при одинаковой температуре подогрева воздуха – 795⁰С. (реакторы были оборудованы системами подогрева воздуха заводской конструкции,
Основные результаты балансовых испытаний показаны в Табл. 1. (Приложение 8.3.) Из приведённых данных видно, что при прочих равных условиях (расход сырья в реактор; качество сырья; температура подогрева воздуха) в реакторе, футерованном корундовыми огнеупорами, увеличение выхода техуглерода по сравнению с реактором, футерованном блоками из КС–90, составило 6,48% абсолютных за счёт повышения температуры в камере горения реактора с 1590 до 1840⁰С. Увеличение выхода техуглерода из сырья на 6,48% соответствует уменьшению расхода сырья для производства 1т. техуглерода на 11%. Это очень существенная разница, так как сырьё для производства техуглерода не только дорогой, но и дефицитный продукт. Тот факт, что по заводским отчётам общий выход техуглерода повысился с 2001 по 2003 годы несколько ниже (на 4,1%) объясняется тем, что помимо протекторных марок техуглерода завод производил около 30% каркасных марок техуглерода (серий 500 и 600), технология получения которых основана на использовании сравнительно низкотемпературных процессов и где применение корундовых огнеупоров не могло дать таких значительных результатов. Кроме того, качество одного из основных компонентов сырьевой смеси – каталитического газойля в этот период непрерывно ухудшалось, что не могло способствовать повышению выхода техуглерода из сырья.
Определение эффективности применения циркониевых огнеупоров проводилось при получении техуглерода N347 с использованием чистого коксохимического сырья на реакторах с корундовой (99% AL2O3) и циркониевой футеровками при температуре подогрева воздуха 795⁰С. в обоих случаях и температурах в камерах горения реакторов 1850⁰С и 1980⁰С соответственно. Результаты испытаний приведены в табл. 1. Анализ результатов испытаний показывает, что выход техуглерода из сырья при использовании реактора с циркониевой футеровкой увеличился на 4,01% абсолютных и достиг величины 66,7%. Соответственно уменьшился на 6,0% и расход сырья на производство 1т. техуглерода, выход техуглерода на сумму сырья и топлива увеличился на 3,29%. Расход воздуха в реактор сократился на 7%, а расход воды уменьшился на 16%. Несколько снизился и расход природного газа на производство 1т. техуглерода. Объём образующихся газов не измерялся, но исходя из уменьшения расходов воздуха и воды он снизился не менее чем на 10%, что позволяет увеличить производительность реактора и технологического потока примерно на ту же величину.
Необходимо отметить, что по зарубежным данным выход техуглерода N347 при применении чистого коксохимического сырья составляет 61-62% абсолютных. Выход техуглерода на уровне 66-67% достигается только при получении низкодисперсного техуглерода N550 при использовании высокоиндексного коксохимического сырья (ИК=160)/1.7.8./.
В мае 2006 года на ОЗТУ были проведены сравнительные балансовые испытания при получении техуглерода серии 300 в реакторах с циркониевой (р-р №342) и корундовой (р-р№312) камерами горения. В связи с недостатком стандартных видов сырья для производства техуглерода в сырьевых смесях использовалось 50% мазута, что в зарубежных фирмах не допускается. Выход техуглерода из сырья составил 50,81% в реакторе с камерой из 99% корунда и 54,98% в реакторе с циркониевой камерой горения. Расход сырья для поучения 1т. техуглерода составил соответственно 1,9681т. и 1,8188т. Уменьшение расхода сырья для получения одной тонны техуглерода составило: Сравнивая результаты этих балансовых испытаний с результатами испытаний начала 2005 года (табл.1) нетрудно установить, что выход техуглерода в реакторе с циркониевой камерой горения даже при использовании сырья с содержанием 50% мазута (ИК=55 ) на 3,29% выше, чем при применении стандартной смеси и технологии ВНИИТУ (Табл.1., пункт1.). Уменьшение расхода сырья при этом составило 6,0%. Из этого можно сделать вывод, что в исключительных случаях в реакторах с циркониевой футеровкой можно использовать низкосортные виды сырья. Рентабельность естественно значительно понизится, но это лучше, чем снижение объёмов производства из-за недостатка стандартных видов сырья и возможного срыва поставок техуглерода.
