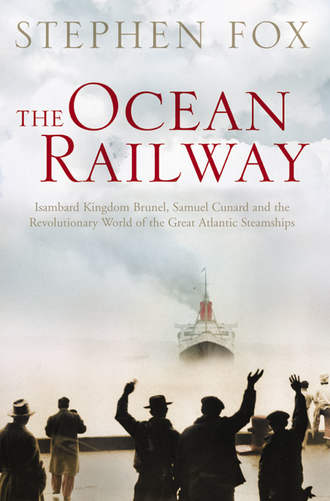
Полная версия
The Ocean Railway: Isambard Kingdom Brunel, Samuel Cunard and the Revolutionary World of the Great Atlantic Steamships
The extent of his fame was revealed in the spring of 1843 when, performing a coin trick for the children of a friend, he accidentally swallowed a half sovereign. It settled in his windpipe, causing pain in the chest and fits of coughing, and could not be dislodged. brunel designed an apparatus for holding himself upside down, hoping that gravity would help expel the coin. He was inverted and tapped on the back, causing such convulsive coughing that the experiment was abandoned. Sir Benjamin Brodie, a prominent physiologist and surgeon, was summoned. He performed a tracheotomy and poked around with his forceps, but without success. Newspapers issued regular bulletins. Even the august Times, which liked to define serious news coverage, kept its readers well informed. ‘Mr. brunel passed a quiet night,’ The Times reported. Four days later: ‘He was able on Thursday to take a small quantity of fish.’ And three days more: ‘Mr. brunel is going on favourably.’ At last, after almost six weeks, he was again turned upside down, with the incision in his windpipe kept open. Hit gently between the shoulder blades, brunel coughed twice, and the coin dropped from his mouth. The Times published a detailed final report (‘And thus, under Providence, a most valuable life has been preserved’).
Over his career, brunel contrived great triumphs and equally great failures. Everything about him was exaggerated; he vividly displayed both the strengths and deficiencies of genius. He reasonably believed that he knew more, across a wider range of engineering fields, than almost anybody he encountered. Among railway men, only Robert Stephenson, the accomplished son of George Stephenson, was greeted as a peer. ‘Stephenson is decidedly the only man in the profession that I feel disposed to meet as my equal, or superior, perhaps,’ brunel noted. ‘He has a truly mechanical head.’ Anyone else was expected to defer to brunel’s authority. His unorthodox mind and dead-sure tenacity pushed him through any obstacles into bold, original achievements – and also made him a quite difficult associate and boss. It was generally best not to resist or disagree with him. ‘Admit him to be absolute,’ one colleague noticed, ‘and he was not only reasonable, but kind. Hint to him that you had rights, and he was inexorable.’
As an engineer, he most valued ‘usefulness’, he insisted, ‘that characteristic of which we are most proud, and for which we have the vanity to think we are peculiarly distinguished.’ But ‘usefulness’ to brunel meant deploying the newest, strongest materials and methods, as called for by the most extravagant engineering standards available. The Great Western was the fastest, most solidly built railway of its time, but also the most expensive at £6.5 million, well over twice brunel’s initial estimate. He characteristically would brush aside budgets and spiralling expenses, preferring not to think about money, wanting only to be left free to do his finest work – thereby distressing his helpless financial associates, endangering and sometimes wrecking the whole enterprise. ‘He was the very Napoleon of engineers, thinking more of glory than of profit, and of victory than of dividends,’ a harsh contemporary estimate in the Quarterly Review concluded. ‘He seemed to love difficulties so much that he not infrequently chose the most difficult manner of overcoming them. Whatever was fullest of engineering perils had the greatest charms for him. That which was easy was comparatively uninteresting.’ Despite his declared focus on usefulness, he was actually the purest of engineers: a demanding, relentless artist intent on finding the most elegant solution regardless of costs or circumstances.
None of his debacles ever impeded his uncanny ability to get jobs and attract new investors. He caught and embodied the relentless engineering optimism of his time. ‘The most useful and valuable experience is that derived from failures and not from successes,’ he once wrote. ‘But what cannot be done?’ When testifying before a board of directors or a committee of Parliament, he was a formidable advocate: overflowing with esoteric knowledge, diplomatic yet seemingly candid, speaking tersely to the point, and charming and witty when that seemed appropriate. He could usually persuade even the most sceptical listeners. He disliked writing and thought he had no talent for it, but his memoranda piled up compelling arguments by steady accretion. brunel was also a facile, accurate draughtsman, decorating his workbooks with fine small drawings tossed off for the apparent fun of it, and if necessary he could go to his workshop and make a skilful model of a design in wood or iron. With his command of speaking, writing, drawing and modelling, he had the rare capacity to explain himself with clarity and eloquence in four modes and three dimensions – a key to his overwhelming powers of persuasion.
