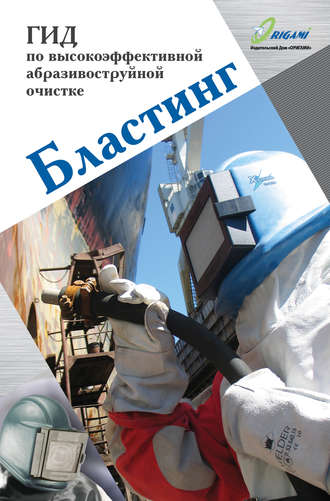
Полная версия
Бластинг. Гид по высокоэффективной абразивоструйной очистке

Д. Ю. Козлов
Бластинг. Гид по высокоэффективной абразивоструйной очистке
«Бластинг» – это первое издание на русском языке по подготовке поверхностей перед окрашиванием с помощью абразивоструйной очистки.
Гид написан на основе многочисленных испытаний производителей оборудования, доказывающих влияние различных параметров на производительность очистки. Издание содержит описание элементов абразивоструйной системы и является руководством для достижения высокопродуктивной абразивоструйной обработки; ценность издания, в этой связи, для практического использования безгранична.
«Бластинг» – это ваш путеводитель в мир эффективной абразивоструйной очистки, содержащий сведения, полезные как для опытных операторов, так и для новичков.
Введение
Идеальная защита от коррозии на 80 % обеспечивается правильной подготовкой поверхности, и только на 20 % качеством используемых лакокрасочных материалов и способом их нанесения.
ISO18 октября 1870 в США был выдан патент на метод пескоструйной очистки, позже в этом же году аналогичный патент был получен в Великобритании. Автором метода является американский изобретатель английского происхождения Бенджамин Чу Тилгман (Benjamin Chew Tilghman). Так на смену всевозможным методам очистки поверхностей – пришла эра Бластинга.
Данное руководство по абразивоструйной обработке было написано после многочисленных испытаний, доказывающих влияние различных параметров на производительность. Данная книга была задумана как руководство для достижения высокопродуктивной абразивоструйной обработки, при этом как доступное для понимания краткое изложение важных элементов абразивоструйной системы.
«Бластинг» – это первая книга о методике очистки абразивоструйным методом изданная в России.
Бластинг включает в себя подробное описание методов эффективной абразивоструйной обработки для введения новичков в суть процесса, а также информацию о современных технологиях для более опытных пользователей. В издании содержится множество указаний на то, как получить оптимальную производительность при проведении работ по подготовке поверхностей. Кроме того, руководство включает в себя наглядные пособия, которые могут быть полезны при выборе особых параметров, подходящих для конкретных случаев применения. Данное издание также содержит напоминания о технике безопасности и большое количество справочной информации для операторов и инспекторов оборудования по абразивоструйной очистке. Помимо этого в книгу включены многочисленные дополнительные источники информации по абразивоструйной обработке.
Однако существует ряд тем, которые данная книга не освещает. Так, «Бластинг» не может служить руководством в комплексной системе обучения абразивоструйной очистке. Процесс очистки состоит из множества сочетаний элементов и различных применений, которые невозможно в полной мере отразить в первом издании. В конечном итоге, сам пользователь с помощью проведения различных испытаний и тестов, должен принять окончательное решение в выборе сочетания элементов, наиболее подходящих для выполнения определенного вида работ. Потребитель должен пройти соответствующее обучение, иметь доступ ко всей имеющейся в наличии полезной информации и приобрести практический опыт, перед тем как он сможет принимать оперативные решения в рамках какого-либо проекта.