1.3. Эффект от внедрения циркониевых огнеупоров на ОЗТУ.
Как показали результаты балансовых испытаний, применение в камерах горения реакторов циркониевых огнеупоров приводит к увеличению выхода техуглерода из сырья на 4% абсолютных, а также уменьшению расхода сырья на производство 1т. техуглерода от 6,0 до 7,6% в зависимости от вида применяемого сырья. При этом, чем ниже индекс корреляции сырья, тем больше его экономия при использовании циркониевых огнеупоров. Но это далеко не весь результат от применения циркониевых огнеупоров. Установлено уменьшение расхода воздуха и воды в реактор на 7,0 и 16% соответственно. Исходя из этих данных можно с уверенностью утверждать, что объём реакционных газов уменьшился не менее, чем на 10%, а это позволяет увеличить количество сырья, подаваемого в реактор тоже на 10%. Если использовать этот ресурс, на эту же величину взрастёт и прибыль, получаемая от реализации техуглерода на этом потоке. Естественно, сокращение потребления воздуха и воды тоже дают экономический результат, имеется и экономия электроэнергии. Понятно, что циркониевые огнеупоры имеют высокую стоимость, однако простые расчёты показывают, что срок окупаемости замены футеровки одной камеры горения составляет не более 1,5месяца при сроке межремонтного пробега реактора 1,0-1,5 года (расчёт прилагается). Расчёт производился только исходя из экономического эффекта от экономии сырья за счёт повышения выхода техуглерода. При этом при дважды подтверждённом при балансовых испытаниях увеличении выхода 4,17 и 4,01% в исходных данных расчёта предусмотрено увеличение выхода только на 3%. Даже при таком заниженном увеличении выхода техуглерода из сырья годовой экономический эффект от применения циркониевых огнеупоров на одном реакторе составляет 11 млн. руб. Срок окупаемости мероприятия при этом составляет 1,3 месяца. Проведены также расчёты при увеличении выхода на 2,0% и 1,0%. Сроки окупаемости при этом составляют соответственно 2 месяца и 3,3 месяца.
В расчёт намеренно не включалась дополнительная прибыль за счёт увеличения нагрузок реактора по сырью, экономия воздуха и воды, экономия газа и электроэнергии. Дополнительная прибыль от увеличения производительности реактора не включалась в расчёт потому, что она зависит и от субъективных факторов – могут увеличить нагрузку, а могут и не увеличивать. Главное же в том, что экономии сырья вполне достаточно, чтобы показать эффективность мероприятия.
Для полной компенсации затрат на мероприятие для одного потока потребуется1380000/9000/1,5=102т. сырья. Где 1380000руб – стоимость огнеупоров, 9000руб/т.– стоимость 1т сырья, 1,5 года – срок службы футеровки камеры горения. Понятно, что 102т. сырья при годовом потреблении 30000т. составляют от годового его потребления всего 0,3%.
Существенное значение имела и экономия самих огнеупоров, как прямая, так и косвенная. Прямая экономия была организована на участке по изготовлению огнеупоров под руководством БабичаГ.В. за счёт изготовления циркониевых огнеупорных блоков с включением в их состав отработанных циркониевых огнеупоров, так называемого огнеупорного лома. Кстати, это было совершенно новое дело в мировой промышленности техуглерода. Целесообразность и возможность повторного использования отработанных циркониевых огнеупоров была подтверждена исследованиями специалистов ОАО УкрНИИО имени А.С.Бережного, г. Харьков. /1.7.10/. Следует отметить, что огнеупорный лом одинаково успешно используется при изготовлении циркониевых огнеупоров как с использованием в качестве стабилизатора окиси иттрия, так и окиси кальция. Под косвенной экономией подразумевается реконструкция реакторов на высокопроизводительных установках с увеличением их производительности в 1,5 раза без увеличения размеров камер горения. В результате при одинаковых объёмах циркониевых огнеупоров в реакторах производительность реакторов возросла в 1,5 раза, следовательно, в расчёте на тонну произведённого техуглерода количество циркониевых огнеупоров уменьшается в 1,5 раза. Это стало возможным в результате полной реконструкции реакторных отделений установок в 2009—2012 годах. Следует отметить, что в результате этой реконструкции и проведённых ранее усовершенствований, установка не уступает вновь построенным в России установкам по производству техуглерода.