Today brunel remains the only British engineer of his era with an enduring popular reputation. In Great Britain he is virtually a folk hero. Some of his notable engineering works have survived as reminders of his wide-ranging inventiveness. The Great Western Railway still runs across many of his bridges and through the Box Tunnel. At one end of the line, his station at Bristol Temple Meads still stands, though now reduced to a humble car park. At the other end, his Paddington Station in London encloses tracks and platforms in a space 700 feet long and 240 feet wide, under a vaulting roof of wrought-iron arched ribs covered with glass and corrugated iron. The Royal Albert Bridge, his greatest feat of bridge building, crosses the River Tamar near Plymouth in two spans of 455 feet each, an artful blend of arch and suspension techniques. With its approaches added, the Royal Albert traverses a total of almost 2200 feet. The Clifton Suspension Bridge in Bristol, over the dramatically deep Avon gorge, was finished to his designs as a posthumous memorial. The Great Britain, his second ocean steamship, was improbably salvaged after a long, chequered career and was brought home to Bristol to be reconstructed and opened to the public.
Other brunel traces help keep his name alive. The reputations of historical figures often depend on the written footprints they happened to leave behind; brunel’s private papers and manuscripts, amounting to at least twenty-seven thick letterbooks and many other files, are housed at the University of Bristol and at the Public Record Office in Kew. Other brunel letters are scattered in a dozen archives across Great Britain. One of the fullest research troves available for any Victorian engineer, these materials allow historians an uncommonly rich record of his life. At Westminster Abbey, a brunel window in the south aisle memorializes him. A brunel statue stands on the Thames Embankment in London, looking upriver towards the Charing Cross site of his Hungerford pedestrian bridge, now long gone. At Paddington Station, another statue has him sitting down, looking thoughtful, holding his tall silk hat in one hand and a notebook in the other. In Bristol, a third statue presents him standing up, a jaunty hand in his waistband, gazing off towards the river and his preserved Great Britain steamship.
Brunel’s biography recapitulates the history of engineering in his time, from its French origins to its ultimate mid-Victorian feats in iron and steam. His father, Marc Isambard brunel, came from a family of tenant farmers in northern France, halfway between Paris and Rouen. Over his father’s opposition, Marc decided to be an engineer and spent six years in the French navy. Came the Revolution, and his Royalist sympathies exiled him to America, then to England, where he married an Englishwoman and settled into a picaresque engineering career. He always dressed and carried himself like a gentleman from the ancien régime, with its antiquated manners and costume. Once, in a British court proceeding, he was asked if he was a foreigner. ‘Yes, I am a Norman,’ he replied, ‘and Normandy is a country from whence your oldest nobility derive their titles.’
Marc brunel met Henry Maudslay in 1799, two years after Maudslay had opened his own machinist’s workshop. Their complementary skills meshed well: the French-trained engineer explaining his concepts, the skilled British mechanic bringing them down to ground and to practical execution. brunel and Maudslay worked on projects together for the next twenty years. At the Portsmouth Royal Dockyard, under the supervision of the naval architect Sir Samuel Bentham they devised steam-powered machinery for making the wooden blocks (pulleys) used in great numbers by sailing ships, turning out a cheaper, more consistent product than by the old hand methods. From this first success, brunel went on to inventions for sawing and bending wood, making shoes and boots, and improving marine steam engines and steamboat paddle wheels. He never quite regained the early heights of his novel blockmaking machinery. Abstracted and absentminded, he would lose umbrellas and take the wrong coach, ending up somewhere out in the country. A financial innocent, at one point he spent three months in a debtors’ prison.
Marc’s greatest work was his son, Isambard, born at Portsmouth in 1806. The boy resembled his father in appearance – small, a large head, dark complexion and eyes – and in his apparently innate knack for drawing and machinery. Isambard grew up in Chelsea, swimming in the Thames and meeting a stream of famous visitors at home. He found his métier at the Maudslay workshop: ‘your firm,’ as he later wrote to the Maudslays, ‘with which all my early recollections of engineering are so closely connected and in whose manufactory I probably acquired all my early knowledge of mechanics.’ Sent off to school near Brighton, he wrote home that he had been making boats, thus injuring his hands, and asked for his father’s eighty-foot tape measure. He spent two years in Paris, studying maths and the French language, and apprenticing under a famous maker of chronometers and scientific instruments. Denied entrance to the elite Ecole Polytechnique because of his foreign birth, he returned to England in 1822 and went to work for his father.