«Бластинг» не претендует на полное освещение проблемы техники безопасности при проведении абразивоструйных работ. Техника безопасности формируется после основательного изучения всех материалов, касающихся конкретного вида струйной обработки, и включает в себя описание самих работ, местное и государственное правовое регулирование, условия места проведения работ и, конечно, руководства по эксплуатации на все виды оборудования, используемого для проведения работ. У каждого производителя есть свои особенности в конструкции оборудования. Перед использованием оборудования необходимо тщательно изучить руководство по эксплуатации, будь то абразивоструйный аппарат или сопутствующая ему техника, например, компрессоры и технологические устройства. Потребитель должен использовать все виды тренингов, видеофильмы и другие материалы, которые помогут ему овладеть техникой безопасности при абразивоструйной обработке.
Мы не ставили цель описать все существующие правила абразивоструйной обработки. Существуют нормы, касающиеся загрязнения воздуха, воды, почвы; техника безопасности оператора и окружающих; конструктивные ограничения оборудования; ограничения по токсичным выбросам; информационные знаки для работников и другие вопросы, которые могут быть очень важны в определенных ситуациях. Данные нормы различны в каждом регионе. Пользователи оборудования должны самостоятельно ознакомиться со всеми соответствующими правилами.
Информация о технике безопасности присутствует на протяжении всего издания, в четвертом разделе подробно описана ответственность оператора и работодателя при обучении безопасному и продуктивному использованию систем струйной очистки. Приложение включает в себя справочный раздел с дополнительными данными.
1. Технология и случаи применения
Технология
При абразивоструйной обработке абразивные частицы ускоряются из абразивоструйного аппарата при помощи энергии сжатого воздуха. Для того чтобы посредством абразивных частиц и сжатого воздуха обеспечить эффективную очистку, требуется профессиональное мастерство, высококлассное оборудование и контроль качества. Каждый элемент влияет на результат работы всей системы.
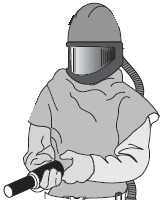
Даже несоответствие одного элемента ограничивает работу системы в целом.
Данная книга подчеркивает необходимость поддержания давления и объема подаваемого воздуха на всей установке.
Система абразивоструйной очистки состоит из трех основных компонентов: компрессор, струйный аппарат и абразив (смотрите Приложение 1: «Составляющие рабочего места абразивоструйщика»).
Компрессор должен создавать достаточное давление и объем воздуха для того, чтобы переместить абразив из абразивоструйного аппарата на обрабатываемую поверхность. Абразивный порошок засыпается в абразивоструйный аппарат и посредством дозирующего клапана подается в воздушный поток, на пути которого не должно быть препятствий. Желаемый результат обработки поверхности достигается посредством регулирования силы сжатого воздуха, воздействующей на абразив. Очистка напрямую зависит от того, насколько эффективно воздух движется из компрессора на очищаемую поверхность. Помеха хотя бы в одном элементе вызывает снижение продуктивности целой системы.
Подрядчики часто не рассматривают абразивоструйный аппарат как возможный источник ограничения подачи воздуха и потока абразива. Воздух под высоким давлением не может проходить через фитинги малого диаметра в таком же объеме, как при фитингах большого диаметра.
Роль абразивоструйного аппарата состоит в том, чтобы равномерно дозировать абразив в воздушный поток. Иногда подрядчики монтируют фитинги, ограничивающие поток воздуха и дозирующие клапаны, которые сокращают воздушный поток наполовину, а в итоге не могут понять, почему производительность снизилась. Данной проблемы можно избежать, выбрав струйный аппарат с трубками, фитингами и клапанами большого диаметра и подсоединив его к шлангу для подачи сжатого воздуха и соплу также большего диаметра.
Другой очень важный элемент в системе абразивоструйной очистки – это абразив. В конечном итоге, очистка поверхности зависит именно от используемого абразива. Выбирайте абразив соответствующей формы, размера, твердости, плотности и состава. Подрядчики, выбирающие неподходящий абразив, рискуют получить перерасход средств, нарушение окрасочного слоя и дорогостоящую повторную обработку.
При обработке поверхности следует тщательно подбирать абразивный материал и размер его частиц для того, чтобы обеспечить наилучший результат по скорости очистки и экономической эффективности работ.