К экономическим результатам внедрения циркониевых огнеупоров нужно отнести и тот факт, что наиболее дисперсные марки техуглерода (например, N121) удавалось получать только в реакторах с циркониевой камерой горения. Если бы не было таких реакторов, то не было бы и возможности получать такие марки техуглерода, не было бы и соответствующих контрактов со всеми вытекающими отсюда последствиями.
Заканчивая этот раздел целесообразно отметить, что достигнутый эффект от применения циркониевых огнеупоров может быть значительно увеличен за счёт дальнейшего повышения температуры в камерах горения. Это вполне реально без изменения конструкции реакторов. Можно на одном из реакторов по специальной программе повышать температуру в камере горения по 5-10⁰С. Можно поднять температуру в камере горения перед остановкой реактора на капитальный ремонт. В реакторе могут выявляться слабые места, но это было всегда и недостатки всегда устраняли.
1. 4. Необходимые условия для внедрения новых огнеупоров
Начиная с 2001 года основной эффект в промышленности техуглерода на передовых заводах достигался за счёт использования новых огнеупоров с повышенной температурой применения, что позволило сначала повысить температуру в камерах горения реакторов с 1550⁰С. до 1840⁰С., а затем (правда, только на Омском ЗТУ) и до 1960–1990⁰С. Внедрение новых огнеупоров на заводах техуглерода не такой простой процесс. Это не означает, что достаточно заказать огнеупоры для футеровки реакторов. Во-первых, такие огнеупоры на отечественных заводах не производились. Во-вторых, стандартные огнеупоры не подходили для камер горения реакторов, ну и последнее – нужно было организовать переоборудование большого количества реакторов в сжатые сроки. Поэтому для быстрого и квалифицированного внедрения новых огнеупоров необходимы следующие условия:
1.4.1Наличие специалистов как по изготовлению, так по применению огнеупоров.
1.4.2. Наличие собственной базы для изготовления огнеупоров.
Ранее уже говорилось об участках по изготовлению огнеупоров, понятно, что для успешной их эксплуатации требуются квалифицированные кадры. Приоритет Омского ЗТУ во внедрении новых огнеупоров связан и с тем, что ОЗТУ имел на этом направлении наиболее квалифицированных специалистов. Так, Бабич Геннадий Васильевич начиная с 90-х годов, как уже отмечалось ранее, проводил всю работу по изготовлению огнеупоров от проектирования прессформ и до окончания процесса изготовления огнеупоров. Кроме того он принимал непосредственное участие в разработке конструкций реакторов, а также проводил основную работу с поставщиками набивной массы. Имеет завод также в технических отделах и цехах квалифицированных специалистов, хорошо разбирающихся в качестве футеровки и процессе эксплуатации реакторов.
С использованием реакторов с циркониевой футеровкой было получено много новых марок техуглерода. Только в 2011 году было разработано 10 новых марок техуглерода, половина из них это высокодисперсные и высокоструктурные марки техуглерода, которые производились в болшегрузных реакторах с камерами горения, футерованными циркониевыми огнеупорами. Следует отметить, что ещё при внедрении техуглерода N121, было выяснено, что эта марка стабильно получается только в реакторах с циркониевой футеровкой камеры горения. Это обстоятельство способствовало изменению отношения многих специалистов к внедрению циркониевых огнеупоров.