Still a teenager, he had already accumulated a range of education and experience – from Marc, Henry Maudslay, and in France – that few British engineers of his generation could match. Bilingual, bicultural, he displayed a precocious sense of engineering theory and practice. His intellectual gifts were obvious. Marc fully recognized them and pushed his son onward. As Isambard’s career took flight, his immersion in real engineering projects eventually crowded out his more theoretical French background. ‘One sadly loses the habit of mathematical reasoning,’ he noted. He became very much an Englishman, speaking with no French accent, and ever wary of continental tendencies. Later he advised a young man to spurn any writings by French engineers. ‘Take them for abstract science,’ he suggested, ‘and study their statics dynamics geometry etc etc to your heart’s content – but never even read any of their works on mechanics any more than you would search their modern authors for religious principles. A few hours spent in a blacksmith’s and wheelwright’s shop will teach you more practical mechanics – read English books for practice. There is little enough to learn in them but you will not have to unlearn that little.’
In 1825 the brunels embarked on a daring, unprecedented project to build a 1200-foot carriage tunnel under the Thames. Nobody had ever run a tunnel beneath a navigable, tidal river. The watery riverbed overhead consisted of unpredictable mixtures of clay, sand, gravel and mud, and was constantly disrupted by tides and river traffic. For these daunting conditions, Marc invented a novel construction shield. It resembled a giant bookshelf, three men high and twelve men across. Each man stood in a separate compartment, digging with pick and shovel; as the ground was excavated, the shield was screwed forward; bricklayers came in behind and shored up the tunnel. The work inched along, beset by leaking water and lighting and ventilation problems. At times the men stood in black water up to their knees.
After a year of difficulties, Marc took sick and told Isambard, twenty years old, to take over. The response of the brawny workmen to their new boss – so young, small, and French-educated to boot – may be imagined. Given all the circumstances, he managed well enough. At one point, with water leaking into the tunnel again, he did not get to bed for five straight nights. ‘No one has stood out like him!’ Marc wrote in his diary. Two hard years into the project, the river broke through from overhead in a gushing flood. Isambard descended on a rope to rescue a workman. For three weeks he could not plug the holes. Marc was harshly criticized by the authoritative Mechanics’ Magazine of London for not accepting advice or taking responsibility for his crucial mistakes. The leaks were finally sealed and work resumed, but in a changed climate of watchful outside scepticism.
Isambard sought refuge in an extraordinary private journal, the most candid and searching self-appraisals he ever committed to paper. He recorded the details of his daily life, the tunnel work, sleeping five hours a night, and stray thoughts about girls. At twenty-one, despite his adult responsibilities in the tunnel, he was between adolescence and grownup-ness. Still under construction, he took an unsparing look at himself. ‘My self-conceit and love of glory or rather approbation vie with each other which shall govern me,’ he wrote. ‘I often do the most silly, useless things to appear to advantage… My self-conceit renders me domineering, intolerant, nay, even quarrelsome with those who do not flatter.…I am always building castles in the air, what time I waste.’ Yet that self-conceit had quite adequate cause; he fully appreciated his own special talents and sought fame and reputation. ‘My ambition, or whatever it may be called (it is not the mere wish to be rich) is rather extensive.’ So probably he should never marry. ‘For one whose ambition is to distinguish himself in the eye of the public, such freedom is almost indispensable.’ Or maybe he should. ‘Yet, in sickness and disappointment, how delightful to have a companion whose sympathy one is sure of possessing.’ In this journal, he is less the engineering wunderkind, more any young man in baffled turmoil about his future.
In January 1828 water again broke into the tunnel, more seriously this time. Six men were killed. Isambard was knocked down, suffered internal injuries, and barely escaped alive. It took him over three months to heal. The Mechanics’ Magazine, no fan of the brunels, praised his coolness under pressure and brave concern for his men. But investors had lost confidence in the project, still only half completed. Work was stopped and the tunnel sealed. ‘Tunnel is now, I think, dead,’ Isambard later wrote in his diary. ‘This is the first time I have felt able to cry… However, nil desperandum [never despair] has always been my motto – we may succeed yet.’