Самый лучший воздушный компрессор и абразивоструйный аппарат не смогут компенсировать неправильный выбор абразива (смотрите раздел «Абразивные материалы», где описаны рекомендации по выбору абразива).
Известная поговорка гласит: «Где тонко, там и рвется», – и ее можно применить к выбору абразивоструйного оборудования. Качество и производительность ключевых элементов влияет на эффективность системы в целом.
Большинство элементов системы абразивоструйной очистки имеют цилиндрическую форму. Даже небольшое изменение диаметра данных элементов влечёт за собой уменьшение объема воздуха, проходящего сквозь них, в геометрической прогрессии.
Даже при выборе компрессора и абразивоструйного аппарата необходимой мощности и соответствующего абразива, требуется мастерство и профессионализм оператора для того, чтобы система работала максимально продуктивно.
Применение
Абразивоструйная очистка делится на три составляющих: подготовка поверхности, очистка и отделка поверхности, а так же дробеструйное упрочнение.
Подготовка поверхности
При очистке ненужные материалы удаляются, и поверхность становится подготовленной для нанесения покрытий.
При помощи абразивоструйной очистки с металлических конструкций удаляют старую краску, ржавчину и другие загрязнения. Кроме того, при струйной очистке удаляется вторичная окалина, которая образуется на новой стали.
Угловатые частицы абразива придают шероховатость поверхности и создают профиль, или насечку. Большинство производителей красок указывают, каким должен быть профиль, чтобы обеспечить эффективное нанесение их продукции. Более подробно профиль поверхности будет обсуждаться далее.
Подрядчики очищают кирпичную кладку перед нанесением шпатлевки или краски. Абразивоструйная очистка наружной штукатурки и кирпича позволяет удалять старую краску, плесень, копоть, красящие вещества и даже граффити, оставляя при этом идеальную поверхность для нанесения покрытия.
Подрядчики очищают преднапряженные железобетонные панели, монолитные бетонные стены, колонны и другие конструкции из бетона для того, чтобы удалить остаточный цемент, следы строительной опалубки, выцветшие участки и обнажить бетон.
Кроме обработки стали и каменной кладки, при помощи абразивоструйной очистки можно снять верхние слои краски с деревянных домов и лодок. Со стекловолокна с помощью данной очистки обычно удаляют верхний слой гелевого покрытия для того, чтобы сделать видимыми пузырьки воздуха. При абразивоструйной очистке алюминия, титана, магния и других металлов удаляют коррозию и, в зависимости от выбранного абразива и давления, наносят профиль.
Новые, более мягкие виды абразива (включая пластик и пшеничный крахмал), а также специальное абразивоструйное оборудование с низким давлением используются для сухого способа удаления покрытий с современных композиционных материалов. Это позволяет компаниям очищать самолеты, вертолеты, автомобили, грузовики и лодки без использования абразивоструйной обработки, которая может нарушить структуру поверхности. Кроме того, переход на сухой способ очистки верхних слоев исключает возможность воздействия на рабочих токсических химических веществ, используемых при очистке, и исключает расходы, связанные с утилизацией опасных отходов.
Перечень возможностей абразивоструйной очистки кажется бесконечным. Каждый день сотни компаний прибегают к помощи абразивоструйной очистки для того, чтобы решить проблемы долговременной очистки и подготовки поверхности. Поскольку в промышленности регулярно изобретаются новые материалы и возникает потребность в обработке новых поверхностей, производителям абразивоструйной техники и материалов приходится непрерывно совершенствовать свои технологии и оборудование.
Очистка поверхности и отделочная обработка
Очистка поверхности и отделочная обработка значительно отличаются от процесса подготовки поверхности. Отличие заключается в том, что ожидаемый результат состоит в совершенствовании внешнего вида продукции и его полезности, а не просто в его подготовке к нанесению покрытий или к сборке. Очистка поверхности включает в себя удаление загрязняющих веществ и окалины. Отделочная обработка поверхности включает удаление заусенцев с отлитых изделий, а также совершенствование внешнего вида продукции.