В этом же году в связи с увеличением потребности в техуглероде завод впервые выпустил более 230 тыс. т. техуглерода, при этом на высокопроизводительных установках проектная мощность была превышена на 16,8%, в цехе №3 на 31,8% при использовании 3-х потоков, тогда, как проектная мощность цеха рассчитывалась на четыре потока. В производстве полуактивных марок техуглерода проектная мощность была превышена на 59,5%. Такого результата удалось достичь за счёт внедрения комплекса мероприятий в течение ряда лет. Мероприятия по повышению производительности технологических потоков осуществлялись постоянно. Однако наибольшее значение для увеличения выпуска техуглерода имело внедрение новых огнеупоров – корундовых, а затем и циркониевых. По сравнению с началом 2002 года выход протекторных марок техуглерода увеличился в 2011 году на 12% что соответствует уменьшению расхода сырья на 19,35%. Таким образом, при выходе техуглерода из сырья, который был достигнут ОЗТУ до внедрения новых огнеупоров, для выпуска 134476,7т. протекторного техуглерода, произведённого в 2011 году, потребовалось бы дополнительно 52 тыс. т. сырья, которое вряд ли можно было приобрести и, тем более, переработать. Что касается результатов внедрения новых огнеупоров в производстве полуактивных (каркасных) марок техуглерода, то здесь необходимо отметить, что при производстве этих марок техуглерода непрерывно снижалось качество сырья. И, если в 90-е годы в цех подавалось сырьё с индексом корреляции 135-140 ед., то затем он был понижен до 115-117 ед. за счёт использования низкоиндексного газойля Омского нефтезавода. При таком уменьшении индекса корреляции (ИК.) выход техуглерода из сырья по данным/1.7.8./ уменьшается на 5-6 %. Это уменьшение выхода техуглерода и было компенсировано за счёт уменьшения соотношения воздух:газ. Как известно, при уменьшении соотношения воздух:газ повышается температура факелов горелок, что приводит к повышению выхода техуглерода. При футеровке реактора муллитокорундовыми огнеупорами с содержанием окиси алюминия 87-90% это соотношение нельзя было понизить менее 14:1, так как повышалась температура в зоне реакции более 1600⁰С., что могло неблагоприятно отразиться на футеровке реактора. При использовании корундовой футеровки это соотношение удалось понизить почти до стехиометрического, при этом температура в зоне реакции после кратковременного повышения понижалась до норм регламента.
Понятно, что применение циркониевых огнеупоров даёт существенное повышение выхода техуглерода из сырья (4,01 и 4,17% по результатам балансовых испытаний), но эксплуатация такого реактора сложнее и требует дополнительного обучения обслуживающего персонала. В связи с применением в реакторе разнородных огнеупорных материалов более высокие требования предъявляются и к самой футеровке реактора. Это обусловлено тем, что окись циркония в смеси с окисью алюминия образуют смеси, имеющие при определённом соотношении температуру плавления даже ниже, чем чистая окись алюминия (письмо ОАО « УКРНИО» им А,.С. Бережного, направленное 03.10.03. в адрес технической службы Омского ЗТУ). К письму была приложена диаграмма состояния системы ZrO₂–Al₂O₃, из которой следует, что минимальная температура плавления (эфтектика) образуется при содержании в системе 61,7 процентов молярных Al₂O₃ и составляет 1710⁰С., притом, что температура плавления окиси алюминия составляет 2050⁰С, а окиси циркония – 2715⁰С.(Приложение 8.2.). Это обстоятельство необходимо учитывать при разработке конструкции футеровки реактора с циркониевой камерой горения. Так, в случае разрушения циркониевого блока футеровки реактора (как правило, в его торцевой части) в камеру горения попадают части разрушенного корундового блока, что сразу же приводит к оплавлению нижней части камеры горения. Эти недостатки конструкции футеровки реактора были устранены и подобные случаи не повторялись. Другим опасным местом в футеровке реактора является примыкание корундового блока к циркониевому в переходной втулке реактора. Как показала практика эксплуатации реакторов, в данном случае низкоплавкая смесь создаётся только при нарушении технологического режима, когда начинает плавиться корундовый блок при превышении температуры более 1900⁰С. в переходной втулке реактора в зоне за сырьевыми форсунками. Это может происходить при неправильных действиях персонала при пусках и остановках реакторов, а также при замене сырьевых форсунок. Вероятность оплавления огнеупоров значительно снижается, если в зоне контакта разнородных блоков вместо корундового блока установить блок из хромистого корунда с содержанием окиси хрома ≥ 12% масс. Как уже отмечалось ранее, по заказу ОЗТУ такой материал изготавливает Верхнепышменский огнеупорный завод, применение его в этой зоне значительно снижает количество оплавов. Огнеупорность такого материала по данным УКРНИИО составляет 2125⁰С., тогда как огнеупорность корунда Богдановичского огнеупорного завода составляет 2030⁰С. Это существенная разница, и это особенно важно в связи с необходимостью повышения температуры в зонах горения реакторов. Возможно использование в этой зоне и блоков, изготовленных из шпинели (MgO∙Al₂O₃), содержащей 28,33% мас. MgO и 71,67% мас. Al₂O₃, и имеющей температуру плавления 2135⁰С. /1.7.6./. Такой состав производится и в России (Востокогнеупор, Екатеринбург, Масса шпинельная набивная—МШПН).