At the time, he felt crushed by such a public defeat. The halting of the Thames Tunnel project did, however, free brunel from an endless, risky, dreadful burden – and from his father’s orbit – to pursue other work on his own. In Bristol, his designs for docks and the Clifton Suspension Bridge brought him to the attention of men involved in starting the Great Western Railway. Elected a fellow of the Royal Society at the early age of twenty-six, he was entering the most successful decade of his career. (The Thames Tunnel project was later resumed, but without brunel fils. It opened in 1843 just for pedestrians, not carriages, and ultimately became part of the London Underground.)
In step with the general progression from civil to mechanical engineering, brunel’s attention moved from tunnels to railways. He took his first trip late in 1831, on the Liverpool and Manchester. The carriage shook too much for easy writing. ‘The time is not far off,’ he decided, ‘when we shall be able to take our coffee and write while going noiselessly and smoothly at 45 miles an hour – let me try.’ He got his chance with the Great Western, the longest railway yet conceived in Great Britain. Appointed its engineer in the spring of 1833, he threw himself into this new work with all the energy of a good engineer at play. He spent long days on horseback surveying and plotting its route, placating resistant landowners along the way, and stayed up late writing letters and reports. Against the advice of most railway men, he convinced his board to accept a broad gauge of seven feet, more than two feet wider than the tracks of existing lines: a bold departure, ultimately proven wrongheaded, but early evidence of brunel’s forceful persuasive gifts.
For two years he was too busy even to scribble in his diary. The day after Christmas in 1835, he finally sat down and took stock. ‘The most eventful part of my life…emerging from obscurity,’ he wrote. ‘What a change – The Railway now is in progress. I am thus Engineer to the finest work in England…and it’s not this alone but everything I have been engaged in has been successful.’ (He was perhaps repressing any memories of the Thames Tunnel.) ‘And this at the age of 29 – Faith not so young as I always fancy tho’ really can hardly believe it when I think of it.…I don’t like it – it can’t last – bad weather must soon come.’ He moved into plusher quarters at 18 Duke Street in the Westminster area of London, with easy access to the corridors of influence at Parliament and Whitehall. It remained brunel’s home and office for the rest of his life. Resolving his earlier doubts about possible marital intrusions on those boundless ambitions, in July 1836 he took a trophy wife, a fabled beauty named Mary Horsley whom he had known and intermittently courted for five years.
Marriage and, later, fatherhood did not affect his usual work habits. During the first four months after his wedding, he made decisions about the brick-arched Maidenhead Bridge over the Thames, the Box Tunnel, the tile drains along the track, the heating and welding of iron bars, the sinking of bridge arches and the proper way of laying bricks, the ordering of four locomotives, the size of engine valves relative to piston area, the question of allowing Great Western work on Sundays, and the cheapest wood for posts. It was brunel’s line, all down the line. He installed his own methods for putting down the roadbed and securing the rails, served as architect for every station along the way, and even picked the names for the first locomotives. ‘It is an understood thing,’ he wrote to one of his men, ‘that all under me are subject to immediate dismissal at my pleasure.’
brunel’s control of every aspect of the Great Western made him the culprit when anything went wrong. As construction took longer and longer, and costs more than doubled, directors in London and Liverpool started having doubts about their young engineer. ‘The Box Tunnel is operating a good deal against the Great Western,’ noted George H. Gibbs, a London director. ‘Connecting it with the name of brunel, the difficulties of the Thames Tunnel are not unlikely to come into people’s mind.’ The first section of the line, from London to Maidenhead, was opened to passengers in June 1838. When trains did not run as fast or as smoothly as expected, brunel recommended reballasting the roadbed, replacing springs in the cars, and improving the locomotives. As the trading price of Great Western stock kept falling, shareholders in Liverpool moved to dismiss brunel. Even George Gibbs, who usually defended him, felt torn. ‘With all his talent,’ Gibbs wrote of brunel, ‘he has shown himself deficient…in arranging his work in his own mind so as to enable him to proceed with it rapidly, economically and surely. There have been too many mistakes, too much of doing and undoing.’