Абразивоструйная очистка с использованием стеклянных или керамических шариков в качестве абразивного материала позволяет создавать матовую поверхность и рельеф на мягких металлах.
На многих литейных предприятиях абразивоструйная очистка используется для удаления заусенцев с отлитых изделий с целью улучшения их функциональности и эстетического вида.
В большинстве случаев при абразивоструйной очистке выявляются микротрещины и дефекты в металлах. Это особенно важно для предприятий, занимающихся ремонтом и модернизацией шасси самолетов.
Мягкие материалы, такие, как резина и пластик, обычно изготавливаются с помощью специальных форм, после которых на них остаются неровности. Абразивоструйная очистка легко удаляет такие неровности, в результате чего получается гладкая однородная поверхность.
Абразивоструйная очистка широко применяется в отраслях промышленности, использующих повышенную температуру для закалки металлов. Высокие температуры могут обесцвечивать изделия. Абразивоструйная обработка позволяет удалять выцветшие участки и окалину с изделий, подвергшихся воздействию высоких температур.
Кроме того, абразивоструйная очистка может улучшить внешний вид продукции благодаря удалению различных пятен, отложений, коррозии и следов инструмента. При этом некоторые абразивные материалы позволяют делать внешний вид поверхности более однородным.
При высокой температуре образуется нагар и отложения отработанного масла на многих автомобильных деталях. Электродвигатели часто засоряются перегретыми изоляционными материалами и расплавленными слоями статора. В большинстве случаев сохранение исходных размеров данных деталей является критичным. Абразивоструйная обработка с помощью пластиковых абразивных материалов, стеклянных шариков или натурального абразива удаляет загрязняющие вещества и обеспечивает желаемый результат.
Дробеструйное упрочнение
При изготовлении металлического изделия, для придания ему определённой формы, производители должны совершать множество действий, а именно: отливать, резать, сгибать, штамповать, прокатывать или сваривать металлы. Иногда все эти процессы вызывают на металлах остаточное напряжение, которое, если от него вовремя не избавиться, может стать причиной поломки изделий.
Дробеструйное упрочнение увеличивает прочность и долговечность деталей посредством их обработки абразивными материалами, имеющими сферическую форму и разогнанными до высокой скорости. К ним относятся: стальная дробь, керамическая дробь, стеклянные шарики и др.
Дробеструйное упрочнение создает эффект, похожий на удар по поверхности молотком. Отличием данного процесса является только то, что при упрочнении образуются более маленькие углубления и удары являются одинаковыми по интенсивности. Данная «бомбардировка» частицами абразива создает равномерно спрессованную поверхность, распределяя напряжение по всей площади поверхности и, тем самым, уменьшая вероятность ломкости металлов.
Дробеструйное упрочнение – это точная наука, требующая строгого соблюдения технических условий по твёрдости абразивного материала, продолжительности очистки, углу наклона сопла и необходимому давлению. Чрезмерное или недостаточное упрочнение детали может быть причиной преждевременного разрушения.
Упрочнение широко используется в автомобильной и авиационной промышленностях. Производители шестерней используют упрочнение для удаления заусенцев и острых граней и для того, чтобы зубья шестерней были более крепкими. Производители пружин используют упрочнение для снятия напряжения.
При дробеструйном упрочнении литых и штампованных металлических изделий очищается поверхность, выявляются дефекты и улучшается внешний вид. Упрочнение деталей с резьбой позволяет удалить заусенцы, острые грани и одновременно увеличить удерживающую способность резьбы. Упрочнение часто используется с безвоздушным оборудованием для удаления вторичной окалины с новой стали.
Технические условия по подготовке поверхности
Производители лакокрасочных материалов давно поняли важность подготовки поверхности для успешного использования их покрытий. Несоответствующая очистка стальной поверхности может стать причиной преждевременного разрушения покрытия. Именно поэтому производители лакокрасочной продукции детально излагают требования по подготовке поверхности перед нанесением их продукции. Кроме того, при отказе выполнять данные требования гарантия на качество покрытия может быть аннулирована.