1. 5. Эксплуатация циркониевых реакторов.
Как уже отмечалось, обслуживание реакторов с циркониевой камерой горения сложнее и требует более высокой квалификации обслуживающего персонала. Поэтому нужно рассмотреть необходимые условия правильной эксплуатации таких реакторов. На Рис/1/ показан эскиз реактора с циркониевой камерой горения, включающий: 1—корпус реактора, 2—камера смешения топлива с воздухом, 3– камера горения, 4—смесительное сопло, 5—плоскость ввода сырья в смесительное сопло, 6—начальная часть зоны реакции. На нём указаны и основные огнеупорные материалы футеровки камеры горения/3/, смесительного сопла/4/ и начальной зоны камеры реакции реактора /6/. Как показано на эскизе огневой слой камеры горения /3/ и основная часть смесительного сопла /4/ футерованы циркониевыми блоками. Последний блок смесительного сопла и блоки начальной части зоны реакции изготовлены из хромистого корунда содержащего 12% Cr₂O₃. Огнеупорность этого материала, как уже было указано, достигает 2125⁰С. Этот материал можно заменить шпинелью с содержанием 28,5%мас. MgO и 71,5%мас. Al₂O₃. Целесообразно также испытать в этой зоне хромистый корунд с содержанием окиси хрома 20—25%. Остальная часть зоны реакции футерована корундовыми огнеупорами с содержанием окиси алюминия ≥99%.
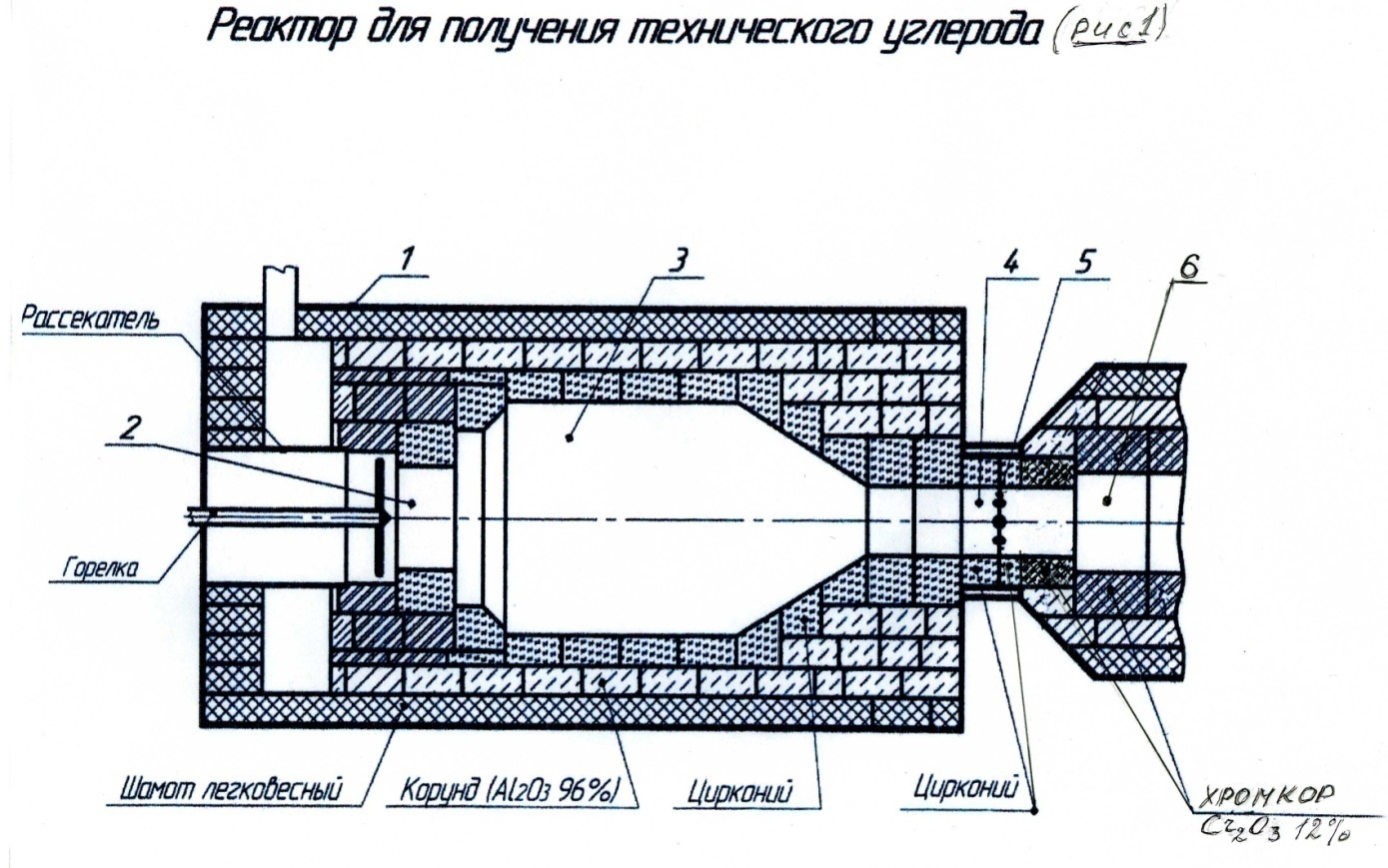
Применение циркониевых огнеупоров только в зоне горения и смесительном сопле обусловлено двумя факторами. Во-первых, температура в зоне реакции не превышает 1870–1880⁰С. даже в аварийных ситуациях и применение дорогостоящих циркониевых огнеупоров не вызвано необходимостью. Во-вторых, и это главное, циркониевые огнеупоры разрушаются в восстановительной газовой среде, что и имеет место в зонах реакции реакторов в связи с наличием в газах зоны реакции окиси углерода, водорода, сероводорода. Особенно быстро разрушаются циркониевые блоки при попадании на них капель или паров сырья.