Under fire, for a brief time brunel felt shattered, even unable to work. His creation, so subject to costly revisions, was mockingly called the Great Experimental Railway. Gibbs had a blunt conversation with him; brunel promised to cooperate and retained the support of Gibbs and his faction. At a tense showdown during a meeting of the directors, brunel was again persuasive, defending himself with an even temper and compelling effect. The Liverpool contingent was outvoted, and brunel proceeded to finish the Great Western. Upon completion, it was acclaimed as the fastest, most strongly built railway in the world, and its engineer’s characteristic problems along the way were forgotten.
Brunel’s first steamship began with a famous jest in October 1835. At a Great Western directors meeting in London, someone objected to the unprecedented length of the line, planned to run all the way to Bristol through many expensive tunnels at the western end. Rising to the challenge and topping it, brunel replied with what he apparently meant as a joke: ‘Why not make it longer, and have a steamboat to go from Bristol to New York?’ A director from Bristol, an engineer turned sugar refiner named Thomas R. Guppy, took the riposte seriously. He and brunel talked it over that night. brunel had almost no prior experience with steam on water, but he recognized few boundaries to his engineering skills. He brought in an acquaintance, a semi-retired Royal Navy officer named Christopher Claxton, whom he knew from his earlier work for the Bristol docks. The three men started an informal steamship committee.
Claxton and William Patterson, a local shipbuilder, toured the main steam ports of Great Britain and sailed on every coastal and channel steamboat line. ‘Great improvements are being gradually introduced,’ they reported in January, ‘more particularly observable in the Clyde than elsewhere.’ For crossing the ocean, they recommended a much larger steamship than any yet built. They invoked a common principle, well known to shipbuilders of the time: that a vessel’s resistance as it moved through the water did not increase in direct proportion to its tonnage. As a measure of interior space, tonnage was computed from three dimensions. Resistance was then estimated from just two dimensions, the width and depth of the hull. Thus tonnage increased as the cube of the dimensions, resistance only as the square of them. A much larger ocean ship could therefore include the necessary space for coals and machinery, well beyond the capacity of a conventional ship, without requiring intolerable increases in power and fuel consumption to maintain adequate speed. Claxton and Patterson estimated that a steamship of 1200 tons and 300 horsepower, loaded with 580 tons of coal, would average between six and nine knots and cross the Atlantic in less than twenty days to the west, and just thirteen days to the east: roughly half the average voyages by sail.
The Great Western Steam Ship Company first planned to build two ships of that size, then decided on a single larger vessel of 1400 tons and 400 horsepower. Patterson – ‘known as a man open to conviction,’ according to Claxton, ‘and not prejudiced in favour of either quaint or old-fashioned notions in ship-building’ – would build her in Bristol. As managing director of the new company, Claxton looked after day-to-day operations. The building committee of brunel, Guppy, Claxton and Patterson met about once a week, whenever railway business brought brunel to Bristol. In general, on this committee Patterson took charge of the ship, brunel of the engine. ‘Mr. Patterson drew the lines,’ Claxton later recalled; ‘Mr. brunel, Mr. Guppy, and myself, often sat over them; Mr. Patterson got instructions and made his own calculations accurately; Mr. brunel made his also often by my side.’ Over the next two years, they planned and built the largest steamship yet, the first designed for regular crossings of the North Atlantic.
They were racing against a competing group in London organized by Junius Smith, an expatriate American businessman. His British and American Steam Navigation Company drew investors from both sides of the ocean. This final sprint to steam across the Atlantic came down to three separate but overlapping rivalries: Britain against America, Bristol against London, and the Clyde against the Thames (or the North against the South). Subtly complicated and multiply crosshatched, the contest was played out amid fierce regional loyalties for rich stakes of prestige and fortune.
The crucial technical questions involved engines and boilers. The two leading British builders of marine steam engines were Robert Napier of Glasgow and Maudslay, Sons and Field of London. (Clyde and Thames.) After Marc brunel’s old friend Henry Maudslay died in 1831, the firm had passed on to his sons, Thomas and Joseph, and in particular to Joshua Field, a skilled engineer and manager. ‘No vessel ever had a sufficient power yet,’ Field had declared in 1822. ‘There is a limit, but that limit has never yet reached its fullest extent.’ As horsepowers kept on growing, the upper border was continuously extended. Progress already seemed infinite. By the 1830s, both Napier and Field were intrigued by the potential honour of powering the first true Atlantic steamship. ‘I have not the smallest doubt upon my own mind,’ Napier wrote in 1833, ‘but that in a very short time it will be one of the best and most lucrative businesses in the country.’ ‘The distance is limited,’ Field added a few years later, ‘only by the quantity of coal she can carry.’