Требования к подготовке стальной поверхности включают в себя два важных параметра: профиль поверхности и степень очистки.
Профиль поверхности
Производители лакокрасочных материалов и профессиональные организации испытывают лакокрасочные покрытия, применяя их при различных профилях поверхности и условиях окружающей среды. В результате исследований обнаружено, что для гарантированной адгезии и абсолютной защиты субстрата перед нанесением покрытия требуется обеспечить соответствующий профиль. Насечка обеспечивает прочное однородное сцепление между поверхностью и покрытием.
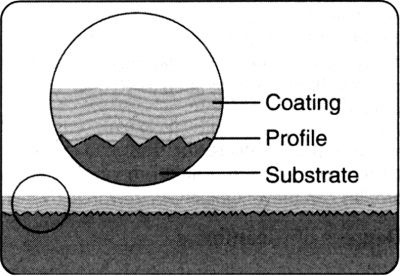
Рис. 1. Профиль поверхности
Частицы абразивного материала образуют на стальной поверхности крошечные пики и углубления. Глубина профиля зависит от размера, типа и твердости абразива, давления воздуха, расстояния и угла наклона сопла к очищаемой поверхности.
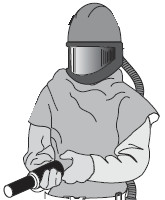
Когда профиль превышает допустимый уровень, то пики проявляются над поверхностью покрытия, приводя к его разрушению.
При увеличении слоя лакокрасочного покрытия для выравнивания глубокого профиля увеличивается себестоимость выполняемой работы. Более детальное описание профилей, образованных при использовании различных абразивов, изложено в разделе «Абразивные материалы».
Профиль выражается в милах, микронах и миллиметрах.
1 мил = 1/1 000 дюйма.
25 микрон = 1 мил.
25,4 миллиметра = 1 дюйм.
39 мил = 1 миллиметр.
В Соединенных Штатах Америки обозначение в милах используют как единицу измерения толщины покрытия и профиля поверхности. Обычно в спецификации указана средняя высота профиля. Например, средний профиль в 2 мила (50 микрон) может включать в себя профили от 1 мила (25 микрон) до 3 мил (75 микрон). Данная классификация профилей вполне приемлема, т. к. нет практического метода производства абразивных частиц одинакового размера.
Отклонения в давлении воздуха, расстоянии до поверхности или в угле наклона сопла также влияют на глубину профиля. Уменьшенное давление воздуха или увеличенное расстояние сопла от обрабатываемой поверхности является причиной небольшого размера профиля. При большом угле отклонения сопла будет лишь поверхностная обработка субстрата без отчётливых пиков и углублений. Для абразивоструйной обработки стали угол наклона сопла к поверхности должен быть 80–90 градусов.
Для определения глубины профиля поверхности используйте специальные измерительные приборы для того, чтобы документально подтвердить соответствие данного профиля заданному. Тщательный контроль глубины профиля поверхности поможет избежать дорогостоящей вторичной обработки.
Степени очистки
Требования к качеству подготовки металлической поверхности перед операциями окрашивания, нанесения металлизационных покрытий устанавливает ГОСТ 9.402-80 «Покрытия лакокрасочные. Подготовка металлических поверхностей перед окрашиванием». В ГОСТе выделяются четыре степени очистки поверхности черных металлов от окалины и продуктов коррозии:
1 – при осмотре с 6-кратным увеличением окалина и ржавчина не обнаруживаются;
2 – при осмотре невооруженным глазом не обнаруживаются окалина, ржавчина, пригар, остатки формовочной смеси и другие неметаллические слои;
3 – не более чем на 5 % поверхности имеются пятна и полосы плотно сцепленной окалины и литейная корка, видимые невооруженным глазом. На любом из участков поверхности изделия окалиной занято не более 10 % площади пластины 25х25 мм;
4 – с поверхности удалены ржавчина и отслаивающаяся окалина.