Как уже указывалось, температура в камерах горения реакторов, футерованных циркониевыми огнеупорами, достигает фактически 1990⁰С., поэтому при прекращении подачи сырья в зоне реакции реактора может превысить допустимую температуру для корундовых огнеупоров (1880⁰С.), что приведёт к их оплавлению. С учётом этого фактора, при переводе реактора на режим полного горения необходимо предварительно понизить температуру в камере горения реактора до 1600⁰с., уменьшив не только расход газа, но и расход воздуха. Следует отметить, что такую же операцию нужно проводить и при переводе на режим полного горения реакторов с камерами горения из корундовых огнеупоров. Если этого не делать, то при температуре в зоне горения реактора 1840-1870⁰С. во время перекрывания сырья температура в зоне реакции неизбежно повысится в течении какого–то времени выше 1900⁰С., так как сырьё не перекрывается мгновенно, более того это может быть значительный период времени (до полного перекрытия запорной арматуры на сырьевые форсунки). Поэтому перед остановкой реактора необходимо понизить температуру не только в камере горения, но и в зоне реакции реактора уменьшением расхода воздуха. Понижать температуру в камере горения и в зоне реакции реактора необходимо и перед заменой сырьевой форсунки. Если же температуру в зоне реакции перед заменой сырьевой форсунки оставить без изменений, то при перекрытии сырья на одну из форсунок температура в зоне реакции резко увеличиться и может превысить допустимую температуру для огнеупора. Это объясняется тем, что температура в зоне реакции зависит от соотношения воздух : сырьё и, если сократить количество сырья, подаваемого в реактор, без уменьшения количества подаваемого воздуха (например, при замене одной форсунки), то температура в зоне реакции резко повысится и будет превышать допустимую температуру для огнеупора. Правильный перевод реактора на режим полного горения, соблюдение инструкции по замене сырьевых форсунок исключают возможность оплавления футеровки реактора, однако каждое значительное изменение температурного режима сокращает срок службы огнеупора. Поэтому очень важно сократить количество переводов реакторов на режим полного горения, особенно в связи с заменой сырьевых форсунок. Для этого нужно исключить причины забивания сырьевых форсунок