Этим степеням подготовки поверхности в основном соответствуют степени Sa3, Sa 2 1/2, Sa 2, Sa1, устанавливаемые международным стандартом ISO 8501-1: 1988: «Подготовка стальной основы перед нанесением красок и подобных покрытий. Визуальная оценка чистоты поверхности. Степени коррозии и степени подготовки непокрытой стальной основы после полного удаления прежних покрытий».
Организация SSPC («Исследователи защитных покрытий») (США) установила пять степеней очистки при абразивоструйной обработке, классифицирующихся от полного удаления всех загрязняющих веществ до удаления только остаточных материалов с обрабатываемой поверхности. К данным пяти степеням очистки относятся: очистка до «белого металла», очистка до «почти белого металла», коммерческая очистка, промышленная очистка, поверхностная очистка. Данные стандарты могут быть пересмотрены и исправлены. Но, несмотря на все это, они используются, как основные принципы. Для более подробного описания каждого из них можно обратиться к «Визуальным стандартам очистки стали с помощью абразивоструйной обработки».
Очистка до «белого металла» – это очистка, видимая без увеличения. Очищенная поверхность до «белого металла» представляет собой поверхность, с которой удалены все видимые загрязнения, а именно: ржавчина, вторичная окалина, краска и посторонние включения. Обычно данная степень очистки требуется при нанесении сложных покрытий (цинкосодержащие краски) на поверхности, подвергающиеся агрессивному воздействию коррозионной среды – химические установки, морские буровые установки и мосты над водой с повышенным содержанием соли.
Очистка до «почти белого металла» – это очистка, видимая без увеличения. Это поверхность, свободная от всех типов видимых загрязнений (ржавчины, вторичной окалины, краски и посторонних веществ). Данный вид очистки похож на очистку до «белого металла». Единственное отличие заключается в том, что на очищаемой поверхности допустимо не более 5 % загрязнений. Данный вид очистки применяется при использовании высокоэффективных покрытий на стальной поверхности, подвергающейся воздействию жесткой среды и интенсивному использованию.
Коммерческая очистка – это очистка, видимая без увеличения. Поверхность очищается от видимых нефтепродуктов, смазочных материалов, пыли, окалины, грязи, вторичной окалины, продуктов коррозии и посторонних веществ. При данной очистке на поверхности может остаться не более 33 % загрязненных участков, полос, обесцвечивания поверхности от пятен ржавчины, вторичной окалины и старых покрытий. Для большинства применений используются стандартные покрытия.
Промышленная очистка – это очистка, видимая без увеличения. Поверхность освобождается от всех видимых нефтепродуктов, смазочных материалов, пыли и грязи. Однако допускается до 10 % плотно прилипшей вторичной окалины, ржавчины и остатков покрытия, если они равномерно распределены. Оставшаяся часть поверхности может содержать следы загрязнений, полосы и обесцвечивания, вызванные пятнами ржавчины, вторичной окалины или старого покрытия.
Поверхностная очистка – видимая без увеличения. Поверхность, обработанная таким образом, может содержать плотно прилипшие остатки вторичной окалины, ржавчины или старого покрытия. Нет необходимости обнажать пятна металла, если субстрат состоит из неповрежденного покрытия. Данный метод приемлем для поверхностей, не подверженных воздействию суровых условий окружающей среды или там, где не ожидается длительный срок службы покрытия.
Там, где требуется коммерческая или поверхностная очистка, следует убедиться в том, что новое покрытие совместимо со старым. Несовместимые покрытия могут вызвать окалину или отслаивание.
Организация SSPC предлагает серию фотографий, которые иллюстрируют четыре существующих состояния стальной поверхности и степени очистки каждой. К существующим состояниям относятся: вторичная окалина, вторичная окалина и ржавчина, полная коррозия и коррозия с образованием углублений.